Bead Winding in Tire Manufacturing
Tire bead winding requires precise control of reinforcing cords and wire placement, with tolerances measured in millimeters across a circumferential path that can exceed 2 meters. Current manufacturing processes face material waste rates of 15-30% during cord splicing, while maintaining consistent cord tension and spacing remains critical for tire durability and performance.
The fundamental challenge lies in balancing manufacturing speed and precision with the need to create robust, uniformly reinforced bead structures that can withstand decades of dynamic loading.
This page brings together solutions from recent research—including continuous cord joining techniques, pre-formed annular section assembly methods, wavy steel cord winding with variable extension, and elastomeric tape-based reinforcement approaches. These and other approaches focus on reducing material waste while improving production efficiency and bead durability.
1. Device for Manufacturing Tire Beads with Stacked Coated Wires of Polygonal Cross Section
KUMHO TIRE CO INC, 2024
Tire bead manufacturing device that improves tire durability by stacking coated wires with polygonal cross sections in close contact. The device has a wire coater to form coated wires with compounded rubber, and a wire winder with segments having grooves. An adhesion unit allows the coated wires to closely stack in the grooves. This reduces gaps between wires in the tire bead, preventing splitting and cracks.
2. Spiral Winding Machine with Adjustable Winding Direction and Detachable Ring Mechanism for Tire Bead Fabrication
ZHONGHUA INTELLIGENT TECH SHANDONG CO LTD, ZHONGHUA INTELLIGENT TECHNOLOGY CO LTD, 2024
Spiral winding machine for making tire beads with adjustable winding direction to allow customization of bead strength for different tire applications. The machine has two groups of winding mechanisms with adjustable rotation direction. Each group has vertical wire cores surrounded by windable wire reels. The reels have detachable outer rings that can be swapped between groups. This allows winding steel wire around the cores in different directions. A transmission mechanism connects the winding rings and a drive mechanism turns both rings simultaneously. An adjustment mechanism allows reversing the rotation of one ring. This provides flexibility to adjust the winding direction for optimal bead strength based on tire requirements.
3. Method for Preparing Lightweight Cable-Type Tire Beads with Adjusted Metal Yield Ratio and Non-Metallic Ring Diameter
SHANDONG DAYE CO LTD, 2023
A method for preparing lightweight cable-type tire beads with improved performance by optimizing the winding process to reduce weight without sacrificing strength. The method involves adjusting the yield ratio of the metal outer winding wire and the diameter of the self-forming ring for the non-metallic outer winding wire. This compensates for the reduced stiffness caused by the lighter non-metallic outer winding wire. It allows using lower weight materials while maintaining comparable strength and formability to conventional cable beads.
4. Structural Cable Bead with Non-Metallic and Metallic Winding Wire Layers
SHANDONG DAYE CO LTD, 2023
A structural cable bead for tires with improved rubber penetration, corrosion resistance, and wear life compared to conventional cable beads. The novel bead has at least one layer of non-metallic winding wire with a different diameter than the metallic winding wires. This allows better rubber penetration between the winding layers, reducing friction and corrosion compared to tightly compacted metallic winding. The non-metallic winding also improves flexibility and reduces weight compared to metallic winding alone.
5. Manufacturing Method for Cable-Type Tire Beads with Controlled Steel Wire Elongation via Heat Treatment
SHANDONG DAYE CO LTD, 2023
Method to manufacture cable-type tire beads for passenger cars that improves tire durability and prevents air leakage between the tire and rim. The method involves regulating the elongation of the steel wire in the tire bead core through heat treatment during manufacturing. This prevents excessive stretching of the bead when mounted on the wheel rim, ensuring tight fit and preventing air leakage. The heat treatment involves annealing the steel wire at specific temperatures and times to control elongation within a range of 1.5-5%. This prevents excessive stretching of the bead when mounted on the wheel rim, ensuring tight fit and preventing air leakage.
