Multiphysics Modeling for Tire Performance
Modern tire design requires precise understanding of coupled thermal and mechanical behaviors. Field measurements show temperature variations of up to 40°C across tire cross-sections during normal operation, while contact patch temperatures can spike above 100°C during aggressive cornering—conditions that significantly affect both traction characteristics and wear patterns.
The fundamental challenge lies in accurately modeling the complex interactions between mechanical deformation, heat generation, and material property changes across varying operating conditions.
This page brings together solutions from recent research—including 3D finite element analysis with thermal coupling, iterative multiphysics simulations that capture temperature-dependent material properties, and advanced contact models that integrate road-tire heat transfer. These and other approaches help engineers predict and optimize tire performance while reducing costly physical prototyping cycles.
1. Finite Element Analysis Method for Simulating Tire Longitudinal Slip Characteristics
HANGZHOU HAICHAO RUBBER CO LTD, ZHONGCE RUBBER GROUP CO LTD, 2024
Simulating tire longitudinal slip characteristics using finite element analysis to efficiently and accurately determine tire forces and moments when sliding on the road. The simulation involves steps like finite element pretreatment, 2D inflation analysis, 3D loading modeling, steady state simulation, and dynamic slip simulation. It uses explicit analysis with customizable slip rates and a fitted friction model from rubber testing to accurately replicate tire longitudinal behavior. This allows tire dynamics modeling and optimization without physical testing.
2. 3D Tire Model Simulation Method for Iterative Temperature Distribution Analysis
Qingdao Sentury Tire Co., Ltd., QINGDAO SENTURY TIRE CO LTD, 2023
Simulating tire temperature distribution using a 3D tire model to improve accuracy and intuitiveness compared to 2D methods. The simulation method involves using a 3D tire model in simulation software like ABAQUS. The tire model is analyzed iteratively to improve accuracy by calculating heat generation based on mechanical properties at each step. This iterative calculation of power density for each unit improves the simulation by considering the mutual influence of cornering, abrasion, and rolling resistance on the temperature field.
3. Tire Performance Simulation Model with Temperature-Dependent Material Properties and Flash Temperature Analysis
Siemens Industry Software Netherlands B.V., 2022
Computer simulation of tire performance using a model that accurately predicts tire behavior at high speeds and loads where traditional tire models struggle. The simulation incorporates a detailed tire temperature model that accounts for temperature-dependent material properties, like rubber compounds, to accurately predict tire temperatures. This improves tire force and handling predictions at extreme conditions. The simulation also includes a flash temperature model for short-term temperature spikes during sliding. The tire model takes vehicle velocity as input and can be integrated into vehicle simulation and control systems.
4. Thermodynamic Model-Based Simulation Method for Tire Behavior Using Fourier Diffusion and Temperature-Dependent Material Scaling
SIEMENS IND SOFTWARE DUTCH CO LTD, SIEMENS INDUSTRIAL SOFTWARE DUTCH CO LTD, 2022
Computer-implemented method for simulating tire performance that accurately models tire behavior over a wide range of operating conditions and temperatures. The simulation method involves using a thermodynamic model to calculate tire properties based on factors like temperature, slip, and vertical load. The model accounts for effects like rolling resistance, tread deformation, and friction. It uses Fourier diffusion to simulate temperature distribution within the tire, and scaling factors to adjust material properties like stiffness and damping at different temperatures. The simulation can be integrated into existing tire models like the magic formula.
5. 3D-2D Hybrid Model for Tire Temperature Simulation Incorporating Groove-Dependent Rolling Deformation
YOKOHAMA RUBBER CO LTD, YOKOHAMA RUBBER CO LTD:THE, 2021
Simulating tire temperature during rolling using a computer to accurately calculate tire temperature while accounting for complex tread patterns. The simulation involves two steps: 1) rolling deformation calculation using a 3D tire model with grooves, and 2) thermal analysis using a 2D tire model with filled grooves. By adjusting material constants, boundary conditions, and heat generation values based on rolling deformation, the 2D model accurately simulates tire temperature during rolling.
6. 3D Tire Model Simulation Incorporating Iterative Stress-Strain and Temperature Calculations
QINGDAO SENTURY TIRE CO LTD, 2020
Simulating tire temperature distribution using a 3D tire model instead of a 2D model for more accurate and intuitive results compared to prior methods. The simulation involves generating a 3D tire model based on a 2D tire model, adding a temperature model to the 3D model, and iteratively calculating stress, strain, and temperature in each step to accurately capture the thermal effects on tire mechanics.
7. Finite Element Analysis Method for Predicting Tire Rolling Resistance via Virtual 3D Model and Strain-Energy Conversion
KUMHO TIRE CO INC, 2020
A method to predict tire rolling resistance using finite element analysis to reduce the cost and time compared to traditional rolling resistance testing. The method involves creating a virtual 3D tire model, analyzing tire deformation on a flat surface with just load and air pressure, converting strain to energy loss and heat generation, and calculating internal tire temperatures.
