Retreading to Extend Tire Lifespan
Tire retreading represents a significant opportunity for resource conservation, with each remanufactured tire saving approximately 15 gallons of oil and 40 pounds of rubber compared to new tire production. Current retreading processes face technical challenges in achieving consistent bond strength between the new tread and carcass, managing heat distribution during vulcanization, and ensuring uniform wear patterns across the retreaded surface.
The fundamental engineering challenge lies in maintaining the structural integrity of the tire-tread interface while optimizing the vulcanization process for both durability and cost-effectiveness.
This page brings together solutions from recent research—including precision-controlled vulcanization processes, innovative joint geometry designs, selective section replacement techniques, and pre-cured tread applications. These and other approaches focus on extending tire lifespan while meeting stringent safety and performance requirements for commercial and passenger vehicles.
1. Predictive Modeling for Sustainable Tire Retreading and Resource Optimization in Public Transport System
anto joseph, n nedunchezhian, muthuraj ramasamy - Multidisciplinary Digital Publishing Institute, 2025
Retreading is a cornerstone in the remanufacturing process of tires, facilitating extraction maximum kilometers (Km) from tire carcass. Tire plays crucial role conserving raw materials, reducing environmental impacts, and lowering overall operating costs. This study employs predictive modeling techniques to forecast performance optimize resource allocation, departing traditional approaches, for bus transport system India. Machine learning models, including linear regression, ensemble boosted trees, neural network were used. Two scenarios devised: Scenario I addressed premature failures optimizing reduce procurement II used targeted interventions, such as eliminating new condemnations retread (RT) strategies, could potentially salvage 169 tires retirement. The results achieved R2 values 0.44, 0.51, 0.45 improved test datasets 0.46, 0.52 0.44. By leveraging these decision-makers can substantially improve mileage, condemnations, increase production, drive cost savings fleet operations. Notably, this approach contributes enhanced operational efficiency promotes sustainability by cutting ... Read More
2. Method for Assessing Retreadability of Worn Tires via Separate Evaluation of Chemical and Physical Degradation
BRIDGESTONE CORP, 2025
Accurately determining whether a worn tire can be retreaded by separately evaluating chemical and physical degradation. The method involves acquiring state characteristic values indicating the tire condition, then making a first determination using the base tire's remaining durability based on rubber degradation. If retreadable, a second determination is made using the base tire's remaining durability based on physical damage. This two-step process allows more accurate assessment of tire condition for retreading by separately evaluating chemical and physical degradation.
3. Retread Tire with Inner Edge Dimples for Enhanced Tread Adhesion
SUMITOMO RUBBER INDUSTRIES LTD, 2025
Retread tire with improved durability to prevent separation of the recapped tread from the base tire. The retread has a recapped tread with dimples on the inside edge that extends into the tread. The dimples have a maximum diameter of 2-5 mm and depth of 1-3 mm. These dimples help prevent separation by absorbing and dissipating heat generated during driving, reducing the risk of the tread separating from the base tire.
4. Preformed Tread Segments with Shortened End Sections for Consistent Tire Retreading Splices
BRIDGESTONE BANDAG LLC, 2025
Reducing waste and improving splicing consistency in retreading tires by optimizing the length of preformed tread segments. The segments are cut from a mold with specialized end segments that have shorter length compared to the main segments. This reduces the amount of tread that needs to be removed from the ends during retreading to provide a suitable splice face. It eliminates waste from excess material that would be cut off during splicing.
5. Retreaded Tire with Dimpled Shoulder Circumferential Groove and Narrow Shoulder Lateral Grooves
Sumitomo Rubber Industries, Ltd., 2024
Retreaded tire with improved resistance to tread peeling off the base tire, especially at the shoulder regions. The retreaded tire has a tread rubber with a shoulder circumferential groove adjacent to the tread edge. This groove has a surface with multiple dimples. The dimples reduce heat buildup in the shoulder area during driving, preventing peeling. The tread also has narrow shoulder lateral grooves opening on the ground contacting surface and buttress surface. This configuration further reduces heat generation and peeling at the shoulder.
