Catalysts for Improving Quality of Tire Pyrolysis Oil
Pyrolysis oil derived from waste materials typically contains high levels of oxygenates, sulfur compounds, and unsaturated hydrocarbons that limit its direct use as fuel. Current processes yield oils with oxygen content above 20 wt%, acid numbers exceeding 100 mg KOH/g, and heating values below 20 MJ/kg—far from the specifications required for commercial fuel applications.
The fundamental challenge lies in selectively removing heteroatoms and stabilizing reactive compounds while maintaining economically viable conversion rates and catalyst longevity.
This page brings together solutions from recent research—including ammonia-assisted pyrolysis, dual-stage catalytic processes, specialized metal oxide catalysts, and integrated hydropyrolysis approaches. These and other techniques focus on improving oil quality metrics while addressing practical constraints around catalyst deactivation and process economics.
1. FAU-Y Zeolite-Supported Bi-Zn Transition Metal Catalyst with Crystallized Metal Clusters
CHINA UNIV OF PETROLEUM EAST CHINA, CHINA UNIVERSITY OF PETROLEUM, 2023
FAU-Y type zeolite-supported multi-component transition metal catalyst for oil shale pyrolysis that reduces pyrolysis temperature and improves oil and gas recovery. The catalyst is prepared by mixing aluminum powder, bismuth nitrate, zinc chloride, sodium citrate, and sodium hydroxide solution to form a clear solution. This solution is added to a FAU-Y zeolite carrier and heated to crystallize the zeolite around the metal clusters. The resulting catalyst contains Bi, Zn, and FAU-Y zeolite for pyrolyzing oil shale at lower temperatures compared to conventional catalysts.
2. Acid-Treated H-Beta Zeolite with Metal Ion Exchange for Catalytic Pyrolysis of Lignin
Fujian Agriculture and Forestry University, FUJIAN AGRICULTURE AND FORESTRY UNIVERSITY, 2023
Acid-modified H-Beta zeolite catalyst for catalytic pyrolysis of lignin to produce bio-oil. The catalyst is prepared by treating H-Beta zeolite with acid to create aluminum vacancies, then exchanging metal ions into the vacancies through a solid-state ion exchange process. This acid modification allows controlling the acidity of the zeolite catalyst. The modified zeolite is then used to catalyze lignin pyrolysis at 600°C to generate high-quality bio-oil with reduced oxygen content.
3. Zeolite-Supported Multifunctional Catalyst with Heteropolyacid-Derived Metal Precursors
SAUDI ARABIAN OIL CO, 2022
A multifunctional catalyst for upgrading pyrolysis oils using heteropolyacids as metal precursors instead of conventional metal precursors. The catalyst is prepared by impregnating a zeolite support with a solution containing the heteropolyacid-based metal precursors. This deposits the catalyst metals onto the zeolite surface. The catalyst enables higher yields of valuable aromatics like benzene, toluene, xylene from pyrolysis oils at lower reaction pressures compared to existing catalysts.
4. Method for Producing Oil from Waste Tires via Ammonia Pyrolysis and Catalytic Hydrogen Refinement
NANJING FORESTRY UNIVERSITY, UNIV NANJING FORESTRY, 2021
A method for producing high-quality oil from waste tires that involves crushing the tires, pyrolyzing them in an ammonia atmosphere under pressure, separating the pyrolysis liquid, and then refining it using hydrogen and catalysts. The pyrolysis in ammonia improves the oil quality compared to regular pyrolysis. The crushing step allows better pyrolysis. The refining step using hydrogen and catalysts further improves the oil quality.
5. Hierarchical Mesoporous Zeolite-Supported Metal Catalyst with Heteropolyacid Precursors
ARAMCO SERVICES CO, SAUDI ARABIAN OIL CO, 2021
Multifunctional catalyst for upgrading pyrolysis oil that provides higher yield of valuable aromatic compounds like benzene, toluene, ethylbenzene, and xylenes from pyrolysis oil at lower reaction pressures compared to existing catalysts. The catalyst is made by depositing metal catalysts onto a hierarchical mesoporous zeolite support using heteropolyacids as precursors. The zeolite's larger pore size allows access of larger multi-ring aromatics. The heteropolyacid precursors enable higher aromatic yields at lower pressures.
