Calendering for Tire Production
Calendering in tire manufacturing requires precise control of rubber sheet thickness, surface texture, and compound homogeneity. Current processes operate at speeds of 30-60 meters per minute while maintaining thickness variations within ±0.05mm across sheets up to 2 meters wide. These tolerances become particularly critical when preparing compounds for specialized tire components like treads and sidewalls.
The fundamental challenge lies in achieving uniform material properties and dimensional accuracy while maximizing throughput rates without introducing internal stresses or surface defects.
This page brings together solutions from recent research—including decentralized manufacturing approaches, specialized rubber tape winding techniques, fiber-reinforced compound processing, and advanced green tire assembly methods. These and other approaches focus on improving calendering efficiency while maintaining strict quality requirements for modern tire production.
1. Green Tire Production Method with Localized Sidewall Reinforcement for Enhanced Protrusions
Sumitomo Rubber Industries, Ltd., 2024
Green tire production method to enable larger sidewall protrusions without increasing weight or rolling resistance. The method involves locally reinforcing the sidewall rubber in regions with protrusions during green tire production. After forming the tire carcass, sidewall rubber is wound onto the outer surfaces. Then, a band-shaped reinforcement is attached to specific areas on the sidewalls where protrusions will be molded. This provides extra thickness at those points without excess in other areas. When the green tire is vulcanized, the reinforcements align with recesses in the mold to form the protrusions. This allows larger sidewall features without over-thickening the sidewalls overall.
2. Calendering and Molding Equipment with Dual Opposing Rolls and Multi-Roller Temperature Regulating Devices
Jiangsu Inpu Technology Co., Ltd., JIANGSU EMP TECH CO LTD, 2024
Calendering and molding equipment with temperature adjustment to control roller temperatures for consistent material processing. The equipment has two opposing calendering rolls, each with a temperature regulating device attached. The temperature regulating devices contain multiple rollers with internal cooling channels. They can be adjusted and buffered using an external bracket. This allows precise temperature control on each roll to prevent material sticking or deformation during calendering.
3. Rubber Calendering Device with Integrated Heating Blocks in Lower Rolls
HEFEN RONGLI RUBBER AND PLASTIC SCIENCE AND TECH LIMITED CO, HEFEN RONGLI RUBBER AND PLASTIC SCIENCE AND TECHNOLOGY LIMITED CO, 2022
A rubber calendering device that improves quality and efficiency of rubber calendering by eliminating the need for preheating and reducing calendering time. The device has multiple calendering rolls below a feeding roll. Heating blocks in the lower rolls preheat the rubber before it is compressed and calendered. This prevents dissipation of heat during placement, which can cause calendering defects. The heated rubber is pushed through and cut off by the lower rolls, then moved to the upper rolls for calendering. This allows immediate calendering without waiting for the rubber to warm up.
4. Tire Molding System with Integrated Radial Channels for Fluid Discharge
PIRELLI TYRE S.p.A., 2022
Controlling fluid discharge during tire molding to improve vulcanization and prevent defects. The method involves building the green tire with a radially internal surface that has channels or grooves extending from the belt to the sidewall. These channels connect to the mold's discharge channels. This allows fluids between the mold and green tire to flow out, preventing trapped air pockets and improving adhesion during vulcanization. The channels can be continuous elastomeric coils wound into the tire.
5. Auxiliary Device with Figure-Eight Shaped Rolling Spokes and Synchronized Gear-Worm Mechanism for Rubber Calendering
JIANG XIUZHEN, 2021
An auxiliary device for improving rubber calendering processes. The device has a fixed box with a molding press hole and two sets of figure-eight shaped rolling spokes inside. One set has fixed gears at the top and universal joints at the bottom. The other set has worms at the bottom connected to a motor. This allows synchronized, coordinated movement of the spokes to evenly press the rubber between them, preventing uneven widths and improving sheet quality.
