Sulfur Reduction Methods for Tire Pyrolysis Oil
Tire pyrolysis oil (TPO) typically contains 0.5-2.0 wt% sulfur compounds, primarily as heterocyclic forms like benzothiophenes and dibenzothiophenes. These sulfur species not only limit the direct use of TPO as a fuel but also pose challenges during upgrading processes, where they can deactivate catalysts and contribute to equipment corrosion.
The fundamental challenge lies in removing sulfur compounds while preserving the valuable hydrocarbon fractions and maintaining economic viability of the overall process.
This page brings together solutions from recent research—including oxidative desulfurization, hydroprocessing with optimized catalysts, solvent extraction methods, and selective distillation approaches. These and other techniques focus on achieving commercial fuel specifications while managing operational costs and maintaining process efficiency.
1. Microwave-Assisted Pyrolysis Reactor with Zoned Temperature Control for Sequential Decomposition of Polymer Waste
MICROWAVE SOLUTIONS GMBH, 2025
Pyrolysis method and reactor for sustainable recycling of polymer waste like tires by fast thermal decomposition using microwaves. The method involves sequential decomposition of the waste's different components at targeted temperatures to maximize recovery and minimize ash. The reactor has a chamber with microwave heating that can rapidly heat the waste to decomposition temps. The microwaves directly heat the compounds to their decomp temps based on their microwave absorption. This allows selective removal of components like sulfur. The reactor can also have zones with varying temps for staged decomposition.
2. Waste tire-based pyrolysis for synthetic fuel and study of its properties
abdugaffor khurmamatov, kumush shakhobiddin kizi akhmedova, giyosiddin o sidikov - The Oil and Gas Institute - National Research Institute, 2025
Thermal pyrolysis of waste tires is an economically viable industrial method for material recovery and energy production. This article presents the results research on processing used car by in a nitrogen-free environment under atmospheric pressure. Tires sourced from local vulcanization center were as raw material. The process was conducted using experimental setup consisting reactor, collector gases liquids, condenser. For experiment, 4180 g tire fragments used. carried out at temperature 500C pressure one hour. As result, 1800 ml oil, 1320 carbon black, 600 metallic cord, 630 gas obtained. physical properties oil studied: density 0.906 kg/m3, kinematic viscosity 0.75 mm2/s, acidity 104.4 mg/dm3. Infrared spectroscopy analysis revealed presence aromatic, alkene, alkyne groups. Liquid fuel obtained distillation unit. From 150 60 liquid produced. Elemental indicated that contained nitrogen (2.57%) sulfur (1.27%).
3. Fixed Bed Reactor Hydroprocessing of Heavy Fossil Oil with Pyrolysis Oil Integration
IFP ENERGIES NOUVELLES, IFP ENERGIES NOW, 2024
Hydroprocessing heavy fossil oil feeds containing minor amounts of pyrolysis oil from plastics, tires, and solid waste to produce lower sulfur, lower viscosity fuels meeting specifications without additives. The process involves hydroconversion of the heavy oil in a fixed bed reactor. The presence of the light pyrolysis oil lowers sulfur and viscosity to meet fuel requirements. This allows direct production of lower sulfur fuels while valorizing the difficult-to-recover pyrolysis oil.
4. Sequential Hydrogenation Process for Waste Tire Pyrolysis Oil Using Dual-Stage Catalytic Treatment
LUOYANG AOHONG PETROCHEMICAL ENGINEERING TECH CO LTD, LUOYANG AOHONG PETROCHEMICAL ENGINEERING TECHNOLOGY CO LTD, 2024
Hydrotreatment process for waste tire pyrolysis oil that overcomes issues like high diolefin content, high sulfur, nitrogen, and chlorine levels. The process involves a specific sequence and catalyst to enable hydrogenation of waste tire pyrolysis oil. It includes mixing the pyrolysis oil with hydrogen at high pressure (15 MPa or more) to hydrogenate the oil. This is followed by a second mixing step with hydrogen at lower pressure (5 MPa or more) using a different hydrogenation catalyst. This two-step hydrogenation sequence allows effective hydrogenation of the oil without deactivating the catalyst due to sulfur and nitrogen levels.
