Devulcanization for Tire Recycling
End-of-life tires present a significant recycling challenge, with over 1 billion waste tires generated annually worldwide. The vulcanization process that makes tire rubber durable creates strong sulfur crosslinks between polymer chains, making the material resistant to conventional recycling methods. Breaking these bonds while preserving the valuable polymer structures requires precise control of thermal, mechanical, and chemical conditions.
The fundamental challenge lies in selectively breaking sulfur crosslinks without degrading the main polymer chains that give rubber its essential properties.
This page brings together solutions from recent research—including mechanochemical catalysis, supercritical fluid treatments, controlled microwave processing, and turbulent gas-phase devulcanization. These and other approaches focus on producing devulcanized rubber that maintains sufficient material properties for reuse in new tires and other high-performance applications.
1. Innovative approaches to thermochemical devulcanization of carbon black-filled SBR
anuwat worlee, sitisaiyidah saiwari, wilma k dierkes - SAGE Publishing, 2025
This investigation fully studied optimizing the thermochemical desulfurization process for carbon black-filled styrene butadiene rubber (SBR) by examining black type effect and loading amount on performance. The analysis of devulcanization efficiency required Horikx-Verbruggen method to evaluate sol fraction crosslink density relationships. When higher amounts are present, speed crosslinking interactions increases. An increase in rate reached 170% N-330, while N-550 showed an 87% such rates. size particles N-330 does not impact performance results. researchers optimized procedures using temperature time variations as critical variables. study results indicate that reduced combined with shorter periods helps minimize formation, improving aggregation behavior system becomes more pronounced when high-temperature conditions prevail, thus it impacts operations outcome. demonstrates necessity match approaches compound characteristics enhanced product properties extended life span applications.
2. Continuous Extrusion Process for Decrosslinking and Recrosslinking Vulcanized Rubber Waste
RUBBERGREEN INDUSTRIE, 2025
Recycling crosslinked elastomer waste like vulcanized rubber by devulcanization followed by crosslinking again. The recycling process involves continuously extruding the waste rubber in chip form, decrosslinking it inside the extruder, cooling the decrosslinked paste, then mixing in crosslinking agents. This allows recovering high-performance rubber from waste that can be used in new applications. The decrosslinking is done by shearing and self-heating the chips in the extruder, followed by cooling to prevent premature curing before adding crosslinking agents.
3. Hydrothermal Cracking and Fractionation of End-of-Life Tires for Component Recovery and New Tire Production
THE GOODYEAR TIRE & RUBBER CO, 2025
Recycling end-of-life tires into new tires with high efficiency by converting the waste tires into valuable feedstocks for tire production. The tires are hydrothermally cracked to separate oil, water, and solids. The oil is fractionated to extract wax and process oil. The wax is refined and the process oil is steam cracked to make tire components like elastomers, resins, and additives. The solids contain fillers like carbon black and silica. The recovered fillers, wax, and process oil are then used to make new tires, with at least 50% of the tire weight coming from recycled tire materials.
4. Plasma-assisted devulcanization of waste rubber powder using a dielectric barrier discharge reactor
nan jiang, yubo wang, ju li - Research Square, 2025
<title>Abstract</title> The extensive production and consumption of ground tire rubber (GTR) have led to a significant accumulation waste, posing substantial environmental challenge. To enhance the recycling efficiency GTR, this work introduces an innovative plasma-assisted method utilizing dielectric barrier discharge (DBD) technology for devulcanization. Experimental results demonstrate that, after plasma treatment at voltage 18 kV 30 minutes, crosslink density decreased from 2.110<sup> 4</sup> 0.810<sup> mol/cm<sup>3</sup>, gel content reduced 96.890.5%, indicating effective cleavage S-S C-S bonds during process. Notably, corresponding tensile strength elongation break plasma-regenerated reached 10.2 MPa 357.7%, respectively, meeting standards high-grade applications. Finally, plausible mechanism underlying devulcanization process is proposed. This novel approach holds promise enhancing sustainability by enabling efficient eco-friendly recycling.
