Pyrolysis Processes for End-of-Life Tire Recovery
Tire pyrolysis presents significant engineering challenges, with reaction temperatures ranging from 400-700°C needed to break down complex polymer networks into valuable compounds. Current industrial processes achieve only 40-45% oil yield efficiency, while generating substantial emissions and requiring energy-intensive preprocessing of whole tires into manageable fragments.
The fundamental challenge lies in achieving uniform heat distribution and controlled decomposition rates while managing the diverse thermal behaviors of tire constituents - from natural rubber to steel reinforcement.
This page brings together solutions from recent research—including microwave-assisted pyrolysis systems, laser-focused thermal decomposition, integrated heat recovery architectures, and continuous processing reactors for whole tires. These and other approaches focus on improving yield efficiency while reducing energy consumption and environmental impact.
1. Method for Enhancing BTX Content in Tire Pyrolysis Oil via Controlled Cracking Chamber Pressure and Particle Size Adjustment
Beijing University of Technology, BEIJING UNIVERSITY OF TECHNOLOGY, 2024
Method to increase BTX (benzene, toluene, xylene) content in tire pyrolysis oil by optimizing cracking conditions. The method involves prolonging the residence time of cycloolefins and aromatic hydrocarbons in the tire particles by increasing cracking chamber pressure. It also increases the residence time of short-chain olefins inside the particles by using larger tire particle sizes. This allows more BTX formation. The BTX is then discharged from the cracking reactor quickly by increasing air velocity to prevent over-conversion.
2. Multi-Stage Pyrolysis Furnace System for Carbon Black Production from Waste Tires
RE WORLD, 2024
Char carbon black manufacturing system that uses a multi-stage pyrolysis furnace to convert waste tires into high quality carbon black without using catalysts or post-processing. The system has a sealed pyrolysis furnace with multiple internal rotating transfer units to mix and heat the waste tire powder. This ensures uniform temperature contact, prevents leaks, and lengthens the thermal contact time. The furnace also has a heat source supply unit to maintain temperature. The system avoids problems of leaks and uniformity in conventional rotary furnaces. The pyrolyzed tire powder goes through metal removal, grinding, and sorting to produce carbon black.
3. Microwave-Assisted Pyrolysis and Plasma Process for Compound Extraction from Feedstocks
Microwave Solutions GmbH, MICROWAVE SOLUTIONS GMBH, 2024
A method for extracting valuable compounds from feedstocks like plastics, tires, and waste by using microwave plasma and pyrolysis. The method involves heating the feedstock in a pyrolysis chamber using microwaves to convert it into pyrolysis products. These products are then exposed to a microwave plasma to break down and extract specific target compounds like olefins. The plasma temperature is precisely controlled using microwave pulse shaping to recover the desired compounds.
4. Reactor with Zoned Heating and Controlled Steam or CO2 Injection for Two-Stage Tire Pyrolysis and Carbon Black Production
G3C Technologies Corporation, 2023
A reactor and method for recycling tires and other rubber materials into high quality carbon black, oil, and gas. The reactor involves converting tire-derived materials into these products in a two-stage process. In the first stage, called pyrolysis, the rubber is heated in an oxygen-free environment to extract oil. In the second stage, the pyrolysis char is heated in an oxygen-free environment with the strategic introduction of water steam or CO2 to create high surface area and structure carbon black. This involves a reactor with zones to heat and maintain the material at specific temperatures, along with injection of water steam or CO2 to enhance the conversion. The oxygen-free atmosphere prevents combustion and allows controlled chemical reactions.
5. Microwave-Assisted Pyrolysis Reactor with Variable Frequency and Power Control for Tire Material Decomposition
Microwave Solutions GmbH, MICROWAVE SOLUTIONS GMBH, 2023
Pyrolysis method and reactor for recovering compounds from tire materials using microwave radiation. The method involves feeding tire material into a chamber and exposing it to controlled microwave radiation at frequencies between 300 MHz and 2.5 GHz. The radiation power can be varied to continuously change the temperature within the chamber over a range that includes the decomposition temperature of the target compounds. This allows selective extraction of oils, hydrocarbons, monomers, plasticizers, etc. from tire materials by varying the microwave power and temperature. The reactor has multiple temperature zones for pyrolyzing different compounds simultaneously.
