Monitoring Systems for Tire Performance
Modern tire monitoring systems must detect and measure multiple parameters simultaneously across diverse operating conditions. Current sensor arrays track pressure variations of 0.1 PSI, temperature changes of 0.5°C, and sub-millimeter variations in tread depth—all while compensating for road surface irregularities, vehicle dynamics, and environmental factors.
The core challenge lies in integrating multiple sensing modalities while maintaining measurement accuracy and reliability in harsh operating environments.
This page brings together solutions from recent research—including multi-sensor fusion systems, predictive wear modeling, automated pressure management, and real-time vibration analysis. These and other approaches focus on providing actionable insights for both individual vehicle owners and fleet operators while minimizing false alerts and maintenance overhead.
1. Tire Pressure Management System with Real-Time Adaptive Adjustment Based on Environmental and Operational Data
VOLVO CAR CORP, 2025
Adaptive tire pressure management system that optimizes tire pressure based on factors like weather, road conditions, driving habits, and energy levels. The system monitors tire pressure, weather, and road conditions. It then determines the optimal tire pressure for safety and performance in those conditions. The system can adjust tire pressure in real-time while driving or before reaching specific locations. This allows optimizing tire pressure throughout a trip based on changing conditions.
2. Tire Pressure Monitoring System Sensor Assembly with Spiral Locking Protrusions and Cylindrical Housing
THE YOKOHAMA RUBBER CO LTD, 2025
Functional component assembly for tire pressure monitoring systems (TPMS) that provides improved damage resistance compared to prior art designs. The assembly has a support body attached to the tire inner surface to hold a TPMS sensor. The sensor is fixed inside the support body using locking protrusions and recesses. The locking protrusions have specific dimensions and locations to prevent sensor falling out. This configuration provides secure retention of the sensor while allowing easy insertion and removal. The sensor has a columnar shape matching the support body's cylindrical housing. The locking protrusions spiral around the housing and sensor to provide stable fixation. The support body rubber has elongation and modulus properties that balance workability, holding force, and breakage resistance.
3. Method for Dynamic Tire Pressure Regulation Using Multi-Mode Selection and Machine Learning-Based Route Adaptation
VOLVO CAR CORP, 2025
A method for regulating vehicle tire pressure that provides safe, cost-effective tire pressure control tailored to different vehicles, users, and environments. It involves dynamically selecting from multiple tire pressure modes based on vehicle speed, weather, route, road conditions, energy state, etc. Some modes adjust tire pressure based on speed for optimal performance. Other modes have fixed or customized pressures. A machine learning algorithm updates a specific mode for repeated routes based on acceleration. This allows optimized tire pressures for specific conditions.
4. Tire Position Identification System Using Footprint Length Sensors
THE GOODYEAR TIRE & RUBBER CO, 2025
Tire position identification system for vehicles that accurately determines the location of sensors on vehicle tires without requiring frequent communication or complex techniques. The system uses footprint length measurement sensors on the tires to calculate mean footprint lengths when the vehicle is stationary or cruising. By comparing the means, it determines which tire has the longer footprint and identifies its position on the vehicle. This avoids issues like rotation, replacement, and power constraints of other methods.
5. Tire Sensor Position Identification via Real-Time Footprint Length and Acceleration Coefficient Analysis
THE GOODYEAR TIRE & RUBBER CO, 2025
Automatically identifying the position of tire sensors on a vehicle without user input or interactions. The technique uses tire footprint length to determine the wheel position of the tire sensor devices in real time during normal driving. It analyzes acceleration coefficients from the tire sensor data to determine the turning direction without needing GPS or other vehicle-based positioning systems. This allows accurate assignment of tire sensor locations without requiring manual entry or external positioning devices.
6. Tire Pressure Monitoring System with Passive RFID Tags and Proximity-Based Data Transmission
HYUNDAI MOTOR CO, KIA CORP, 2025
A tire pressure monitoring system that reduces power consumption and eliminates the need for sensor ID learning. The system uses passive RFID tags on the tires to transmit tire pressure instead of battery-powered sensors. A nearby RFID reader receives the tire pressure data when the tag is close enough. When the tag moves away, the reader stops receiving. This avoids repeated transmissions. The system also prevents false learning of IDs from nearby vehicles by only learning when close and not traveling.
