Vulcanization Presses for Tire Production
Modern tire vulcanization presses operate at temperatures up to 180°C and pressures exceeding 20 bar, processing green tires through precise heating and pressure cycles that typically last 10-15 minutes. During this critical phase, trapped fluids, thermal gradients, and pressure variations can lead to defects that compromise tire integrity and performance.
The fundamental challenge lies in maintaining uniform heat distribution and pressure across the tire while efficiently evacuating trapped gases and managing energy consumption during both continuous operation and idle periods.
This page brings together solutions from recent research—including optimized inner heating cycles, integrated fluid discharge systems, advanced bladder pressure controls, and novel vulcanization accelerators. These and other approaches focus on improving tire quality while reducing energy consumption and cycle times in industrial vulcanization processes.
1. Inner Heating Cycle Adjustment for Tire Vulcanization Press Based on Idle Duration
CONTINENTAL REIFEN DEUTSCHLAND GMBH, 2024
Improving the inner heating method for vulcanizing tires in a vulcanization press to prevent excessive energy loss and ensure consistent vulcanization quality after prolonged idle times. The method involves adjusting the inner heating cycle duration based on whether the vulcanization press has been idle for a long time. If the press has been idle, the inner heating cycle is extended to compensate for potential component cooling. This prevents insufficient energy input during the first heating cycle after an idle period, which can lead to deterioration in tire properties.
2. Vulcanizing Equipment with Magnetically Coupled Sealed Motor Drive System
HIMILE MECHANICAL SCIENCE AND TECHNOLOGY CO LTD, 2024
Tire vulcanizing equipment with a sealing hood to isolate the driving motor from the high temperature and pressure inside the vulcanizing bladder. The hood seals between the motor, rotating shaft, and fan. Magnets on the shaft and fan attract to rotate the fan. This allows the motor to drive the fan externally, preventing damage to the motor inside the sealed bladder. The sealing hood isolates the motor from the hot, pressurized vulcanizing environment.
3. Vulcanizing Equipment with Vertical Stacked Heating and Gas Circulation Assemblies
HIMILE MECHANICAL SCIENCE AND TECHNOLOGY CO LTD, 2024
Vulcanizing equipment for curing rubber tires that improves tire quality, reduces space requirements, and eliminates condensation issues compared to conventional steam vulcanization. The equipment uses a stacked arrangement of a heating assembly and gas circulation assembly inside the vulcanizing bladder, rather than horizontally distributing them in the bladder. This saves space and allows better gas circulation. A rotating shaft sleeve outside the center rod connects the gas circulation assembly to a driving assembly. The bladder seals in the tire during vulcanization. The vertical stacked assembly eliminates condensation compared to horizontal arrangements.
4. Tire Vulcanization Device with Integrated Fluid Path and Movable Pressure Body for Heat Loss Reduction
CONTINENTAL REIFEN DEUTSCHLAND GMBH, 2024
Reducing heat losses during tire vulcanization in a device that allows vulcanizing tires of varying shapes and sizes. The device has a tire receiving unit with a mold, heating body, and fluid path for a temperature control medium. The fluid path exits through a movable pressure body. This eliminates recesses and openings in the insulator around the unit, reducing heat transfer. The pressure body connectors are shared between units, allowing swapping without disconnecting.
5. PLC System with Cycle-Based Adaptive Pressure Control for Tire Curing Press Bladders
BRAZELTON EDGAR PEARSON, GORE TEDDY LEE, 2024
Programmable logic control (PLC) system for accurately controlling tire curing press bladder pressure during tire manufacturing. The system uses learning and analysis of past cycles to improve pressure control. It collects data like pressure, set point, and valve output during cycles. It analyzes that data to identify issues like overshoot and undershoot. Then it uses algorithms to adjust the valve output for the next cycle to mitigate those issues. This learns from past cycles to improve pressure control accuracy.