6. Method for Producing Fuel Oil and Carbon Black from Waste Tires via High-Temperature Cracking Under Negative Pressure
JINZHOU HAITONG IND & TRADE CO LTD, JINZHOU HAITONG INDUSTRY & TRADE CO LTD, 2023
A large-scale, efficient and environmentally friendly method for producing fuel oil and carbon black from waste tires. The process involves breaking the tires into small particles, then cracking the tire particles at high temperatures to produce fuel oil and carbon black. The cracking is done at negative pressure to prevent leaks and emissions. The fuel oil is condensed and dehydrated to remove water. The method provides high productivity and improved safety compared to existing tire recycling processes.
7. Rotary Kiln-Based Pyrolysis System for Producing Hard Carbon-Graphene from Waste Tires
Xi'an Jiaotong University, XIAN JIAOTONG UNIVERSITY, 2023
Continuous waste tire pyrolysis equipment to prepare high-value hard carbon-graphene material from waste tires. The system involves crushing the tires, pyrolyzing the rubber particles in a sealed rotary kiln, separating pyrolysis oil, and further processing the solid phase to make graphene. The pyrolysis gas is treated to recover energy. This closed-loop recycling of tires avoids pollution and waste, and produces valuable graphene.
8. Waste Tire Pyrolysis Device with Direct Molten Salt Heating and Closed-Loop Heat Exchange System
EVERBRIGHT GREEN ENVIRONMENTAL PROTECTION TECH SERVICE JIANGSU CO LTD, EVERBRIGHT GREEN ENVIRONMENTAL PROTECTION TECHNOLOGY SERVICE CO LTD, EVERBRIGHT GREENTECH MAN SHENZHEN CO LTD, 2023
Waste tire pyrolysis device for recycling pyrolysis gas that improves the yield of pyrolysis oil and gas compared to indirect heating methods. The device has a waste tire silo, molten salt pyrolysis furnace, pyrolysis gas condenser, molten salt heating furnace, and pyrolysis gas heat exchanger. The molten salt pyrolysis furnace and heating furnace are connected in a closed loop. Waste tires feed into the pyrolysis furnace, and the molten salt contacts and heats the tires directly. The pyrolysis gas exits the furnace and condenses in the condenser to separate the pyrolysis oil. The pyrolysis gas then passes through the heat exchanger to preheat the molten salt before entering the pyrolysis furnace again. This allows efficient recycl
9. Rotating Tubular Reactor System with Zoned Heating and Tube Cleaning for Continuous Pyrolysis of Organic Materials
KLEAN IND, KLEAN INDUSTRIES, 2022
System for continuous pyrolysis of organic materials like used tires to produce recovered carbon black. The system has a rotating tubular reactor, quenching unit, and burner unit. The reactor has multiple heating gas outlet valves along its length to control heat supply to different zones. This allows optimized pyrolysis conditions. The reactor also has a tube cleaning device to prevent clogging by transporting deposited solids from the pyrolysis gas outlet back into the reactor.
10. System for Pyrolyzed Steel Cord Residue Processing to Extract Carbon Fuel for High-Temperature Applications
STIBRANYI LADISLAV ING CSC, Štibrányi Ladislav Ing. CSc., 2022
A system for using pyrolyzed steel cord residue as a fuel in cement kilns and other high heat applications without burning whole tires. The system involves pyrolyzing the steel cord residue to separate out the pyrolyzed carbon fuel from the remaining steel cord pieces. This allows controlled addition of the carbon fuel to the kiln instead of whole tires which can cause temperature spikes. The pyrolysis process breaks down the rubber and steel in the residue to produce carbon fuel. The carbon fuel can be used as an alternative to traditional fossil fuels in cement kilns and other high heat applications to reduce reliance on primary resources and emissions.
11. Vertical Tower Reactor Pyrolysis Process with Steam Jet Pump for Waste Tire Conversion
Yang Song, SONG YANG, 2022
A process for recycling waste tires into pyrolysis oil and gas. The process involves pyrolyzing waste tires at 350-400°C using a vertical tower reactor with internal heating and stirring. The pyrolysis gas is combusted to generate high-temperature flue gas. A steam jet pump extracts exhaust gas from the combustion kiln and mixes it with steam to reduce the pressure. This mixed fluid is compressed and discharged back to the kiln. The steam jet pump allows efficient utilization of the high-temperature flue gas as a heat source for pyrolysis, condensing pyrolysis oil into liquid fuel, and recycling pyrolysis gas into fuel.
12. Pyrolysis Device with Dual-Screw Mechanism and Nitrogen Purging for Carbon Black Production from Waste Tire Rubber
UNIV ZHEJIANG, ZHEJIANG UNIVERSITY, ZHONGCE RUBBER GROUP CO LTD, 2021
A device and method for producing environmentally friendly carbon black from waste tire rubber using pyrolysis. The device has separate screws for pyrolysis and deep pyrolysis of the rubber particles at different temperatures. The pyrolysis screw has a horizontal and vertical spiral feed mechanism to compact the particles and reduce air intake. Nitrogen purging is used to remove toluene during deep pyrolysis. This allows producing carbon black with low toluene content (toluene transmittance >85%) and low ash, meeting environmental standards.