6. Metal-Doped Hierarchical Pore ZSM-5 Zeolite Catalyst with HF-Etched Porosity
China University of Mining and Technology, CHINA UNIVERSITY OF MINING AND TECHNOLOGY, 2020
Preparation of a high-activity catalyst for biomass pyrolysis using metal-doped hierarchical pore ZSM-5 zeolite. The catalyst is made by etching HZSM-5 with HF acid to create hierarchical porosity, then doping the etched zeolite with nickel to increase cracking and hydrogen transfer activity. This enhances aromatics yield in biomass pyrolysis compared to conventional zeolites.
7. Hierarchical Mesoporous Zeolite-Supported Metal Catalyst with Heteropolyacid Precursors
Saudi Arabian Oil Company, 2020
Multifunctional catalyst for upgrading pyrolysis oil with improved yield and lower reaction pressure compared to existing catalysts. The catalyst is made by depositing metal catalysts onto a hierarchical mesoporous zeolite support using heteropolyacids as precursors. The zeolite support has an average pore size of 2-40 nm. This enables conversion of larger aromatics in pyrolysis oil. The heteropolyacid precursors increase yield at lower pressures. The catalyst composition is a mixture of metal catalysts supported on the zeolite.
8. Biomass Catalytic Cracking Using Alkaline MNC-13 Mesoporous Molecular Sieve Catalyst Synthesized with Acid-Functionalized Ionic Liquid Template
Qingdao University of Science and Technology, 2019
Preparing liquid fuel oil from biomass by catalytic cracking using a novel alkaline MNC-13 mesoporous molecular sieve catalyst. The MNC-13 sieve is synthesized using an acid-functionalized ionic liquid as a template. The MNC-13 sieve has high acidity, stability, and larger pore size compared to traditional microporous sieves, allowing wider molecular weight distribution of the pyrolysis oil products. This enables higher liquid fuel yields and better quality compared to other catalysts.
9. Nickel-Zirconia-Zeolite Catalyst for Biomass Oil Cracking and Deoxygenation
Guangdong University of Petrochemical Technology, GUANGDONG UNIVERSITY OF PETROCHEMICAL TECHNOLOGY, 2017
Catalyst for cracking and deoxygenation of biomass liquefied oil to improve its quality and suitability as a fuel. The catalyst is composed of specific amounts of nickel, zirconia, and zeolite. This catalyst enables efficient catalytic cracking of biomass oil at mild conditions to remove oxygen as CO2 or water, leaving hydrocarbons. It provides high deoxygenation rate and good anti-coking performance for biomass oil refining.
10. Two-Stage Catalytic Process with Mineral and Zeolite Catalysts for Biomass Pyrolysis Oil Refinement
Southeast University, SOUTHEAST UNIVERSITY, 2016
A two-stage catalytic process to improve the quality of bio-oil from biomass pyrolysis. The first stage uses a mineral catalyst to pyrolyze the biomass at lower temperatures to increase the hydrogen-to-carbon ratio of the pyrolysis gas. This reduces the oxygen content and improves the yield of hydrocarbons in the pyrolysis oil. The second stage uses a zeolite catalyst to further reform the pyrolysis oil and remove oxygen. The zeolite also selectively separates the hydrocarbons, improving the oil quality. The first stage gas is directly fed to the second stage to provide hydrogen for reforming. This avoids coking the zeolite catalyst and extends its life.
11. Recycling Method for Waste Tires and Rubber via Carbon Co-Processing at Elevated Temperatures
CONSEJO SUPERIOR INVESTIGACIONES CIENTIFICAS, 2001
A method to recycle waste tires and rubber by co-processing with carbon to produce synthetic oils and storable heat energy products. The method involves mixing crushed waste tires, carbon, and optionally a Fe catalyst. The mixture is heated at 400-600°C for 1-2 hours to convert the rubber and carbon into oils, gases, and solid residues. The oils can be fractionated for use as fuels or chemicals, and the solid residues have medium and high caloric value for energy storage. The Fe catalyst helps fix oxygenates and sulfur.
12. Rubber Waste Conversion via Catalytic High-Temperature Low-Pressure Cracking with Closed-Loop Gas Recycling
FUBAOCHENG INDUSTRY & TRADE CO, FUBAOCHENG INDUSTRY & TRADE CO LTD, 1993
Recycling rubber waste into useful fuel oil and gas without causing pollution. The method involves mixing rubber waste with a catalyst and cracking it at high temperature and low pressure in a reactor to produce gas. The gas is then catalytically reacted and condensed to separate oil and gas. The recovered gas is recycled back into the reactor and catalytic tube. This closed loop allows processing rubber waste into saleable products without environmental harm.