5. Green Chemical Devulcanization Systems
zaheer ul haq, shifeng wang - Royal Society of Chemistry, 2025
This chapter provides an overview of environmentally-friendly chemical devulcanization systems, with in-depth discussion the key methodologies, advantages, and challenges. Beginning introduction to rubber technologies, proceeds various systems currently in use. A focal point is emergence green practices devulcanization, including thermo-oxidation, bioremediation, utilization supercritical fluids as mediums for devulcanization. The effectiveness, sustainability, applicability different processes are discussed, advantages disadvantages commonly employed devulcanizing agents compared. Finally, a summary findings recommendations future research directions provided. serves comprehensive resource understanding advancements challenges
6. Low‐Temperature Rubber Devulcanization via Sulfate Removal Using Hypochlorous Acid and Novel Turbidimetric Analysis
yonchen hariyanto, chen wai wong, joash ban lee tan - Wiley, 2025
ABSTRACT This study presents a novel approach to rubber devulcanization using combination of hydrochloric acid (HCl) and hydrogen peroxide (H 2 O ) as an alternative traditional nitric acidbased methods. The optimized process, utilizing HCl H relative the rubber's weight, demonstrated superior sulfur removal compared conventional treatments. Notably, :HCl achieved significant extraction, reducing SO 4 content by 0.00444 g at 120% w/w concentration. process effectively restores gummy state with minimal oxidation (17.95%), making it ideal for recycling applications. Sulfur was accurately measured newly developed turbidimetric barium test confirmed through field emission scanning electron microscopy (FESEM) analysis, which revealed morphological changes. Additionally, this method resulted in significantly lower nitration devulcanized acid, potentially allowing material be pressed revulcanized into new products. Finally, gas chromatographymass spectrometry (GCMS) analysis sol fraction that chain scissions led formation various valueadded compounds. challenges indicators succe... Read More
7. Microwave-Assisted Surface Devulcanization Process for Recycling Waste Tire Rubber
1307843 BC LTD, 2025
Recycling waste tires into useful rubber compounds using microwave-assisted surface devulcanization. The process involves separating metal and fibers from waste tires, micronizing the vulcanized crumb rubber, applying a dose of microwave energy to sever sulfidic crosslinks, mixing the devulcanized rubber with plastic and oil, and extruding it to produce recycled rubber compounds like crumb rubber or end-of-life tire compounds. The microwave devulcanization step enables efficient recycling of waste tires without harsh solvents or chemical compatibilizers.
8. Method for Co-Vulcanization of Vulcanized Rubber Using Diffusion Barrier for Crosslinking Control
APPIA, LLC, 2024
Method for recycling vulcanized rubber to increase performance and allow higher recycled rubber content compared to prior methods. The key is using a barrier material to prevent sulfur and cure accelerators from the fresh rubber diffusing into the recycled rubber during co-vulcanization. This prevents additional crosslinking in the recycled rubber and improves bonding between the two types of rubber. The barrier material forms a diffusion barrier around the ground recycled rubber particles in the fresh rubber matrix during vulcanization.
9. Ultrasonic Cracking Method for Producing Reclaimed Rubber from Waste Tires
ANHUI ZHONGHONG RUBBER & PLASTIC CO LTD, 2023
Method for producing reclaimed rubber from waste tires using ultrasonic cracking. The method involves crushing tires, mixing with oil and acid, ultrasonic agitation, aging, extrusion, and kneading. The ultrasonic agitation step breaks down the rubber's crosslinked network using ultrasonic waves. The aging step allows the oil and acid to penetrate. The extrusion and kneading steps further process the rubber. The ultrasonic cracking improves reclaimed rubber properties compared to traditional methods.
10. Process for Producing Rubber Powder from Waste Tires Using Sequential Magnetic, Microwave, and Ultrasonic Treatments
GUIZHOU HUAYU RUBBER TECH CO LTD, GUIZHOU HUAYU RUBBER TECHNOLOGY CO LTD, 2023
A process for preparing high quality rubber powder from waste tires with improved yield and desulfurization compared to existing methods. The process involves cutting waste tires into particles, followed by steps of magnetic separation, microwave radiation, grinding, magnetic separation, microwave radiation, selective separation, desulfurizer treatment, ultrasonic treatment, ammonia circulating fluidized bed treatment, and final microwave radiation to produce the rubber powder. This sequence of treatments allows smooth grinding, high yield, good desulfurization, and high quality rubber powder.
11. Rubber Dissolution Method Using Fatty Acid Methyl Ester and Propyl Bromide for Component Separation
Eiko Co., Ltd., EIKO CO LTD, 2023
Waste disposal method for dissolving rubber products like tires and seismic isolation rubber units to recycle the rubber and separate the rubber and metal components. The method involves immersing the waste rubber in a solvent containing fatty acid methyl ester (FAME) to dissolve the rubber at temperatures below the ignition point. Before dissolution, the rubber can be pretreated with a solvent containing propyl bromide to accelerate dissolution without damaging the metal. This allows separating and recycling the rubber without burning or shredding the waste.