13. Pyrolysis Apparatus with Plasma Beam for Controlled Thermal Energy Transfer and Phase Separation
Paolo Peri, 2021
Pyolysis of raw material, in particular raw materials deriving from tires or bitumen and pyrolysis equipment operating according to a method that allows precise control of the transfer of thermal energy and consequently of the reaction temperature to be exerted. The method includes generating a plasma beam from the mass of raw material, focusing or distributing the beam of the laser radiation on a localized area of a pre-established surface area on the surface of the mass of raw material, being progressively moved along the entire surface of the mass of raw material by activating the pyrolytic reaction on all of said mass of raw material, and separating one from another the gaseous, liquid and solid phases of the reaction products and storing, for further treatment, said reaction products separated one from another.
14. Two-Stage Continuous Pyrolysis Device with Dual Pressure Reactors and Material Transport Screws
QINGDAO UNIVERSITY OF SCIENCE & TECHNOLOGY, UNIV QINGDAO SCIENCE & TECH, 2021
A two-stage continuous pyrolysis device for waste tires that maximizes both oil and carbon black yields compared to single-stage systems. The device has two reactors, a settling tank, and screws for transporting the material between stages. The first reactor operates at negative pressure to prevent secondary cracking of oil and gas. Carbon black is partially separated here and settles. The second reactor has positive pressure to prevent carbon black powder from entering the condensing system. This allows optimizing carbon quality. The two-stage process enables maximizing oil production in stage 1 and carbon quality in stage 2.
15. Tire Processing System with Steel Extraction, Magnetic Separation, Flue Gas Transport, and Molten Salt Pyrolysis
BEIJING YUNSHUI HAORUI ENV TECH CO LTD, BEIJING YUNSHUI HAORUI ENVIRONMENTAL TECHNOLOGY CO LTD, 2021
A system and method for processing tires that improves efficiency and reduces costs compared to existing methods. The system involves spinning the tires to extract steel wire, crushing the remaining tire, magnetically separating the iron, using flue gas to transport the rubber particles, cycloning the mixture, and pyrolyzing the rubber in a stirred reactor with molten salt. The spinning, magnetic separation, and flue gas transport steps allow recycling the steel and avoiding iron contamination in pyrolysis. The molten salt provides indirect heating and high heat capacity to improve pyrolysis efficiency. The stirring and cycloning steps prevent agglomeration and enable homogeneous pyrolysis.
16. Micro-negative Pressure Pyrolysis System with Dual-stage Tire Crushing and Microporous Plate Reactor
Fujian Aolin Magnesium Environmental Protection Technology Co., Ltd., FUJIAN AOLINMEI ENVIRONMENTAL PROTECTION TECHNOLOGY CO LTD, 2021
Micro-negative pressure pyrolysis method for recycling waste tires that improves the efficiency and mechanization of tire thermal cracking. The method involves crushing the tires in two stages, injecting the crushed material into a sealed reactor with a microporous plate, heating it under low pressure to 120°C, then increasing the heating rate and pressure to 450°C, and pyrolyzing it at reduced pressure while the solid phase remains on the microporous plate. This allows consistent tire crushing, pyrolysis, and material collection without steel wire stripping.
17. Two-Stage Pyrolysis and Gasification Device with Zoned Gasifier for Tire-Derived Oil and Charcoal Processing
CHANGSHA INDUSTRY TECH RESEARCH INSTITUTE ENVIRONMENTAL PROTECTION CO LTD, CHANGSHA INDUSTRY TECHNOLOGY RESEARCH INSTITUTE ENVIRONMENTAL PROTECTION CO LTD, 2021
Device for modifying pyrolysis oil and charcoal from waste tires to improve their quality and market value. The device consists of a two-stage process with a pyrolysis furnace followed by a gasifier. The pyrolysis converts the tires into pyrolysis gas and charcoal. The hot pyrolysis gas and charcoal then enter the gasifier where they are further processed. The gasifier has separate zones for gasification, modification, and ash accumulation. This allows further cracking of the gas to remove heavy tars, and separation of remaining organic matter from the charcoal. The modified gas is combusted, and the cleaner charcoal is recovered.
