High-Strength Materials for Tire Manufacturing
Heavy-duty tires in mining and industrial environments routinely face temperatures exceeding 100°C, dynamic loads over 400 tons, and sustained exposure to cutting agents. Under these conditions, conventional rubber compounds experience accelerated wear, with field data showing up to 40% reduction in service life compared to standard operating environments.
The fundamental challenge lies in developing materials that maintain elasticity and wear resistance at temperature extremes while preserving the structural integrity needed to handle massive dynamic loads.
This page brings together solutions from recent research—including modified carbon fiber compounds for puncture resistance, nanocomposite-enhanced filler dispersion systems, and specialized rubber matrices with controlled compatibility between components. These and other approaches focus on extending tire life and reliability in the most demanding industrial applications.
1. Polymeric Blend for Non-Pneumatic Tire Components with Thermoplastic Polyester Elastomer and High Temperature Polymer
BRIDGESTONE AMERICAS TIRE OPERATIONS LLC, 2025
Temperature stable polymeric blend for non-pneumatic tire components like spokes that can maintain strength over a broad range of temperatures. The blend combines a thermoplastic polyester elastomer with a high temperature thermoplastic polymer like polysulfone. A compatibilizer resin, delayed crosslinking agent, and activator are mixed in. The blend can be prepared by melting the high temperature polymer and blending in the other components. The temperature stable polymeric blend is processable by injection molding and crosslinks to form a stable, high temperature tire component.
2. Synergistic Enhancement of Bio‐Based <scp><i>Eucommia Ulmoides</i></scp> Gum Nanocomposites Through Epoxidized Natural Rubber and Silane Coupling Agent Integration: Advancements in High‐Performance Engineering Tires
zhi chen, dexian yin, xin wang - Wiley, 2025
ABSTRACT As the global transportation industry evolves, there is a rapid surge in market demand for engineering tires. Nevertheless, working environment becoming increasingly complex and challenging, tires are now subject to more stringent performance requirements, including reduced rolling resistance, decreased heat generation, enhanced wear cut resistance. In this work, type of Eucommia ulmoides gum (EUG)/natural rubber (NR)/styrenebutadiene (SBR) nanocomposite was effectively prepared with silica as nanofiller. Subsequently, epoxidized natural (ENR) introduced into EUG/NR/SBR nanocomposites address issue agglomeration within enhance comprehensive nanocomposites. The relationship between ENR content further investigated. results demonstrate that reduces surface activity via hydrogen bond effect grafting reaction, thus enhancing dispersion. Moreover, at an 9 phr, dynamic temperature rise 25.2C volume abrasion 0.135 cm 3 1.61 km 1 , representing 12.2% reduction 21.1% decrease compared without ENR. This work develops innovative approach dispersion fillers EUGbased multifu... Read More
3. Bulk Nanocomposites with Aligned Nanostructures and Solid Matrix Infusion via Capillary Action
MASSACHUSETTS INSTITUTE OF TECHNOLOGY, 2025
Bulk nanocomposites with high nanostructure loading and low void volume for lightweight, strong, and high-temperature materials. The composites have a domain with aligned nanostructures like carbon nanotubes infused with a solid matrix material. The nanostructures occupy a high volume fraction while voids are minimized. This is achieved by aligning the nanostructures then infusing them with the matrix via capillary action. Densification hardens the composite. The aligned nanostructure array allows matrix flow. This allows making large-scale, high nanostructure volume composites with low voids using stacking and hardening. The composites can be used as feedstock for additive manufacturing.
4. Elastomeric Composites with Ultra-Fine Purified Carbonaceous Product Filler Derived from Coal Waste
ARQ IP LTD, 2025
Elastomeric composites with improved properties by replacing traditional carbon black filler with a purified carbonaceous product (PCP) derived from coal waste. The PCP has ultra-fine particles less than 25 microns in size and low ash and water content. The PCP provides better dispersion and reinforcement in elastomers compared to conventional carbon black. It enables improved tensile strength, toughness, and elastomer performance compared to carbon black. The PCP can be used as a standalone filler or blended with carbon black. The composites have lower ash content and better sustainability compared to recycled carbon black.
5. Rubber Compound Incorporating Carbon Nanotubes for Enhanced Durability and Microcrack Prevention
MOLECULAR REBAR DESIGN LLC, 2025
Using carbon nanotubes called Molecular Rebar in rubber compounds to improve tire durability and reduce environmental impact. The carbon nanotubes bind with the polymer matrix, improving wear resistance without detrimentally affecting rolling resistance, and reducing overall environmental concern over antiozonants in the tire. The nanotubes halt microcracks that form from ozone exposure, allowing use of less antizoonant or safer alternatives without increased tire failure. The nanotubes also slow antizoonant migration from the rubber.
