Pyrolysis Oil Separation from Recycled Tires
Pyrolysis oil from waste materials contains hundreds of chemical compounds distributed across wide boiling point ranges (40-550°C), making efficient fractionation challenging. Current industrial processes achieve oil yields of 45-50% by weight, but the heterogeneous nature of feedstocks leads to significant variations in chemical composition and physical properties between batches.
The core challenge lies in developing selective separation techniques that can isolate valuable chemical compounds while managing the complex interactions between different oil fractions and contaminants.
This page brings together solutions from recent research—including two-stage pyrolysis systems, low-temperature fractional distillation for limonene recovery, vacuum-assisted separation techniques, and methods for producing high-quality carbon black as a co-product. These and other approaches focus on maximizing the commercial value of pyrolysis oil fractions while ensuring consistent product quality.
1. Continuous Refining Process for Waste Plastic Pyrolysis Oil with Isodewaxing and Dual-Stage Hydrotreating Using Weak Acid Catalysts
SK ENERGY CO LTD, SK INNOVATION CO LTD, 2024
A continuous refining process for waste plastic pyrolysis oil that reduces impurities, improves quality, and mitigates process issues. The process involves three steps: 1) isodewaxing to improve pour point, 2) hydrotreating to remove chlorine and nitrogen, and 3) further hydrotreating to further reduce impurities. The process uses weak acid catalysts and specific temperature ranges in each step to optimize reactions without excessive side effects. The continuous refining device with reactors allows scaling up the process for commercial applications.
2. Refining Process for Producing High-Quality Light Oil from Pyrolysis Oil Through Pre-Treatment, Heavy Oil Stripping, Hydrocarbon Cracking, Fractional Distillation, and Filtration
CHO SANG TAE, 2023
Refining high-quality light oil from pyrolysis oil to make it versatile as fuel. The process involves pre-treating the pyrolysis oil to remove impurities, stripping out heavy oil, cracking the remaining hydrocarbons, fractionally distilling the cracked oil, and filtering the final light oil to purify it. This refining method converts pyrolysis oil into high-quality light oil suitable as a general-purpose fuel.
3. Pyrolysis Oil Fractionation with Catalyst Bed Dehydrohalogenation, Decontamination, and Hydrogenation
CHEVRON PHILLIPS CHEMICAL COMPANY LP, 2023
Fractionating pyrolysis oil into useful products like gasoline, distillate, heavy oil, and fuel gas while removing contaminants like halogens and metals. The process involves dehydrohalogenation, decontamination, and hydrogenation in a treatment catalyst bed above the pyrolysis oil inlet. The treated oil is then fractionated into light, middle, heavy, and bottom streams. The light stream is condensed to produce gasoline and fuel gas. The middle stream is stripped to make distillate. This allows extracting valuable components like gasoline while removing undesirable ones like halogens and metals.
4. Waste Plastic Pyrolysis Oil Separation with Raffinate and Extract Stream Processing
EASTMAN CHEMICAL CO, 2023
Optimizing recovery of recycled content products from waste plastic pyrolysis by separating and sending specific streams to downstream processing facilities like crackers. The process involves pyrolyzing waste plastic to produce a pyrolysis oil stream. Some of the oil is separated into a depleted raffinate stream and an enriched extract stream. The raffinate is sent to the cracker, while the extract is further processed. This allows recovering valuable aromatics and diolefins from the pyrolysis oil upstream of the cracker, improving recycled content product yield compared to direct feeding the pyrolysis effluent.
5. Refining Process for Waste Plastic Pyrolysis Oil Using Sequential Hydrotreating and Hydrocracking with Variable Pressure and LHSV Control
SK Innovation Co., Ltd., SK Geo Centric Co., Ltd., 2023
Refining waste plastic pyrolysis oil to produce high value-added hydrocarbon oil with a high content of naphtha and kerosene. The refining process involves hydrotreating the waste plastic pyrolysis oil in a first reactor region to remove impurities like nitrogen, chlorine, and olefins. Then, the hydrotreated oil is further hydrocracked in a second reactor region to produce naphtha and kerosene. The two reaction zones are separated and operated at lower pressures and optimized LHSV ratios to maximize naphtha/kerosene yields.
