Rubber Compound Mixing in Tire Production
Modern tire manufacturing requires precise control over material interactions at multiple scales - from nano-level filler dispersion to macro-scale compound distribution. Current mixing processes must handle increasingly complex material combinations, including functionalized rubbers, pre-treated silica, and engineered carbon structures, while maintaining strict quality parameters across production volumes that can exceed 500,000 tires per facility annually.
The fundamental challenge lies in achieving uniform dispersion of performance-critical materials while managing the competing requirements of mixing efficiency, thermal control, and final compound properties.
This page brings together solutions from recent research—including novel dispersion techniques for reduced graphene oxide, rotatable applicator systems for compound coextrusion, functionalized rubber technologies, and in-situ material modification approaches. These and other advances are helping manufacturers achieve consistent material distribution while meeting demanding production schedules.
1. Solvent-Free Ball Milling Process for Dispersing Reduced Graphene Oxide in Rubber Composites
Frederic VAUTARD, Compagnie Generale des Etablissements Michelin, 2024
A scalable method to disperse reduced graphene oxide (RGO) in rubber composites without using solvents. The method involves milling RGO with a liquid rubber to improve dispersion and prevent stacking compared to dry milling. The RGO and liquid rubber are ball milled together with milling media until the RGO particles reach the desired size. This milled RGO-liquid rubber mixture can then be added to rubber compounds during mixing. The liquid rubber acts as a co-agent to reduce RGO agglomeration and stacking during rubber processing.
2. Rubber Compound Mixing Method with Pre-Dispersion of Fillers and Processing Aids
HANGZHOU HAICHAO RUBBER CO LTD, ZHONGCE RUBBER GROUP CO LTD, 2024
Mixing method to improve filler dispersion in rubber compounds by pre-dispersing fillers and processing aids before adding the rubber. In the mixing stage, fillers and processing aids are initially stirred in the mixer at lower speeds (40-60 rpm) for 30-200 seconds to fully mix and disperse the fillers. Then rubber is added to continue mixing. This pre-dispersion step shortens filler-processing aid distances and increases contact probability, leading to better filler dispersion and rubber compound properties like wear resistance and dynamic performance.
3. Sequential Mixing Process for Diene Rubber Compositions with Staged Component Integration
CIE GENERALE DES ETABLISSEMENTS MICHELIN, COMPAGNIE GENERALE DES ETABLISSEMENTS MICHELIN, 2023
Process for preparing diene rubber compositions with improved properties for tire treads. The process involves a specific order of mixing steps to optimize the rubber composition. It includes mixing the elastomer matrix alone first, then adding the modification agent, filler, silane, and vulcanization system in separate steps. This sequence allows the elastomer to fully incorporate and disperse before adding the other components. It reduces agglomeration and improves the distribution of filler and silane. The resulting rubber composition has lower hysteresis and higher rigidity compared to conventional mixing orders.
4. Two-Step Mixing Method for Tire Rubber Composition with Sequential Vulcanizing Agent Addition
Nexen Tire Corporation, 2023
A method for preparing a tire rubber composition that improves dispersion of fillers like silica and carbon black to enhance tire performance. The method involves a two-step mixing process. In step 1, raw rubber, fillers, and a low amount of vulcanizing agent are mixed. In step 2, additional vulcanizing agent and accelerator are added to the step 1 product. This two-step mixing sequence improves filler dispersion compared to adding all vulcanization components in step 1.
5. Rubber Composition with Network-Structured Depolymerized Carbon Nanotube Reinforcing Fillers
Michelin Group Headquarters, MICHELIN GROUP CORP, 2023
Rubber compositions containing depolymerized carbon nanotubes as reinforcing fillers for tire components like treads. The carbon nanotubes are aggregated into a continuous network with defects and voids, rather than being dispersed individually. The network structure is achieved by compressing the nanotube powder and shearing it in a mixer. This prevents nanotube entanglement during mixing. The nanotubes have retained their original diameter and wall number. The network nanotubes provide improved physical properties like wear resistance compared to dispersed nanotubes.