7. Rubber Patch with Tapered Blind Holes for Tool-Free Sensor Mounting Inside Tires
YOKOHAMA TWS SOCIETA PER AZIONI, 2025
A rubber patch for mounting sensors inside tires that provides a simple, inexpensive, and functional way to attach sensors to tires without interfering with their performance. The patch has blind holes with walls that taper inward. This allows the sensors to be inserted into the holes without tools, and the tapered walls hold them securely. The patch adheres directly to the inner liner of the tire, keeping the sensors in contact with the tire for accurate sensing. The patch dimensions are minimized to minimize interference with sensor readings.
8. Road Surface Condition Detection Using Tire Force Estimation and Vehicle Data Inputs
THE GOODYEAR TIRE & RUBBER CO, 2025
Predicting road surface conditions like wet or dry based on estimated tire forces to enable vehicles to adapt their control systems for optimal performance and safety on different road types. The method involves estimating tire tractive forces using vehicle data like engine torque, speed, acceleration, etc. When the vehicle is steady, these forces are used as inputs to a trained road condition detection model along with speed. The model outputs a probability of wet or dry road based on the estimated forces, which can be used by other vehicle systems to adjust braking, stability, suspension, etc. accordingly.
9. Vehicle Tire Rotation Detection System Utilizing Onboard Sensors for Rolling Radius Discrepancy Analysis
FORD GLOBAL TECHNOLOGIES LLC, 2025
Detecting when a tire rotation is needed for a vehicle using onboard sensors to monitor tire rolling radius and recommending tire rotations based on the difference in rolling radius between the front and rear tires. The system compares the rolling radius difference to a threshold and notifies the driver when it exceeds the threshold, indicating that a tire rotation is recommended. This allows optimizing tire wear by moving the less worn tires to the positions that will wear down faster.
10. Method for Associating Tire Sensors and RFID Tags Using Activation Status Discrimination
VOLVO TRUCK CORP, 2025
Discriminating between tire sensors and RFID tags on a vehicle wheel to properly associate them during assembly. The method involves receiving sensor signals with activation status and RFID tags. It determines which sensor belongs to a wheel based on the activation statuses to prevent confusion when multiple sensors transmit simultaneously. This allows correct association of tire sensors and RFID tags during wheel assembly in noisy environments.
11. Vehicle Tire Sensor with Multi-Mode Ultra-Wideband Device for Sensing, Communication, and Ranging
NXP BV, 2025
A tyre monitoring sensor for vehicles that reduces cost by using an ultra-wideband (UWB) device that can switch between sensing, communication, and ranging modes. The sensor can measure tyre properties, transmit data, and determine its location on the vehicle using UWB. This eliminates the need for separate components to perform these functions. The sensor alternates between sensing, communicating, and ranging modes. After initial ranging to associate the sensor with a wheel, it only ranges on user input.