6. Adducts of Sulfur-Containing Pyrrole Derivatives with sp2 Hybridized Carbon Allotropes
PIRELLI TYRE S.P.A, 2025
Adducts between pyrrole derivatives containing sulfur atoms and sp2 hybridized carbon allotropes like carbon black, graphene, and nanotubes. The adducts improve elastomer reinforcement by enhancing compatibility between the filler and matrix. They can be obtained by reacting the pyrrole derivatives with the carbon allotropes. The adducts have applications in crosslinkable elastomer compositions for tire compounds. The process involves mixing the carbon allotrope and pyrrole derivative at room temperature. The adducts formed provide reduced Payne effect and improved reinforcement at high deformations compared to unreacted filler.
7. Improvement of Tribological Properties of Natural Rubber Filled With Waste Tire Pyrolysis Carbon Black Treated by Plasma
xiaogang wen, xinyu zhu, shuo chen - Wiley, 2025
ABSTRACT The erosion and polarization effects were much more evident with the increase in plasma power for pyrolysis carbon black (CBp) arising from waste tire. However, a strong fusion effect appeared when reached 600 W. CBp400 W had best dispersion rubber matrix deepest interaction molecular chains. CBp600 worst most remarkable weak matrix. Compared NR/CBp0 W, tensile strength increased by 16.6%, DIN abrasion volume decreased 8.1% NR/CBp400 Its coefficient of friction (COF) resistance enhanced 22.6%/56.5% (7 N : 0.25 m/s), 13.5%/30.1% 0.5 7.6%/28.8% (14 20.3%/34.1% m/s) under dry conditions. steady COF 53% compared wet conditions, regulation was accordance that tan at 0C detected dynamic mechanical measurement. In this work, it proved 400 optimized power. Filler fillerpolymer crucial factors enhancing resistance. Additionally, research introduced novel approach assessing wetslip materials.
8. Rubber Composition Incorporating Carbon Black with Defined Oil Absorption and Surface Area Characteristics
BRIDGESTONE CORP, 2025
Rubber composition for tires with improved wear resistance, breaking strength, and processability. The composition contains a rubber component and carbon black with specific properties. The carbon black has an oil absorption number of 105-122 mL/100g, CTAB specific surface area of 130-153 m2/g, D50/Dst ratio of 0.75-0.88, oil absorption difference of 11-33 mL/100g, and hydrogen evolution of 2300-3500 ppm. This carbon black provides wear resistance and breaking strength while avoiding excessive structure and agglomeration for better processability compared to conventional carbon blacks.
9. State-of-the-art of poly(ether ether ketone) matrix reinforced with nanocarbons (carbon nanotube/carbon black) and carbon fibers—promising design, physical attributes and futuristic opportunities
ayesha kausar - SAGE Publishing, 2025
This state-of-the-art overview highlights technical worth of a high-tech engineering thermoplastic polymer, poly(ether ether ketone), and its hybrids with carbonaceous nanoreinforcements carbon fibers. Accordingly, literature up till now reports on different categories multifunctional ketone)/carbon nanotube, black, fiber materials. These composites/nanocomposites have been fabricated through various techniques including solution processing, melt casting, prepreg method, injection/compression molding, three dimensional printing, other efficient strategies. Adding nanofiller/filler revealed significant enhancements in morphological profiles, heat stability, mechanical features, electrical conductivity, biological properties ketone). In the case composites, interfacial compatibility superior physical performance achieved sizing fibers (using nanocarbon nanoparticles or polymers). Subsequently, modification nanoparticles, fiber, ketone) backbone led to technically high end applications for aerospace, fuel cells, bone implants. Nevertheless, further research regarding design/structural o... Read More
10. Diene-Based Elastomers with Benzoxazine-Functionalized Polymer Chains and Carbon Spacers
THE GOODYEAR TIRE & RUBBER CO, 2025
Benzoxazine-functionalized diene-based elastomers with reinforcing properties for rubber compositions like tires. The elastomers have polymer chains with repeat units from conjugated dienes like butadiene, isoprene, and styrene, and benzoxazine rings attached via spacers. The spacers are 3-8 carbon atoms long. The benzoxazine groups provide reinforcement when attached to the polymer chains. The elastomers can be used in rubber compositions for tire reinforcement instead of carbon black or silica.