12. Process for Producing Tread Regenerated Rubber Using NMP, DMF, DBTDL, and MBA with Specific Mass Ratios
FUJIAN ZHONGHONG NEW MATERIAL TECH CO LTD, FUJIAN ZHONGHONG NEW MATERIAL TECHNOLOGY CO LTD, 2023
A process for producing tread regenerated rubber that reduces pollution and improves properties compared to conventional methods. The process involves treating waste tire rubber powder with a specific combination of solvents, catalysts, and crosslinking agents to regenerate the rubber into usable tread material. The solvents used are N-methylpyrrolidone (NMP) and dimethylformamide (DMF). The catalyst is dibutyltin dilaurate (DBTDL). The crosslinking agent is N,N'-methylene bisacrylamide (MBA). The mass ratios used are 1:1:1 (solvent:catalyst:crosslinking agent) and 2:0.7:2.5 (rubber:solvent:crosslinking agent). This treatment allows efficient desulfurization and regeneration of the rubber
13. Method for Devulcanizing Diene Rubber Using Solid Amine Compound with Shear Force Application
TOYO TIRE CORP, 2023
A method for producing devulcanized rubber with improved properties after vulcanization. The method involves heating and mixing vulcanized diene rubber with a desulfurizing agent that is a solid amine compound. The mixing is done at temperatures below 100°C to prevent rubber chain scission. Applying a shear force during mixing enhances desulfurization efficiency. The amine compound selectively cleaves sulfur crosslinks without degrading the rubber chain. This produces devulcanized rubber with better post-vulcanization properties compared to conventional devulcanization methods.
14. Devulcanized Rubber with High Molecular Weight Liquid Component via Aldehyde Solvent and Aliphatic Double Bond Cleavage
BRIDGESTONE CORP, 2023
Devulcanized rubber with high molecular weight liquid component for recycling and reuse in rubber products like tires. The devulcanization process involves heating vulcanized rubber in a solvent containing an aldehyde with a carbon chain of at least 2. This breaks crosslinks and generates free radicals. Adding a compound with aliphatic double bonds further helps cleavage. The solvent and reaction conditions prevent complete degradation, yielding a devulcanized rubber with a soluble component having molecular weight 260-600kDa. This can be used as a high molecular weight liquid rubber in new crosslinked products like tires, providing better mechanical strength compared to conventional devulcanized rubbers.
15. Continuous Process for Producing High-Strength Liquid Rubber via Desulfurization and Regeneration of Pulverized Waste Tires
HANGZHOU ZHONGCE RUBBER CYCLE SCIENCE AND TECH CO LTD, HANGZHOU ZHONGCE RUBBER CYCLE SCIENCE AND TECHNOLOGY CO LTD, ZHONGCE RUBBER GROUP CO LTD, 2023
Continuous process for preparing high-strength liquid rubber from waste tires that can be used as a processing aid in tire manufacturing. The process involves crushing tires, removing impurities, and then blending the pulverized rubber with specific proportions of liquid rubbers, functionalized liquid rubbers, and unsaturated dienoic acids. This modified rubber is then extruded to desulfurize and regenerate it into a high-strength, low-viscosity liquid rubber that has improved compatibility, adhesion, and properties compared to unmodified waste tire rubber.
16. Mill-Based Process for Devulcanizing Tire Rubber via High Turbulence and Micronization
ATLANTIS RUBBER POWDERS B V, ATLANTIS RUBBER POWDERS BV, 2023
Manufacturing devulcanized rubber that can be used as a viable substitute to virgin rubber in different types of applications, such as in tyres and general rubber goods such as conveyor belts, sheeting, extrusion profiles and moulded products. The process includes introducing tyre rubber particles to a mill; introducing a gaseous flow in the mill for generating a field of high turbulence, strong eddies and high energy impact between the tyre rubber particles which causes micronization and rupture of the tyre rubber particles due to extreme hysteresis and mechanical forces sufficient to at least partially devulcanize the tyre rubber particles; and fast dissipation of the heat generated into the gaseous flow.
17. Devulcanization of Vulcanized Rubber Using Twin-Screw Extruder with Upper Barrel Regenerative Agent Feed
CONTINENTAL REIFEN DEUTSCHLAND GMBH, 2023
Method for devulcanizing vulcanized rubber to recycle old tires and improve properties of rubber articles. The method involves using a twin-screw extruder with a regenerative agent feed point in the upper half of the barrel. The extruder devulcanizes the rubber at temperatures around 100-150°C. This breaks the sulfur bonds without shortening the polymer chains. The devulcanized rubber can be further processed into new rubber mixtures with better properties compared to using fully devulcanized rubber. The extruder configuration with regenerative agent feed allows efficient devulcanization without chain scission.