6. Dual Reactor System for Refining Waste Plastic Pyrolysis Oil with Staged Hydrotreating and Hydrocracking
SK Innovation Co., Ltd., SK Geo Centric Co., Ltd., 2023
Refining waste plastic pyrolysis oil to produce high value-added hydrocarbon oil with high naphtha and kerosene content. The refining process involves two reactors in series. In the first reactor, the waste pyrolysis oil and hydrogen react to remove impurities. In the second reactor, the oil from the first reactor is split into two regions. In the first region, secondary hydrotreating removes further impurities. In the second region, hydrocracking converts the oil into naphtha and kerosene. The dual reactor setup with staged hydrotreating and hydrocracking allows efficient impurity removal and high naphtha/kerosene yield from waste pyrolysis oil.
7. Process for Producing Fuel from Waste Rubber Pyrolysis Oil with Enhanced Stability and Defined Flash Point
CIRCTEC LTD., 2023
A process to make fuel products from waste rubber pyrolysis oil with improved stability and flash point for marine fuels. The process involves pyrolyzing waste rubber like tires to extract an oil. The oil is then separated to remove solids and further processed to obtain a fuel product with specific properties. The fuel has a flash point above 40°C, low boiling point, low density, low acid number, low styrene, and low halogen content. This fuel can be blended into marine fuels to improve stability without the need for expensive specialized storage and transportation equipment.
8. Purification Method for Liquid Pyrolysis Oil from Waste Plastic Using Extraction, Adsorption, or Precipitation to Remove Heterogenates
INDAVER PLASTICS2CHEMICALS, UNIV ANTWERPEN, UNIVERSITEIT ANTWERPEN, 2023
Method to purify liquid pyrolysis oil from waste plastic without fouling and instability issues. The method involves pyrolyzing the plastic to produce a gaseous pyrolysis product. This is then condensed into liquid pyrolysis oil fractions. Next, the fractions are further purified by removing heterogenates using extraction, adsorption, or precipitation. This results in stable, clear, and unsaturated pyrolysis oil fractions that can be used for chemical applications without fouling issues. The purification steps avoid problems like fouling, filming, and gelling that can occur in the raw pyrolysis oil.
9. Biomass Pyrolysis Oil Fractionation via Solvent-Anti-Solvent Phase Separation and Liquid-Liquid Extraction
ALDER ENERGY, LLC, 2022
A process for fractionating biomass pyrolysis oil into two distinct phases: a hydrophobic aromatic fraction (HAF) and a concentrated aqueous solution of water soluble organics. The fractionation uses solvent/anti-solvent concepts to quantitatively separate the hydrophobic and hydrophilic components in pyrolysis oil. The process involves phase separation of pyrolysis oil using a solvent that selectively extracts the hydrophobic aromatic fraction. The solvent is then distilled to recover it along with the aromatic fraction. The aqueous phase is further processed by liquid-liquid extraction with solvents to extract and recover water soluble organics like pyrolytic sugars and low molecular weight phenolics. This allows selective extraction of valuable components from pyrolysis oil for various applications like fuel,
10. Process for Concurrent Production of Un-Hydrogenated and Hydrogenated C9+ Hydrocarbons from Pyrolysis Gasoline
SABIC Global Technologies B.V., 2022
Process to produce both un-hydrogenated and hydrogenated C9+ hydrocarbons from pyrolysis gasoline. The process involves separating the pyrolysis gasoline stream to produce a first stream containing primarily un-hydrogenated C9+ compounds. A portion of the un-hydrogenated stream is hydrogenated to produce hydrogenated C9+ compounds in a separate step. This allows concurrent production of both un-hydrogenated and hydrogenated C9+ hydrocarbons.
11. Fractionated Hydroprocessing System for Mixed Waste Plastic Pyrolysis Oil
CLEAN PLANET ENERGY, 2021
Upgrading mixed waste plastic pyrolysis oil to make it suitable for use as a diesel fuel. The process involves hydroprocessing the pyrolysis oil in a section with separate units for heavy, middle, and light fractions. The fractions are dynamically adjusted based on desired diesel properties and fed to the corresponding units. This allows customization of the upgrading conditions for each fraction to optimize conversion and improve the overall product quality.