6. Retread Tire with Dimpled Buttress Surface on Recapped Tread
SUMITOMO RUBBER IND, SUMITOMO RUBBER INDUSTRIES LTD, 2024
Retread tire with improved resistance to separation of the recapped tread from the base tire, especially at high temperatures during driving. The retread has a recapped tread with a buttress surface extending inward from the tread edge. This buttress surface has a pattern of dimples with specific size and depth ranges. The dimples help prevent separation by dissipating heat and reducing stress concentration at the tread-base interface.
7. Automated Molding Process for Retread Tire Manufacturing with Tread Extrusion and Rubber Application Mechanism
HANYONG TIRE CO LTD, 2024
Method for manufacturing retread tires using an automated molding process to improve quality, reduce costs, and enable customization compared to manual retreading. The process involves preparing a buffed tire, designing the tread extrusion shape based on the buffed tire profile, mapping it, calculating the required rubber amount, mounting the buffed tire in a rotating fixture, attaching the calculated rubber strip using an applicator calendar, inserting and molding in the curing mold, then removing the retreaded tire.
8. Retreading Method Utilizing Pre-Vulcanized Composite Treads with Cold Adhesive Bonding
TIPTOP RUBBER TECHNOLOGY CO LTD, TIPTOP TIANJIN RUBBER TECH CO LTD, 2024
Method for retreading tires using pre-vulcanized composite treads to reduce energy consumption and cost compared to traditional hot retreading. The method involves washing and inspecting the tire carcass, repairing any damage, then bonding a pre-vulcanized composite tread directly to the carcass using cold adhesive. The composite tread has layers like crown, transition, wing, and bottom. The pre-vulcanized tread is made by extruding or calendering the layers at temperatures below 100°C. This allows the tread to be attached at room temperature rather than vulcanizing the entire tire.
9. Multi-Step Tire Retreading Process Involving Inspection, Milling, Repair, Polishing, Vulcanization, and Testing
HEILONGJIANG INST TECH, HEILONGJIANG INSTITUTE OF TECHNOLOGY, 2023
Method for retreading large tires that extends the life of tires by selectively repairing and reusing them instead of replacing them when worn. The method involves a multi-step process to inspect, mill, repair, polish, vulcanize, and test the tires. It starts with an initial inspection to determine if the tire can be retreaded based on factors like exposed wire, damage beyond manufacturer limits, or contamination. If the tire passes, it's milled to expose the carcass, repaired, polished, vulcanized with a new tread, and inspected again. This allows selective retreading of tires that still have good carcasses instead of premature scrapping.
10. Retreading Method for Waste Solid Tires with Damage-Based Classification and Carbon Fiber Powder Integration
HEILONGJIANG INSTITUTE OF TECH, HEILONGJIANG INSTITUTE OF TECHNOLOGY, 2023
Retreading method for waste solid tires that improves efficiency, utilization rate, and performance of retreaded tires. The method involves classifying waste solid tires based on damage levels before retreading. This allows shorter retreading times for less damaged tires versus longer times for severely worn tires. During retreading, carbon fiber powder is added to the tire core bonding process to enhance strength and rigidity of the retreaded tire.
11. Cold Retreading Method Utilizing Conductive Cushioning Pads for Radial Pressure Application
Bridgestone Europe NV/SA, BRIDGESTONE EUROPE NV/SA, 2023
Cold retreading method for tires that allows high productivity and safety compared to traditional cold retreading without using autoclaves or envelopes. The method involves using cushioning pads with specific composition during the curing step. The cushion pads contain conductive materials like graphite, graphene, or carbon black. These pads are connected to a heat or power source during curing to provide radial pressure on the tire instead of using autoclaves. This eliminates the need for internal pressures, complex envelopes, and autoclave safety.
