Sidewall Extrusion in Tire Production
Modern tire sidewall manufacturing faces strict demands on durability and heat management, with thermal buildup during operation frequently exceeding 70°C under normal driving conditions. Current extrusion processes must precisely control rubber flow and thickness uniformity while maintaining the careful balance of material properties that determine sidewall performance.
The fundamental challenge lies in achieving uniform material distribution and proper molecular alignment during extrusion while preserving the complex balance of flexibility, durability, and heat resistance required in sidewall compounds.
This page brings together solutions from recent research—including advanced polymer functionalization techniques, shear layer architectures for impact resistance, and innovative mixing sequences for improved processability. These and other approaches focus on practical manufacturing solutions that enhance sidewall performance while maintaining production efficiency.
1. Pneumatic Tire with Integrated Sidewall Gum Layers and Overlapping Bead and Tread Construction
The Goodyear Tire & Rubber Company, 2024
Pneumatic tire with improved durability and reduced sidewall heat generation. The tire has a unique sidewall construction that reduces heat buildup compared to conventional tires. The sidewall gum layers extend inward between the ply turns and the innermost belt edge. This sandwiches the sidewall rubber between the ply turns and innermost belt, preventing bulging and deformation that generates heat. The sidewall rubber overlaps the bead region and tread. This wraps the sidewall rubber around the bead core and tread instead of having separate sidewall parts. This reduces sidewall deformation and heat buildup.
2. Tire with Continuous Internal Stiffening Structure Extending Through Sidewalls, Beads, and Crown
COMPAGNIE GENERALE DES ETABLISSEMENTS MICHELIN, 2024
A tire design with improved durability and longevity. The tire has a unique stiffening structure inside the cavity that extends continuously from the sidewalls through the beads and into the crown. The stiffening elements are anchored in both the inner sidewall/bead reinforcements and the outer crown reinforcements. This prevents peeling and separation of the stiffening elements from the inner surfaces of the beads and crown. The continuous path around the tire helps distribute loads and forces between the sidewalls, beads, and crown to prevent localized failures.
3. Tire with Continuous Stiffening Structure Anchored in Sidewall and Crown Reinforcements
COMPAGNIE GENERALE DES ETABLISSEMENTS MICHELIN, 2024
A tire design with a stiffening structure that improves durability and regularity of the tread contact area. The stiffening structure extends continuously from the sidewalls through the crown. It anchors into inner and outer reinforcing structures in the sidewalls/beads and crown. The anchor points in the ribs prevent flexing and deformation compared to anchoring in cutouts. This prevents separation and wear of the stiffening elements.
4. Low-Temperature Extrusion Process for Wear-Resistant Rubber Compounds in Tire Sidewalls
Sailun Tire Co., Ltd., SAILUN TIRE CO LTD, 2023
Low-temperature extrusion method for making wear-resistant rubber compounds used in tire sidewalls. The method involves extruding the rubber at lower temperatures to reduce heat generation during the process. This prevents excessive temperature rise and improves processing speed compared to extruding at normal temperatures. The lower temperature extrusion allows the rubber to flow properly without overheating, reducing ripening and improving consistency. The lower temperature extrusion also reduces friction and heat generation during the final molding step, preventing excessive temperature rises.
5. Four-Component Sidewall Structure with Integrated Bead Reinforcement for Light Truck Tires
SICHUAN YUANXING RUBBER CO LTD, 2023
A specialized four-component sidewall design for light truck tires that improves bead durability without increasing molding steps. The sidewall has separate hard rubber, main rubber, reinforcing glue, and rubber channels. This allows targeted reinforcement of the bead area without adding layers or strips. The hard rubber prevents bulging, the main rubber provides flexibility, the reinforcing glue holds the bead, and the rubber channels distribute stress. The specialized sidewall design prevents delamination and bead failure in heavy load conditions without increasing molding complexity.