12. Thin-Film Distillation Process for Fractionation of Pyrolysis Oil from Tire Pyrolysis
RJ LEE GROUP INC, 2021
Efficient and effective methods for separating pyrolysis oil from tire pyrolysis into commercially desirable fractions and a fuel oil fraction. The methods involve initial thin-film distillation to separate a lighter fraction and a heavier fraction. The lighter fraction is further fractionally distilled to obtain improved quality products. The heavier fraction is processed to remove sulfur and nitrogen for use as a fuel oil. The thin-film distillation allows stable separation of the fractions due to low wall temperatures. Vacuum thin-film distillation at 100-400 torr further improves separation.
13. Pyrolysis-Derived Fuel Extraction from Waste Rubber with Dual-Product Separation
YANCHEP TECH LTD, YANCHEP TECHNOLOGY LTD, 2021
Extracting fuel products from waste rubber like tires through pyrolysis and separation to produce valuable fuel compositions. The pyrolysis of waste rubber produces an oil with high levels of black carbon. This oil is then separated to extract two fuel products. One product is a low-density, low-sulfur fuel with low halogen content and low aromatic content. The other product is a high-density fuel with high aromatic content. The low-density fuel has properties suitable for commercial use as a fuel while simultaneously satisfying requirements like low flash point, low sulfur, low halogen, and low aromatic content. This allows using it in tanks, vessels, and equipment without the need for post-use cleaning due to the black color. The high-density fuel has high aromatic content and can be used as a boiling stock.
14. Device for Fractional Separation of Pyrolysis Oil with Funnel-Shaped Sedimentation and Cylindrical Collection Sections
KOREA INST ENERGY RES, KOREA INSTITUTE OF ENERGY RESEARCH, 2020
Device and method for separating and recycling pyrolysis oil from waste plastic to obtain high-value oil. The device has a funnel-shaped sedimentation section and cylindrical collection section connected to an injection section. Pyrolysis oil is injected, separates into low-boiling and high-boiling fractions, and the low-boiling fraction is recycled back to the pyrolysis reactor. This removes wax and high-boiling residues from the pyrolysis oil. By recycling the low-boiling fraction, the pyrolysis reactor receives oil with less contaminants for better conversion. The device can be connected to multiple pyrolysis reactors for cascading.
15. Method for Fractionating Pyrolysis Oil Using Sequential Steam and Fractional Distillation
RJ LEE GROUP, INC., 2019
A cost-effective and efficient method to extract valuable fractions from pyrolysis oil derived from recycled tires. The method involves an initial steam distillation followed by fractional distillation. In the steam distillation, the pyrolysis oil is separated into a lighter fraction containing high value compounds like limonene and a heavier fraction. The lighter fraction is further distilled to isolate commercial products. The heavier fraction can be used as a solvent, fuel oil, or feedstock for further processing. The steam distillation allows separation of the high value compounds without exposing them to high temperatures that decompose them.
16. Biomass Pyrolysis Oil Stabilization and Fractional Distillation Process
FUTURE BLENDS LTD, 2016
Integrated process for upgrading biomass pyrolysis oil into useful transportation fuels and chemicals. The process involves stabilizing the pyrolysis oil with additives like alcohols, distilling it under reduced pressure to separate water and light fractions, then further distilling the stabilized oil to separate a heavy fraction. This provides a dewatered oil with improved stability, reduced acidity, and higher heating value for fuel applications. The water-rich light fraction can be recycled as solvent for further pyrolysis. The heavy fraction has higher heating value and viscosity for fuel blending.
17. Apparatus and Method for High Temperature Pyrolysis of Tires and Oil with Simultaneous Decomposition
KOREA ENERGY RESEARCH INST, KOREA ENERGY RESEARCH INSTITUTE, 1993
A method and apparatus for thermally decomposing waste tires and waste oil simultaneously to recover oil and reduce environmental pollution. The tires and oil are pyrolyzed at high temperatures to yield oil, gas, and carbon black. This simultaneous processing increases tire oil recovery and reduces environmental impacts compared to separate processing. The high temperature pyrolysis avoids the low oil yield issues of lower temperature tire pyrolysis. The resulting oil has similar properties to diesel. The heavy metals remain in the residue, allowing its reuse as an asphalt additive.