6. Vulcanization Equipment with External Heating and Gas Circulation Mounting for Unrestricted Tire Sizing
HIMILE MECHANICAL SCIENCE AND TECH SHANDONG CO LTD, HIMILE MECHANICAL SCIENCE AND TECHNOLOGY CO LTD, 2024
Tire vulcanization equipment that allows larger tire sizes to be vulcanized without restriction from the internal heating and gas circulation devices. The equipment has an external mounting piece for the heating and circulation devices instead of inside the mold. This saves space inside the mold for larger tire sizes. The external devices divert and circulate the heated gas to the mold cavity.
7. Vulcanization Center with Centralized Mold Handling and Cooling Stations for Sequential Tire Engineering
GUILIN RUBBER MACHINERY CO LTD, 2024
Intelligent vulcanization center for engineering tires that improves efficiency of equipment use by coordinating actions of devices in each vulcanization unit, integrating mold opening/closing and unloading/loading on a central unit, and using cooling stations between units to shorten auxiliary operation time. The center consists of four vulcanization hosts in sequence, each with upper and lower chambers, mold locking, and central mechanisms. A cooling station is provided between adjacent hosts. A centralized auxiliary unit between hosts performs mold closing/opening and tire handling. This centralized replacement of molds and centralized loading/unloading of tires efficiently coordinates device actions, shortens auxiliary operation time, and allows efficient operation of each unit.
8. Axially Movable Heating Press for Tire Vulcanization with Radial Mold Closure Mechanism
CONTINENTAL REIFEN DEUTSCHLAND GMBH, 2023
Heating press for vulcanizing vehicle tires that eliminates the need for bellows to prevent tire distortion during vulcanization. The press has an upper and lower part that can move axially. The upper part has the mold and can close on the lower part to compress the tire. This allows radial closure of the mold without using bellows. It also enables radial compression while heating from both inside and outside.
9. Vertical Stack Vulcanization Equipment with Integrated Gas Circulation and Clamping Assembly
HIMILE MECHANICAL SCIENCE AND TECH SHANDONG CO LTD, HIMILE MECHANICAL SCIENCE AND TECHNOLOGY CO LTD, 2023
Vulcanization equipment for tire curing that improves space efficiency and gas circulation compared to conventional horizontal bladder designs. The equipment uses a vertical stacking of the heating assembly and gas circulation assembly inside the vulcanization bladder. This eliminates the need for radial space around the bladder and allows tighter tire fits. The vertical arrangement also facilitates gas flow and prevents interference. The bladder sealing is done by a clamping device with air ducts. The heating assembly has a vertical heater and sleeve. The gas circulation assembly has a deflector ring, diffuser, and air duct.
10. Tire Vulcanization Device with Size-Specific Lower Molds, Sealing Pistons, and Gas Recovery System
Jintiecheng Intelligent Technology Co., Ltd., Jintiecheng Intelligent Technology (Qingdao) Co., Ltd., 2023
Tire vulcanization device and process that improves efficiency and reduces smoke compared to conventional methods. The device uses separate lower molds for large and small tires, allowing better fit and faster demolding. It also has sealing pistons, closed dust covers, and gas recovery to prevent smoke and waste gas. The device can also use electric heating instead of steam to reduce noise. The tire fixing mechanism uses a mechanical stretcher for small tires instead of capsules.
11. Tire Vulcanizer with Vertical Plate and Hydraulic Cylinder Assembly for Direct Base Clamping and Separate Heating Plate Configuration
Shandong Lichuang Mould Co., Ltd., SHANDONG LICHOND MOULD CO LTD, 2023
Tire vulcanizer for more convenient and stable mold clamping and heating during vulcanization compared to existing vulcanization devices. The tire vulcanizer has a base for the mold to be placed on. The mold clamping is achieved by a vertical plate, hydraulic cylinder, and heating plate assembly that moves vertically to clamp the mold. This allows the mold to be easily positioned and clamped directly on the base without needing to overlap the heating plate. The heating plate is separately heated rather than overlapping the plates, eliminating the need for mold hoisting and pipeline connections. An opening and closing mechanism further assists in clamping the mold.