6. Tire Sidewall Extrusion Method with pH-Controlled Cooling Water to Minimize Surface Precipitation
SAILUN GROUP CO LTD, 2023
Reducing air bubbles in tire sidewalls to improve aesthetics by adjusting the cooling water pH during extrusion. The method involves controlling the pH of the cooling water used in the tire sidewall extrusion process. By keeping the pH between 5.5 and 6.5, it prevents blue substance from precipitating on the sidewall surface which can lead to air bubbles. Lower pH values below 5.5 also suppresses blue substance formation but can negatively impact vulcanization speed.
7. Extrusion Die and Extruder with Multi-Outlet Glue Channels and Variable Pitch Screw for Tire Sidewall Manufacturing
DOUBLE COIN GROUP ANHUI HUILI TYRE CO LTD, DOUBLE COIN GROUP HUILI TYRE CO LTD, 2023
Sidewall production extrusion die and extruder for tire sidewall manufacturing that addresses the issue of high extrusion temperature degrading tire performance. The die has three glue outlets, with the upper and lower outlets connected to the same middle outlet. This allows outputting the same glue from the upper and lower while a different glue comes from the middle. The extruder has separate channels for each outlet. The screw channels have a decreasing pitch closer to the die end. This allows lower temperature glue from the middle outlet to mix with hotter glue from the upper and lower outlets, reducing overall extrusion temperature.
8. Tire Sidewall Double Extrusion Die Plate with Overlapping Glue and Rubber Channels
SHANDONG WANDA BOTO TIRE CO LTD, WANDA GROUP CO LTD, 2023
Tire sidewall double extrusion die plate for manufacturing tires with improved quality and efficiency, particularly for smaller tire widths. The die plate has separate glue and sidewall rubber extrusion channels that overlap in the middle. This allows simultaneous extrusion of the glue and sidewall rubber, avoiding scorching issues and improving efficiency compared to sequential extrusion. The glue channels are on the top and bottom of the plate, with the overlapping sidewall rubber channels on the left and right sides.
9. Extrusion Die with Segmented Structure for Radial Tire Tread Formation
SALT CITY HENGTAI RUBBER CO LTD, 2022
Optimizing the design of extrusion dies for radial tire production to reduce swelling and distortion of the extruded tread. The die is divided into sections with specific lengths and cross-sectional areas. These parameters are varied through orthogonal testing to find the optimal die shape for minimizing extrusion swelling. The sections include a fluid extrusion segment, constant section, expanding diameter section, and pre-die segment connected to the mold.
10. Method for Controlling Rubber Extrusion Shape Via Temperature-Adjusted Base
TOYO TIRE CORP, 2021
A method for manufacturing rubber products like tire beads with improved shape control. The method involves heating or cooling the base that receives the extruded rubber to alter the flow velocity of the rubber. This compensates for the natural curvature that occurs when extruding into thin sections. By changing the rubber's velocity before discharge, the base can be used to fine-tune the shape of the rubber product. This eliminates the need to manage the opening size of the extruder die, which is difficult to control accurately. By temperature-controlling the base, the shape of the rubber can be adjusted without requiring active mechanical adjustments.
11. Rubber Extrusion Device with Sliding Control Plate for Adjustable Fluid Flow Distribution
THE YOKOHAMA RUBBER CO LTD, 2020
A rubber extrusion device and method to control the shape of extruded rubber parts by adjusting the fluid flow distribution. The device has a sliding control plate between the extrusion head and die. By moving the plate, the position of the flow connection between the extrusion path and adjustment path can change. This alters the pressure distribution and prevents unwanted curvature of the extruded rubber when passing through the flow paths. The sliding plate allows fine tuning of the flow configuration to counteract any natural curvature tendencies of the specific rubber compound being extruded.
12. Method for Producing Rubber Profiles with Controlled End Shaping via Variable Speed Extrusion and Tapered Transitions
CONTINENTAL REIFEN DEUTSCHLAND GMBH, 2020
A method to produce rubber profiles, like reinforcement profiles for tire sidewalls, that have precisely shaped ends without defects. The method involves extruding the profile sections separately with different speeds, shaping templates, and taper transitions. This allows the side outlet sections to be extruded first at a slower speed, then the core section at a faster speed. The taper transition at the side outlet opening helps prevent cracking. The final profile is formed using an end template.
