Reduce Tire Manufacturing Cost
Modern tire manufacturing involves complex process chains where raw material costs account for 60% of total production expenses, while energy consumption during vulcanization and curing cycles adds another 15-20%. Current production lines typically require 45-60 minutes per tire, with significant variations in quality and consistency across batches.
The fundamental challenge lies in reducing material and energy costs while maintaining the precise mechanical properties that determine tire performance and safety.
This page brings together solutions from recent research—including thermoplastic elastomer alternatives to conventional rubber, modular mold designs that reduce maintenance costs, single-step manufacturing processes using horizontal centrifugal casting, and customizable production systems that optimize inventory management. These and other approaches focus on practical ways to lower production costs while maintaining or improving tire quality and performance specifications.
TABLE OF CONTENTS
1. Recycled and Bio-Based Rubber Feedstocks That Compress Raw Material Cost
Raw polymers, fillers and process oils typically account for forty to fifty percent of a tire’s cost of goods. The most direct way to cut that spend is to widen the feedstock window so that low-value reclaim, micronized scrap or non-petroleum fillers can stand in for prime elastomer without destabilising cure kinetics or end-use performance.
1.1 Factory-floor reclaim with real-time pedigree control
A factory already generates off-spec strips, splices and milling wafers that can be reincorporated if their chemistry is known and repeatable. The containerized digital inventory of reclaim solves the traceability gap by loading every scrap fragment into RFID-tagged totes, logging rheometer and FTIR fingerprints, and storing the totes in a barcode-gated carousel. When the mixer PLC calls for a batch containing five percent reclaim, the warehouse pulls only those totes whose Mooney and bound-sulfur values fall inside the recipe window. The closed loop lifts the upper limit for reclaim from the legacy two percent to routinely eight percent, reducing virgin polymer consumption by close to seventy kilograms per thousand passenger tires while avoiding the re-milling labour that used to erode savings.
1.2 Surface-activated end-of-life tire powder
End-of-life tires dwarf factory scrap by a factor of twenty, yet conventional micronized rubber powder (MRP) has a smooth, chemically exhausted surface that weakly couples to fresh polymer. The in-situ silica-silane MRP activation introduces precipitated silica and optional mercapto-silane directly into the cryogenic mill. Silica acts as both grinding aid and functional nucleant. Particle size d50 drops from 350 µm to below 120 µm, fines yield climbs fivefold and the freshly generated surfaces are already dusted with silanol groups. During subsequent mixing those groups react with curing sulfur so that two to six weight percent of functionalised MRP can be exchanged for virgin S-SBR, lowering compound cost by roughly fifty Euro per metric ton while cutting tan δ at sixty degrees Celsius by up to six percent.
1.3 Oleophilic lignin masterbatches from pulp-mill sidestreams
For producers targeting a largely fossil-free bill of materials, lignin from Kraft or soda pulping plants is an abundant aromatic fill-reinforcer. Its polarity mismatch, however, once restricted loading levels to less than five phr. The dual-esterified lignin-rubber masterbatch first caps the abundant phenolic hydroxyl groups with acetic anhydride to dampen hydrogen bonding, then grafts oleic-acid side chains to add hydrocarbon character. A twin-screw hot-granulation step locks forty phr of this modified lignin inside natural rubber crumbs that feed directly into a Banbury. Tensile strength reaches 18 MPa at only 35 phr carbon black, replacing another 15 phr with lignin and dropping the cradle-to-gate CO₂ footprint by almost 1.4 kg per tire. Because both esterification reagents derive from biomass, the masterbatch advances the European Union’s ninety-three percent renewable-content target proposed for 2030 truck tires.
Combined, these three supply-side levers can trim raw-polymer purchases by eight to fifteen percent and carbon black by up to twenty percent. They also lay the foundation for the next stage: engineering each kilogram of compound to deliver more mechanical work so that further loading increases are unnecessary.
2. Functionalised Polymers and High-Efficiency Fillers That Shrink Curative Demand
With reclaimed and bio-based feedstocks secured, the next opportunity is to reduce the mass of curatives and high-cost reinforcing agents needed to achieve a given modulus or abrasion index. Two complementary strategies dominate: embedding the crosslink chemistry inside the polymer chain and substituting bulky carbon black with nanoscale, renewable fibres.