8. Tire Performance Simulation Utilizing Euler Elements for Snow-Covered Road Interaction
TOYO TIRE Corporation, 2019
Simulating tire performance on snow-covered roads using a tire model and a road surface model. The simulation optimizes calculation efficiency for snowy road conditions by strategically placing Euler elements, which simulate fluid behavior, around the tire contact patch. The maximum contact length is calculated and Euler elements are placed 0.5 times that length in front and behind the contact point. This covers the minimum required area for snow traction without excess elements. The Euler elements also move with the tire to further reduce calculation cost.
9. Tire Turning Simulation System Incorporating Temperature-Dependent Friction Analysis
Toyo Tire & Rubber Co., Ltd., 2018
Tire turning simulation method, device, and program that improves accuracy by considering temperature dependence of friction. The simulation divides the tire into elements, predicts ground temperature, simulates rolling with load, calculates contact pressures and friction coefficients using predicted temperature, then calculates forces on each element. This allows iterative simulations with varying slip angles and speeds to acquire sets of relationships between slip and forces. By considering temperature effect on friction, it improves accuracy of calculating lateral forces and cornering forces applied to the tire.
10. Simplified Tire Model for Simulating Temperature with Reduced Finite Element Complexity
Sumitomo Rubber Industries, Ltd., 2017
Simulating tire temperature during running using a simplified tire model to reduce calculation time compared to accurately modeling all the grooves. The method involves filling in some of the grooves of the virtual tire model with finite elements. This reduces the number of elements and nodes compared to a complete groove model. The simulation calculates tire running state and temperature at filled groove positions using the simplified model. To account for missing groove heat dissipation, it estimates a temperature rise at those positions versus a full groove tire. Subtracting this rise from the filled groove model temperature gives the actual running temperature.
11. Tire Temperature Simulation Model with Differential Thermal Conductivity in Recessed Regions
SUMITOMO RUBBER IND, SUMITOMO RUBBER IND LTD, 2017
Creating a tire model for accurately simulating tire temperatures with reduced computational time compared to traditional methods. The key idea is to define higher thermal conductivity values in the elements of the recessed regions of the tire model compared to the non-recessed regions. This accounts for the increased heat dissipation through the recesses like grooves. By defining larger thermal conductivity values in the recesses, the tire model can more accurately simulate the temperature distribution and heat flow in tires with complex groove patterns. This allows for faster tire temperature simulations compared to subdividing and modeling the grooves individually.
12. Tire Temperature Simulation Model with Element-Specific Heat Transfer Coefficient Calculation
SUMITOMO RUBBER IND, SUMITOMO RUBBER IND LTD, 2017
Creating a tire model for simulating tire temperature that accurately calculates temperature by considering both the heat transfer between the tire and road and the heat transfer between the tire and air. The method involves dividing elements on the tread surface into grounded and ungrounded elements based on a grounding condition. Heat transfer coefficients between tire-road and tire-air are separately input for each type of element. Then, a weighted average of these coefficients is calculated for each region of the tire to create a customized heat transfer coefficient that accounts for both road and air effects.
13. Tire Durability Evaluation Simulation Method Incorporating Strain and Stress Analysis
SUMITOMO RUBBER IND, SUMITOMO RUBBER IND LTD, 2015
Tire simulation method to accurately evaluate tire durability using a computer. The simulation involves calculating tire contact with ground conditions, then analyzing strain amplitudes and Mises stresses in elements of the tire model. Durability is evaluated based on both strain (deformation) and stress (heat generation) indices. By considering both deformation and heat in elements, the simulation provides more accurate tire durability evaluation compared to just strain analysis.
14. Tire Temperature Prediction via Region-Specific Heat Transfer Coefficient Simulation
SUMITOMO RUBBER IND, SUMITOMO RUBBER IND LTD, 2015
Accurately predicting the running temperature of a tire using computer simulation by defining different heat transfer coefficients on the outer surface of the virtual tire model to mimic the non-uniform heat radiation and air flow patterns of a physical tire. The simulation involves dividing the tire surface into regions with distinct heat transfer coefficients based on factors like radial position and speed. This allows more realistic heat transfer modeling compared to uniform coefficients.
15. Real-Time Simulation Method for Tire Forces and Torques Using Dynamic Physical Parameters
MICHELIN RECHERCHE ET TECHNIQUE SA, 2015
Simulating tire forces and torques in real-time for vehicle dynamics modeling. The method accurately predicts longitudinal, lateral, and self-aligning torque forces of a tire rolling on a road surface based on physical parameters and dynamic conditions. It calculates forces like longitudinal force Fx and lateral force Fy using tire-specific parameters like rigidity and temperature profiles, as well as dynamic factors like tire deformation and road friction. This allows more accurate tire modeling compared to simplified methods like the Magic Formula.
16. Finite Element Model for Simulating Vulcanization-Induced Tire Shape Changes and Residual Stress Analysis
BRIDGESTONE CORP, 2012
Accurately simulating tire performance using a finite element method. The simulation involves creating a tire model with elements, setting expansion rates, calculating vulcanization-induced shape changes, calculating thermal shrinkage and residual stress, and analyzing tire performance based on those factors. This allows simulating tire behavior after vulcanization and accounting for expansion, shrinkage, and stress changes.
