Pyrolysis Reactors for Tire Recycling
Tire pyrolysis reactors must maintain precise thermal conditions across large material volumes while managing the complex physics of decomposition. Current systems struggle with temperature gradients of 50-150°C between reactor zones, leading to inconsistent product quality and reduced oil yields that can drop below 45% of input mass.
The fundamental challenge lies in achieving uniform heat transfer throughout the feedstock while preventing material agglomeration and managing the evolving gas-solid interactions during thermal decomposition.
This page brings together solutions from recent research—including segmented temperature control systems, vertical cascade designs, specialized heat transfer surfaces, and advanced gas circulation methods. These and other approaches focus on optimizing both reaction efficiency and product quality in commercial-scale operations.
1. Vertical Reactor System for High-Temperature Pyrolysis of Waste Tires with Rubber Powder Injection and Integrated Gas Processing Components
Liuzhou Ganyuan Environmental Protection Technology Co., Ltd., LIUZHOU GANYUAN ENVIRONMENTAL PROTECTION TECHNOLOGY CO LTD, 2023
High-temperature pyrolysis of waste tires to produce oil and carbon black in a compact, efficient system. The system uses a vertical reactor with a nozzle to inject rubber powder into the reactor. A fly ash filter separates carbon black from the pyrolysis gas. An absorption tower removes sulfur from the gas before combustion in a blast furnace to provide heat for the reactor. The system is self-sufficient with the blast furnace providing heat and the gas booster evacuating the reactor. The rubber powder injection allows uniform dispersion and high initial velocity for better pyrolysis.
2. Method for Producing Fuel Oil and Carbon Black from Waste Tires via High-Temperature Negative Pressure Cracking
JINZHOU HAITONG IND & TRADE CO LTD, JINZHOU HAITONG INDUSTRY & TRADE CO LTD, 2023
A large-scale, efficient and environmentally friendly method for producing fuel oil and carbon black from waste tires. The process involves breaking the tires into small particles, then cracking the tire particles at high temperatures to produce fuel oil and carbon black. The cracking is done at negative pressure to prevent leaks and emissions. The fuel oil is condensed and dehydrated to remove water. The method provides high productivity and improved safety compared to existing tire recycling processes.
3. Waste Tire Pyrolysis Device with Integrated Gas Recirculation Heating System
LI JIE, 2023
Waste tire processing device that reduces energy consumption in pyrolysis by using the pyrolysis gas to heat the tires instead of external heat sources. The device has a reactor, screw conveyor, and gas separation tank. Crushed tires are loaded into the reactor and stirred by the screw. Gas is ignited in a chamber around the reactor. The heat from burning gas helps pyrolyze the tires. The pyrolysis gas is separated and returned to the chamber to assist heating. This recycles the waste tire heat to reduce external energy needs.
4. Waste Tire Pyrolysis Device with Molten Salt Direct Heating and Closed-Loop Gas Condensation System
EVERBRIGHT GREEN ENVIRONMENTAL PROTECTION TECH SERVICE JIANGSU CO LTD, EVERBRIGHT GREEN ENVIRONMENTAL PROTECTION TECHNOLOGY SERVICE CO LTD, EVERBRIGHT GREENTECH MAN SHENZHEN CO LTD, 2023
Waste tire pyrolysis device for recycling pyrolysis gas that improves the yield of pyrolysis oil and gas compared to indirect heating methods. The device has a waste tire silo, molten salt pyrolysis furnace, pyrolysis gas condenser, molten salt heating furnace, and pyrolysis gas heat exchanger. The molten salt pyrolysis furnace and heating furnace are connected in a closed loop. Waste tires feed into the pyrolysis furnace, and the molten salt contacts and heats the tires directly. The pyrolysis gas exits the furnace and condenses in the condenser to separate the pyrolysis oil. The pyrolysis gas then passes through the heat exchanger to preheat the molten salt before entering the pyrolysis furnace again. This allows efficient recycl
5. Rotating Tubular Reactor with Zoned Heating and Tube Cleaning for Continuous Pyrolysis of Organic Materials
KLEAN IND, KLEAN INDUSTRIES, 2022
System for continuous pyrolysis of organic materials like used tires to produce recovered carbon black. The system has a rotating tubular reactor, quenching unit, and burner unit. The reactor has multiple heating gas outlet valves along its length to control heat supply to different zones. This allows optimized pyrolysis conditions. The reactor also has a tube cleaning device to prevent clogging by transporting deposited solids from the pyrolysis gas outlet back into the reactor.