6. Device and Method for Rubber Mixture Production Using Tandem Mixers with Differential Blade Speed and Volume Configuration
Continental Reifen Deutschland GmbH, 2023
A method and device for producing rubber mixtures with improved dispersion and homogeneity of fillers like silica, without increasing production time. The method involves two mixers in tandem with specific blade design and volume ratios. The first mixer has higher blade speeds and lower volume. The second mixer has lower blade speeds and higher volume. This allows transferring and mixing the rubber between the mixers at lower speeds for better filler dispersion, while still maintaining efficient mixing overall. The device has a top mixer with higher aspect ratio rotor blades and a bottom mixer with lower aspect ratio rotor blades. The volume of the bottom mixer is higher than the top mixer.
7. Three-Stage Mixing Process for Silica-Filled Rubber Compounds with Controlled Temperature Sequence
HUBEI LINGLONG TIRE CO LTD, SHANDONG LINGLONG TYRE CO LTD, 2023
A mixing process for rubber compounds used in tire production that reduces heat generation during mixing of silica-filled rubber compounds compared to conventional mixing methods. The process uses a three-stage mixing sequence in internal mixers, all at temperatures below 150°C. This allows better dispersion of silica without agglomeration and reduces heat generation compared to longer, multi-stage mixing. The lower temperatures also prevent excessive rubber degradation. The three-stage process involves mixing raw materials, then adding silica and dispersing it, followed by final mixing. This controlled constant temperature mixing sequence improves dispersion of silica and reduces heat generation during mixing of silica-filled rubber compounds for tires.
8. Method for Producing Rubber Composition via Sequential Component Addition and Controlled Kneading Temperature
TOYO TIRE CORP, 2023
A method for producing a rubber composition for tires with improved vulcanization rate, low fuel consumption, and wet road braking performance. The method involves adding certain components like modified polymer, silica, silane coupling agent, zinc oxide, and amine antiaging agent into a closed mixer in a specific order. The kneading temperature is controlled to suppress reactions between the components until a later stage. This prevents agglomeration and improves dispersion of the fillers. Simultaneous kneading at higher temperature allows reactions to proceed while stabilizing the temperature. The optimized order and temperature control allows good dispersion, bonding, and vulcanization properties.
9. Method of Silica Dispersion in Rubber Using Vertical Motion Closed Mixer with Gas Injection
TOYO TIRE CORP, 2023
A method for improving low heat generation, wet road braking performance, and wear resistance in tires by using a closed mixer with a weight that moves up and down during kneading. The mixer has a chamber, neck, and hole. Compressed gas is fed into the chamber through the hole while the weight is not pressed. This closed mixer with vertical movement of the weight allows kneading above the lower limit temperature for silane coupling reaction. Using this closed mixer with gas injection during kneading improves dispersion of silica in rubber compositions for tires.
10. Rubber Compound Mixing and Resting Procedure with Scorch Retarder Adjustment for Stabilized Foaming Point
SAILUN SHENYANG TYRE CO LTD, SAILUN TYRE CO LTD, 2023
Stabilizing the foaming point of final rubber in tire manufacturing to reduce vulcanization time. The stabilization is achieved through a specific mixing and resting process. The final rubber compound is prepared in stages: primary mixing, secondary mixing, and final mixing. The final mixing is done with sulfur and accelerators. The key is to allow the mixed rubber to park for 8-48 hours before extrusion. The scorch retarder dosage is adjusted based on the mixing and resting time. This stabilizes the foaming point and vulcanization time.
11. Rubber Compounding Method Utilizing Closed Internal Mixer at Reduced Temperatures
FUZHOU FUGUANG RUBBER CO LTD, 2023
Rubber mixing method to improve efficiency, homogeneity, and prevent issues like whitening and deglazing in rubber compounding. The method involves mixing rubber compounds at lower temperatures (<110°C) using a closed internal mixer instead of open mixers. This allows adding vulcanization agents like accelerators and sulfur directly during mixing. The lower temperature prevents whitening and deglazing issues. By mixing in the closed internal mixer, it eliminates the need for re-mixing on open mixers to add vulcanization agents. This reduces energy consumption and improves efficiency compared to traditional mixing methods.