18. Rubber Devulcanization via High-Boiling Swelling Agent and Oxygen-Induced Sulfur Oxidation
GOODYEAR TIRE & RUBBER, THE GOODYEAR TIRE & RUBBER CO, 2023
Devulcanization of rubber products like tires to recycle them by breaking the sulfur crosslinks without melting the rubber. The process involves mixing the vulcanized rubber particles with a high-boiling swelling agent and heating them in oxygen. The high-boiling swelling agent causes the rubber to swell, making it easier to break the sulfur bonds. The oxygen oxidizes the sulfur and devulcanizes the rubber. After devulcanization, the rubber chains can be separated from the swelling agent. This allows recycling of the devulcanized rubber by reusing it in new products rather than disposing of it.
19. Extruder-Based Method for Crosslink Disruption and Functional Group Grafting in Tire Rubber Recycling
Hangzhou Zhongce Rubber Recycling Technology Co., Ltd., HANGZHOU ZHONGCE RUBBER LOOP TECHNOLOGY CO LTD, 2022
A method to recycle old tires into reusable rubber by breaking the crosslinks in the tire rubber and adding functional groups to improve compatibility with other rubber compounds. The method involves using an extruder to mechanically shear and heat the tire rubber powder. This partially breaks the three-dimensional network crosslinks, reverting the rubber to a linear structure. Simultaneously, the high temperature and mechanical force cause chemical reactions between the tire rubber and a composite functionalized modifier containing groups like -C=C- and -COOH. This grafts functional groups onto the reverted rubber to improve its properties and compatibility with other rubbers.
20. Reclaimed Rubber Production via Magnetic Separation and Dynamic Desulfurization with Specific Additive Ratios
WANG JINMING, 2022
Reclaimed rubber made by crushing waste vulcanized rubber and separating it by magnetic separation to obtain rubber powder, which is then dynamically desulfurized and refined. The preparation includes uniformly mixing 98-102 parts by weight of waste tire rubber powder, 4-8 parts by weight of regeneration activator, 6-12 parts by weight of paraffin oil and 1-4 parts by weight of anti-aging agent, Add to the reaction kettle for reaction, the reaction temperature is 100-130 °C, and the reaction time is 2-4 hours; After completion, the cooling water is cooled, and the temperature of the material in the reaction kettle is lowered to 60-80 ° C, and then 6-12 parts of regeneration activator, 0.2-5 parts of aromatic oil, 0.8-2.4 parts of zinc oxide, 0.3-1.2 parts of regenerating activator are added.
Get Full Report
Access our comprehensive collection of 80 documents related to this technology
Identify Key Areas of Innovation in 2025
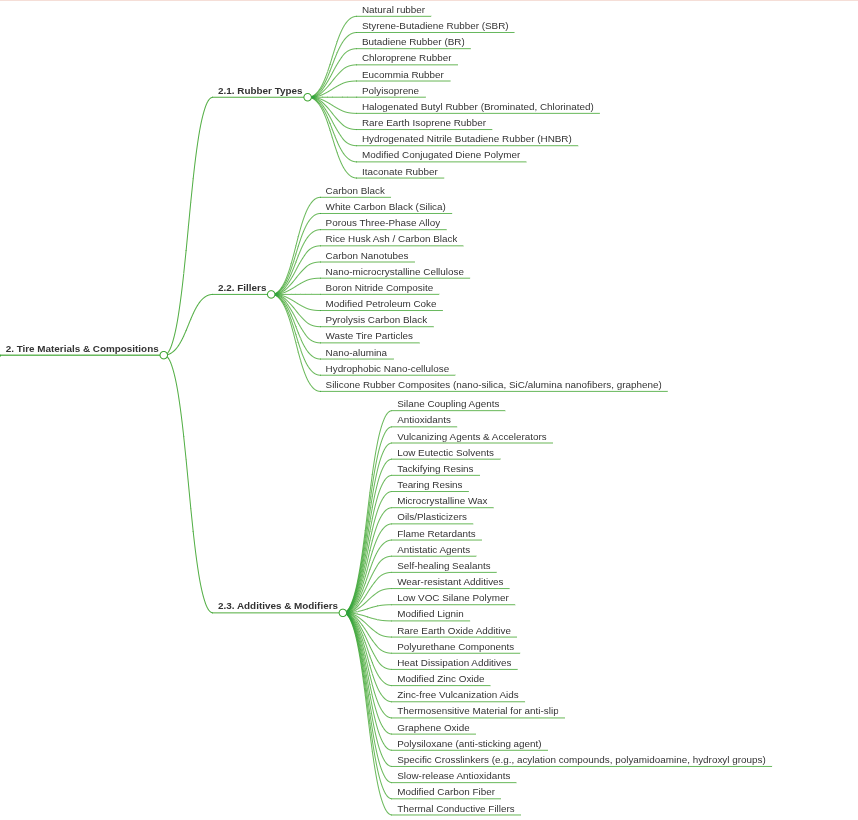