17. Vehicle Model-Based Elemental Pneumatic Tire Simulation for Fluid Dynamics and Rotational Motion Analysis
BRIDGESTONE CORP, 2011
Accurate tire performance prediction using simulation by creating a vehicle model with the pneumatic tire divided into elements, calculating the fluid behavior around the tire using the vehicle model, and accounting for tire rotation and vehicle motion to more accurately represent real-world tire performance.
18. Method for Simulating Tire Forces Incorporating Deformation, Adhesion, Temperature, and Airflow Effects
MICHELIN RECHERCHE ET TECHNIQUE SA, 2009
Method for simulating the physical behavior of a vehicle tire rolling on the ground that provides more accurate and realistic tire forces compared to traditional methods. The simulation accounts for factors like tire deformation, ground adhesion, temperature, and airflow. It uses a set of equations and iterative methods to calculate forces like longitudinal, lateral, and self-aligning torque. The simulation involves calculating forces based on tire parameters, ground conditions, and dynamic vehicle motion. It aims to provide real-time available values of tire forces more reliably than prior methods that lacked physical causality.
19. Tri-Model Computational Framework for Vehicle Tire Dynamics Simulation
MICHELIN RECHERCHE ET TECHNIQUE SA, 2009
Method for simulating the physical behavior of a vehicle tire rolling on the ground. The simulation involves three models: 1) a model of the contact forces between the tire and ground, based on adhesion coefficients and equilibrium conditions of shear and slip; 2) a model of the tire's dynamic behavior during rolling, using parameters like cornering stiffness and natural frequency; and 3) a model of the tire's self-aligning torque, based on force distribution and tire geometry. The simulation iteratively applies these models to calculate forces like longitudinal, lateral, and self-aligning torque.
20. Iterative Finite Element Model for Temperature-Convergent Stress and Thermal Analysis in Tires
BRIDGESTONE CORP, 2007
Accurately predicting the temperature distribution inside and outside a tire during rolling using a finite element analysis model of the tire. The method involves iteratively refining the tire model's material properties and analysis steps until convergence. The steps are: 1. Determine temperature and strain dependence of tire rubber properties. 2. Create a stress analysis model with finite element tire. 3. Calculate stress/strain with load/roll analysis. 4. Generate heat distribution based on stress/strain and rubber properties. 5. Perform thermal analysis to predict temperature. 6. Create new stress analysis model with updated rubber properties at predicted temps. 7. Calculate stress/strain again. 8. Generate new heat distribution. 9. Perform thermal analysis again. Keep iterating until temperature convergence.
Get Full Report
Access our comprehensive collection of 34 documents related to this technology
Identify Key Areas of Innovation in 2025
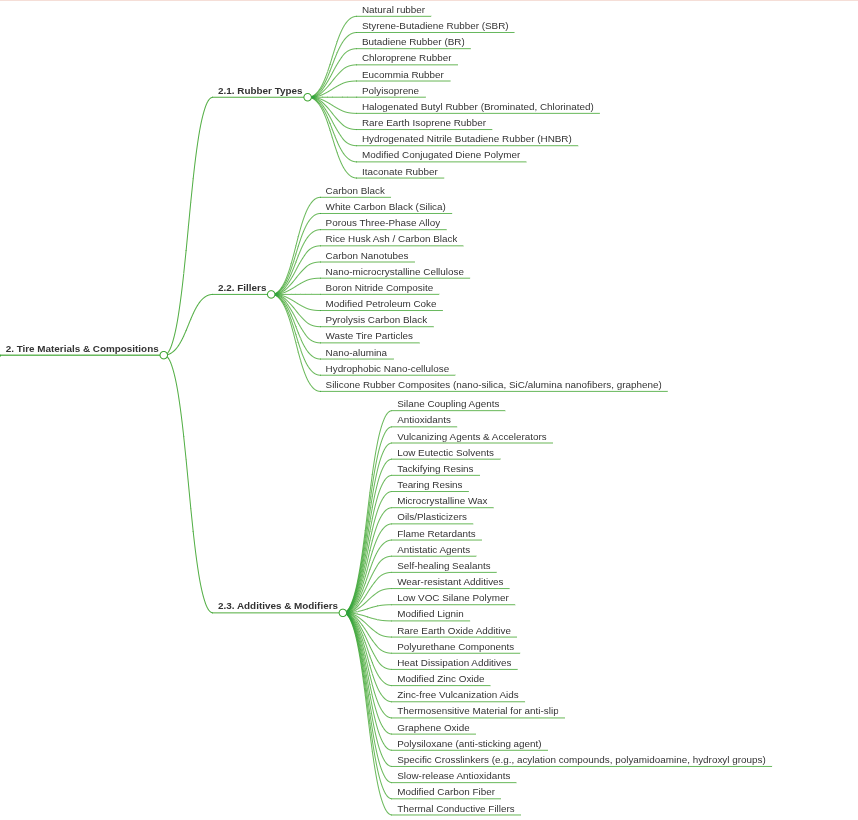