6. Rubber Waste Processing via Pyrolysis with Gas Separation and Solid Residue Gasification
2022
Integrated processing of rubber waste like tires to extract valuable products, generate energy, and reduce environmental impact. The process involves pyrolysis at 550-700°C to release volatile compounds. The gaseous pyrolysis products are cooled, separated into a methane-hydrogen mixture and heavy hydrocarbons C5-C12. The heavy hydrocarbons are distilled to extract valuable components. The methane-hydrogen mixture is used to maintain pyrolysis temperature and generate energy. The solid residue is gasified with CO2 to make sorbents and capture CO2 for recycling. The CO is reformed into H2 and CO2.
7. Pyrolysis Reactor for Waste Rubber Material with High-Temperature Polyolefin and Rubber Decomposition
MONASH UNIVERSITY, UNIV MONASH, 2022
Pyolysis of waste rubber material, such as tyre waste, into a pyrolytic oil. The process involves operating at least a pyrolysis stage of the pyrolysis reactor at an operating temperature at or above a temperature at which pyrolysis of both the polyolefin and the rubber containing material commences and up to about 600°C under a substantially inert atmosphere.
8. Vertical Cascade Pyrolysis Gasification Device with Rotating Cylinder and Internal Gas Circulation for Waste Tires
CHINA UNITED ENGINEERING CORPORATION LTD, 2022
Vertical high-efficiency cascade controllable pyrolysis gasification device for waste tires that improves pyrolysis efficiency and reduces environmental pollution compared to existing methods. The device uses a vertical rotating cylinder to pyrolyze tires. The cylinder has a feeding system for introducing tires, a rotating shaft inside, and a gas extraction pipe. The shaft has channels for circulating hot gas. This allows continuous pyrolysis at high temperatures to maximize oil yield. The device also has a carbon black discharge system. The vertical design, internal gas circulation, and controlled feeding provide higher efficiency compared to horizontal systems.
9. Waste Tire Pyrolysis System with Integrated Multi-Stage Shearing, Uniform Distribution, Radiant Heating Pyrolysis, and Solid Pulverization Steps
BEIJING XINYUAN ENVIRONMENTAL PROTECTION SCIENCE AND TECH LIMITED CO, BEIJING XINYUAN ENVIRONMENTAL PROTECTION SCIENCE AND TECHNOLOGY LIMITED CO, 2022
A waste tire pyrolysis process with integrated shearing, uniformization, pyrolysis, and solid pulverization steps to efficiently treat waste tires without secondary pollution. The process involves crushing tires into smaller pieces using multiple shearing stages, then feeding them into a sealed silo for uniform distribution. The uniform material is pyrolyzed at high temperatures without contact with hot components using radiation heating. Finally, the pyrolyzed solid is pulverized as it's discharged. This integrated process avoids issues like coking, blocking, dust, and secondary pollution compared to conventional pyrolysis systems.
10. Pyrolysis Process for Waste Tires Using Vertical Tower Reactor with Internal Heating and Steam Jet Pump System
Yang Song, SONG YANG, 2022
A process for recycling waste tires into pyrolysis oil and gas. The process involves pyrolyzing waste tires at 350-400°C using a vertical tower reactor with internal heating and stirring. The pyrolysis gas is combusted to generate high-temperature flue gas. A steam jet pump extracts exhaust gas from the combustion kiln and mixes it with steam to reduce the pressure. This mixed fluid is compressed and discharged back to the kiln. The steam jet pump allows efficient utilization of the high-temperature flue gas as a heat source for pyrolysis, condensing pyrolysis oil into liquid fuel, and recycling pyrolysis gas into fuel.
11. Tire Processing System with Spinning, Magnetic Separation, Flue Gas Transport, and Molten Salt Stirred Reactor Pyrolysis
BEIJING YUNSHUI HAORUI ENV TECH CO LTD, BEIJING YUNSHUI HAORUI ENVIRONMENTAL TECHNOLOGY CO LTD, 2021
A system and method for processing tires that improves efficiency and reduces costs compared to existing methods. The system involves spinning the tires to extract steel wire, crushing the remaining tire, magnetically separating the iron, using flue gas to transport the rubber particles, cycloning the mixture, and pyrolyzing the rubber in a stirred reactor with molten salt. The spinning, magnetic separation, and flue gas transport steps allow recycling the steel and avoiding iron contamination in pyrolysis. The molten salt provides indirect heating and high heat capacity to improve pyrolysis efficiency. The stirring and cycloning steps prevent agglomeration and enable homogeneous pyrolysis.