18. Two-Stage Integrated Device with Sealed Feeding, Pyrolysis, Gas-Solid Conveying, and Activation Sections for Waste Tire Processing
Dalian University of Technology, DALIAN UNIVERSITY OF TECHNOLOGY, 2021
Integrated device and method for efficiently pyrolyzing and activating waste tires in a two-stage process. The device has a sealed feeding section, a pyrolysis section, a gas-solid conveying channel, and an activation section. The pyrolysis section breaks down the tires into pyrolysis products like oil and gas. The gas-solid conveying channel transfers the pyrolysis gas to the activation section where it reacts with the remaining solid tire pieces to produce further products. The sealed feeding section prevents oxygen from entering during pyrolysis. This two-stage process improves efficiency by maximizing pyrolysis in the first stage and then further converting the remaining solids in the second stage.
19. Pyrolysis Chamber with Partitioned Sections and Integrated Gas Recovery for Tire Recycling
PUZAUSKAS EDVINAS, PUŽAUSKAS EDVINAS, 2021
Recycling end-of-life tires into petroleum products in an efficient, economical, and environmentally friendly way using pyrolysis. The recycling process involves heating the tires in a pyrolysis chamber to break down the rubber into usable petroleum products. The pyrolysis chamber has partitions to separate the feed section for tires, the input section for gas recovery, and the pyrolysis chamber itself. A gas shut-off fan and burners provide heat. A condenser collects liquid products and channels separate the pyrolysis gas. The control panel regulates the process. The design aims to improve efficiency and environmental impact compared to existing pyrolysis systems for recycling tires.
20. Pyrolysis System Utilizing Modified Carbon as Thermosetting Carrier for Waste Tire Processing
Dalian University of Technology, DALIAN UNIVERSITY OF TECHNOLOGY, 2021
Device and method for efficient and high-value utilization of waste tires through pyrolysis. The pyrolysis process involves heating waste tires without steel wires using modified pyrolysis carbon as a thermosetting carrier. This avoids the need for external heat sources like gas or oil. The modified carbon is produced by incompletely combusting the pyrolysis gas. The modified carbon is then used as the heating media to rapidly pyrolyze the tires. This provides a self-sustaining and efficient pyrolysis process that recovers maximum value from waste tires.
Get Full Report
Access our comprehensive collection of 93 documents related to this technology
Identify Key Areas of Innovation in 2025
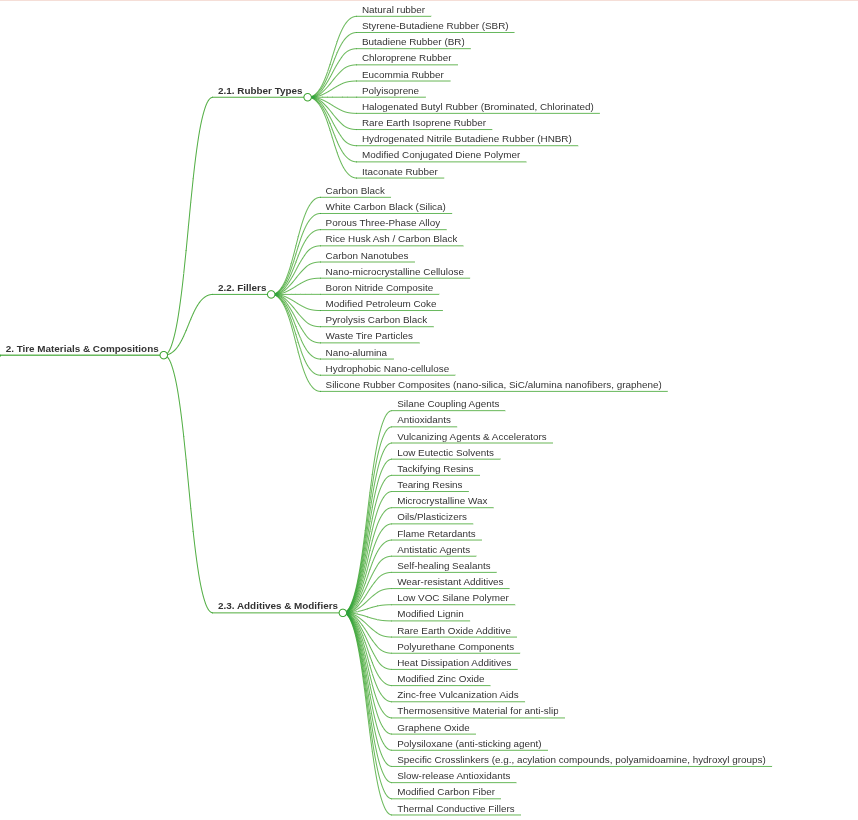