5. Two-Step Selective Adsorption Method for Sulfur and Nitrogen Removal from Cracked Diesel Oil Using SMIP Adsorbents and Modified Hydroxyl Alumina Catalysts
CHINA UNIVERSITY OF PETROLEUM BEIJING, UNIV CHINA PETROLEUM BEIJING, 2023
Cleaning method for removing sulfur and nitrogen from cracked diesel oil containing high levels of sulfur and nitrogen compounds, such as pyrolysis oil from waste tires. The cleaning involves a two-step process using specific catalysts and adsorbents. The first step is selective adsorption of benzothiophene using benzothiophene-selective SMIP adsorbent. The second step is selective adsorption of 4,6-dimethylbenzothiophene using 4,6-dimethylbenzothiophene-selective SMIP adsorbent. This two-step process using specialized adsorbents improves the desulfurization and denitrification efficiency of the cracked oil. The catalysts used in the hydrofinishing step have modified hydroxyl alumina carriers with dispersed metal sites
6. Method for Selective Adsorption and Catalytic Hydroprocessing of Sulfur- and Nitrogen-Containing Pyrolysis Diesel Oil
CHINA UNIVERSITY OF PETROLEUM BEIJING, UNIV CHINA PETROLEUM BEIJING, 2023
A high-value utilization method for sulfur- and nitrogen-containing pyrolysis diesel oil from waste tires. The method involves selective adsorption of quinoline, indole, and carbazole using specialized adsorbents, followed by hydrodesulfurization and denitrogenation using a modified catalyst. This removes sulfur and nitrogen compounds efficiently. The cleaned oil is further processed to extract aromatics, which are then hydrocracked into low-carbon aromatics. The method improves yield of valuable products like low-carbon aromatics while reducing waste from high-sulfur, high-nitrogen pyrolysis diesel.
7. Sulfur-Containing Pyrolysis Gasoline Cleaning Method with Multi-Stage Selective Adsorption, Hydrodesulfurization, and Distillation Using Tailored Catalysts
CHINA UNIVERSITY OF PETROLEUM BEIJING, UNIV CHINA PETROLEUM BEIJING, 2023
Cleaning method for sulfur-containing pyrolysis gasoline that uses specific catalysts and processes to efficiently remove sulfides from the oil. The cleaning involves three stages: (1) Selective adsorption of thiophene, 2-methylthiophene, and 3-methylthiophene from the oil using specialized adsorbents. (2) Hydrodesulfurization of the intermediate oil using a catalyst with dispersed active metals on hydroxylated nano-alumina. (3) Further distillation and cracking of the cleaned oil. The catalysts are designed to match the specific sulfur compounds in pyrolysis oil and improve desulfurization efficiency.
8. Method and Apparatus for Clarifying Pyrolysis Oil Using Polar Solvent Separation and Clay-Based Solvent Regeneration
RJ Lee Group, Inc., RJ LEE GROUP INC, 2022
Method and apparatus for clarifying pyrolysis oil obtained from waste materials like tires to remove impurities like sulfur and amines, reduce odor, and lower polyaromatic hydrocarbons (PAHs). The process involves separating the pyrolysis oil from a polar solvent using distillation or a wiped film evaporator. The solvent is chosen to adsorb polar compounds in the oil. After separation, the clarified oil has a lighter yellow color and reduced PAH levels. The solvent is regenerated by passing through clay to extract adsorbed impurities. This allows continuous operation limited by clay column capacity.
9. Process for Recovering Desulfurized Fuel Oil and Fuel Gas from Waste Tires via Hydroprocessing and Distillation
WASTEFRONT AS, 2022
Economical process to recover desulfurized fuel oil and fuel gas from waste tires by using a combination of hydroprocessing and distillation. The process involves hydroprocessing tire pyrolysis oil to desulfurize it, followed by distilling the hydroprocessed oil to separate into different fuel products like kerosene, naphtha, fuel oil, fuel, and diesel. The process allows converting impurities in tire pyrolysis oil into higher-value fuels while removing sulfur. It also involves using byproduct fuel and electrolysis to produce low-cost hydrogen for the hydroprocessing step. This leverages the excess fuel and hydrogen availability from pyrolysis to reduce costs.
10. Process for Sulfur Compound Adsorption and Distillation in Tire Pyrolysis Oil with Regenerable Adsorbent
WASTEFRONT AS, 2022
Economically recovering desulfurized fuel products from pyrolysis oil of waste tires by adsorption, distillation and regenerating the regenerable adsorbent material for reuse. The process involves adsorbing polar sulfur compounds from the tire pyrolysis oil using a regenerable adsorbent. The adsorbed oil is then distilled to separate into fuel products like kerosene, naphtha, fuel oil, fuel and diesel. The adsorbent is regenerated using hot gas and reused. This allows extracting high-quality fuels from tire pyrolysis oil while recovering sulfur compounds as a separate stream for utilization.
