Mixing Equipment for Tire Production
Modern tire manufacturing requires precise mixing of up to 30 distinct components, including polymers, fillers, and chemical agents, at temperatures between 120-150°C. Internal mixing chambers must maintain uniform dispersion while managing material viscosities that can vary by several orders of magnitude during the process. Current systems struggle to achieve consistent mixing quality across batch sizes ranging from 150 to 400 liters.
The fundamental challenge lies in balancing thorough material dispersion against the heat generation that occurs during high-shear mixing operations.
This page brings together solutions from recent research—including tandem mixer systems with variable blade speed ratios, sealed chambers with rotatable enclosures, and multi-stage temperature-controlled mixing sequences. These and other approaches focus on achieving uniform dispersion while preventing material degradation and maintaining precise temperature control throughout the mixing cycle.
1. Upper Mixing Auxiliary Machine with Internal Stirring Chamber and External Motor for Rubber Processing
HENAN GUILUN TYRE CO LTD, 2023
Upper mixing auxiliary machine for rubber tire production that has an internal mixing chamber for stirring and mixing rubber. The upper end of the chamber has a feed port to add materials. An internal stirring mechanism mixes the rubber. A motor outside the chamber drives the stirrer. The lower end has a discharge pipe with a holding box. This upper mixing auxiliary machine for rubber tire production allows efficient internal mixing of rubber in a dedicated chamber before further processing.
2. Sealed Rubber Mixing Machine with Rotatable Enclosed Chamber and Integrated Drive System
HENAN GUILUN TYRE CO LTD, 2023
A closed rubber mixing machine for tire production that reduces pollution compared to open mixers. It has a sealed mixing chamber around the rotor to enclose the mixing process and prevent toxic gases from escaping. The chamber is attached to a frame that connects to the base and rotor via bearings. This allows the chamber to rotate with the mixer while being sealed. The machine also has a motor, reducer, and coupling to drive the mixer.
3. Rotating Barrel Mixing Device with Sliding Sealing Plate and Anti-Accumulation Mechanism for Tire Production
JIANGSU ANLUCHI TECH CO LTD, JIANGSU ANLUCHI TECHNOLOGY CO LTD, 2023
Raw material mixing device for tire production that allows full mixing and stirring of materials without material accumulation at the bottom. The device has a rotating barrel with a closing plate and a sliding sealing plate. The closing plate can seal the barrel to contain the materials. The sliding sealing plate can move along the barrel to close the feeding and discharge ports. When the materials are mixed, the barrel rotates and the materials swing out the top. The sealing plate moves to prevent material buildup at the bottom. This allows full mixing without obstruction. The device has features like snap-fit components, springs, and hooks to enable easy sealing and unsealing operations.
4. Mixing Device with U-Shaped Frame and Spiral Stirring Blades for Aviation Tire Rubber Compounds
QINGDAO SENTURY TIRE CO LTD, 2023
Mixing device for aviation tire production that provides optimal mixing of tire rubber compounds to improve tire quality. The device has a U-shaped fixed frame, a mixing assembly with a rotating rod and spiral stirring blades driven by a motor, and a direction changer with bevel gears to rotate the mixing assembly. This allows 360 degree mixing without dead zones. A removable top cover, feed pipe, and handle complete the device.
5. Method for Producing Rubber Mixtures Using Tandem Mixers with Variable Blade Speed Ratios
Continental Reifen Deutschland GmbH, 2023
A method for producing rubber mixtures using tandem mixers with optimized blade speeds to improve dispersion and homogeneity. The key steps are: 1. Mixing the rubber in the first mixer with higher blade speeds. 2. Transferring the mixed rubber to the second mixer with lower blade speeds. 3. Finishing mixing the rubber in the second mixer. The ratio of blade field speeds in the first and second mixers should be in the range of 100:1 to 1:2. This allows achieving better dispersion and homogeneity in the finished rubber compared to using the same blade speeds in both mixers.
6. Horizontally Arranged Mixing Device with Telescopic Adjustable Stirring and Pressing Assemblies for Tire Rubber Compounds
Weifang Shunfuchang Rubber and Plastics Co., Ltd., WEIFANG SHUNFUCHANG RUBBER & PLASTIC CO LTD, 2023
Mixing and internal mixing device for tire rubber compound formula that improves mixing quality, adaptability, and adjustability compared to existing internal mixers. The device has a horizontally arranged assembly base with a stirring mixing assembly and an internal mixing and pressing assembly. The stirring assembly has a mixing drum that rotates between vertical support plates. The pressing assembly has telescopic adjustment to change the distance between high-temperature compression spokes and spiral feeding spokes. This allows customization of mixing and pressing conditions for different rubber compounds. The telescopic adjustment also syncs the pushing plate position inside the mixing box. The mixing drum and feeding spokes rotate to transport and mix the rubber. The adjustable assembly enables optimized mixing and pressing for different rubber compounds compared to fixed internal mixers.
7. Rubber Mixing Device with Oppositely Rotating Tank, Fan, and Multi-Roller Mechanism
MAANSHAN JIECHUANG PLASTICS TECH CO LTD, MAANSHAN JIECHUANG PLASTICS TECHNOLOGY CO LTD, 2023
A high-performance rubber tire mixing device that provides improved mixing of rubber compound ingredients to make better tires. The device uses a unique rotating mechanism with multiple rollers and a fan inside a rotating tank. This allows simultaneous rotation of the tank, fan, and rollers in opposite directions to thoroughly mix the rubber ingredients. The fan pushes the materials against the tank wall and the rollers rotate the frame around a circular track. This forces the ingredients to move and mix as they are fed into the tank. The tank rotation direction is opposite the fan to avoid segregation. After mixing, the tank can be tilted to discharge the mixed rubber.
