Bead Winding Machines in Tire Production
Modern tire manufacturing demands precise control of bead geometry and wire placement, with tolerances measured in fractions of a millimeter across the entire circumference. Current bead winding operations must maintain consistent wire tension of 200-300N while precisely positioning up to 5 layers of wire bundles, each containing 4-6 individual steel wires, to form bead cores with diameters ranging from 13 to 24 inches.
The fundamental challenge lies in balancing high-speed production requirements with the need for precise wire placement and consistent tension control throughout the winding process.
This page brings together solutions from recent research—including magnetic wire securing systems, radially adjustable winding drums, automated multi-stage assembly processes, and spiral groove formations for wire guidance. These and other approaches focus on improving production efficiency while maintaining the critical dimensional accuracy needed for tire bead integrity.
1. Apparatus and Method for Forming Bead Rings with Adjustable Cross-Sections Using Drum Guide and Holding Plate
YOKOHAMA RUBBER CO LTD, YOKOHAMA RUBBER CO LTD:THE, 2022
A method and apparatus for manufacturing bead rings for tires that allows easy creation of bead rings with arbitrary cross-sections. The method involves winding bead wires around a drum guide to form annular elements, then sliding them onto a holding plate to join side surfaces and make the bead ring. This allows sequential formation of custom-shaped bead rings by adjusting the number of wire winds per element.
2. Wire Bundle Manufacturing Apparatus with Magnetically Secured Groove for Tire Bead Core Formation
SUMITOMO RUBBER IND, SUMITOMO RUBBER IND LTD, 2021
A wire bundle manufacturing apparatus for making tire bead cores by winding wire around a drum. The apparatus has a drum with a groove and a magnet to fix the wire base. The magnet attracts the wire end inside the groove to prevent slippage. This allows winding the wire tightly around the drum to form the bead core bundle. The magnet distance from the groove is 6mm or less. The wire can be a single wire with a coated rubber covering.
3. Manufacturing Apparatus with Radially Adjustable Drum for Reinforced Tire Beads
PIRELLI TYRE S.P.A., 2017
Process and apparatus for manufacturing tires with reinforced beads using a radially expandable/contractable drum. The process involves building the tire on a drum, looping a reinforcement around the bead, then loading the bead onto the drum. The drum can adjust size to fit different bead radii. This allows using the same drum and looping apparatus for tires with varying bead diameters. The looping step involves depositing a band on the drum, then loading the bead on the drum to turn the loop up. It also includes features like adjustable drum supports, conical rollers, and gripping arms.
4. Apparatus for Bead Core Manufacturing with Integrated Rotating Body and Wire Handling Mechanism
FUJI SEIKO CO LTD, FUJI SHOJI CO LTD, 2016
Simplified apparatus for manufacturing bead cores used in tires by winding wire around a rotating body. The apparatus has a divided rotating body, expansion/contraction mechanism, and clamping mechanism. The divided body elements expand/contract while gripping/releasing the wire, eliminating separate steps for diameter change and wire attachment/detachment. This simplifies the bead core manufacturing process compared to prior art devices with separate mechanisms for expansion, contraction, and wire handling.
5. Rotatable Member-Based Tire Carcass Ply Manufacturing Apparatus with Axially Slidable Bead Support Holders
GOODYEAR TIRE & RUBBER CO, 2016
Apparatus for manufacturing tire carcass plies that allows efficient and precise production of tire carcasses. The apparatus has a rotatable member with a wind ply tape reel mechanism positioned adjacent to bead support holders on either side. The rotatable member can be positioned inside each bead to wind and unwind the ply tape. The bead support holders are axially aligned and slidable on an upper/lower frame portion. This allows simultaneous ply winding in both beads as the rotatable member moves around the tire circumference. The sliding frame movement compensates for tire width variations.
6. Automatic Multi-Stage Bead Assembly Device with Integrated Forming, Cutting, Molding, and Joining Mechanisms for Large Tires
SUMITOMO RUBBER IND, SUMITOMO RUBBER IND LTD, 2015
Automatic bead assembly device for large tires that improves productivity by automating the bead assembly process. The device has multiple stages for forming, cutting, molding, and joining the bead components. It uses specialized machines to wind, cut, and crimp the bead rubber onto the core. The beads are then transferred between stages until the complete bead is loaded onto the tire. This automated process allows consistent and efficient bead assembly for large tire production.
7. Bead Core Molding Apparatus with Spiral Convex Slopes in Bead Former Groove
SUMITOMO RUBBER IND, SUMITOMO RUBBER IND LTD, 2014
A bead core molding apparatus for preventing bead core unwinding and jumping during winding. The apparatus has convex slopes spirally formed at equal intervals on the bottom of the bead former groove. The slopes guide the metal wire during winding to prevent it from unwinding or jumping at the start end. The slope height is 1/6 to 1/3 wire diameter and the slope width is the wire diameter. This allows winding the bead core at high speed without unwinding issues.