2.1 Intrinsically crosslinkable copolymers
Sulfur and ZnO together can total four phr in a conventional passenger tread, yet only about sixty percent participates in crosslink formation. A statistical terpolymer containing vinylbenzocyclobutane self-crosslinking copolymer units eliminates that waste. At mold hold temperatures of 170 to 240 °C the benzocyclobutane ring opens and reacts with adjacent double bonds along the same chain or with neighbouring chains, creating a uniform network without external curatives. Cure time mirrors sulfur systems, but the absence of metal oxides simplifies REACH compliance and avoids the green-state final-mix pass that once consumed twenty kilowatt-hours per batch. Winter-tire prototypes show a ten percent higher ice traction coefficient because the metal-free glassy modulus is lower at minus ten °C.
2.2 Protein-based elastomers activated by benign initiators
Where petro-elastomer replacement is a goal, yeast-expressed resilin offers an amino-acid-level control over hardness and damping. The persulfate-induced resilin elastomer crosslinks in bulk water at 60 °C when exposed to ammonium persulfate. Glycerol post-exchange raises glass-transition temperature, whereas DMSO yields a softer, vibration-isolating network. Side-wall membranes cured this way reach one million flex cycles at twenty-five percent strain without crack initiation. They also sidestep photoinitiator residues that complicate recycling.
2.3 Nanocellulose and polysaccharide masterbatches that displace carbon black
Carbon black remains a key strength contributor, yet its large surface area drives both viscosity and mixing torque. When 1.5 phr of phosphoric acid-modified cellulose nanofiber reinforcement is co-mixed with standard grade N330, tensile strength climbs eight percent while compound Mooney viscosity drops 5 MU. Processors can therefore achieve the same target modulus with four to six fewer phr of carbon black. For applications needing even higher bio-derived loading, a latex-route polysaccharide–elastomer masterbatch coagulates up to eighty weight percent glucan chains inside the rubber phase. The pre-dried crumb granulates like standard bale rubber, keeps mixer throat temperature ten degrees lower and lets formulators substitute fifteen phr of carbon black without losing DIN abrasion performance.
Collectively, the polymer-embedded crosslinkers and high-surface-area renewable fillers cut sulfur, ZnO and carbon black by twenty to thirty percent. They also simplify downstream compounding because fewer dosage streams need to be metered, preparing the ground for lighter, faster-curing components.
3. Thermoplastic Elastomer Components and Microlayer Gas-Barrier Films for Mass and Energy Reduction
Having raised the performance per kilogram of compound, engineers can now delete entire cure passes by switching from thermoset to thermoplastic elastomers (TPEs) wherever dynamic strain is moderate. Each skipped press cycle eliminates roughly fifteen kilowatt-hours of steam and four kilowatt-hours of electricity per truck tire.
3.1 TPE overmolding after carcass cure
The selective TPE overmolding of tread and sidewall vulcanises only the radial carcass before injecting a melt-processable styrene block copolymer tread around it. Because the tread never enters a conventional press, mold occupancy per curing bladder falls from twelve minutes to six, effectively doubling cavity throughput. Rolling-resistance modelling shows a four percent gain due to lower hysteresis in the TPE cap, while end-of-life carbon separation is simplified because infrared-sorting robots can distinguish the thermoplastic shell from the sulfur-set core.
3.2 Ultra-thin thermoplastic inner tubes
Where pneumatic retention performance used to mandate four-millimetre butyl tubes, a ultra-thin polymer film inner tube replaces butyl with a 100 to 400 µm blow-extruded film comprising PA6 and a saturated SEBS elastomer alloy. Post-cutting heat sealing forms a seamless torus around a grommet RF-welded valve. Air retention over 90 days at forty degrees Celsius equals traditional butyl, while weight drops up to 2.4 kg on a 22.5-inch commercial wheel. The sealed film welds cleanly without solvents so existing extrusion lines merely add a hot-bar station instead of an entire solvent-ventilation suite.
3.3 Flex-resistant microlayer barrier liners
For tubeless passenger tires and flexible bladders, multilayer EVOH films crack after two hundred thousand flex cycles at eight percent strain. The microlayered flex-resistant gas-barrier film stacks forty to eighty EVOH layers each no thicker than 0.75 µm between SEBS interlayers. Finite-element modelling shows that strains never reach the eight percent critical threshold inside any barrier ply, extending crack-free life past two million cycles. Oxygen permeability remains below 4 cc m-2 day-1 yet EVOH mass drops by forty percent. Because the film co-extrudes at below 240 °C, processors can incorporate up to thirty percent post-industrial recycle without hydrolytic degradation.