6. Automated Tire Manufacturing Machine with Integrated Stirring and Calendering Devices Featuring Adjustable Spiral Cylinders and Screw Belt Agitation
LI SHUBO, 2021
Automobile tire manufacturing and processing technology that reduces waste, improves efficiency, and simplifies processing steps compared to traditional methods. The technology uses an automated tire manufacturing machine with features like a stirring device, calendering device, and specialized barrels. The stirring device has a rotating column with screw belts to agitate and melt the rubber. The calendering device has spiral-wrapped cylinders with adjustable lengths and angles to control the thickness and shape of the extruded rubber. This allows precise calendering without trimming or scraping, as the cylinders can be quickly swapped out. The stirring and calendering steps are integrated into the machine to minimize waste and simplify processing. The stirring device scrapes and filters the rubber before extrusion, and the calendering device has features like arc-shaped grooves and adjustable spacing to optimize processing.
7. Rubber Cloth Production Process with Sequential Calendering and Drum Vulcanization
WUXI DEBANG RUBBER IND CO LTD, WUXI DEBANG RUBBER INDUSTRY CO LTD, 2021
A production process for improving the elasticity of rubber cloth by using a specific calendering and vulcanization sequence. The process involves initially calendering the rubber between two rolls, then conveyor belt transport followed by vulcanization on a drum. The final calendering step is done after vulcanization using the original calendering rolls to further shape the rubber. This sequence reduces viscosity and deformation issues compared to traditional pressing-vulcanization-calendering methods.
8. Tire Belt Laminating Process Utilizing Four-Spoke Calender with Defined Temperature Profile
SHANDONG LINGLONG TYRE CO LTD, 2021
A tire belt laminating process that reduces belt sticking and improves belt quality during tire manufacturing. The process involves using a four-spoke calender with specific temperature settings to bond rubberized steel wire. The rubber supply temperature is 95-105°C, the upper and middle spoke rollers are 60-70°C, the side spoke roller is 85-95°C, and the lower spoke roller is 85-95°C. The belt temperature is maintained at 80°C. This temperature profile reduces belt sticking, improves belt surface quality, and allows faster calendering speeds compared to traditional belt lamination processes.
9. Multi-Roll Calender with Oppositely Turning Rolls and Adjustable Jacking Rod Mechanism
JIANGSU MAGICPOWER POWER SUPPLY EQUIPMENTS & TECH CO LTD, JIANGSU MAGICPOWER POWER SUPPLY EQUIPMENTS & TECHNOLOGY CO LTD, 2020
High-safety multi-roll calender that can quickly adjust the calendering state. The calender has features like oppositely turning calendering rolls, an adjusting mechanism with a jacking rod, a rubber hanging mechanism with separate cylinders and a rubber tube, and a winding mechanism. These features allow quick adjustment of calendering force, roll gap, and rubber thickness during processing.
10. Concave-Convex Nested Roller Calender with Integrated Laminating and Forming Mechanism
HUAIYIN INST TECHNOLOGY, HUAIYIN INSTITUTE OF TECHNOLOGY, 2020
A concave-convex nested rubber calender with integrated laminating and forming capabilities. The calender has two parallel rollers, a first roller with bumps on its surface and a second roller with matching larger grooves. The rollers rotate at the same speed and the bumps fit into the grooves. This allows the rollers to simultaneously laminate and form the rubber materials. The concave-convex configuration provides a continuous process without separate steps for bonding and forming.
11. Composite Rubber with Dispersed Tetrapod-Shaped Ceramic Crystals and Manufacturing Method
Moon Sang-hoon, 2020
Composite rubber with improved slip resistance for shoes and tires, and a method to manufacture it. The composite contains a tetrapod-shaped ceramic single crystal dispersed in the rubber matrix. The crystals significantly enhance friction and abrasion resistance compared to regular rubber. The composite is made by mixing the rubber, blending agents, and crystals, kneading, calendering, and molding.