18. Pyrolysis Process for Extracting High-Value Chemicals and Enhanced Carbon Black from Used Tires
UNIV LAVAL, UNIVERSITE LAVAL, 1993
Recovering valuable products from used tires through pyrolysis. The process involves pyrolyzing tire material at high temperatures (490-510°C) and low pressures (<5 kPa) to extract commercially valuable chemicals, like paraffins, naphthenes, olefins, and aromatics, from the pyrolysis oils. It also yields carbon black with high iodine adsorption numbers (130-150 mg/g) compared to regular tire carbon black. This is achieved by increasing the reactor bed temperature to 500°C while maintaining low pressure. The pyrolysis process also recovers a distillation fraction boiling below 204°C containing paraffins, naphthenes, olefins, and aromatics. This fraction contains unexpected compounds like limon
19. Fractional Distillation Method for Isolating Hydrocarbons and Terpenes from Tire Pyrolysis Oil
UNIV LAVAL, UNIVERSITE LAVAL, 1993
Separating valuable chemicals from tire pyrolysis oil through distillation. The method involves fractional distillation of tire pyrolysis oil at temperatures below 204°C to isolate paraffins, naphthenes, olefins, and aromatics. This distillation fraction also contains dl-limonene, a terpene compound. Further distillation at 178°C isolates pure dl-limonene.
20. Pyrolysis System for Extracting Rubber Oil and Carbon Black from Automobile Tires
MUNGER JOSEPH H, MUNGER; JOSEPH H, 1992
Recycling used automobile tires by pyrolysis to extract a reusable rubber oil and carbon black. The pyrolysis involves heating the tires in an oxygen-limited atmosphere to generate recoverable products. The recovered rubber oil has similar properties to fuel oil but contains hazardous chemicals that limits its commercial viability. The carbon black has an ash content too high for tire applications. The invention aims to demonstrate the feasibility of recycling tires by pyrolysis by showing that the rubber oil can be used as a reusable rubber extender/plasticizing agent. The tests show that the rubber oil derived from tire pyrolysis can be used as a rubber extender/plasticizer at similar levels to standard extender/plasticizers, despite not being specifically engineered for that purpose.
Get Full Report
Access our comprehensive collection of 28 documents related to this technology
Identify Key Areas of Innovation in 2025
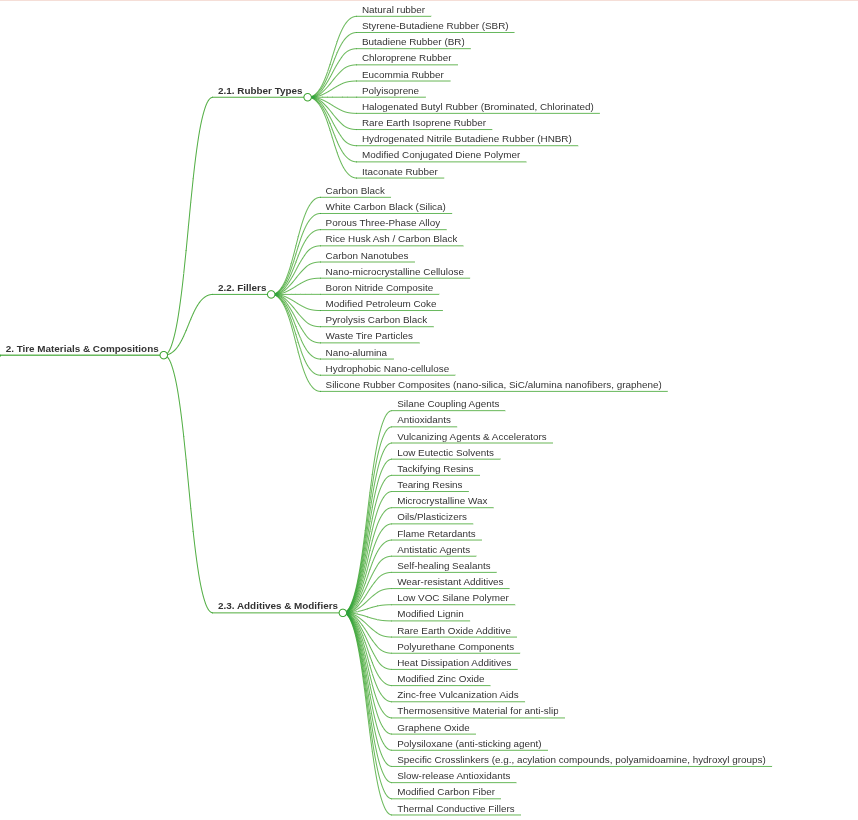