With these three architectures a typical 315/80R22.5 achieves a weight reduction of 3.8 kg while saving one third of press energy and freeing expensive curing bladder capacity for premium SKUs.
4. Single-Step Casting, Parallel Forming and Gear-Pump Co-Extrusion That Collapse Press Time
The benefits of lighter thermoplastic components compound when forming and extrusion lines can deliver multiple layers in one pass, eliminating queue time and intermediate storage.
4.1 Centrifugal spin-molding of non-pneumatic tires
Non-pneumatic tires for skid-steer and telehandler markets used to require separate rim casting, body curing and tread bonding. The one-step spin-molding of an NPT with an in-situ metallic rim places the fully machined rim inside a horizontal mould that spins at up to 350 rpm. Elastomer injected through a radial gate sweeps outwards under centrifugal force and fills spoke and tread cavities created by movable inserts. A six-minute cure followed by water spray cooling delivers a rim-bonded wheel that exits the cell ready for dynamic balance testing. Cycle time shrinks from four hours to forty-five minutes and two mating presses are removed from the capex line-up.
4.2 Gear-pump regulated multi-compound extrusion
For pneumatic tire treads the limiting step is often the profile extruder, where three or more screws feed a common head. Traditional screw-feed rate changes propagate pressure disturbances that distort the cap-base interface. The gear-pump controlled co-extrusion inserts a precision gear pump after each screw so each compound stream is metered independently of screw slip. Layer thickness control tightens from ±0.15 mm to ±0.05 mm even during ten percent throughput ramps, enabling finer cap gauges that save two phr of high-silica compound across the tread crown. Changeover time between high-performance and touring formulations drops sixteen minutes because set-point recalculation is no longer iterative.
These forming upgrades release 5 percent additional press hours per day and raise extrusion line OEE above ninety-five percent, smoothing the flow toward finishing while supporting the lighter, multi-material constructions introduced earlier.
5. Segmental and Additively Manufactured Molds That Re-Set Tooling Economics
Fast curing loses impact if tread molds take weeks to arrive. By replacing machined aluminium with high-temperature polymers and hybrid castings, tooling lead time falls in line with the new compound development cadence.
5.1 FFF-printed tread inserts for overnight prototypes
The FFF-printed high-temperature thermoplastic tread insert converts a CAD file into a polyetherimide or PEEK insert within ten hours on a 0.6 mm nozzle printer. Variable infill densities let ribs be forty percent solid for knife-edge stability while the backing plate is only twenty percent to save material. After six hours at 110 °C in a vacuum oven to desorb moisture the insert tolerates a 120 °C, 20-minute press cure without creep. A tread-development team can therefore iterate four pattern revisions in a single week, sidestepping the 2 000 Euro wire-EDM invoice that previously limited trial frequency.
5.2 Silicone-to-epoxy hybrid casting for reusable small-batch segments
Fine groove fidelity sometimes exceeds FFF resolution. The hybrid elastomer-to-thermoset casting workflow starts with a low-cost PLA or ABS master, over-molds it in room-temperature vulcanising silicone and cures a fibre-reinforced epoxy shell inside the silicone negative at 80 °C. The shell reaches thirty-five MPa tensile strength and Shore D fifty hardness, surviving more than one hundred vulcanisation cycles with less than 0.02 mm cumulative wear. From upload of the STL file to first article delivery only twenty-four hours elapse and no CNC queue is required. The approach is ideal for sectional endurance testing or military runs under two hundred units where aluminium amortisation fails.
These two insert strategies match the throughput gains achieved in Sections 3 and 4, ensuring that tooling will never be the rate-limiting step when novel tread patterns or material recipes emerge.
6. Integrated MES, Scheduling and Autonomous Logistics That Convert Islands of Efficiency Into Plant-Wide Savings
A high-velocity cell can still starve if upstream mixers or downstream mold-handling carts lag behind. Digital optimisation across the plant’s entire constraint set aligns asset utilisation so that material and energy savings translate into realised margin.
6.1 Global recipe optimisation via swarm intelligence
Conventional line supervisors tune viscosity or scorch time in isolation. The whole-process sparrow search optimization feeds five years of MES and QA data into neural surrogates that predict Mooney, tensile and cure curve outputs. A swarm-based meta-heuristic then searches millions of Banbury-calender-building-press parameter vectors while penalty functions enforce each unit’s torque or temperature limits. In a 32-SKU passenger plant the system converged on one globally feasible recipe set that cut scrap from 3.7 to 1.9 percent and shaved 4 kWh of electricity per green tire.