12. Vulcanizing Composition with Cyclododecasulfur for Enhanced Thermal Stability and High-Temperature Processing
EASTMAN CHEM CO, EASTMAN CHEMICAL CO, 2020
Vulcanizing compositions and processes for vulcanizing elastomers that provide improved thermal stability and processing conditions compared to conventional sulfur-based vulcanizing agents. The compositions contain a cyclododecasulfur compound as the vulcanizing agent, which has a high melting point and improved thermal stability compared to conventional insoluble sulfur. This allows higher processing temperatures and reduces the risk of premature crosslinking during mixing, extrusion, calendering, etc. The cyclododecasulfur vulcanizing agent enables faster processing speeds and better performance in elastomeric compounds compared to conventional sulfur vulcanizing agents.
13. Three-Roll Calender with Angled Upper Roll and Two-Stage Profiling for Rubber Compounds
COMPAGNIE GENERALE DES ETABLISSEMENTS MICHELIN, MICHELIN RECHERCHE ET TECHNIQUE S.A., 2018
A calender for profiling rubber compounds used in tire casings that reduces defects in the profiled sheets. The calender has three rolls with parallel axes where the lower and intermediate rolls are vertically aligned and the upper roll is angled. The lower and intermediate rolls form the main profiling nip, while the upper roll forms a secondary nip. After exiting the main nip, the profiled sheet goes onto a table to separate it further. This two-stage profiling with a separating table prevents lateral edge and cohesion defects in the profiled sheets that can occur with single-stage calendering.
14. Method for Manufacturing Rubber Sheet with Selective Surface Semi-Vulcanization Using Differential Thermal Treatment
Yokohama Rubber Co., Ltd., 2018
Method for manufacturing a sheet-shaped rubber member that can easily bring only one surface of the sheet into a semi-vulcanized state. It involves heating one surface of the rubber sheet using a contact heating device while cooling the other surface. The temperature difference between the heated surface and the cooled surface is 80°C or more. The heat history applied to the heated surface is 3-10 minutes at an equivalent vulcanization degree of 150°C. This selectively semi-vulcanizes one side of the rubber sheet to prevent cord biting in tires. The cooling prevents shrinkage.
15. Method for Forming Raw Green Tires with Continuous Conductive Inserts via Simultaneous Rubber Feeding and Extrusion
COMPAGNIE GENERALE DES ETABLISSEMENTS MICHELIN, 2016
A method for manufacturing raw green tires with improved electrical conductivity inserts between the tread and carcass layers. The method involves simultaneously feeding rubber into the gap between two calendered layers to form the ply, while also continuously extruding rubber from nozzles extending from the sides of the calender into the gap. This creates conductive inserts between the ply layers. The nozzle rubber extends continuously from one ply to the next to maintain electrical conductivity through the tire.
16. Calender Roller Speed Differential Method for Elastomer Sheet Non-Adhesion
COMPAGNIE GENERALE DES ETABLISSEMENTS MICHELIN, MICHELIN RECHERCHE ET TECHNIQUE SA, 2016
Preventing adhesion of elastomer sheets to calender rollers during startup and continuous operation to allow automatic threading through the calender rolls without operator intervention. The method involves running the slower roller at a lower speed compared to the faster roller. This reduces adhesion force between the sheet and slower roller, allowing it to detach and pass through the nip. During startup when the sheet is not under tension, the lower roller speed prevents sticking. During continuous operation, the lower roller speed helps detach the sheet as it passes through the nip. The higher roller speed after startup counteracts tension forces.
17. Automated Tire Rolling Line with Integrated Real-Time Thickness Measurement and Quality Control System
SHANDONG YONGTAI GROUP CO LTD, 2016
Automated tire rolling production line with real-time thickness measurement and quality control to improve efficiency and quality. The line has a rolling system with a host calender, tension adjustment, ply conduction, cooling, storage, after-traction, cutting, and winding. The calender has a thickness sensor connected to a display, weight sensor, and recording module. This allows real-time monitoring of ply thickness during rolling. If thickness deviates from set values, the host stops. This prevents defective products and allows identification and correction of issues.
18. Compression Molding Method for Tire Tread Feature Formation
Bridgestone Americas Tire Operations, LLC, 2016
A method for manufacturing tires with features like ribs, lugs, bars, or tread blocks using compression molding instead of conventional vulcanization. The process involves making green (unvulcanized) tire segments in a compression mold with negative shapes of the desired tread features. These segments are then assembled onto the green carcass and vulcanized with the mold features aligned. This allows precise replication of the tread design without the need for viscous rubber filling gaps during vulcanization.