12. Low-Temperature Tire Retreading Using Halogenated Primer and Urethane Adhesive
Bridgestone Americas Tire Operations, LLC, 2023
Retreading tires at lower temperatures by priming the rubber surfaces with a treatment composition before adhering them with a urethane adhesive. The treatment composition contains a halogenating agent and solvent like water or alcohol. Applying multiple coating layers of the treatment enhances adhesion when cured. The primed rubber components are then sandwiched together with the urethane adhesive at lower temperatures for retreading. The low-temperature curing is enabled by the priming process.
13. Retreading Process Utilizing High-Pressure Diaphragm Inflation for Enhanced Tire Uniformity
MEDINA MED OOD, 2023
Retreading heavy duty tires with improved quality and longevity by inflating the diaphragm inside the tire to 15 bar before retreading. This eliminates air pockets between the diaphragm and tire inner surface that can deform the diaphragm during retreading and cause premature failure. The inflated diaphragm provides consistent pressure for optimal vulcanization of patches and uniform thickness of the retreaded tire.
14. Truck Tire with Retread-Compatible Tread Pattern and Angled Reinforcing Belt Cables
AMERICAN TIRE ENG INC, AMERICAN TIRE ENGINEERING INC, 2023
Truck tire design optimized for retreading to maintain performance and durability when the original tread wears out. The tire has a specific tread pattern for the drive wheels of a truck tractor that can be retreaded without compromising safety or longevity. The tire also has reinforcing belts with cables oriented at a specific angle to the tire circumference. This optimized tread and belt construction allows retreading while preserving the functional and structural cooperation between the tread and tire casing.
15. Tire Retreading Method Using Ambient Temperature Curing with Moisture Reservoir
BRIDGESTONE BANDAG LLC, 2022
Retreading tires without a curing chamber to enable tire retreading in remote locations. The method involves applying a primer to the inner surface of the tread and outer surface of the tire carcass, then applying an adhesive to the primed surfaces. The tread is attached to the carcass, and a moisture reservoir is placed around the tread. The assembly is enclosed in an envelope and left to cure at room temperature using the moisture in the reservoir. This allows retreading without a curing chamber or furnace.
16. Retreading Method Using Carbon Nanotube-Reinforced Resin Glue with Tannic Acid and Silane Coupling Agent
JIANGSU YISHENG INVEST GROUP CO LTD, JIANGSU YISHENG INVESTMENT GROUP CO LTD, 2022
Retreading method for tires to improve wear resistance and extend tire life when retreading worn tires. The method involves using a reinforced resin glue with carbon nanotubes, tannic acid, and an organic silane coupling agent. The carbon nanotubes improve hardness and wear resistance. The reinforced resin glue is applied to retread the tire. The specific composition of the reinforced resin glue is: epoxy resin, white carbon black, neoprene, vulcanizing agent, and vulcanization accelerator. The carbon nanotubes make up 1.8-2.6% of the reinforced resin glue. The carbon nanotubes are dispersed in ethanol along with tannic acid and the silane coupling agent in a ratio of 15:3-4:1.
17. Method for Attaching Annular Tread Segments to All-Steel Radial Tire Carcasses Using Adhesive Film Lamination
QUZHOU TAIZHOULUN TYRE RENOVATION CO LTD, 2022
Production process for retreading all-steel radial tires that improves retread durability and reduces failures compared to traditional retread methods. The process involves attaching a new annular tread segment to the worn tire carcass using a unique technique. The steps are: 1. Clean and prepare the worn tire. 2. Cut a new annular tread segment from natural rubber with super wear-resistant furnace black reinforcement. 3. Apply an antioxidant to the tread segment. 4. Attach the tread segment to the tire using a special adhesive film lamination process. 5. Cut the film at the ends to create a clean, angled joint between the old and new rubber. 6. Cure the retread tire to bond the new tread segment securely. This process provides a more consistent retread shape, reduces joint failures, and impro
18. Cold Retreading Method Utilizing Conductive Adhesive Compound with Integrated Heat Transmission
Bridgestone Europe NV/SA, 2022
Cold retreading method for tires that allows faster and safer retreading compared to existing methods. The method involves using a conductive adhesive compound between the retread strip, cushion, and casing during curing. The compound contains 5-20% conductive material like graphene, graphite, or high surface area carbon black. This compound is connected to a heat source or power source during curing to transmit heat to the cushion. This eliminates the need for envelopes and autoclaves to compress the retread strip during curing, improving productivity and safety compared to existing cold retreading methods.