11. Impact of quenching on the microstructure and mechanical properties of hybrid aluminum matrix composites (Al7075/SiC/TiB <sub>2</sub> )
mahendra singh, ajay biswas - SAGE Publishing, 2025
The introduction of hybrid composites, which integrate multiple reinforcements, presents opportunities for further optimization. Hybrid aluminum matrix composites (AMCs) reinforced with silicon carbide (SiC) and titanium diboride (TiB 2 ) are particularly noteworthy due to the complementary advantages provided by these reinforcements. Microstructural analysis shows good bonding between reinforcements; however, particle agglomeration casting defects indicate a need improved processing. While SiC dispersion enhances strength, TiB can be minimized through optimized processing, leading more homogeneous composite. Despite anticipated increase in hardness from overall decreased non-uniform defects, negatively affecting wear resistance. Quenched composite had lowest (113.03 HV), likely residual stresses interfacial issues. Such have been shown ideal automotive brake systems, aerospace sliding interfaces, structural wear-resistant components. synergistic interaction imparts superior resistance across range tribological conditions. This improvement is result microstructural hardening, efficie... Read More
12. Efficient fabrication of lightweight high-strength carbon fiber reinforced PEEK with node-reinforced truss
pengfei xiang, longze chen, chao song - SAGE Publishing, 2025
Carbon fiber-reinforced polyetheretherketone (CF/PEEK) composite offer lightweight, high strength and toughness by combining benefits of resin fiber materials. However, current shaping methods face challenges such as forming difficulties, inconsistent shapes, significant mechanical damage. Herein, a CF/PEEK thermoforming device were designed. Thermoforming employs two heating molds (crimping mold at 310C roll pipe 400C) coiling roller operating 45 rpm to enable automatic efficient continuous production pipes with diameters ranging from 3 5 mm. High-strength retain excellent thermal stability during shaping, commendable properties-tensile 1467 N (decrease 8.8 %) specific stiffness 1.61 10 6 Nm/kg, 35-fold increase. Furthermore, stronger braided winding points introduced into hollow truss enhance their strengths, radial compression node-reinforced structure is 550 (improved 151 % compared that single pipe). This truss, its ultra-lightweight tensile/compressive strength, significantly expands application potential
13. Metallic Reinforcing Cord with Helical Structure and Specific Wire Spacing
PIRELLI TYRE S.P.A, 2025
Metallic reinforcing cord for tires with improved adhesion and reduced corrosion compared to traditional metallic cords. The cord has a helical structure with a specific spacing between the metallic wires. The spacing allows the tire rubber to penetrate between the wires for better adhesion. The cord provides a balance of elongation and rigidity like textile cords at low loads, but higher rigidity like metallic cords at high loads. This is achieved by twisting the metallic wires together with a specific pitch.
14. Reinforcing Material with Thermosetting Resin Layer Containing Diene Rubber and Tackifier Resin with Specified Softening Temperature and Bromine Value
NITTO DENKO CORP, 2025
Reinforcing material and structure with improved reinforcement performance. The reinforcing material has a resin layer with specific components to enhance adhesion and strength. The resin layer contains a thermosetting resin, diene rubber, tackifier resin, and vulcanizing agent. The tackifier resin has a softening temperature of 75°C to 100°C and a bromine value of 30 g/100g or more. This tackifier composition provides good tack for initial adhesion while also allowing the resin to cure and harden for long-term strength. The reinforcing structure uses this reinforcing material to reinforce an object by applying the reinforcing material as a layer on the object.
15. Method for Uniform Vulcanization of High-Modulus Graphene Oxide/Natural Rubber Tires with Specific Ingredient Ratios
UNIV NORTH CHINA, 2025
A method to make uniformly cured high-modulus graphene oxide/natural rubber tires that have improved wear resistance and tear strength. The method involves optimizing the vulcanization process for thick rubber tires using specific ingredient ratios. It balances internal and external rubber cure to prevent over or under vulcanization. The ratios are: 0.5-5% graphene oxide, 40-120% carbon black, 1-20% activator, 1-20% softener, 1-10% anti-aging agent, 1-10% antioxidant, 1-20% vulcanization accelerator, 1-20% vulcanizing agent, and 1-20% interface modifying agent.
16. Method for Enhancing Interfacial Interaction in Graphene-Modified Natural Rubber Composites via Free Radical Scavenger-Loaded Reduced Graphene Oxide
SHANXI ZHONGBEI NEW MATERIAL TECH CO LTD, 2025
A method to improve the properties of graphene-modified natural rubber composites by enhancing interfacial interaction between the rubber matrix and graphene. The method involves loading a free radical scavenger onto the surface of reduced graphene oxide (rGO) during its preparation. When the rGO-modified rubber is mixed, the scavenger annihilates free radicals generated from the rubber due to heat or force, improving interfacial interaction beyond hydrogen bonding. This increases rubber bound to rGO, enhances crosslink density, and improves strength and toughness of the graphene-modified rubber composite.