12. Development of an Intelligent Instrumented Tire for Real-Time Hydroplaning Risk Estimation
alexandru vilsan, corina sandu, gabriel anghelache, 2025
<div>This study introduces an innovative intelligent tire system capable of estimating the risk total hydroplaning based on water pressure measurements within tread grooves. Dynamic represents important safety concern influenced by depth, design, and vehicle longitudinal speed. Existing systems primarily assess using wedge effect, which occurs predominantly in deep conditions. However, shallow water, is far more prevalent real-world scenarios, effect absent at higher speeds, could make existing unable to reliably risk. Groove flow a key factor dynamics, it governed two mechanisms: interception rate pressure. In both cases, groove will increase as result increasing speed for constant depth. Therefore, grooves also approaches critical Unlike conventional systems, proposed design utilizes amplitude shape measured signals from Experimental results indicate that peak increases with hydroplaning. Furthermore, overall signal be By addressing limitations current offers robust solution real-time estimation across diverse driving conditions.</div>
13. Developing smart tire pressure monitoring system: A performance evaluation of ESP32-C3 with ESP-NOW communication
reftito indi muhammad, giva andriana mutiara, muhammad rizqy alfarisi - Conscientia Beam, 2025
This study aims to develop a low-cost and energy-efficient Tire Pressure Monitoring System (TPMS) that provides real-time monitoring of tire pressure temperature using IoT-based wireless communication. The system was built the MS5803-14BA sensor, ESP32-C3 microcontroller, ESP-NOW protocol. Performance tested through laboratory real-world scenarios compared two commercial TPMS systems (Level A B). proposed achieved 95.91% accuracy, closely aligning with Level (99.87%) slightly outperforming B (95.35%). It showed highest sensitivity (10.00%) while maintaining stable readings (6.45%). In contrast, exhibited greater fluctuation (9.68%). protocol enabled reliable, low-power data transmission without interference. developed delivers high accuracy in detecting conditions real time demonstrates superior power efficiency environmental stability, making it strong alternative traditional RF-based solutions. can be integrated into smart vehicles or fleet management platforms, enhancing safety alerts enabling predictive maintenance. Future enhancements will include broader IoT connectivity, impro... Read More
14. Valve Stem Assembly with Externally Replaceable Battery and Spring-Loaded Terminal Connection to Separate Sensor
ASTRA SENSOR TECHNOLOGIES CORP, 2025
A tire pressure monitoring system with an externally replaceable battery in the valve stem. The valve stem has a removable core that holds the battery. The sensor is separate from the stem. The stem connects to the sensor via spring-loaded terminals. This allows battery replacement without removing the tire or stem. The stem interior cavity retains the battery. The stem core removably secures the battery. The stem is separated from the sensor by a connector. The stem has a port for airflow. The battery provides power to the sensor inside the stem.
15. Wheel Balance Monitoring Method Utilizing TPMS Sensor Acceleration Signal Noise Analysis
CONTINENTAL AUTOMOTIVE TECHNOLOGIES GMBH, 2025
A method to monitor wheel balance in vehicles using existing TPMS sensors without additional hardware. The method involves measuring the noise of the raw acceleration signal from each wheel and comparing the variation to detect unbalanced wheels. It uses the standard deviations of the acceleration signals transmitted by the TPMS wheel units. If the variation exceeds a threshold over multiple iterations, indicating simultaneous noise on both wheels, it's interpreted as a bad road rather than wheel imbalance. This prevents false warnings from road vibrations. The reference averages are reset if both wheels exceed a threshold simultaneously to avoid false warnings from road conditions.
16. Tire Pressure Monitoring System with Environmental Condition-Based Alert Calibration
GOODYEAR TIRE & RUBBER, 2025
A tire pressure monitoring system that provides more accurate and contextual tire pressure alerts based on environmental conditions like temperature, humidity, and weather. The system uses sensor data from the tires along with external environmental data to determine if a tire pressure warning is necessary. This allows adjusting the threshold for what constitutes an underinflated tire based on factors like cold weather, rain, and snow. The goal is to avoid false positives and unnecessary alerts in certain conditions where slight pressure drops may be normal.
17. Tire Condition Acquisition and Storage System with Location-Based Data Collection
SUMITOMO RUBBER INDUSTRIES LTD, 2025
Tire management system that can acquire tire condition information when a vehicle visits specific locations like service stations, and store it for later analysis. This allows diagnosing tire issues based on acquired data instead of relying solely on real-time monitoring. The system can also provide guidance to nearby repair shops, coupons for reduced fees, or route information to the closest service center when abnormalities are detected.
18. Tire Wear Estimation System with Independent Sensor-Based Footprint and Shoulder Length Measurement
The Goodyear Tire & Rubber Company, 2024
A tire wear estimation system that accurately and reliably estimates tire wear state using easily obtained and accurate parameters, and which can operate independently of the vehicle CAN bus. The system involves mounting sensors on the tire to measure footprint length and shoulder length, as well as tire pressure and temperature. This data, along with tire identification, is used to predict tire wear using an analysis module.