19. Tire Retreading Method Utilizing Cured Rubber Component with Functional Polymer-Based Cushion Gum
Bridgestone Americas Tire Operations, LLC, 2022
Retreading a tire in order to extend the life of tires. The retreading process involves providing a tire casing, providing a cured rubber component having first and second planar surfaces, where the first planar surface includes a tread pattern, providing a cushion gum, wherein the cushion gum is a composition including a functional polymer including at least one functional group, and a crosslinking agent including at least two moieties that will react with the functional group of the functional elastomer.
20. Manufacturing Method for Retread Tires Using Sequential Adhesive Element Application and Electron Beam Curing
SUMITOMO RUBBER IND, SUMITOMO RUBBER IND LTD, 2021
Method for manufacturing retread tires that allows reuse of worn tires with uneven treads. The method involves forming an adhesive layer on the worn tire's outer surface before attaching the new tread. The adhesive layer is applied by sequentially placing small adhesive elements on the tire surface. This ensures the adhesive coverage matches the uneven worn surface. The tire is then rotated while attaching the new tread, pressing it against the base tire with a roller. This ensures full contact between the new tread and base tire, even with the uneven worn surface. After attaching, the tire is irradiated with an electron beam to cure the adhesive. This joins the base tire and retread securely, promoting retread longevity.
Get Full Report
Access our comprehensive collection of 124 documents related to this technology
Identify Key Areas of Innovation in 2025
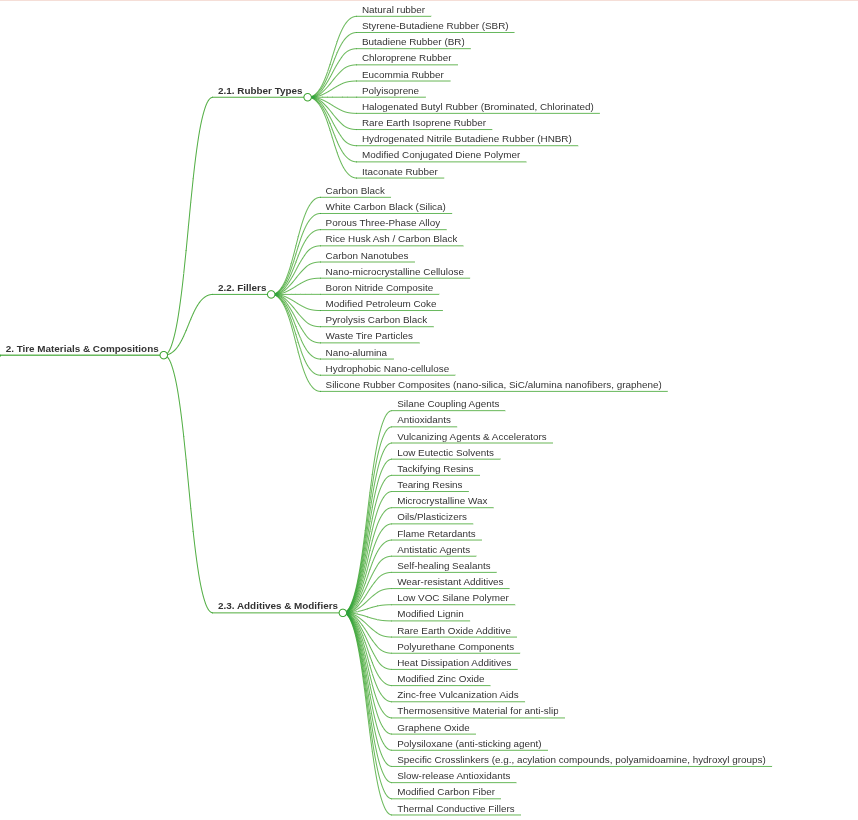