11. Catalytic Desulfurization Process for Waste Tire Pyrolysis Oil Using Regenerable Zeolite Y
Yingde Trump Environmental Protection Technology Co., Ltd., YINGDE ECO-PYROLYSIS ENVIRONMENTAL PROTECTION TECHNOLOGY CO LTD, 2021
Efficient desulfurization of waste tire pyrolysis oil without hydrogenation to reduce energy consumption compared to hydrodesulfurization. The process involves using a catalyst like zeolite Y to remove sulfur from the oil. The catalyst is regenerated after deactivation by burning off carbon buildup using steam and air. This allows reusing the catalyst instead of replacing it, reducing costs compared to hydrodesulfurization which requires hydrogen and new catalysts.
12. Method for Producing Oil from Waste Tires via Pressurized Ammonia Pyrolysis
NANJING FORESTRY UNIVERSITY, UNIV NANJING FORESTRY, 2021
A method to produce high quality oil from waste tires that involves crushing the tires, pyrolyzing them under pressure in ammonia, extracting the oil, and refining it. The pyrolysis is done at 425°C for 2 hours under 6.2 MPa pressure. This yields an oil with low sulfur and nitrogen content that can be further refined into a product similar to industrial grade oil.
13. Regeneration Process for Adsorbent with Precursor Solution in Adsorption Desulfurization
China University of Petroleum, Beijing Zhongshi Daxin Energy Research Institute Co., Ltd., CHINA UNIVERSITY OF PETROLEUM, 2020
Regenerating a targeted anchoring and separating agent for sulfur in oil that can be used in adsorption desulfurization processes. The regeneration involves heating the adsorbent in the presence of a specific precursor solution. The precursor selectively adsorbs onto the adsorbent's surface, replacing the sulfur compounds. The adsorbent can then be desulfurized by passing oil through it. The desulfurized adsorbent is then regenerated by heating it in the precursor solution. This regeneration process allows recycling the adsorbent without burning off oil or producing sulfur oxides.
14. Hydrotreating Process for Pyrolysis Products Using Cobalt-Molybdenum Catalyst on Aluminosilicate Carrier
Bondarenko Mykhailo Serhiiovych, 2019
Hydrotreating pyrolysis products from used tires to produce cleaner motor fuels. The hydrotreating involves optimized conditions using a catalyst with cobalt and molybdenum on an aluminosilicate carrier. The conditions are a temperature of 330-370°C, pressure of 2.2-2.6 MPa, volumetric feed rate of 1.5-3.0 hours-1, and a hydrogen-to-feed ratio of 200-300 nm3/m3. This allows high desulfurization (96.5-98.0%) and hydrogenation (98.1-99.5%) of the gasoline-kerosene fraction, and moderate desulfurization (94.8-96.7%) and hydrogenation (56
15. Thin-Film Distillation and Oxidative Desulfurization Process for Fractionation of Pyrolysis Oil from Tire Waste
RJ LEE GROUP INC, 2019
A process for separating pyrolysis oil from tire waste into two fractions: a lighter, commercially valuable fraction and a heavier, usable-as-fuel fraction. The process involves an initial thin-film distillation to separate a lighter fraction and a heavier fraction. The lighter fraction is further distilled to isolate the valuable components. The heavier fraction undergoes oxidative desulfurization to remove sulfur and nitrogen compounds, producing a usable fuel oil.
16. Desulfurized and Hydrogenated Rubber-Filled Oil with Reduced Aromatic Hydrocarbon Content
China Petroleum & Chemical Corporation, Anhui Shilian Special Solvent Co., Ltd., Guangdong University of Technology, 2018
An environmentally friendly rubber-filled oil for use in tire manufacturing that reduces pollution compared to traditional rubber-filled oils. The oil is prepared by desulfurizing and hydrogenating a furfural-extracted oil, followed by stripping of hydrogen sulfide. The process involves catalytic hydrodesulfurization and hydrogenation reactions. The resulting oil has lower aromatic hydrocarbons and sulfur levels, making it compliant with EU restrictions.
