Techniques to Control Tire Temperature
Tire heat management presents a critical engineering challenge, with operating temperatures routinely reaching 50-85°C during normal driving conditions and exceeding 100°C during high-performance use. This thermal loading affects everything from compound durability and wear characteristics to rolling resistance and grip performance, with temperature variations of just 10°C significantly impacting tire behavior.
The fundamental challenge lies in balancing heat generation, retention, and dissipation across different tire components while maintaining optimal mechanical properties throughout the operating temperature range.
This page brings together solutions from recent research—including targeted thermal conductivity zones in tread compounds, advanced rubber compositions with optimized hysteresis characteristics, multi-component temperature management systems, and strategic heat dissipation designs. These and other approaches offer practical methods for managing tire thermal loads while preserving performance metrics.
1. Tire Cooling Fixture with Cup Segments for Tread-Only Engagement
COMPAGNIE GENERALE DES ETABLISSEMENTS MICHELIN, 2025
A fixture for holding a cured tire during cooling without deforming the sidewalls. The fixture has cup segments with contact surfaces shaped to only engage the tread of the tire. This allows the tire to be held upright and cooled without contacting the sidewalls, preventing deformation that would occur if cooled horizontally. The tire can cool without inflation since it's held upright by the tread contact.
2. Rubber Composition for Sidewalls with Solution-Polymerized Aromatic Vinyl-Conjugated Diene Copolymer and Carbon Black
ZEON CORP, ZS ELASTOMERS CO LTD, 2025
Rubber composition for sidewalls that provides a cross-linked rubber with reduced heat buildup, high reinforcing ability, and improved tear resistance compared to conventional sidewall rubbers. The composition contains a specific type of solution-polymerized aromatic vinyl-conjugated diene copolymer with functional groups that interact with carbon, along with carbon black. The copolymer has a vinyl content of 0-50% in the conjugated diene units and 0.5-25% aromatic vinyl content. This composition enables sidewall rubbers with lower heat generation, higher reinforcement, and better tear resistance.
3. Numerical Study on the Influence of Cooling-Fin Geometry on the Aero-Thermal Behavior of a Rotating Tire
kintak raymond yu, sangwook lee - Multidisciplinary Digital Publishing Institute, 2025
An excessive temperature rise in vehicle tires during driving can degrade dynamic performance, safety, and fuel efficiency by increasing rolling resistance softening materials. To mitigate these issues, it is essential to enhance the cooling performance of without inducing significant aerodynamic penalties. In this study, we propose use sidewall-mounted fins investigate their aero-thermal effects under both ground-contact no-ground-contact conditions. Seven fin configurations were tested, with installation angles ranging from 67.5 67.5, positive indicating an orientation opposite direction wheel rotation negative alignment rotation. High-fidelity unsteady Reynolds-averaged NavierStokes simulations conducted using SST k-w turbulence model. The sliding mesh technique was employed capture transient flow behavior induced tire results showed that, conditions, 45 configuration achieved a 16.8% increase convective heat transfer drag less than 3%. Under 22.5 increased over 13% minimal penalty (~1.7%). These findings provide valuable guidance for designing passive solutions that... Read More
4. Closed-Loop Tire Inflation System with Convective Fluid Cooling and Continuous Pump Circulation
APERIA TECHNOLOGIES INC, 2025
A tire inflation system that uses a closed-loop convective cooling system to efficiently and continuously inflate tires without external power sources. The system uses a pump to circulate fluid between stages to maintain pressure in the tires. The fluid is cooled in the stages by convective cooling to prevent overheating. The closed-loop design allows continuous operation without external power.
5. Vehicle Tire Heating System Utilizing Excess Braking Energy with Electrical Power Source Integration
VOLVO TRUCK CORP, 2025
A tyre heating system for vehicles like trucks that can increase range by capturing excess electrical power generated during braking and using it to heat the tires instead of wasting it. The system has an electric power source like an electric motor or fuel cell that generates excess power during braking. When this exceeds the battery charging capability, it feeds the excess to the tire heating system. This avoids wasting the power and uses it to heat the tires, reducing rolling resistance and improving range.