12. Tire Rubber Compound Mixing Method with Remilled Master Batches for Uniform Silica Distribution
NEXEN TIRE CORP, 2023
Mixing method for tire rubber compounds to ensure uniformity in compound quality. The method involves preparing multiple master batches, each containing a silica compound, and then remilling and dispersing them together to form the final compound. This creates a uniform crosslinked structure with minimized variation compared to directly compounding the master batches. The remilling step allows consistent distribution of the silica and other components throughout the compound.
13. Rubber Compound Composition Incorporating Syndiotactic 1,2 Polybutadiene with Peroxides
QINGDAO FIHONOR CHEMICAL TECH CO LTD, QINGDAO FIHONOR CHEMICAL TECHNOLOGY CO LTD, 2023
A composition for preparing rubber compound, rubber compound, and a method to prepare it, along with a tire made from the compound. The composition includes natural rubber, butadiene rubber, styrene-butadiene rubber, carbon black, vulcanizing agent, syndiotactic 1,2 butadiene Dienes, peroxides, antioxidants, activators, accelerators, tackifiers, and coupling agents. The key innovation is adding syndiotactic 1,2 polybutadiene to the compound and using peroxides to reduce its crystallization and improve adhesion with other rubbers. This provides tires with improved wear resistance, flame retardancy, and lightweight properties.
14. Sequential Mixer Arrangement for Staged Rubber Compound Production
CONTINENTAL REIFEN DEUTSCHLAND GMBH, 2023
Device and method for efficiently producing rubber compounds, especially for tires, by staging the mixing steps. The device has three interconnected mixers arranged in sequence. The first mixer is loaded with initial ingredients, the second mixer receives the first mixer's output, and the third mixer receives the second mixer's output to complete the compound. This allows staged mixing and reworking of the rubber in multiple steps for improved efficiency compared to a single mixer.
15. Rubber Mixing Process with Sequential Banbury and Parallel Open Mill Stages
HUBEI LINGLONG TIRE CO LTD, SHANDONG LINGLONG TYRE CO LTD, 2023
A rubber mixing process for tires that reduces loss of vulcanizing agents during mixing to improve tire quality. The process involves using a banbury mixer followed by multiple parallel open mills for supplementary mixing. The banbury mixer initially mixes the rubber, then evenly divides the batch between the parallel open mills for further mixing. This longer supplementary mixing compensates for the reduced rubber quantity in each mill compared to fewer parallel mills, preventing quality fluctuations and loss of volatile additives.
16. Method for Coextruding Tire Components Using Rotatable Applicator Head with Variable Compound Ratios
The Goodyear Tire & Rubber Company, 2022
A method for forming tire components like treads using a rotatable applicator head to coextrude rubber compounds with varying volume ratios. The rotatable head allows complex tire designs with specific performance and durability characteristics by coextruding multiple compounds from a single head. The head rotates around the tire build direction to prevent material curling and ensure uniform flow as the rubber changes direction. This allows efficient production of coextruded strips with varied compound ratios that can be used to manufacture complex tire components like treads with improved performance and durability.
17. Rubber Mixing Process with Internal Mixer-Based Masterbatch Refinement and Sulfur Integration
SHANDONG LINGLONG TYRE CO LTD, 2022
A one-step rubber mixing process for tires that improves efficiency, reduces costs, and provides better rubber quality compared to conventional one-shot mixing methods. The process involves refining the masterbatch in an internal mixer instead of adding sulfur directly in the mill. This reduces mixing time, eliminates issues like sticking, spilling, and inconsistent vulcanization. By returning a portion of the refined masterbatch to the mixer along with calculated amounts of sulfur, the desired rubber properties are achieved.
18. Automated Two-Stage Rubber Mixing System with Sequential Banbury Mixers and Integrated Material Feeders
Sichuan Chuanhuan Technology Co., Ltd., SICHUAN CHUANHUAN TECHNOLOGY CO LTD, 2022
Automated rubber mixing system and method to improve efficiency, quality and consistency of rubber compounding. The system involves a two-stage mixing process with separate banbury mixers. Raw materials except vulcanizing agent and accelerator are mixed in the first banbury. The product is then transferred to the second banbury where vulcanizing agent and accelerator are added for final mixing. The first mixing stage temperature is higher than the second stage to enable better homogenization. This two-step process allows better control and consistency of mixing compared to conventional single-stage mixing. The system also uses automated feeders to precisely measure and add materials instead of manual weighing. The automated feeders are connected to the mixers and the system monitors and controls the mixing parameters.
