Automated Systems in Tire Production
Modern tire manufacturing involves coordinating multiple critical processes—from compound mixing and extrusion to assembly and curing—with typical plants producing over 20,000 tires daily. Traditional methods rely heavily on manual inspection and handling steps that introduce variability and limit production rates to around 1-2 minutes per tire in even the most efficient facilities.
The fundamental challenge lies in automating highly tactile processes while maintaining the precision needed for safety-critical components.
This page brings together solutions from recent research—including thermal imaging systems for automated defect detection, robotics-assisted mounting and demounting operations, and intelligent tread wear monitoring technologies. These and other approaches show how automation can enhance both manufacturing efficiency and quality control in tire production.
1. Annular Frame Conveyance Device with Independently Driven Suction Pads for Transferring Cylindrical Tire Forming Members
TOYO TIRE CORP, 2025
A conveyance device for transferring cylindrical tire forming members between drums in a tire manufacturing process. The device has an annular frame that surrounds the drums, a sucker on the frame with suction pads to grip the tire, and a frame conveyor to move the annular frame. The suction pads are side by side in circumferential direction and adjacent pads are driven by different mechanisms to allow radial movement. This allows conveying a tire between drums without needing a separate vacuum chamber for each drum size.
2. Thermal Imaging-Based Automated Tire Defect Detection System with Inflation-Induced Temperature Variation Analysis
PAUL E HAWKINSON CO, 2025
Automated tire defect detection system that uses thermal imaging to identify tire defects without the need for water immersion or manual inspection. The system captures infrared images of a tire section before and after inflation to detect areas that cooled due to air escaping through defects. By comparing frames, it identifies defect locations based on temperature changes. The system is fully automated and records results without requiring trained operators.
3. Conveyance Device with Adjustable Suction Pad Assembly for Cylindrical Tire Mold Handling
TOYO TIRE CORP, 2025
A conveyance device for moving cylindrical tire molds between drums in a tire manufacturing process. The conveyance device has a frame that surrounds the drums and a sucker attached to the frame. The sucker has center suction pads to grip the mold's center and end suction pads to grip the mold's ends. There is a gap between the center and end pads. An adjustment device can vary the gap length in the axial direction. This allows the conveyor to properly grip molds of varying thicknesses without deforming them due to excessive suction force. The end pads move opposite directions to adjust the gap length.
4. Cutting Device with Retaining Members and Active Pressing for Tire Components
VMI HOLLAND BV, 2025
Cutting device and method for reliably cutting tire components like breaker cushions and gum strips without damaging the edges. The device has retaining members along the cutting line to hold the component at specific regions. This prevents biting and curling of the edges during cutting. A pressing device moves the component onto the retaining members before cutting. The cutting device also has features like vacuum-cup retaining, simultaneous retaining symmetry, and active pressing to accurately engage the edges. The method involves aligning the component, pressing the edges, and then cutting.
5. Complex Forming Device with Extrusion Roller and Threaded Chamber for Non-Protruding Rubber Layer Formation
COMPAGNIE GENERALE DES ETABLISSEMENTS MICHELIN, 2025
Complex forming device for making rubber products with non-protruding layers by using blades to pass underneath. The device has an extrusion roller with a chamber for plasticizing the rubber. The chamber is defined by the roller and a wall with projecting threads. The threads delimit the chamber to shape the rubber. But the device also has additional features to allow blades to pass beneath the extruded rubber. This prevents protrusions and provides smooth layers. The device has supports for an additional roller below the extrusion roller, and securing to hold it in place. This allows the blades to move between the rollers. It also enables removing any rubber particles trapped between the rollers. The device can be used in tire production lines to make tires with consistent smooth layers.
6. Apparatus with Peeling Device for Detaching Rubberized Electronic Tags from Carrier Band During Tire Assembly
PIRELLI TYRE SPA, 2025
Automated method and apparatus for applying rubberized electronic tags to tires during the tire building process. The method involves using a specialized peeling device to detach the lightweight, flexible, sticky tags from a continuous band carrying them. The device has a section where the band with tags enters and slides. The tags initially adhere strongly to the band's front surface. As the band moves through the section, the tags gradually detach due to a lower adhesion force on the back surface. This prevents the tags from following the band's curvature and jamming. The detachment force required is lower at the exit since the adhesion force is reduced.
7. Robotic System for Variable Profile Sealing Agent Application in Pneumatic Tire Cavities
BRIDGESTONE EUROPE NV/SA, 2025
A method and system for applying sealing agent to the internal cavity of a pneumatic tire to improve sealing uniformity and reduce weight. The system uses a robot with a movable arm to apply a uniform sealing bead to the internal cavity. It takes into account the actual profile of the cavity and fluctuations in sealing agent flow to provide consistent thickness and width of the sealing bead. This prevents overapplying sealing agent in some areas to compensate for thickness variations. The robot's reciprocating motion applies the bead between the lateral ends of the cavity. This allows adjusting the bead thickness based on the cavity shape. It also compensates for flow variations by applying the bead using the robot rather than a fixed applicator. This improves sealing uniformity compared to conventional methods.