6. Manufacturing Method for Cable-Type Beads with Controlled Outer Winding Wire Yield Ratio
SHANDONG DAYE CO LTD, 2023
Method for manufacturing cable-type beads for passenger car tires that can be predicted to prevent unexpected failures. The method involves controlling the yield ratio of the outer winding wire during bead production. The yield ratio is kept between 70% and 90%. This allows the bead to deform more before breaking, providing warning signs and delaying failure compared to higher yield ratios. By adjusting the pressing force on the outer winding during bead straightening, the yield ratio can be targeted.
7. Radial Tire Bead Wire Winding Device with Adjustable Plate and Movable Tube Mechanisms
JIANGSU SHENGDA TECH CO LTD, JIANGSU SHENGDA TECHNOLOGY CO LTD, 2023
High-speed radial tire bead wire winding device that improves wire winding stability for radial tire production. The device has a rotating disk with winding plates that can move towards or away from the disk axis. The plates have moving mechanisms to adjust their position. A wire blocking mechanism with a movable tube moves towards and away from the disk and axis. The tube corresponds to each plate and guide rods connect them. This allows controlling wire tension during winding for improved fatigue resistance in radial tires.
8. Bead Wire Winding Mechanism with Synchronized Forming Heads and Clamping Device
ZHANGJIAGANG SUTENG ELECTROMECHANICAL EQUIPMENT CO LTD, 2022
Bead wire winding mechanism for bead forming equipment in tire manufacturing that prevents wire scatter and bead misalignment during winding. The mechanism has synchronized moving forming heads and clamping device to keep wire centered as it winds around spokes. The heads have slotted arches to accommodate the wire and spokes. A clamping device on one head grabs the wire end and holds it while the heads move opposite directions. This prevents wire separation and ensures consistent bead wire positioning.
9. Cable Bead with Annular Core and Spirally Wound Side Wires
OHASHI SHOICHI, 2022
Cable bead for tires with improved strength and manufacturing efficiency. The cable bead has an annular core made by winding round steel wire without twisting, and side wires spirally wound around the core. The annular core shape provides better bead-rim contact due to uniform deformation. The side wires follow the core curvature. This integrates the core and side wires into a single cable bead, eliminating separate core welding steps. The cable bead can be manufactured at lower cost and higher speed compared to conventional stranded cable beads.
10. Tension Control System with Detection and Adjustment Mechanisms for Bead Ring Winding Machine
TIANJIN SAIXIANG ELECTROMECHANICAL ENG CO LTD, TIANJIN SAIXIANG ELECTROMECHANICAL ENGINEERING CO LTD, TIANJIN SAIXIANG TECH CO LTD, 2022
Tension control system for a bead ring winding machine used in tire production. The system aims to improve consistency and quality of bead rings by controlling the tension of the steel wire during winding. It uses a tension detection device to measure wire tension before winding, and a tension adjustment mechanism in the wire storage device to change wire tension. This allows precise tension control of the wire as it is wound into the bead ring, mitigating deformation issues caused by tension variations during winding.
11. Manufacturing Method for Bead Wires with Folded Excess Braided Wire via Plastic Deformation
Michelin Group Headquarters, MICHELIN GROUP CORP, 2022
Method for manufacturing bead wires for tires that reduces length and simplifies assembly by folding the excess braided wire after winding. After braiding the wire around a looped core to form the bead wire, an extra-long section protrudes. This section is then plastically deformed to create a bend that deflects it outward from the braided toroid. This folds and shortens the excess wire while keeping the main toroid shape. The folded section now protrudes partially, making it easier to handle and join compared to the elastic winding section.
12. Polyhedron-Shaped Bead Wire with Twisted Core and Rubber Coating
NEXEN TIRE CORP, 2022
Bead wire for tires that reduces weight, improves flexibility and durability compared to traditional bead wires. The bead wire has a polyhedron shape formed by topping a twisted wire part with rubber. This provides a specific cross-sectional shape to the bead wire instead of the traditional round wire. The polyhedron shape reduces weight, maintains rigidity and flexibility, and allows combining multiple polyhedrons to expand cross-sectional area. The unique bead wire design improves tire bead installation and retention.