12. Micro-Negative Pressure Pyrolysis System with Two-Stage Tire Crushing and Microporous Plate Reactor
Fujian Aolin Magnesium Environmental Protection Technology Co., Ltd., FUJIAN AOLINMEI ENVIRONMENTAL PROTECTION TECHNOLOGY CO LTD, 2021
Micro-negative pressure pyrolysis method for recycling waste tires that improves the efficiency and mechanization of tire thermal cracking. The method involves crushing the tires in two stages, injecting the crushed material into a sealed reactor with a microporous plate, heating it under low pressure to 120°C, then increasing the heating rate and pressure to 450°C, and pyrolyzing it at reduced pressure while the solid phase remains on the microporous plate. This allows consistent tire crushing, pyrolysis, and material collection without steel wire stripping.
13. Two-Stage Pyrolysis and Gasification Device with Zoned Gasifier for Processing Waste Tire Derivatives
CHANGSHA INDUSTRY TECH RESEARCH INSTITUTE ENVIRONMENTAL PROTECTION CO LTD, CHANGSHA INDUSTRY TECHNOLOGY RESEARCH INSTITUTE ENVIRONMENTAL PROTECTION CO LTD, 2021
Device for modifying pyrolysis oil and charcoal from waste tires to improve their quality and market value. The device consists of a two-stage process with a pyrolysis furnace followed by a gasifier. The pyrolysis converts the tires into pyrolysis gas and charcoal. The hot pyrolysis gas and charcoal then enter the gasifier where they are further processed. The gasifier has separate zones for gasification, modification, and ash accumulation. This allows further cracking of the gas to remove heavy tars, and separation of remaining organic matter from the charcoal. The modified gas is combusted, and the cleaner charcoal is recovered.
14. Two-Stage Device with Sealed Feeding, Pyrolysis, Gas-Solid Conveying, and Activation Sections for Tire Processing
Dalian University of Technology, DALIAN UNIVERSITY OF TECHNOLOGY, 2021
Integrated device and method for efficiently pyrolyzing and activating waste tires in a two-stage process. The device has a sealed feeding section, a pyrolysis section, a gas-solid conveying channel, and an activation section. The pyrolysis section breaks down the tires into pyrolysis products like oil and gas. The gas-solid conveying channel transfers the pyrolysis gas to the activation section where it reacts with the remaining solid tire pieces to produce further products. The sealed feeding section prevents oxygen from entering during pyrolysis. This two-stage process improves efficiency by maximizing pyrolysis in the first stage and then further converting the remaining solids in the second stage.
15. Pyrolytic Syngas System with Continuous Solid Carbonaceous Material Recycling and Decanter for Water Separation
BOLDER IND, BOLDER INDUSTRIES, 2021
Preventing clogging in a pyrolytic syngas system integrated into a pyrolysis system to improve reliability and safety. The clogging prevention involves continuously removing and recycling a portion of the solid carbonaceous material generated during tire pyrolysis to prevent buildup in the exhaust channel that can cause clogs and pressure buildup. This recycled material is mixed with the incoming feed to dilute and disperse any remaining solid particles in the pyrolysis reactor, reducing the likelihood of clogs. The system also has a decanter to separate and remove water from the light oil cut, preventing corrosion and clogs in downstream components.
16. Pyrolysis System with Modified Carbon Heating Media for Waste Tire Processing
Dalian University of Technology, DALIAN UNIVERSITY OF TECHNOLOGY, 2021
Device and method for efficient and high-value utilization of waste tires through pyrolysis. The pyrolysis process involves heating waste tires without steel wires using modified pyrolysis carbon as a thermosetting carrier. This avoids the need for external heat sources like gas or oil. The modified carbon is produced by incompletely combusting the pyrolysis gas. The modified carbon is then used as the heating media to rapidly pyrolyze the tires. This provides a self-sustaining and efficient pyrolysis process that recovers maximum value from waste tires.
17. Low-Temperature Pyrolysis Method for Waste Tire Recycling in Nitrogen Atmosphere
China University of Petroleum, CHINA UNIVERSITY OF PETROLEUM, China University of Petroleum (East China), 2021
A low-temperature pyrolysis method for recycling waste tires that produces pyrolysis oil, gas, and carbon black. The method involves pyrolyzing tires at lower temperatures in a nitrogen atmosphere. It allows rapid pyrolysis of tires at lower temperatures compared to conventional high-temperature methods. The low-temperature pyrolysis enables continuous operation and reduces energy consumption. It also increases pyrolysis oil yield and decreases gas yield compared to high-temperature pyrolysis.