19. Tire Pressure Monitoring System with Acceleration and Time-Based Sensor Control
SHANDONG HONGSHENG RUBBER TECH CO LTD, SHANDONG HONGSHENG RUBBER TECHNOLOGY CO LTD, SHANDONG HUASHENG RUBBER CO LTD, 2024
Power-saving tire pressure monitoring system that reduces energy consumption by intelligently controlling the sensor operation based on vehicle acceleration and time of day. The system has a microcontroller that monitors sensors like pressure, temperature, and acceleration. It uses a real-time clock to determine the time and day. The microcontroller puts the sensor system into a sleep state when the vehicle is stationary or at night to save power. It wakes up the sensors when acceleration indicates driving or it's daytime. This allows the system to operate without affecting the warning function while minimizing power consumption.
20. Internal Tire Temperature Monitoring System with Integrated Intelligent Sensor and Vehicle Terminal Connectivity
JIANGSU LUBIDA INTERNET OF THINGS TECH CO LTD, JIANGSU LUBIDA INTERNET OF THINGS TECHNOLOGY CO LTD, 2024
Monitoring device and method for detecting internal temperature of dangerous spots in mining tires to prevent blowouts and damage. The device involves installing an intelligent tire sensor inside the tire lining. It connects to a vehicle terminal. The method involves monitoring the sensor readings to detect abnormal temperatures in critical areas like belt joints. Early warning and remote alarm are provided to prevent tire failures. This addresses limitations of surface temperature monitoring, lack of internal sensors, and manual intervention.
The continuous attempts to improve vehicle performance and safety are reflected in developments in tire monitoring technologies. These developmentsᅳwhich include integrated sensor assemblies to real-time feedback devicesᅳprovide vital information that aids drivers in maintaining ideal tire conditions.
Get Full Report
Access our comprehensive collection of 159 documents related to this technology
Identify Key Areas of Innovation in 2025
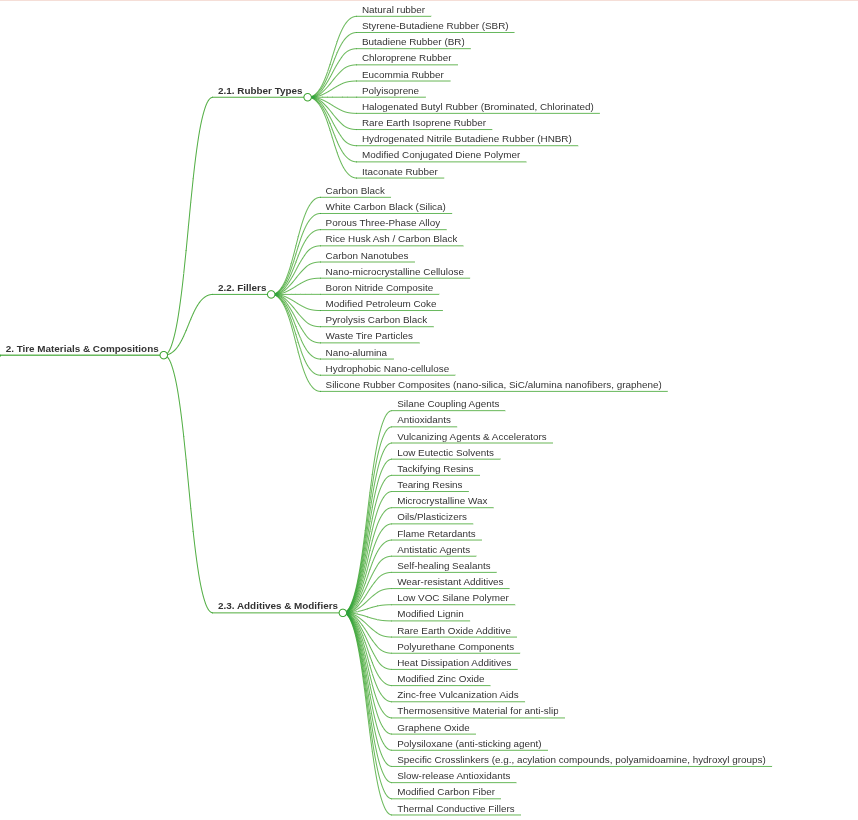