6. Polyurethane Composition with Ester/Ether Copolymer Polyol Derived from Polyether Polyols, Polyhydric Alcohols, and Multifunctional Carboxylic Acids
DOW GLOBAL TECHNOLOGIES LLC, 2025
Polyurethane composition, foam, and molded products with improved properties for applications like tires. The composition has a unique ester/ether copolymer polyol derived from polyether polyols, polyhydric alcohols, and multifunctional carboxylic acids. Incorporating this copolymer into the polyurethane main chain enhances properties like internal heat buildup, thermal stability, tear strength, abrasion resistance, and hydrolysis resistance. It enables preparing microcellular polyurethane foams with the copolymer incorporated in the chain to improve properties like internal heat buildup, thermal stability, tear strength, abrasion resistance, and hydrolysis resistance.
7. Tire Tread with Multi-Thickness Cutouts for Enhanced Durability and Heat Management
COMPAGNIE GENERALE DES ETABLISSEMENTS MICHELIN, 2025
Tire tread design for heavy vehicles like dump trucks that improves durability on rough terrain and heat dissipation. The tread has blocks separated by sipes and has optimized cutout thicknesses. The outer portion of each cutout is thin, less than 20% of the cutout depth, while the inner portion is thicker. This balances crack resistance and venting. Outer transverse cutouts, internal cutouts in blocks, and outer longitudinal cutouts have similar thickness profiles.
8. Development of an Intelligent Instrumented Tire for Real-Time Hydroplaning Risk Estimation
alexandru vilsan, corina sandu, gabriel anghelache, 2025
<div>This study introduces an innovative intelligent tire system capable of estimating the risk total hydroplaning based on water pressure measurements within tread grooves. Dynamic represents important safety concern influenced by depth, design, and vehicle longitudinal speed. Existing systems primarily assess using wedge effect, which occurs predominantly in deep conditions. However, shallow water, is far more prevalent real-world scenarios, effect absent at higher speeds, could make existing unable to reliably risk. Groove flow a key factor dynamics, it governed two mechanisms: interception rate pressure. In both cases, groove will increase as result increasing speed for constant depth. Therefore, grooves also approaches critical Unlike conventional systems, proposed design utilizes amplitude shape measured signals from Experimental results indicate that peak increases with hydroplaning. Furthermore, overall signal be By addressing limitations current offers robust solution real-time estimation across diverse driving conditions.</div>
9. Developing smart tire pressure monitoring system: A performance evaluation of ESP32-C3 with ESP-NOW communication
reftito indi muhammad, giva andriana mutiara, muhammad rizqy alfarisi - Conscientia Beam, 2025
This study aims to develop a low-cost and energy-efficient Tire Pressure Monitoring System (TPMS) that provides real-time monitoring of tire pressure temperature using IoT-based wireless communication. The system was built the MS5803-14BA sensor, ESP32-C3 microcontroller, ESP-NOW protocol. Performance tested through laboratory real-world scenarios compared two commercial TPMS systems (Level A B). proposed achieved 95.91% accuracy, closely aligning with Level (99.87%) slightly outperforming B (95.35%). It showed highest sensitivity (10.00%) while maintaining stable readings (6.45%). In contrast, exhibited greater fluctuation (9.68%). protocol enabled reliable, low-power data transmission without interference. developed delivers high accuracy in detecting conditions real time demonstrates superior power efficiency environmental stability, making it strong alternative traditional RF-based solutions. can be integrated into smart vehicles or fleet management platforms, enhancing safety alerts enabling predictive maintenance. Future enhancements will include broader IoT connectivity, impro... Read More
10. Construction Vehicle Tire with Cavities Containing Silica-Filled Low-Hysteresis Elastomer Layer
COMPAGNIE GENERALE DES ETABLISSEMENTS MICHELIN, 2025
Heavy duty construction vehicle tire with reduced crown temperature for longer tire life. The tire has cavities extending into the tread from the surface or edge that contain a low-hysteresis elastomer layer with silica filler. The depth of the cavities varies linearly with the silica content of the adjacent low-hysteresis layer. This allows heat exchange between the cavities and external environment to dissipate internal tire heat.
11. Vehicle Tire Cooling System with Deployable Airflow Deflector Panels
BRIDGESTONE AMERICAS TIRE OPERATIONS LLC, 2025
Active cooling system for vehicle tires that uses deployable deflector panels to increase airflow around the tires and prevent overheating. The deflector panels are mounted adjacent to the wheels and can extend outward beyond the vehicle body when deployed. This directs more air around the tires during driving, increasing convective cooling compared to when the panels are retracted. Sensors monitor tire conditions and if temperature exceeds a threshold, the panels deploy to boost airflow and prevent overheating.