19. Manufacturing Apparatus with Integrated Rubber Supply and Feedback-Controlled Extruder for Tire Top Rolls
SUMITOMO RUBBER IND, SUMITOMO RUBBER IND LTD, 2016
A manufacturing apparatus and method for making tire top rolls with reduced defects compared to conventional methods. The apparatus has a rubber supply unit with an extruder and cutter blade to directly feed rubber to the calendar roll. This eliminates the need for separate heating and cutting steps. Sensors monitor rubber amount and temperature on the calendar roll. Feedback adjusts the extruder temperature based on roll temperature, preventing sticking. This allows real-time rubber supply to the calendar roll, preventing defects like rubber attachment.
20. Open Roll Calendering Method for Polyether Thermoplastic Polyurethane Composites
Jiangsu Zengqiang New Material Technology Co., Ltd., Jiangsu Jinlin Outdoor Products Co., Ltd., Jiangsu Jinling Net Industry Co., Ltd., 2016
Processing method for polyether thermoplastic polyurethane elastomer (TPU) composites using an open roll calender. The method involves extruding the TPU material between rollers in a calender setup to produce thin sheets. The TPU composition can have fillers, plasticizers, or other additives to optimize properties like strength, flexibility, and weather resistance. The open roll calendering allows continuous production of TPU sheets with wide widths and uniform thickness. The sheets can be further processed into finished products like covers, coatings, and films with improved properties compared to PVC.
Get Full Report
Access our comprehensive collection of 23 documents related to this technology
Identify Key Areas of Innovation in 2025
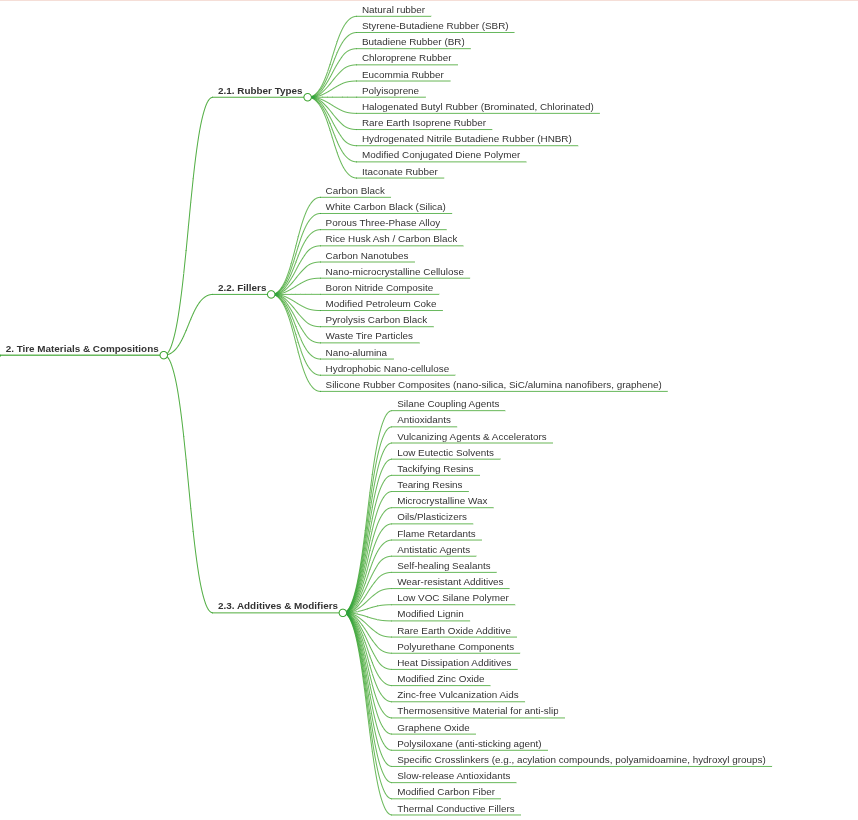