Vulcanization Techniques for Tire Performance Optimization
Modern tire compounds require precise control of vulcanization chemistry to achieve specific mechanical properties. During vulcanization, crosslink density must be carefully managed at temperatures between 150-180°C, where competing reactions can lead to network degradation and reversion. Current industrial processes struggle to maintain optimal crosslinking while preventing thermal degradation, particularly in compounds requiring high elasticity.
The fundamental challenge lies in controlling the rate and extent of crosslinking reactions while preventing network breakdown during the vulcanization process.
This page brings together solutions from recent research—including specialized auxiliary agents that reduce reversion, metal-organic crosslinking systems, optimized carbon black ratios, and novel vulcanizing agents with controlled reaction kinetics. These and other approaches focus on achieving consistent mechanical properties while maintaining practical processing windows in industrial tire manufacturing.
1. Cross-Linked Rubber Composition with Ethylene-Based Polymer and Specific Crosslinking Accelerators
Asahi Kasei Corporation, ASAHI KASEI KK, 2023
Cross-linked rubber composition for tires with improved properties like faster vulcanization, higher tensile modulus, and better tear strength compared to conventional rubber compositions. The composition contains a rubber-like polymer with an ethylene structure and unsaturated groups. The ethylene content and iodine value of the polymer are optimized to balance properties like crosslink density, vulcanization speed, and tensile modulus. The composition also uses a crosslinking accelerator like guanidine or thiazole derivatives.
2. Rubber Composition Incorporating Bis(2-Citraconimidophenyl) Disulfide for Enhanced Crosslinking Density and Reduced Vulcanization Reversion
JIANGSU RUIBA NEW MATERIAL TECH CO LTD, JIANGSU RUIBA NEW MATERIAL TECHNOLOGY CO LTD, 2023
Rubber composition with high stretching stress for applications like tires that reduces reversion during vulcanization and improves stretching properties. The composition contains natural rubber, filler, activator, anti-aging agent, sulfur, accelerator, metal organic matter, and a specific auxiliary agent called bis (2-citraconimidophenyl) disulfide. This auxiliary agent improves crosslinking density and reduces reversion during vulcanization, allowing higher stretching stress compared to traditional rubber compositions.
3. Rubber Composition with Disulfide-Bonded Vulcanization Auxiliary and Controlled Sulfur Ratio
SOUTH CHINA UNIV OF TECHNOLOGY, SOUTH CHINA UNIVERSITY OF TECHNOLOGY, 2023
Rubber composition with improved processability and reduced vulcanization reversion, and a preparation method using green vulcanization aids. The composition contains rubber, filler, zinc oxide, antioxidant, sulfur, and promoter. The vulcanization auxiliary agent is a compound with a disulfide bond and a vinyl or citraconimide group. This auxiliary improves processing by peptizing the rubber and reduces reversion by crosslinking during overvulcanization. The dosage ratio of the auxiliary to sulfur is limited to optimize its effects. The auxiliary has a disulfide bond to work with sulfur in vulcanization.
4. Rubber Compound with Styrene-Butadiene Copolymer Blend and Accelerated Vulcanization System
CONTINENTAL REIFEN DEUTSCHLAND GMBH, 2022
Sulphur-vulcanizable rubber compound for tire treads that provides improved elongation at break. The compound contains a specific blend of styrene-butadiene copolymers with different microstructures. The copolymers have styrene contents of 25-35 wt% and 40-45 wt%, respectively. The compound also has a specific accelerated vulcanization system containing CBS, TBzTD, and elemental sulfur. The compound improves tire elongation at break compared to conventional tire rubber compounds.
5. Continuous Vulcanization Rubber Composition with Calcium Oxide and Lewis Acid Additives
JIANGSU RUIBA NEW MATERIAL TECH CO LTD, JIANGSU RUIBA NEW MATERIAL TECHNOLOGY CO LTD, 2022
High-performance continuous vulcanization rubber with improved properties and a process to make it. The rubber composition contains EPDM base, vulcanizing agent, promoters, calcium oxide, and a Lewis acid like anhydrous ferric chloride. The calcium oxide absorbs moisture from the rubber raw materials to prevent air bubbles during vulcanization. The Lewis acid accelerates the vulcanization process and prevents chelation of the accelerator by calcium oxide. This allows faster vulcanization and better crosslinking density compared to using calcium oxide alone. The process involves mixing the rubber components in an open mill at elevated temperature and short time, followed by vulcanization at lower temperature for a shorter duration.