6.2 Automated retrieval of proven extrusion set-points
Line operators still burn minutes re-keying screw speeds each shift. The data-driven extrusion parameter retrieval loop polls the historian for the last ten batches of the requested SKU, ranks them by a composite process-performance index and writes the median settings directly to the extrusion PLC. If the SKU is new, a fall-back recipe is applied, then auto-tuned over the first fifty metres of profile. The closed loop halves meter-weight deviations and removes ten manual inputs per changeover.
6.3 Demand-driven cart allocation for semi-finished stock
The demand-driven cart allocation and conveyance integration merges WIP inventory with building-machine pull signals. Every minute the algorithm forecasts rubber strip consumption, selects the smallest cart combination that meets the need and reserves conveyors accordingly. In a plant running sixty presses the system reduced idle curing minutes caused by absent strip from 2.4 percent to 0.3 percent and freed nine floor operators for higher-value tasks.
Together these MES and logistics overlays close the gap between cell-level velocity and plant-level takt time, ensuring that the material and energy savings elaborated earlier register directly on the income statement.
7. Modular Casing-Tread Assembly for Point-of-Sale Customisation and Retread Uptime
Even the most efficient central plant cannot stop dealers from over-stocking slow movers or scrapping age-expired inventory. Modular curing at the point of sale shifts value creation closer to the customer while drawing on many of the material innovations already discussed.
7.1 On-demand bonding of uncured tread belts to prepared casings
The point-of-sale tire assembly keeps four uncured carcasses and four tread belts in inventory, yielding sixteen finished SKUs. A user interface captures driver priorities and suggests compatible pairs. A local bonding press cures the stack in two hours because the casing’s sacrificial subtread is buffed away moments before bonding, ensuring uniform heat flow. Since belts are light, air-freight replenishment is viable, allowing dealers to cut inventory cube by seventy-five percent. Real-time customisation also leverages the TPE overmolding from Section 3 because thin thermoplastic belts heat up in half the time of conventional sulfur composites.
7.2 Retread strip prepared for zero-buff turnaround
Fleet retreaders grapple with energy-intensive buffing to remove oxidised surfaces. The double tread precure strip moulds two tread patterns back-to-back. At application the strip is guillotined along its mid-plane, exposing pristine bonding faces that require no buffing or cement. Cure presses process twice the tread metres per cycle while eliminating the VOC ventilation step. The same local presses installed for modular new-tire builds can process retread strips, creating a unified service bay for new builds and retreads and raising retreader throughput by thirty percent.
By transferring final curing closer to the end user, manufacturers offload capital, reduce distribution cost and shorten lead-times, which is particularly valuable in the volatile OTR and specialty segments.
8. Optimised Tread and Wheel Geometries That Push Wear and Heat Limits
Manufacturing efficiencies lose their economic punch if the product wears out prematurely. Geometry optimization informed by finite-element and thermofluid simulation catches that value leakage before the tire leaves the press.
8.1 Shoulder rib siping that balances traction and durability
Drive-axle scalloping begins at the shoulder edge. The partial-depth transverse sipes in shoulder ribs halt that failure mode. Sipes penetrate only fifty percent of the shoulder-rib width, maintaining bulk stiffness while presenting fresh micro-edges. Rubber strain energy density falls fifteen percent compared with full cuts, and a fleet trial on 4x2 tractor units saw shoulder wear rate converge with center rib wear for the first four millimetres of tread life.
8.2 Concave multi-sided blocks for mixed-terrain trucks
Construction fleets need mud traction on site and long mileage back on pavement. The concave multi-sided geometry recesses the centre of each lug so that only ten to sixty percent of its height carries load on soft ground, cutting self-cleaning time in half. On asphalt, the tapered sidewalls distribute contact stress, avoiding the stone drilling that often destroys standard block patterns. Field data show a seventeen percent life extension on aggregate-rich site-to-road cycles.
8.3 Dual-compound treads that dissipate heat
At motorway speeds hysteretic heating triggers blister failure. The dual-compound heat-dissipating tread pairs a high-k, silica-rich sub-layer with a lower-k cap. Lateral micro-grooves pump air into the higher-k layer, which then spreads heat toward the steel belt. Thermocouple testing shows belt edge temperature reductions of nine degrees Celsius at 140 km h-1, raising the speed rating by one letter category while preserving wet grip.