8. Continuous X-Ray Scanning System for Analyzing Longitudinal Quality Variations in Elongated Tire Components
THE YOKOHAMA RUBBER CO LTD, 2025
A method and system for quickly and accurately determining variation in quality of long elongated tire components like belts by continuously scanning them with X-rays as they are conveyed. The system uses an X-ray source to scan a continuous section of the tire component as it moves. The X-ray transmittance images are acquired without gaps in the longitudinal direction. By analyzing the contrast in each image, the system calculates the variation in quality like thickness or compound composition along the length of the component.
9. Tire Component Servicer with Oblique Cutter Bar and Independent Movable Clamping Element
VMI HOLLAND BV, 2025
Servicer for cutting and supplying tire components to a tire building drum or transfer wheel that allows improved quality of the resulting tire. The servicer has a conveyor for transporting the tire component in a specific direction, a cutter bar downstream, and a movable blade on the cutter bar. The blade angle is oblique to the conveyor plane, allowing oblique cuts. A movable clamping element clamps the component near the cutter line. The blade and clamping element can move independently. This allows the component to be clamped and cut closer to the desired shape. The oblique cuts reduce distortion and improve splice quality compared to perpendicular cuts.
10. Automated Flow Control System with Modular Robotic Cells for Rubber Block Handling and Bin Construction
COMPAGNIE GENERALE DES ETABLISSEMENTS MICHELIN, 2025
Automated flow control system for rubber product manufacturing using modular robotic cells to optimize flow of rubber blocks between production installations. The system involves robotic cells with features like weighing, precise positioning, and locking to construct bins of rubber blocks that satisfy production campaigns. Robots pick specific blocks from containers based on parameters like viscosity to match recipes. The system trains itself to recognize block properties and target values. This allows automated construction of optimized bins with consistent block qualities for consistent batches.
11. 3D-Configured Production Structure with Mobile Intelligent Manufacturing Units for Rubber Products
CHENGDU HOLY AVIATION SCIENCE TECHNOLOGY CO LTD, 2025
A 3D-configured production structure for rubber products using mobile intelligent manufacturing units that can be moved and placed in a warehouse for flexible and scalable production. The mobile units contain all necessary components like molds, vulcanization, feeding, collection, and reclaiming. The warehouse has a roadway and shuttle cars to move the units between storage areas. This allows multiple units to be produced simultaneously in different areas and enables flexible capacity adjustment. The units can be moved in and out of the warehouse using conveyors.
12. Machine Learning-Driven Imaging System for Defect Detection in Vehicle Disks
TNSAI CO LTD, 2025
AI-based system for accurately and efficiently detecting defects in vehicle disks using machine learning and imaging techniques. The system involves projecting light at an angle onto moving disks on a conveyor, capturing images, and analyzing them using AI algorithms to determine if the disk is defective. Defective disks are stored separately and non-defective ones are moved to storage. The AI image analysis allows more accurate defect detection compared to manual inspection and shortens production time by quickly separating defective disks.
13. Device with Radially Expanding Frames for Pressing Sound Absorbing Material Inside Tires
KUMHO TIRE CO INC, 2025
A device to uniformly and firmly press sound absorbing material inside tires to reduce tire noise. The device has a fixer to align the tire, a crimping unit with expanding frames, and a motor to lower the crimping unit onto the tire. The frames radially expand to press the inner liner's sound absorber. The expanding frames have connected segments that radially expand/contract. The frames are driven by a servomotor with bevel gears.
14. Automated Tire Carcass Skived Area Detection and Filling System
BRIDGESTONE BANDAG LLC, 2025
Automated system for filling skived areas on tire carcasses during retreading. The system uses a scanner to analyze the tire surface and identify skived areas. It then determines whether to fill those areas and sends instructions to a filling device to do so. This allows efficient, automated skived area filling during tire retreading.
15. Automated Fastener Fixation System with Sliding Gripper and Vacuum Control in Tire Assembly
COMPAGNIE GENERALE DES ETABLISSEMENTS MICHELIN, 2025
Automated system for fixing fasteners with electronic components inside tires. The system has a preparation and fixation installation that allows optimized placement and secure fixation of fasteners inside tires without reducing productivity. The installation has a housing with a fixed and sliding section. The sliding section contains a gripper that engages the fastener center. A deformation actuator moves the gripper between gripping and deforming positions. The installation also has a vacuum control system to hold the fastener. The tire is fed between rollers and a positioning device aligns the fastener. A laser treats surfaces before fixation. The installation trains itself to recognize fastener locations and compare them to targets.