8. Tire Building Apparatus with Continuous Ribbon-Shaped Bead Filler Lamination Mechanism
BRIDGESTONE CORP, 2012
Tire building apparatus that reduces production time and material consumption when forming the bead of a tire. The apparatus continuously winds and laminates a ribbon-shaped bead filler rubber on the inner and outer sides of the bead core without stopping. This is achieved by having a swing plate to position the bead core on a ring while laminating bead filler on the backside. Then the bead core is installed and more filler laminated on the outer side. This allows continuous winding without interruption or extra material waste compared to separate inner and outer winding steps.
9. Method for Forming Tire Beads Using Butterfly-Shaped Wire Winding with Circumferential Clips
HANKOOK TIRE CO LTD, 2012
Method to improve durability and uniformity of tire beads to prevent overlap issues. The method involves winding the bead wire in a butterfly shape and securing clips around the internal circumference of the completed bead. This prevents wire overlap and improves bead durability. The clips are coupled in the circumferential direction of the finished bead after winding. Wrapping a cover over the bead with the clips further enhances durability. The wire feed rate and winding speed are adjusted based on wire storage to optimize bead shape.
10. Apparatus with Spiral Groove Die for Pre-Winding Bead Wire in Green Tire Manufacturing
2012
Method and apparatus for manufacturing green tires that reduces bead molding time and improves productivity by pre-winding bead wire onto a specialized die before attaching it to the torus drum. The bead wire former die has a spiral groove to wind the bead wire in advance. This allows the green tire to be formed faster since the bead wire is already in place instead of needing to be wound during molding. The pre-wound bead wire is then pressed onto the torus drum along with the inner liner to create the green tire. The pre-winding die can be located on either side of the torus drum and has a shape matching the tire cross-section.
11. Apparatus and Method for Pre-Winding Bead Wire on Die Inside Torus Drum for Green Tire Formation
HANKOOK TIRE CO LTD, 2011
Method and apparatus for manufacturing green tires that reduces molding time and improves productivity by pre-winding bead wire onto a die inside the torus drum before forming the green tire. This avoids wire disturbance during vulcanization by having the wire already arranged before pressing the tire into the drum. A bead wire former die with a spiral groove is used inside the drum to pre-wind the bead wire before attaching it to the green tire.
12. Apparatus and Process for In-Situ Formation of Bead Reinforcement on Toroidal Tire Carcass Support
PIRELLI TYRE S.p.A., 2010
Process and apparatus for manufacturing tires by directly forming the bead reinforcement on the tire carcass as it is being built on a toroidal support. The process involves feeding a continuous reinforcing band around the toroidal support, deforming it into a loop, and joining pieces to create the bead reinforcement. The apparatus has devices for feeding and depositing the reinforcing element on the support.
13. Apparatus and Method for Tire Bead Formation Using Elastomeric Apex Filler Winding and Transfer Mechanism
VMI EPE HOLLAND BV, 2010
Method and apparatus for forming tire beads with improved efficiency and versatility. The method involves winding an elastomeric apex filler around a former, gripping the ends, and then throwing it onto the bead wire ring to form the bead assembly. The apparatus includes grippers to capture and move the filler ends, a cylindrical former, and a drum with the bead wire ring. The grippers wind the filler onto the former, then transfer it to the drum where it's thrown onto the bead ring. This allows simultaneous winding and bead assembly formation.
14. Bead Structure Building Apparatus with Continuous Bead Winding Mechanism for Green Tire Production
HANKOOK TIRE CO LTD, 2009
Bead structure building apparatus for green tire production that eliminates the need for turning the carcass after bead installation. The apparatus has a bead wire supply, two lateral bead winding mechanisms, a moving mechanism to move the wire supply between the winders, and a moving mechanism to move the winders between positions. This allows winding the bead wire onto the drum in a continuous motion without turning the carcass. The bead structure is then attached at the end of the wound wire. This provides a more uniform and consistent green tire compared to turning the carcass after bead installation.
15. Apparatus and Process for In-Situ Formation of Tire Reinforcing Beads on Carcass Using Curved Path Deposition
PIRELLI TYRE SPA, 2009
Process and apparatus for manufacturing tire reinforcing beads directly onto the tire carcass as it is built. The process involves cutting, deforming, and depositing reinforcing bands onto the toroidal tire support in a side-by-side fashion along a curved path. The apparatus has a feeding device, cutter, gripping device, and deformation mechanism to execute this process. The gripping device deforms the cut bands to match the tire's curvature at each deposition location. This allows the bead reinforcement to be formed and attached in-situ instead of as separate components.
16. Automated Machine with Sequential Forming Stations for Tire Bead Ply Wrapping
BECCAVIN CHRISTIAN, MICHELIN RECH TECH, MICHELIN RECHERCHE ET TECHNIQUE SA, 2008
Automated machine and method for making tire beads with improved efficiency and consistency compared to traditional hand wrapping methods. The machine has multiple forming stations with rollers that sequentially wrap a bead ply around a bead profile. The rollers have profiles that press, turn, and pull the bead ply as it's fed through the stations. This allows automated, consistent wrapping of the bead ply around the bead profile. The wrapped bead can then be stored or fed directly to the tire assembly drum. The automated wrapping avoids the complexity and time-consuming hand wrapping on the assembly drum.