13. Rubber Extrusion Base with Cone-Cylindrical-Rear Section and Axial Adjustability
SUMITOMO RUBBER IND, SUMITOMO RUBBER IND LTD, 2020
A rubber extrusion base and molding method for extruding tubular rubber with improved surface quality and workability, especially when using rubber compositions with poor compatibility. The extrusion base has a unique shape with a cone-shaped front end, a cylindrical center section, and a larger diameter rear section. This design provides a larger cross-sectional area for the rubber to flow through, preventing excessive friction and heat buildup that can cause skin defects. The base can be adjusted axially to fine-tune the extrusion process. The method involves maintaining the temperatures of the extruder screw, cylinder, and base around 60-110°C, and using the optimized extrusion base shape. This allows extruding rubber compositions with poor compatibility without issues like uneven skin or surface defects.
14. Pneumatic Tire with Thick Sidewall and Protrusion for Rim, and Method for Controlled Vulcanization
Yokohama Rubber Co., Ltd., 2018
Pneumatic tire design and manufacturing method to reduce rubber entrainment and prevent cracks. The tire has a thick sidewall with close-to-final shape side rubber near the bead. This prevents rubber flow during vulcanization that can cause cracks. The thick sidewall section has a protrusion for the rim. The tire is molded green with an unvulcanized side rubber member matching the shape. Vulcanizing in a mold with recesses matching the protrusion shape prevents rubber entrainment there. Measuring rubber thickness at multiple points on the green and vulcanized tires with a correlation coefficient over 0.6 reduces widespread rubber flow during vulcanization.
15. Extruder with Die and Cord Guide Featuring Adjustable Cord Positioning and Integrated Heating Elements
VMI HOLLAND BV, 2017
Extruder and method for extruding cord reinforced tire components that improves flexibility in positioning of the cord within the tire component. The extruder head has a die for receiving extruded material and a cord guide to insert the reinforcement cord into the die. The die cross-section profile has a height. The cord guide has a heating element to guide the cord into the die at a specific height relative to the profile height. The extruder also has heating elements on the die side to transfer heat into the extruded material from that side. This allows precise control over cord embedding depth in the die cross-section, enabling adjustment of cord position in the final tire component.
16. Integrated Extrusion Method for Pneumatic Tire Apex and Sidewall Formation
SUMITOMO RUBBER IND, SUMITOMO RUBBER IND LTD, Sumitomo Rubber Industries, Ltd., 2017
A method for manufacturing pneumatic tires with improved quality and reduced defects by integrating the outer apex, sidewall, and clinch apex during tire production. Instead of separately molding and joining these components, the outer apex, sidewall, and clinch apex are extruded together. This prevents steps and air pockets between the apexes that can form during separate molding and joining. The apex material has higher hardness and viscosity than the sidewall to aid dispersion during mixing. By integrating the apexes, it allows reusing the entire molded rubber instead of separating and recycling specific components.
17. Mold Die with Separate Pre-Formers and Direct White Rubber Passage for Tire Sidewall Extrusion
HANKOOK TIRE CO LTD, 2016
A mold die for extruding sidewalls of tires with improved white sidewall quality and reduced weight. The die has separate pre-formers and final dies for extruding the sidewall rubber. The white sidewall rubber passage is connected directly from the pre-former to the final die, bypassing the main die cavity. This allows the white rubber to be extruded separately and contactlessly from the main rubber. This prevents separation issues and weight reduction compared to extruding the white rubber in the main cavity. The white rubber is combined with the main rubber at the final die. The die also has separate passages for the sidewall rubber and rim cushion rubber.
18. Tire Sidewall Manufacturing Process with Differential Hardness Rubber for Bead Area
JIANGSU GENERAL SCIENCE TECH CO LTD, JIANGSU GENERAL SCIENCE TECHNOLOGY CO LTD, 2016
A process to avoid fractures in the sidewall rubber of tires that can occur during the manufacturing process. The process involves three steps: 1) Extruding the sidewall rubber through a die plate to form the desired shape. 2) Crimping the extruded rubber onto a mold. 3) Curing the rubber to harden it. The key innovation is to use lower hardness sidewall rubber for the bead area compared to the rest of the sidewall. This prevents fractures at the bead due to the higher hardness of the clinch rubber in that area. By reducing the hardness at the bead, it matches the flexibility of the adjacent sidewall rubber, avoiding the mismatch that causes fractures.