6. Rubber Vulcanizing Agent Comprising Organic Sulfur Compounds from High Molecular Weight Resin and Low Molecular Weight Olefin Reaction
YOKOHAMA RUBBER CO LTD, YOKOHAMA RUBBER CO LTD:THE, 2022
Vulcanizing agent for rubber compositions that improves elongation at break, resistance to heat aging, and resistance to abrasion compared to conventional sulfur vulcanization. The vulcanizing agent is a mixture of organic sulfur compounds formed by reacting a high molecular weight resin, a low molecular weight olefin compound, and sulfur in the presence of a vulcanization accelerator.
7. Rubber Vulcanizing Agent Comprising Resin-Sulfur Reaction Product with Specific Softening Point
YOKOHAMA RUBBER CO LTD, YOKOHAMA RUBBER CO LTD:THE, 2022
A vulcanizing agent for rubber compounds that improves elongation, heat aging resistance, and wear resistance of vulcanized rubbers compared to conventional sulfur-based vulcanization. The vulcanizing agent is a mixture of a specific resin with a softening point of 50-140°C and sulfur, formed by reacting them in the presence of a vulcanization accelerator. The unique resin-sulfur reaction creates a novel vulcanizing agent with enhanced rubber compound dispersibility and vulcanization properties.
8. Elastomeric Compositions with Reversible Metal Cation Cross-Linking Agent Forming Three-Dimensional Lattice in Cured Rubber
PIRELLI, PIRELLI TYRE SPA, 2022
Elastomeric compositions for tire treads that provide improved road grip, rolling resistance, and wear compared to conventional tire compounds. The compositions contain a reversible cross-linking agent with a metal cation, like zinc, that forms a three-dimensional lattice in the cured rubber. This lattice enhances hysteresis properties of the rubber to provide better grip in sports driving conditions, reduced rolling resistance, and lower wear in moderate driving conditions. The compositions also contain standard tire components like diene elastomers, fillers, and vulcanizing agents.
9. Process for Preparing Vulcanizable Elastomeric Composition with Mixed Silica Fillers and Silane-Reactive Functionalization
PIRELLI, PIRELLI TYRE SPA, 2022
A process for preparing a vulcanizable elastomeric composition with improved properties for tire treads. The composition contains a combination of a non-functionalized silica filler and a functionalized silica filler. The process involves mixing the elastomer, non-functionalized silica, and functionalized silica in specific ratios. The functionalized silica has silane groups that react with the elastomer. This improves dispersion of the silicas during mixing and vulcanization. The composition provides better balance of rolling resistance, grip, and mechanical properties compared to using just non-functionalized silica.
10. Multi-Network Elastomer with Ethylene/Acrylic Matrix and Amide Crosslinks Formed by Hexamethylene Diamine Carbamate
AGRICULTURAL PRODUCT PROCESSING RES INST CHINESE ACADEMY TROPICAL AGRICULTURAL SCIENCES, AGRICULTURAL PRODUCT PROCESSING RESEARCH INSTITUTE CHINESE ACADEMY OF TROPICAL AGRICULTURAL SCIENCES, LINGNAN NORMAL UNIVERSITY, 2021
High-performance multi-network structure elastomer with enhanced mechanical properties, viscoelasticity, and damping compared to conventional rubber compounds. The elastomer is made using ethylene/acrylic elastomer (AEM) as the matrix material, with hexamethylene diamine carbamate (Diak No. 1) as the vulcanization crosslinking agent. The AEM rubber contains ethylene, methyl acrylate, and vulcanization points. The amine crosslinking agent forms amide bonds in the rubber network. This multi-network structure with amide crosslinks provides improved mechanical properties, viscoelasticity, and damping compared to conventional rubber compounds.
11. Method for Sequential Vulcanization of Immiscible Elastomer Blends with Controlled Filler Distribution
ExxonMobil Chemical Patents Inc., 2021
A method to create double-vulcanized elastomer compositions with improved filler and plasticizer distribution compared to traditional immiscible blends. The method involves sequentially vulcanizing the immiscible elastomers separately. First, a curative system is activated to vulcanize one elastomer in dispersed phase while the other elastomer remains flowable. Then, the partially vulcanized mixture is vulcanized again to fully cure the second elastomer. This prevents fillers and plasticizers from migrating between phases during vulcanization.