13. Method for Continuous Joining of Reinforcing Cords with Sequential Feeding and Splicing in Tire Manufacturing
THE YOKOHAMA RUBBER CO LTD, YOKOHAMA RUBBER CO LTD, 2021
Method to reduce waste in manufacturing tires with reinforcing cords that are wound multiple times around the tire circumference while extending in the tire width direction. The method involves feeding and joining the reinforcing cords in a specific order to avoid cords becoming too short during tire formation. First, a cord is fed ahead to form the desired section. Then, the next cord is fed and joined to the first cord at a splice mechanism. This continues, joining the trailing end of the first cord to the leading end of the next cord, until the desired length is reached. This allows using shorter cords without waste since they are continuously joined together.
14. Tire with Reinforced Bead Structure Incorporating Folding Carcass and Protrusion Elements
GOODYEAR TIRE & RUBBER, THE GOODYEAR TIRE & RUBBER CO, 2021
A tire design with improved durability and reduced stresses in the bead area. The tire has a unique bead construction that aims to mitigate cyclic stresses and deformations in the bead structures. The bead has a folding part of the carcass reinforcement and a protrusion that extends inward. A wire reinforcement contacts the carcass ply at the inner bead and the folding part. This prevents cyclic bending and stresses at the folding end. A filler between the carcass and folding part reduces deformations. The seating portion contacts the rim to prevent cyclic displacement. The protrusion prevents cyclic bending at the inner bead.
15. Cable Bead with Core Wire and Outer Winding Wires Featuring Unique Cross Sectional Geometry
Jiangsu Xingda Steel Tyre Cord Co., Ltd., 2020
A cable bead for tires with improved strength and durability compared to conventional beads. The bead has a core wire surrounded by at least one layer of outer winding wires. The outer winding wires have a unique cross section shape, with a major axis perpendicular to the radial direction and a minor axis parallel to the radial direction. The minor axis axes all converge at a point. This shape eliminates large gaps between wires and prevents point contact between adjacent layers. The wires contact the core wire and line contact between layers.
16. Tire Bead Structure with Slotted Rubber Sealing Sleeve and Curved Block Inserts
ZHANG KANGWEI, 2020
Anti-broken tire bead structure to prevent wire separation in tires. It has a bead wire, rubber sealing sleeve, curved rubber blocks, apex, and carcass cord layer. The rubber sealing sleeve around the bead wire is slotted and the curved rubber blocks fit inside the slots. This adds thickness to the friction protection layer between the bead wire and carcass cord. It reduces wire-wire contact and friction compared to just an apex. The blocks are inserted and sealed using a processing device with steps like wire fixing, slotting, block pushing, apex gluing, and cord wrapping.
17. Bead Wire Array Former with Rotating Body and Sensor-Controlled U-Shaped Groove Frame Members
NEXEN TIRE CORP, 2020
Bead wire array former for tires that allows easy and precise arrangement of bead wires in tires to improve tire performance and durability. The bead wire array former has a rotating body controlled by a sensor-based system that winds bead wires into the tire carcass. The rotating body has fixed central fastening parts and variable frame members that form U-shaped grooves. When winding the bead wires, they are guided into the U-shaped grooves on the outer surfaces of the fixed central parts. This provides a simple way to change the bead wire arrangement structure by varying the frame members. The U-shaped grooves also have features like recesses or pyramids between the bead fillers to improve binding force and prevent separation.