19. Tire Sidewall with Opposing Shear Layers Composed of Diene Elastomers
Michelin Recherche et Technique S.A. a corporation, 2011
Tire sidewall architecture to mitigate damage from pinch shock during severe impacts. The tire has shear layers in the shoulder and bead sections that oppose each other when the tire is pinched. This prevents cord breakage in the carcass layer from the sidewall buckling during pinch shock. The shear layers are made of softer, highly unsaturated diene elastomers compared to the carcass layer. This allows deformation of the shear layers without breaking the carcass cords when the tire pinches.
20. Rubber Composition with Sulfenamide Accelerator Featuring Branched Alkyl Group for Tire Bead Fillers and Sidewalls
BRIDGESTONE CORPORATION, 2011
Rubber composition with improved elasticity and adhesion for tire bead fillers and sidewalls. The composition contains a specific sulfenamide-based vulcanization accelerator, a phenolic resin, a methylene donor, and sulfur. The sulfenamide accelerator has a particular structure with a branched alkyl group on the sulfenamide nitrogen. This accelerator, along with the phenolic resin and methylene donor, enhances elasticity while maintaining adhesion compared to using conventional accelerators. The accelerator structure balances vulcanization rate and adhesion properties.
Get Full Report
Access our comprehensive collection of 22 documents related to this technology
Identify Key Areas of Innovation in 2025
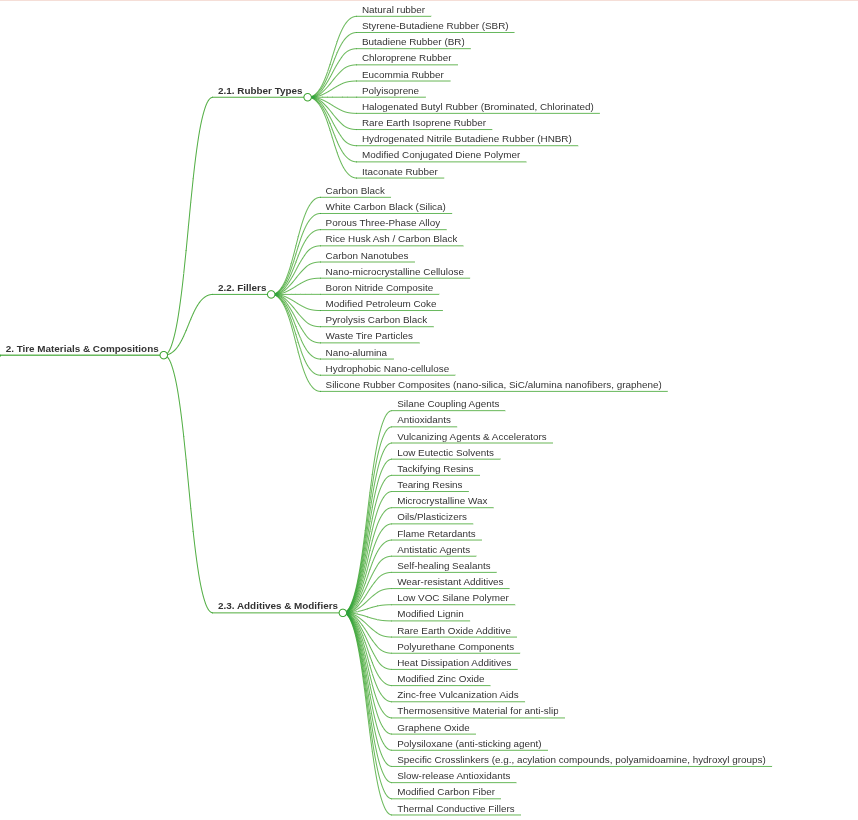