12. Rubber Compound Vulcanization with Polyol-Based Accelerator Integration
CEAT LIMITED, 2021
Efficient and cost-effective vulcanization of rubber compounds using a polyol-based accelerator like glycerol in addition to conventional accelerators like sulfur. The mix of elastomer, cross-linking agent, and polyol-based accelerator provides vulcanization times and properties comparable to using only conventional accelerators. The polyol accelerator can replace some or all of the conventional accelerator, reducing cost and improving efficiency.
13. Diene Rubber Compound with Brominated Isobutylene-p-Methylstyrene Copolymer and Fine Particle Carbon Black
CHENG SHIN RUBBER IND LTD, CHENG SHIN RUBBER XIAMEN IND LTD, 2021
Rubber formula for tire compounds that reduces the length of uncured rubber after vulcanization and prevents crude rubber from breaking and blocking holes. The formula contains diene rubber, brominated isobutylene-p-methylstyrene copolymer (BIMSM), carbon black filler with smaller particle size, and optimized ratios of carbon black sizes. Adding BIMSM and smaller carbon black reduces fluidity while maintaining strength. This shortens uncured rubber length and prevents breaks during vulcanization.
14. Rubber Compound Incorporating Serpentinite as Vulcanization Accelerator and Reinforcement Agent
OTTAVIO RAUL DOMENICO RIBERTI CARMIGNANO, 2021
Using serpentinite as a vulcanization accelerator, activator, and reinforcer in rubber compounds like natural rubber (NR) and styrene-butadiene rubber (SBR). Serpentinite, an inorganic magnesium silicate, was found to significantly reduce vulcanization times and increase mechanical properties like modulus, strength, and elongation at break when added to rubber compounds during vulcanization.
15. Vulcanizing Compositions with Cyclododecasulfur for Enhanced Thermal Stability in Elastomers
EASTMAN CHEM CO, EASTMAN CHEMICAL CO, 2020
Vulcanizing compositions and processes for vulcanizing elastomers that provide improved thermal stability and processing conditions compared to conventional sulfur-based vulcanizing agents. The compositions contain a cyclododecasulfur compound as the vulcanizing agent, which has a high melting point and improved thermal stability compared to conventional insoluble sulfur. This allows higher processing temperatures and reduces the risk of premature crosslinking during mixing, extrusion, calendering, etc. The cyclododecasulfur vulcanizing agent enables faster processing speeds and better performance in elastomeric compounds compared to conventional sulfur vulcanizing agents.
16. Chalcogenide Hybrid Inorganic/Organic Polymer Vulcanizing Agent for Rubber and Polymers
ARIZONA BOARD OF REGENTS ON BEHALF OF THE UNIVERSITY OF ARIZONA, 2020
Using a novel chalcogenide hybrid inorganic/organic polymer (CHIP) material as a vulcanizing agent for rubber and other polymers. The CHIP material has chalcogenic monomers like sulfur or selenium, and comonomers with reactive functional groups. It can vulcanize latex rubber at lower temperatures and shorter times compared to traditional sulfur vulcanization. The CHIP vulcanization is more efficient and compatible with polymers, providing crosslinked rubbers with improved properties.
17. Preparation Method for Sidewall Rubber Composition Incorporating Natural Rubber and EPDM Blend with Anti-Reversion Additives
DONGYING FANGXING RUBBER CO LTD, 2020
Preparation method for sidewall rubber for run-flat tires that reduces reversion during vulcanization to improve long-term properties. The method involves using a specific blend of natural rubber, ethylene propylene diene monomer (EPDM), carbon black, elastomer compatibilizer, zinc oxide, stearic acid, process oil, mold release agent, microcrystalline wax, anti-aging agent, accelerator, sulfur, and an optional anti-reversion auxiliary agent. The blended rubber composition improves compatibility between the natural rubber and EPDM to prevent network cracking and degradation during vulcanization.