17. Method for Forming Triangular Bead Apex Rubber Using Tapered Spiral Winding of Ribbon-Shaped Rubber Strip
SUMITOMO RUBBER INDUSTRIES LTD, 2007
Efficiently forming a bead apex rubber with a triangular cross section on the radial outer peripheral surface of a bead core in tires. The method involves winding a ribbon-shaped rubber strip in a tapered spiral around the bead core to create the triangular shape. The strip width is 5-20 mm and thickness 0.5-2.0 mm. The strip is wound radially outward from the base piece on the bead core. This allows forming the triangular bead apex rubber efficiently compared to molding a triangular cross section. The strip winding starts at the outer peripheral surface of the bead core supported on a rotating body.
18. Method for Direct Application of Rubber and Cable Components on Rotating Toroidal Mandrel for Tire Bead Construction
Christopher David Dyrlund, Gary Robert Burg, Brian Richard Koch, 2005
A method for building tire beads on a rotating toroidal mandrel that eliminates the need for pre-made strips and improves bead quality. Instead of sequentially layering pre-made strips onto the mandrel, the method involves simultaneously applying the rubber and cable components to the rotating mandrel. An ejector nozzle applies the rubber in a semi-solid state while a cable is fed through the nozzle and applied along with the rubber. This builds the bead configuration directly onto the mandrel without layering pre-made strips. This avoids inventory, storage, and lamination issues of the prior art.
19. Pneumatic Tire Building Drum with Axially and Radially Movable Concentric Segments and Turn-up Bladders
John Wiens, 2005
Building pneumatic tires on a drum that allows for a unistage process to improve consistency and precision in the tire bead architecture. The drum has concentric segments that can move axially and radially. This allows the bead gorges to move with the segments. Turn-up bladders expand to wrap the uncured rubber section without rotating it. This maintains the orientation as the bladders expand and contract. The segments, gorges, and bladders move together to capture bead complexes and form the beads. The consistent bead shape is achieved by keeping the uncured rubber section aligned during expansion and contraction.
20. Single-Wire Bead Manufacturing System with Integrated Winding and Apex Fitting Devices
Sumitomo Rubber Industries, Ltd., 2002
Automated single-wire bead manufacturing system with integrated winding and apex fitting steps. The system has a winding device, a thread winding device, and an apex fitting device linked by a transfer device. A single production line moves the wire between the devices to create the bead without intermediary storage. This eliminates the need for bead storage and handling steps, reducing costs and improving efficiency. The synchronized winding and fitting steps also prevent defects from long storage.
Get Full Report
Access our comprehensive collection of 28 documents related to this technology
Identify Key Areas of Innovation in 2025
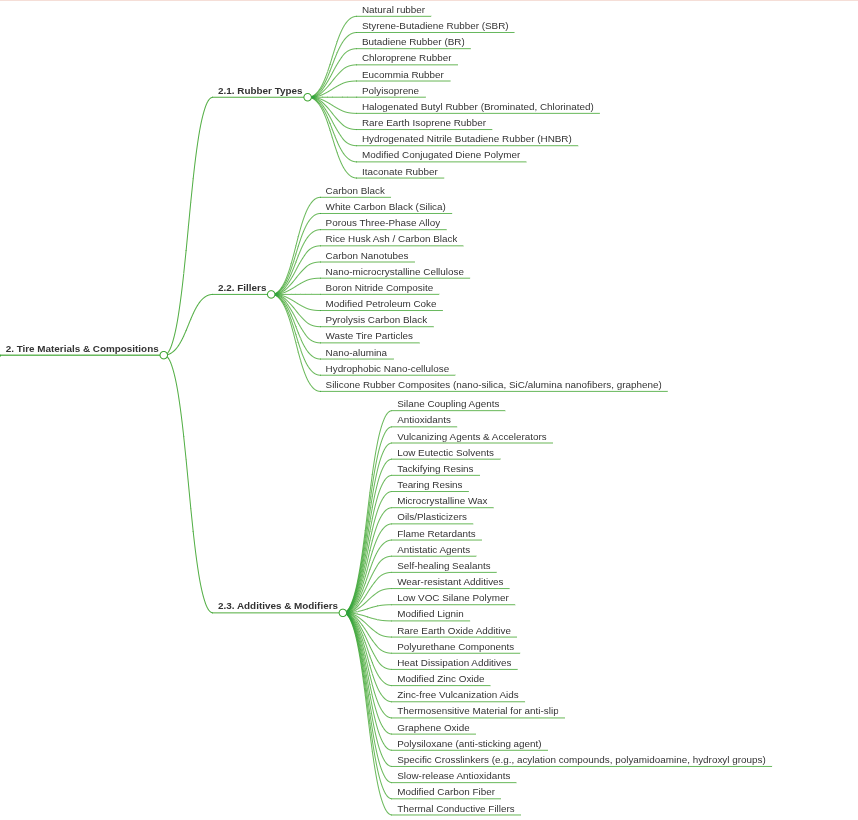