12. Tire Vulcanization Mold with Differential Thermal Expansion Exhaust Gap and Reverse Block Tread Design
HANGZHOU HAICHAO RUBBER CO LTD, ZHONGCE RUBBER GROUP CO LTD, 2023
Tire vulcanization mold and tire design to improve tire appearance by preventing mold marks. The mold has an inner wall with an exhaust device formed by an aluminum plate around an inner steel plate. During vulcanization, the different thermal expansion of the metals creates a gap less than 0.05mm between them. This prevents rubber from entering the gap and reduces mold marks on the tire tread. The mold can also have vacuum to remove internal air. The tread has reverse blocks and grooves matching the mold features.
13. Vulcanization Apparatus with Electromagnetically Induced Rotating Member for Uniform Tire Heating
Shandong Haomai Machinery Technology Co., Ltd., SHANDONG HIMILE MECHANICAL SCIENCE AND TECHNOLOGY CO LTD, 2023
Vulcanization equipment for evenly heating tires during vulcanization to improve quality. It has a rotating member with an electromagnetic component inside a chamber on the ring seat. When energized, electromagnetic induction between the ring seat and rotating member causes it to rotate. This drives an air outlet to vent the hot nitrogen inside the vulcanization bladder, allowing circulation and balanced heating. The heating component guides gas to the bladder inner wall. This prevents hotspots and uneven vulcanization compared to static bladders.
14. Tire Vulcanization Method Using Nitrogen Pre-Inflation and Gradual Superheated Water Pressurization
AEOLUS TYRE CO LTD, 2023
Tire vulcanization process to prevent unevenness and steel wire bending in large tires like 25" OTR tires. The process uses a non-water-soluble gas like nitrogen to initially inflate the tire mold during pre-vulcanization. This prevents steam condensation and rapid pressure fluctuations. The gas is gradually replaced with superheated water at increasing pressures to shape the tire. The water pressure is held at each stage for 3-20 minutes. This gradual pressurization and buffering prevents sudden pressure spikes that can deform the tire. Finally, vulcanization is done with superheated water circulation.
15. Tire Vulcanization System with Electrically Heated Mold and Distributed Temperature Feedback Control
HIMILE MECHANICAL SCIENCE AND TECH SHANDONG CO LTD, HIMILE MECHANICAL SCIENCE AND TECHNOLOGY CO LTD, 2023
Tire vulcanization heating system for improving tire vulcanization quality and reducing energy consumption compared to steam vulcanization. The system uses electric heating instead of steam. It has multiple heating units located at specific positions inside the mold and plates. Temperature feedback devices measure temperatures at those positions. A master control unit coordinates the heaters and compares feedback temps to targets for optimal vulcanization. This allows gradual, uniform heating of the mold surfaces. The temperature feedback provides more accurate control than just mold cavity temperature.
16. Heating Gas Circulation Mold Assembly with Integrated Turbine and Clamping Mechanism for Tire Vulcanization
HIMILE MECHANICAL SCIENCE AND TECH SHANDONG CO LTD, HIMILE MECHANICAL SCIENCE AND TECHNOLOGY CO LTD, 2023
Heating gas circulation mold assembly for tire vulcanization to improve quality and consistency of tire vulcanization by circulating heated gas inside the mold. The mold has a gas circulation pipeline with a turbine or diffuser device to guide the gas flow. A clamping device seals the vulcanization bladder in the mold cavity. The pipeline connects to an air intake and exhaust on the mold. This circulates heated gas throughout the bladder during vulcanization for more even heating versus stationary nitrogen.
17. Vulcanizing Device with Interchangeable Mold Units and Integrated Fluid Path Connections
CONTINENTAL REIFEN DEUTSCHLAND GMBH, 2023
Device for vulcanizing tires that reduces heat loss during curing while allowing vulcanization of tires of different shapes and sizes. The device has a tire receiving unit with a mold that surrounds the tire, a heating element around the mold, and a movable pressure body. The heating element has a fluid path for temperature control. The insulating body around the tire unit is solid without recesses or openings to prevent heat loss. The fluid path connections are on the movable body instead of the unit. This allows replacing units for different tire sizes without disconnecting the fluid path each time.