18. Lanthanide-Catalyzed High Cis Content Block Copolymers of Polybutadiene and Polyisoprene with Pseudo-Living Polymerization
BRIDGESTONE CORP, 2019
High cis content block copolymers of polybutadiene and polyisoprene for tire applications with improved low temperature properties, wear resistance, and reduced cut growth. The copolymers have a cis content of at least 90%, prepared using lanthanide-based catalysts in a pseudo-living polymerization process. The catalyst comprises a lanthanide compound, aluminoxane, organoaluminum compound, and halogen compound. The pseudo-living polymerization allows selective block formation with reactive chain ends that can be functionalized. The copolymers are used in vulcanizable compositions for tire components like sidewalls and treads.
19. Preparation Process for Crosslinkable Rubber Compound Incorporating High Melting Point Vulcanization Accelerators
CONTINENTAL REIFEN DEUTSCHLAND GMBH, 2019
A process for preparing a crosslinkable rubber compound for bonding vulcanized and unvulcanized rubber components in cold-renewal applications like tire retreading. The compound contains vulcanization accelerators with melting points above 130°C. The accelerators are mixed into the compound below their melting points, preventing reaction. But during extrusion steps like retreading, the heat activates the accelerators for rapid vulcanization. This balance between storage stability and process reactivity allows the compound to bond components without premature cure.
20. Rubber Compositions with Low Initiator Time Vulcanization Accelerators and Diene Elastomers for Enhanced Stiffness
COMPAGNIE GENERALE DES ETABLISSEMENTS MICHELIN, 2019
High stiffness rubber compositions for tire treads that provide improved stiffness without compromising other properties like processability. The compositions contain diene elastomers, fillers, and crosslinking agents. The crosslinking is done using a low initiator time vulcanization accelerator to increase stiffness. The accelerator has an initiation time below 3 minutes. This allows higher stiffness without adding large amounts of stiffening resins. The low initiator time accelerator speeds up curing and prevents over-crosslinking.
Get Full Report
Access our comprehensive collection of 63 documents related to this technology
Identify Key Areas of Innovation in 2025
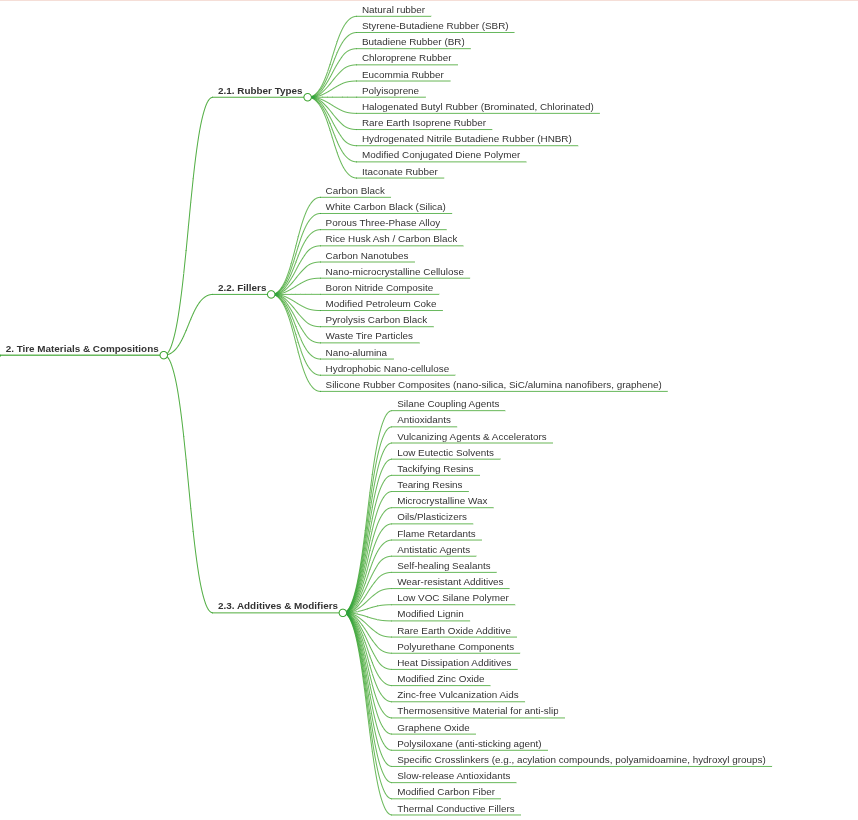