18. Bead Core Manufacturing Apparatus with Diameter Measurement and Tension Adjustment Mechanism
SUMITOMO RUBBER IND, SUMITOMO RUBBER IND LTD, 2020
Bead core manufacturing apparatus for stable production of bead cores used in tires. The apparatus has a winding mechanism to form bead cores by winding a rubber-coated wire. It measures the winding diameter and adjusts the wire tension based on that measurement. This prevents variation in bead core outer diameter caused by tension changes during winding. It also has an option to adjust wire temperature based on extruded rubber temperature to prevent sticking issues.
19. Automated Tire Bead Winding Machine with Synchronized Flattening and Rolling Mechanisms
RONG WENLONG, 2020
Tire bead winding molding process using a specialized machine that allows automated, synchronized flattening and rolling of the steel wire reinforcement around the tire bead. The machine has a rotating platform with a flattening rod, a locking mechanism, and a leveling mechanism. The locking mechanism secures the wire belt during winding, while the leveling mechanism positions and rolls the belt. This prevents manual support, synchronizes flattening, and avoids irregular bead shapes.
20. Bead Core Manufacturing Device with Rotating Support and Clamping Mechanism for Wire End Crimping
TOYO TIRE CORP, 2020
A device for manufacturing bead cores of pneumatic tires that prevents the bead wire from bouncing during winding and protruding at the ends. The device has a rotating support to wind the bead wire onto an expandable/contractible diameter body. A clamping device grips the bead core widthwise to include the winding end of the bead wire. This crimps the wire end to the core instead of allowing it to extend. This prevents the wire from twisting during winding and keeps the end from protruding in the finished bead core.
Get Full Report
Access our comprehensive collection of 72 documents related to this technology
Identify Key Areas of Innovation in 2025
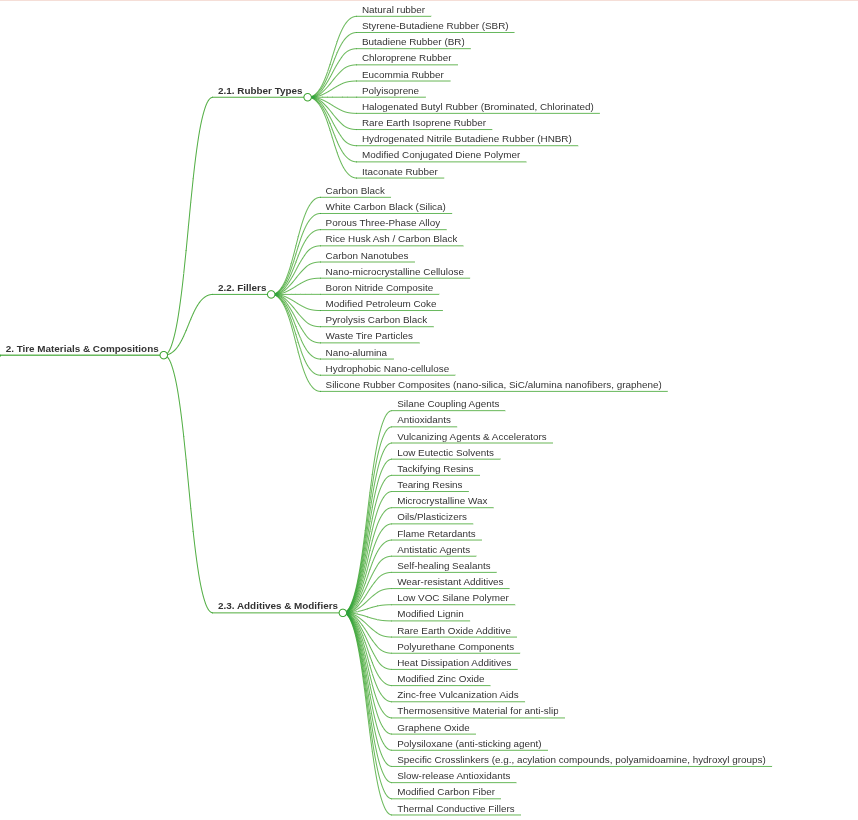