17. Precipitated Silica Modified with Alkali Metal Alkyl Siliconates During Precipitation
RHODIA OPERATIONS, 2025
Chemically modified precipitated silica with improved compatibility with polymeric matrices. The silica is modified during the precipitation process by adding alkali metal alkyl siliconates. This allows the formation of silica chemically modified with alkyl groups. The modification takes place during the precipitation without additional steps. The modified silica can be used as a reinforcing filler in polymeric compositions like tires.
18. Method for Preparing Wet Master Batch Elastomer Composition with Silica-Modified Styrene-Butadiene Rubber
KOREA KUMHO PETROCHEMICAL CO LTD, 2025
Method to prepare a wet master batch elastomer composition for making rubber with excellent processability and abrasion resistance. The method involves dispersing silica particles and an organic silane coupling agent in a styrene-butadiene rubber (SSBR) solution, stirring to pulverize the silica while modifying its surface with the coupling agent, removing solvent, drying, and solidifying to create a composite. Compounding this composite with additional additives makes a wet master batch elastomer composition with improved silica dispersion and binding strength in the final rubber. The composite has 8-20 parts organic silane coupling agent per 100 parts SSBR.
19. Rubber Composition Incorporating Silane-Modified Resin with Specific Modulus and Melting Temperature for Enhanced Silica Dispersion
TOYO TIRE CORP, 2025
Rubber composition for tires with enhanced wet grip performance, strength, and tensile properties. The composition contains a diene rubber, silica, and a silane-modified resin with a modulus of 700-1200 MPa and melting temperature of 110-140°C. The silane-modified resin improves silica dispersion and rubber matrix interaction compared to conventional silanes.
20. Feedstock Particles Coated with Discrete Carbon Nanotubes Featuring Controlled Porosity and Surface Modifications
MECHNANO LLC, 2025
Coating molding feedstock particles with discrete carbon nanotubes to improve properties like strength, conductivity, and processability. The coating thickness is 5-5000 nm on particles <5 mm. The carbon nanotube coatings have controlled porosity and surface modifications for sintering, wetting, and flow. The coating composition has <20% entangled nanotube bundles >5 µm in size. The coatings can be used in 3D printing, molding, and injection molding processes.
Get Full Report
Access our comprehensive collection of 61 documents related to this technology
Identify Key Areas of Innovation in 2025
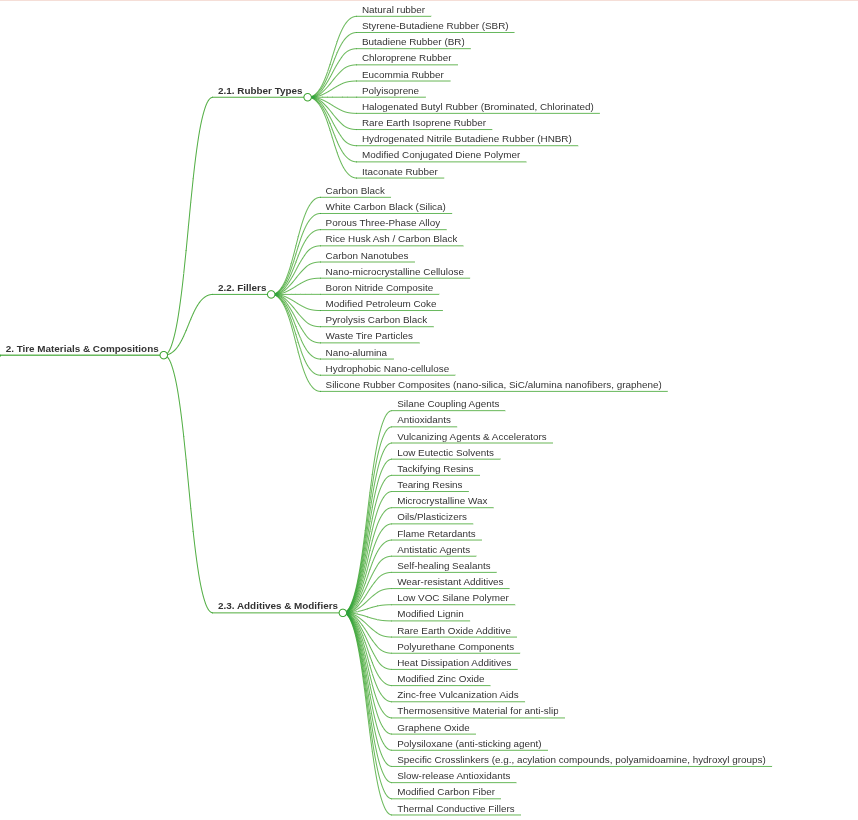