These geometric and material synergies extend wear life by ten to twenty percent, lowering cost per kilometre and enhancing the business case for the lighter, modular tires introduced earlier.
9. Mechanical and Battery-Free Alignment Systems That Maintain Those Gains in the Field
Finally, service-life savings require that the wheel remains correctly inflated and aligned without adding maintenance overhead.
9.1 Passive RF-powered strain and pressure sensor
Battery swaps add labour and hazardous waste. The passive resonant tire-mounted sensor harvests the interrogation RF field, then back-scatters a resonance shift proportional to casing strain or internal pressure. At 90 kph the tag communicates over 1.2 m, allowing a roadside reader coil to scan whole axles. Weight is four grams versus over twenty for a battery TPMS, reducing imbalance mass and eliminating battery end-of-life disposal.
9.2 Taxi-angle aware steering controller for aircraft
Aviation tires fail mainly from lateral scrub during tight taxi manoeuvres. The steering-angle-aware taxi controller calculates a dynamic damage threshold based on weight and fuel burn, then limits hydraulic commands as that threshold is approached. Taxi-test data on an A321 demonstrate a forty-nine percent reduction in shoulder temperature spikes, doubling tire life and halving the rotable pool size airlines must carry.
9.3 Pre-cambered telescopic rails for tow dollies
Trailer and dolly wheels see edge loading when the cross-rail sags. The arched telescoping cross-rail with built-in positive camber starts with plus three degrees camber that relaxes to zero under design load. Finite-element analysis shows a fifty-one percent lower bending stress at full gross weight compared with gusseted straight rails. Straight-line tread wear equalises between inner and outer ribs, adding twenty percent mileage before a retread is required.
By integrating cost-free energy harvesting, software limiters and geometry-based alignment, these field upgrades ensure the manufacturing savings captured in Sections 1 to 8 translate into lower total cost of ownership.
Get Full Report
Access our comprehensive collection of 38 documents related to this technology
Identify Key Areas of Innovation in 2025
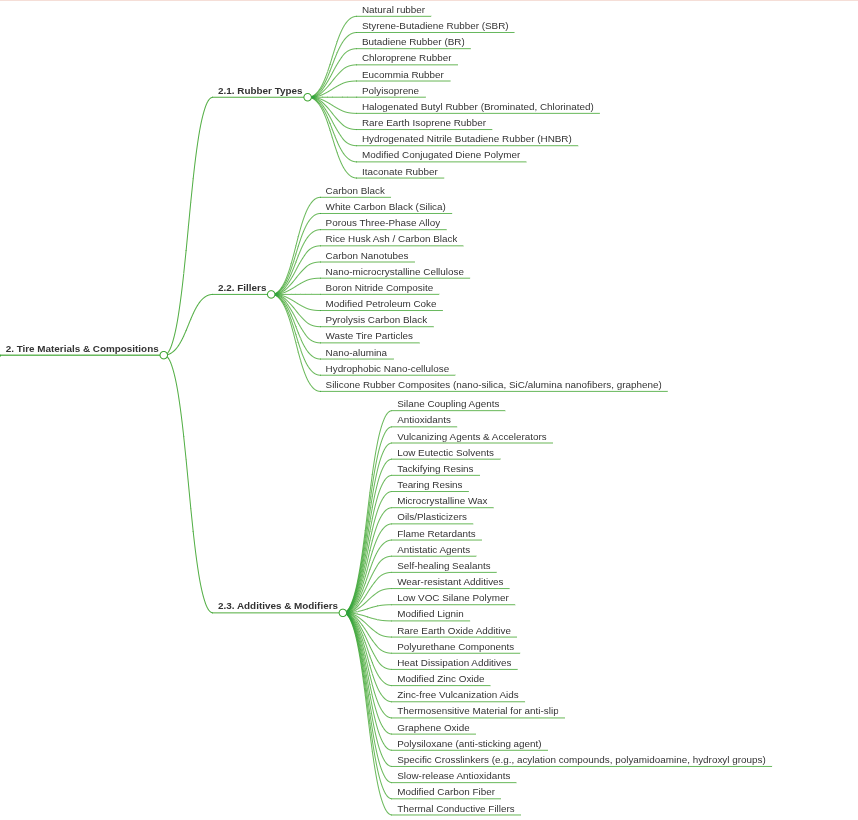