12. Pneumatic Tire Tread with Dual-Compound Thermal Conductivity and Defined Groove Geometry
SUMITOMO RUBBER INDUSTRIES LTD, 2025
Pneumatic tire with improved grip and durability at high speeds. The tire has a tread with at least two rubber compounds with different thermal conductivities in the ground contacting surface. This allows efficient heat dissipation during high-speed running to prevent excessive heat buildup. The tire also has specific dimensions and groove geometry to further enhance grip and durability.
13. Pneumatic Tire with Shoulder Rib Depressions Having Angled Flanks and Convex Base
CONTINENTAL REIFEN DEUTSCHLAND GMBH, 2025
Pneumatic vehicle tire with improved cooling and stone trapping resistance in the shoulder region. The tire has sidewall and tread with a shoulder-side profile rib containing depressions. The depression openings are elongated rectangular or trapezoidal, with angled end flanks and a base that transitions from inner base to outer base to a convex middle base. The depression length is 30-50% of the rib width. This shape provides better cooling by maximizing surface area and stone trapping resistance by preventing stone retention. The zigzag groove shape and depression placement beside bend inner sides further improves rigidity and cooling.
14. Tire Thermal Model with State Observer Integration for Enhanced Real-Time Temperature Prediction
a longobardi, sanjay raghav balaga, mario labella, 2025
<div class="section abstract"><div class="htmlview paragraph">This paper focuses on the development of a tire thermal model for automotive applications, addressing challenge accurately predicting temperatures different layers tire, under various driving conditions. The primary goal is to enhance understanding temperature behavior improve safety, performance, and durability. research utilizes physics 1-D from which system differential equations, describing interaction between derived. Furthermore, state observer used estimate temperatures, using Tire Pressure Monitoring System (TPMS) measurements correct predictions. In particular, TPMS are assumed be sufficient exclude additional contributions coming rims disk brakes, simplifies model, making it more suitable real-time applications. A calibration procedure defined deriving parameters, based data collected in maneuvers. For validation, predicted tread surface have been compared with infrared sensors measurements.</div><div paragraph">The final demonstrates how can differ across layers. use non-linear crucial... Read More
15. Cylindrical Load Wheel Hub with Chemically Bonded Non-Pneumatic Tire and Enhanced Heat Dissipation Properties
SUPERIOR TIRE & RUBBER CORP, 2025
Load wheel for vehicles like forklifts that has a hub design to improve performance and longevity by dissipating heat more effectively than traditional solid steel hubs. The hub has a cylindrical shape with bearings in the center core. The outer surface is smooth and free of projections that mechanically engage the tire. Instead, a non-pneumatic tire is bonded chemically to the hub using adhesive. This isolates the heat generated by the bearings from the tire elastomer, preventing thermal breakdown and bond failure. The hub has lower mass, higher surface area, and better heat transfer properties compared to solid steel hubs. This allows excess heat to be dissipated more efficiently, reducing temperatures experienced by the tire bond and bearings.
16. Non-Pneumatic Electric Wheel with Integrated Motor and Dual-Shell Cooling System
NANJING UNIV OF AERONAUTICS AND ASTRONAUTICS, NANJING UNIVERSITY OF AERONAUTICS AND ASTRONAUTICS, 2024
Non-pneumatic electric wheel with integrated motor and temperature control for electric vehicles. The wheel has a hub, spokes, rim, tread, motor, and two shells. It uses a unique cooling system to maintain optimal motor and tire temperatures. The wheel has a heat dissipation module inside the inner shell. A heat sink attached to the motor transfers heat to a cooling fluid. The outer shell has vents to exhaust the hot fluid. The cooling system also has a thermostat to regulate temperature. When the motor gets too hot, the thermostat closes a valve to restrict fluid flow. When the motor cools, the valve opens. The wheel also has a tire pressure sensor to monitor tire temperature. If the tire gets too cold, a heating element inside the rim warms it. The wheel's unique design allows integrated temperature control for both the motor and tires.
17. Method for Tire Temperature Regulation via Integrated Liquid and Gas Circulation Paths with Condition-Based Control
GREAT WALL MOTOR CO LTD, GREAT WALL MOTOR COMPANY LTD, 2023
Method for controlling tire temperature in vehicles using circulating liquid and gas paths to heat or cool tires. The method involves detecting ambient temperature, tire temperature, and vehicle conditions like speed and pressure to decide whether to heat or cool tires. It uses a liquid treatment module to circulate heated/cooled fluid through the tires for temperature control, and a gas treatment module to circulate heated/cooled gas through the tires. This bilateral control using liquids and gases allows more efficient and flexible tire temperature regulation compared to just relying on ambient air or external heat sources.