19. Apparatus with Dual Mixing Chambers and Transfer Device for Sequential Rubber and Additive Mixing
CONTINENTAL REIFEN DEUTSCHLAND GMBH, 2022
Device and method for producing rubber mixtures used in tire manufacturing that improves efficiency and processability. The device has two mixing chambers connected by a transfer device. One chamber mixes rubber and filler, the other chamber mixes additives like zinc oxide and diamines. Solid additives are fed directly into the second chamber. This allows separate optimization of base rubber and additive mixing. The transfer device moves the base rubber into the second chamber for final mixing. The method involves separately mixing the rubber/filler and additives in each chamber, then transferring the rubber to the additive chamber for final mixing. This enables better control over the rubber properties and additive distribution compared to mixing everything together.
20. Single-Stage Rubber Component Mixing Process with Sequential Additive Integration and Reduced Dump Temperature
CEAT LTD, 2022
Mixing rubber components using a single stage process that reduces the dump temperature of the final rubber mixture to a temperature below 120°C. The mixing includes mixing at least one polymer, a peptizer, a soft carbon black and at least one first additive sequentially in an internal mixer to obtain a first mixture; b) contacting the first mixture with a cold oil to obtain a second mixture; and c) kneading the second mixture with at least one second additive to obtain a final rubber mixture.
Get Full Report
Access our comprehensive collection of 134 documents related to this technology
Identify Key Areas of Innovation in 2025
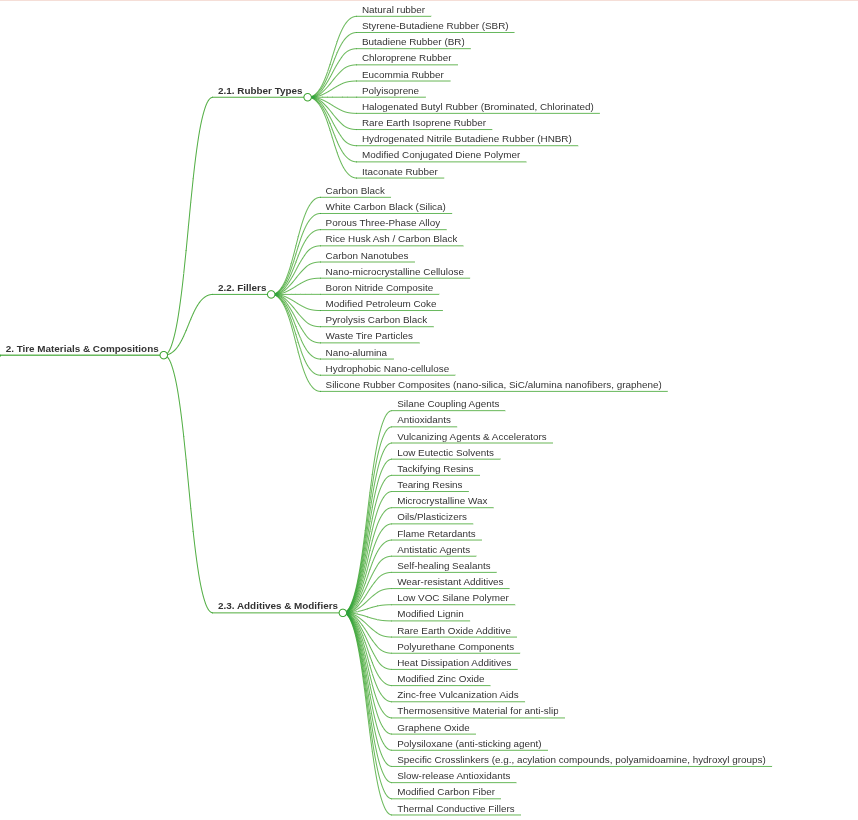