16. Sequential Multi-Station Green Tire Forming and Inspection System with Integrated Drum Transfer Mechanism
THE YOKOHAMA RUBBER CO LTD, 2025
Efficiently forming and inspecting green tires during tire manufacturing by sequentially moving the forming drum to multiple stations, bonding the tire components at each station, temporarily placing the drum with components at an inspection station to check quality during forming or after completion, and then vulcanizing the green tire. This allows continuous production without idle time between stations while still inspecting the green tire quality.
17. Continuous X-Ray Scanning Method for Quality Variation Detection in Longitudinally Bonded Tire Members
THE YOKOHAMA RUBBER CO LTD, 2025
Quickly and accurately determining variation in quality of an elongated tire member formed by bonding multiple constituent materials in the longitudinal direction. The method involves continuously scanning the tire section with X-rays as it moves along a conveyor. The X-ray transmittance images are acquired without gaps to create a continuous sequence. By analyzing contrast in each image, the method determines variation in quality across the tire length.
18. Conveyor System with Recessed Measuring Slot for Edge Detection of Thin Tire Components
VMI HOLLAND BV, 2025
Reliably detecting the edges of thin tire components like inner liners on a conveyor belt using a system with a recessed measuring slot. The belt has a recessed section between the support areas for the component. A sensor views the slot to measure component height. The recessed section prevents false edge detection from belt textures or irregularities.
19. Continuous X-Ray Scanning and Feedback System for Tire Manufacturing Quality Control
THE YOKOHAMA RUBBER CO LTD, 2025
Method and system for manufacturing tires with reduced variation in quality along the longitudinal direction. It involves continuously scanning the tire using X-rays as it's being conveyed, acquiring image data without gaps, calculating quality variation from contrast, and correcting extruder screw speeds based on the variation to even out quality. This allows accurately determining and correcting quality variation without stopping the conveyor or thinning sections.
20. Robotic Automation System for Tire Manufacturing with Movable Drum Stations
THE YOKOHAMA RUBBER CO LTD, 2025
Flexible and efficient method to manufacture tires with robotic automation and movable drum stations. The method involves sequentially moving a forming drum body between workstations using robots and a movable placement device. Tire components are bonded and vulcanized on the moving drum. This allows flexible sequential movement between workstations without rigid conveyors. The drum movement path and workstation selection are optimized for specific tire types.
These developments raise productivity, reduce expenses, and enhance quality. They range from automated inspection systems to sophisticated production processes. These solutions will become even more important as the industry develops to fulfill the demands of the global tire market and remain competitive.
Get Full Report
Access our comprehensive collection of 54 documents related to this technology
Identify Key Areas of Innovation in 2025
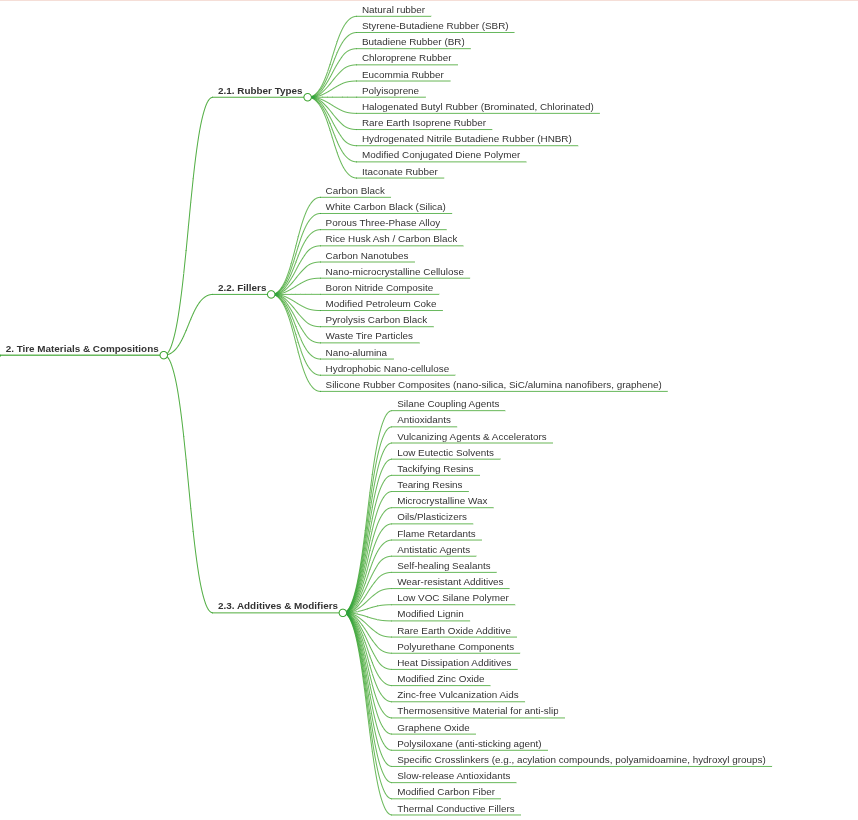