18. Pyrolysis Device with Internally Installed Screw and External Heater for Waste Tire Processing
Yonsei University Wonju Industry-Academic Cooperation Foundation, 2020
Rapid pyrolysis of waste tires using a device with an internally installed screw and externally installed heater to promote agitation and heat transfer. The device has a sample supply, reaction chamber with screw, heater, carbon black recovery, cyclone, condenser, and dust collector. The screw transports tires, heating by heater and chamber walls. This provides simultaneous internal and external heating for efficient pyrolysis compared to just external heating.
19. Sequential Pyrolysis System for Tire Conversion into Superheated Steam with Integrated Reformer
Fengyang Aiersi Light Alloy Precision Forming Co., Ltd., FENGYANG L-S LIGHT ALLOY NET FORMING CO LTD, 2020
Continuous, efficient and green method to convert waste tires into superheated steam. The method involves pyrolyzing the tires in stages at controlled temperatures to produce pyrolysis oil, carbon black and gas. The pyrolysis devices are connected in sequence. The first device pyrolyzes the tires at a low temperature to yield oil and carbon black. The second device further pyrolyzes the oil at a higher temperature to produce gas. This two-stage pyrolysis allows selective conversion of the tire components into valuable products. The resulting superheated steam is generated by passing the gas through a reformer device heated by combustion of the carbon black. The method provides a closed-loop conversion process that avoids environmental issues like dioxin generation and coking.
20. Segmented Rotary Kiln Pyrolysis Reactor with Adjustable Heaters and Feeders for Continuous Waste Tire Processing
SOUTHEAST UNIVERSITY, UNIV SOUTHEAST, 2020
Segmented temperature-controlled continuous pyrolysis reactor for waste tires that allows precise temperature control, high efficiency, and continuous operation compared to traditional waste tire pyrolysis systems. The reactor has a sectioned rotary kiln with adjustable heaters, thermometers, and feeders. This allows dividing the kiln into zones for preheating, cracking, and heat preservation. The segmented design enables accurate temperature control in each zone for optimal pyrolysis. It also facilitates continuous feeding without blocking or leaks.
Get Full Report
Access our comprehensive collection of 80 documents related to this technology
Identify Key Areas of Innovation in 2025
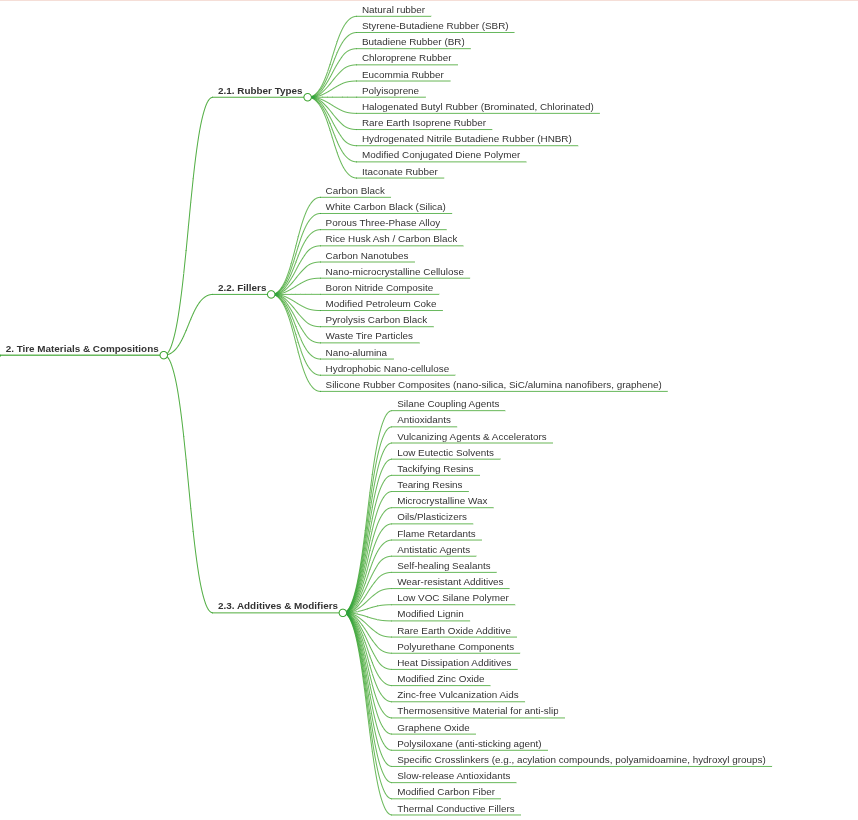