18. Pneumatic Tire with Differential Thermal Conductivity Tread Regions
SUMITOMO RUBBER INDUSTRIES, LTD., 2023
A pneumatic tire that exhibits excellent grip performance and durability during high-speed running, and also improved fuel efficiency. The tire achieves this by having tread regions with different thermal conductivities. These regions are made of rubber compositions with high and low thermal conductivity. The high thermal conductivity composition dissipates heat generated during high-speed running, preventing overheating and maintaining grip. The low thermal conductivity composition retains heat and provides durability.
19. Tire Temperature Control System with Integrated Liquid Circulation and Heat Exchange Module
GREAT WALL MOTOR COMPANY LTD, 2023
Automatically controlling tire temperature using a liquid circulation system with a heating/cooling module. The system circulates a heat exchange fluid between the tires and a module to heat or cool the tires. This avoids external fluid leaks affecting tire performance. The module state is controlled based on tire temperature and a target range. This enables automated tire temperature control without external liquid spraying.
20. Method for Tire Temperature Regulation and Pressure Stabilization Using Thermoelectric System and Hub Generator
HARBIN UNIV OF COMMERCE, HARBIN UNIVERSITY OF COMMERCE, 2023
Tire temperature control and pressure stabilization method for vehicles using thermoelectric refrigeration and hanging hub generator technology. The method involves using a thermoelectric cooling/heating system inside the tire to actively regulate tire temperature. A temperature sensor detects tire temperature during driving, which is fed to a controller that operates thermoelectric cold and hot fins. The vehicle's kinetic energy is also harnessed through a suspended hub generator to provide power for the fins and stabilize tire pressure. This allows rapid and efficient temperature control without relying on manual tire pressure checks.
Tire heat management technologies have advanced to meet the problem of effectively dispersing heat while maintaining other performance attributes like rolling resistance and tread longevity. Innovative rubber compositions and tire designs are constantly improving heat management, making tires safer and longer-lasting.
Get Full Report
Access our comprehensive collection of 43 documents related to this technology
Identify Key Areas of Innovation in 2025
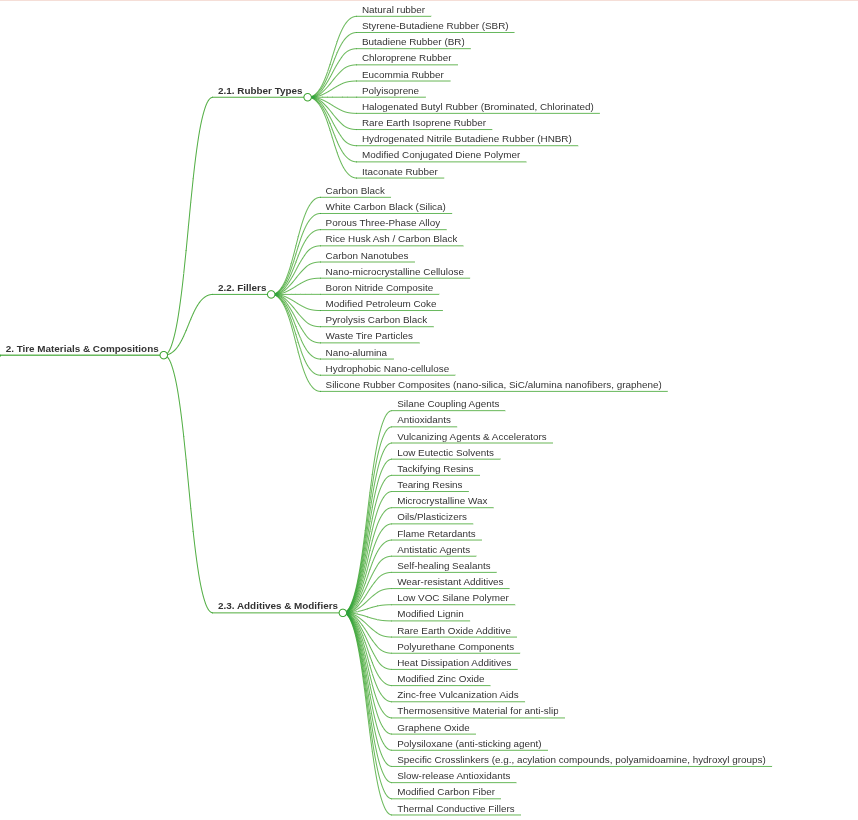