18. Method for Independent Temperature Regulation of Tire Vulcanization Mold Regions via Separate Steam Supply Control
TRIANGLE GROUP CO LTD, 2023
Method for adjusting external temperature of different regions in tire vulcanization molds to improve tire quality by preventing uneven heating during vulcanization. The method involves separately regulating the steam supply to the upper hot plate, mold cover, and lower hot plate instead of connecting them in series. Steam pipes with temperature valves are used to separately supply steam to the upper plate, mold, and lower plate. This allows setting different temperatures for each region instead of a single mold-wide temperature.
19. Tire Vulcanization Process with Inert Gas Pressure and Temperature Modulation
QINGDAO SENTURY TIRE CO LTD, 2023
A tire vulcanization process using inert gas to improve tire quality by avoiding defects caused by traditional steam/water vulcanization. The process involves swinging the pressure and temperature of inert gas during vulcanization. The steps are: 1) Collecting and storing inert gas. 2) Heating the gas to 195-215°C. 3) Circulating the heated gas through the mold. 4) Initial shaping and warming at low pressure. 5) High pressure vulcanization. 6) Recovering the gas. The pressure swing allows better mold filling, cord tension control, and crosslinking density. The temperature swing maintains optimal vulcanization conditions. The gas circulation ensures consistent pressure and temperature.
20. Hydraulic Transmission System for Synchronizing Multiple Vulcanization Units in Tire Curing Apparatus
Nexen Tire Corporation, 2022
Tire curing apparatus and method for curing using the same that enables efficient transmission of hydraulic power to multiple vulcanization units to prevent hydraulic shortage and speed differences. The apparatus has a driving unit connected to multiple vulcanization units that transmits hydraulic pressure. A control unit receives remaining curing time from sensors and opens units in groups to synchronize curing. It stops curing if too many units are close to finish. This prevents hydraulic power shortage when simultaneously supplying many units.
Get Full Report
Access our comprehensive collection of 126 documents related to this technology
Identify Key Areas of Innovation in 2025
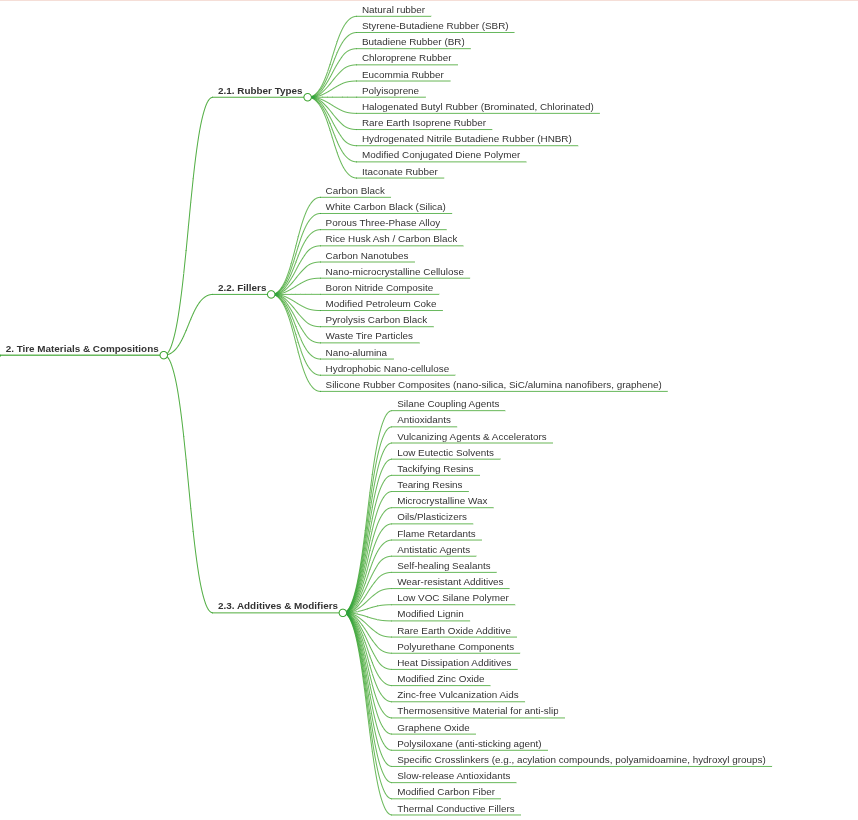