17. System for Producing Fuel Oil from Waste Tires via Rotary Cracking and Desulfurization Components
NINGBO UNIVERSITY OF TECHNOLOGY, UNIV NINGBO TECHNOLOGY, 2017
A system for producing low sulfur fuel oil by cracking waste tires. The system uses a rotary cracking furnace, condenser, stripping tower, gas cabinet, and desulfurization absorption tower. The waste tires are cracked in the furnace to produce pyrolysis gas. The gas is condensed in the condenser to extract fuel oil. The condensate is further stripped of non-condensable gases in the stripping tower. The stripped condensate is desulfurized in the desulfurization absorption tower to remove sulfur compounds and produce low sulfur fuel oil.
18. Microwave Pyrolysis System for Fractionating Vapors from End-of-Life Tire Decomposition
COOPERATIVA AUTOTRASPORTATORI FIORENTINI CAF -SOCIETA COOPERATIVA A RL, 2014
Recycling end-of-life tires using microwave pyrolysis to produce valuable products like fuel oils and gases. The microwave pyrolysis process involves heating the tires in a microwave oven to decompose them into gases, liquids, and solids. The key innovation is fractionating the vapors from the pyrolysis reaction before condensing them. This allows separating the gases and liquids into different streams. By adjusting the microwave power and heating rate, pyrolysis oils with low sulfur content and high distillable hydrocarbon fractions can be obtained.
19. Hydroprocessing of Pyrolysis Oil Using Non-Aluminum Catalyst for Reduced Sulfur Fuel Blending
EXXONMOBIL RES & ENG CO, EXXONMOBIL RESEARCH AND ENGINEERING COMPANY, HICKEY KARLTON J, 2011
Producing reduced sulfur fuels like diesel or home heating oil by hydroprocessing pyrolysis oil to reduce its sulfur content, then blending the hydroprocessed pyrolysis oil with a higher sulfur base fuel to make an overall lower sulfur fuel. The hydroprocessing conditions involve using a non-aluminum catalyst and low hydrogen-to-oil ratio. The lower sulfur pyrolysis oil is then blended with a higher sulfur base fuel to create a lower sulfur final fuel. This allows using pyrolysis oil as a fuel component without strict sulfur limits, then blending with higher sulfur base fuels to meet sulfur specifications.
Get Full Report
Access our comprehensive collection of 19 documents related to this technology
Identify Key Areas of Innovation in 2025
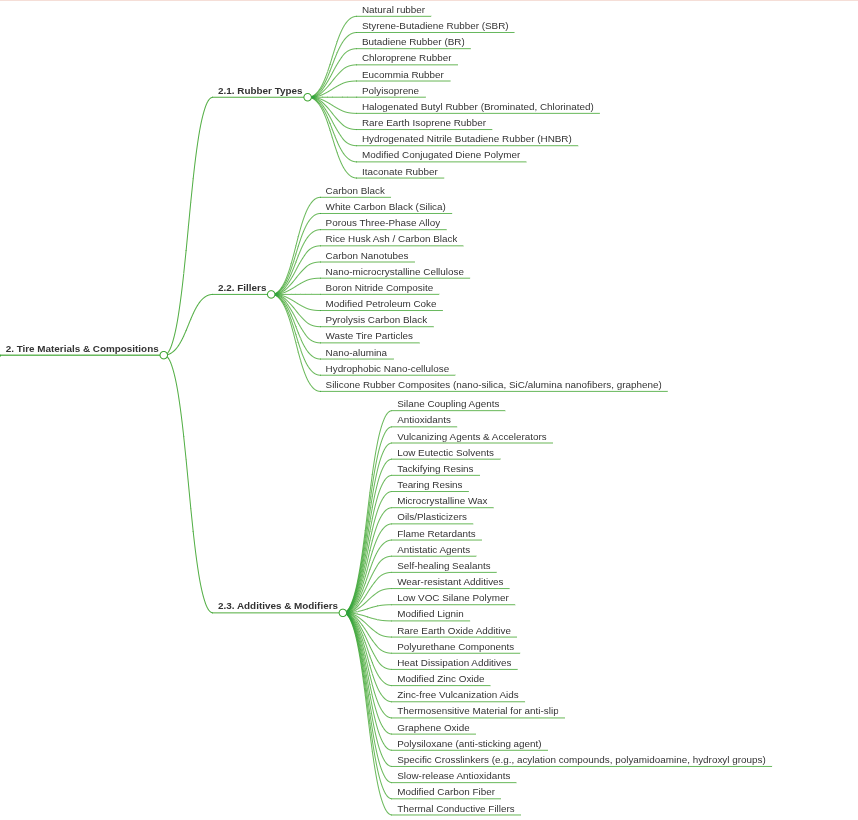