13. Catalytic Cracking Process for Waste Rubber Using Calcium Oxide-Nickel-XT-10 Catalyst Composition
FULL BORN CHEN INDUSTRIAL CO LTD, 1993
A process for efficiently converting waste rubber into fuel oil and gas by cracking the rubber using a specific catalyst composition. The catalyst contains calcium oxide (CaO), nickel (Ni), XT-10 (a mixture of minerals), and trace amounts of niobium and titanium. The catalyst is reacted with waste rubber at temperatures around 280°C under pressure. The resulting products are filtered, condensed, and fractionated into light oil, heavy oil, and gas for storage. The catalyst allows rapid cracking of the rubber into fuels in just 2 hours.
14. Catalytic Cracking Process for Rubber Waste Using CaO-Ni-XT-10-Niobium-Titanium Catalyst
FUBAOCHENG INDUSTRY CO LTD, 1993
Recycling rubber waste into fuel oil, gas, and carbon black by cracking the rubber with a specific catalyst and process. The catalyst is a mixture of calcium oxide (CaO), nickel (Ni), XT-10, niobium, and titanium. The rubber waste is heated in a sealed reactor with the catalyst to soften and melt, then cracked at high temperatures to produce flammable gases and oils. The gases are separated and stored, while the carbon black and remaining solids are collected. The process converts rubber waste into useful resources instead of landfilling.
15. Catalyst Composition for Biomass Conversion to Hydrocarbons with Alumina and Optional Silica, Zeolites, Rare Earth Oxides, and Sodium Oxide
NATIONAL UNIVERSITY OF SINGAPORE, 1991
Catalytic conversion of biomass materials like plant oils, animal oils, and rubber into hydrocarbons like gasoline, kerosene, and diesel fuel. The conversion is done using a catalyst containing alumina with optional additions of silica, zeolites, rare earth oxides, and sodium oxide. The catalyst composition and amounts are optimized to efficiently crack the biomass feedstock into hydrocarbons. The process is energy efficient and provides a route to produce renewable fuels from biomass resources.
Get Full Report
Access our comprehensive collection of 15 documents related to this technology
Identify Key Areas of Innovation in 2025
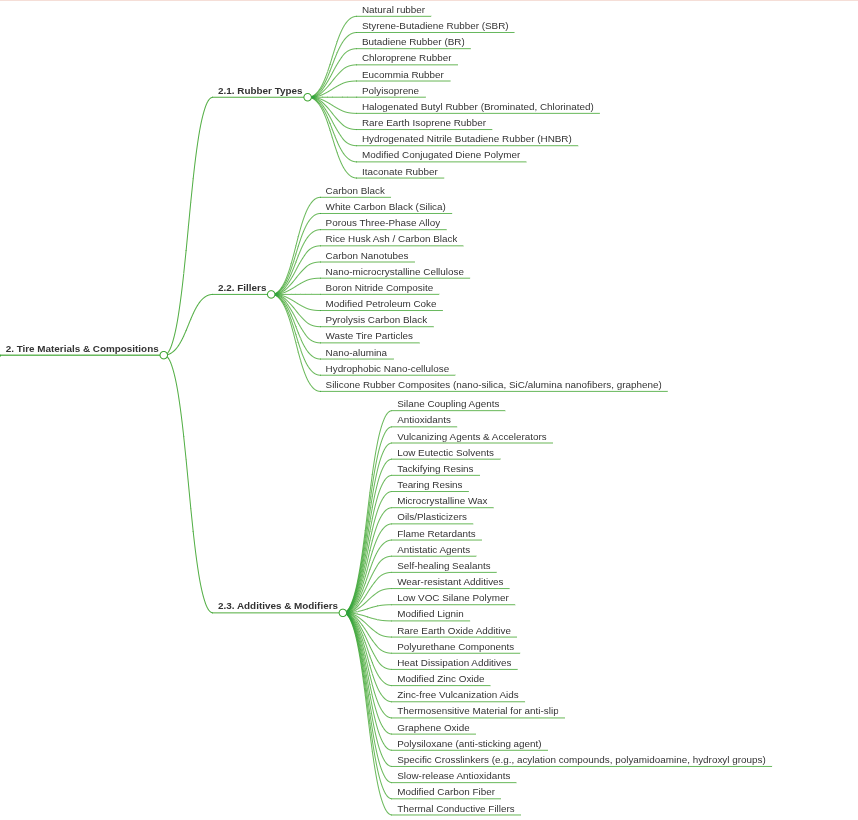