8. Three-Stage Mixing Process for Silica-Filled Rubber Compounds with Controlled Temperature Sequence
HUBEI LINGLONG TIRE CO LTD, SHANDONG LINGLONG TYRE CO LTD, 2023
A mixing process for rubber compounds used in tire production that reduces heat generation during mixing of silica-filled rubber compounds compared to conventional mixing methods. The process uses a three-stage mixing sequence in internal mixers, all at temperatures below 150°C. This allows better dispersion of silica without agglomeration and reduces heat generation compared to longer, multi-stage mixing. The lower temperatures also prevent excessive rubber degradation. The three-stage process involves mixing raw materials, then adding silica and dispersing it, followed by final mixing. This controlled constant temperature mixing sequence improves dispersion of silica and reduces heat generation during mixing of silica-filled rubber compounds for tires.
9. Automatic Stirring Device with Central Shaft Agitator and Separate Liquid Diversion for Tire Vulcanization Bladder Production
SHANDONG YONGYU RUBBER CO LTD, 2023
Automatic stirring device for producing tire vulcanization bladders that allows uniform mixing of liquid and solid materials. The device has an agitator body with a central shaft, a diversion assembly for feeding liquid, a solid delivery pipeline, an agitation assembly, and a mixed material output pipeline. The liquid diversion assembly allows feeding liquid into the agitator body without direct addition, preventing concentration issues. The solid delivery pipeline feeds solids into the agitator body. The agitation assembly with blades stirs the mixed materials. This enables separate feeding and uniform mixing of the liquids and solids.
10. Raw Material Mixing Device with Integrated Crushing Mechanism and Spiral Delivery Rod for Rubber Tire Production
QINGDAO TAIHENGYUAN METAL PRODUCTS CO LTD, 2023
Raw material mixing device for rubber tire production that improves mixing efficiency of large particle size raw materials. The device has a mixing box, feeding housings, drive housing, stirring mechanism, mixing cylinder, delivery rod, and crushing mechanism. The stirring blades in the mixing box mix the raw materials. The delivery rod with a spiral blade connects the mixing cylinders. The feeding housings have crushing mechanisms to pulverize large particles before feeding into the mixing box. This pre-crushing step helps break down larger particles for better mixing.
11. Device and Method Utilizing Single-Screw and Twin-Screw Extruders for Homogenous Mixing of High Liquid Content Rubber Compounds
NANJING LVJINREN RUBBER HI TECH CO LTD, NANJING LVJINREN RUBBER HI-TECH CO LTD, 2023
Preparation device and method for self-repairing tire rubber that allows efficient mixing of high liquid content formulations without issues like slippage or inability to discharge from traditional mixers. The device uses a combination of single-screw and twin-screw extruders with optimized screw configurations and temperature control to achieve homogenous mixing of high liquid rubber compounds. The method involves preheating the solid masterbatch in a single-screw extruder to the appropriate viscosity, then feeding it into the twin-screw extruder with liquid PIB injected at the barrel. This allows thorough mixing without slippage or separation issues.
12. Rotating Mixing Chamber with Integrated Scrapers and Stirring Rods for Tire Material Processing
ZHEJIANG SHUNDA MATERIAL TECH CO LTD, ZHEJIANG SHUNDA MATERIAL TECHNOLOGY CO LTD, 2023
A tire mixing machine that prevents waste and speeds up mixing compared to conventional tire mixing machines. The machine has a rotating mixing chamber with feed pipes, discharge pipe, and a motor-driven screw. Scrapers on the chamber walls and stirring rods between the screw and scrapers improve mixing and prevent material buildup. This prevents raw materials from sticking to the chamber walls during mixing, which reduces waste and simplifies cleanup compared to traditional machines where residue remains on the walls. The chamber can be easily emptied and cleaned between batches.
13. Stirring Device with Coordinated Stirring and Mixing Mechanisms for Uniform Raw Material Blending in Aviation Tire Production
QINGDAO SENTURY TIRE CO LTD, 2023
Raw material stirring device for aviation tire production that provides uniform mixing of tire components in the mixing drum to prevent uneven mixing and adhering to the drum walls. The stirring device uses a cooperating stirring mechanism and mixing mechanism to stir the drum interior without dead angles. It has a central stirring shaft driven by a motor. Sliding parts on a plate move in synchronization with cams to move mixing shafts. Scrapers on the mixing shafts prevent material buildup. This allows full drum stirring range for consistent mixing.
14. Tandem Mixer System with Three-Stage Mixing Configuration for Continuous Rubber Compound Production
CONTINENTAL REIFEN DEUTSCHLAND GMBH, 2023
Device and method for efficiently producing a ready-made rubber compound, like tire rubber, by using a tandem mixer setup with three mixers. The first mixer prepares the base rubber compound, the second mixer further mixes and adds components, and the third mixer finishes the compound. This allows continuous production of the final rubber mixture in the third mixer while the other two mixers are cycling. It improves efficiency compared to sequential mixing steps.
15. Dual-Mixer System with Differential Aspect Ratio Rotors for Rubber Compound Processing
CONTINENTAL REIFEN DEUTSCHLAND GMBH, 2023
A device and method for producing rubber compounds with improved filler dispersion and homogeneity in large-scale rubber mixing. The device has two mixers, a top mixer with high aspect ratio rotors and a bottom mixer with lower aspect ratio rotors. This configuration allows efficient mixing with short processing times while maintaining filler dispersion and homogeneity. The top mixer has higher aspect ratio rotor blades for initial mixing, while the bottom mixer with lower aspect ratio rotor blades for final mixing. The aspect ratio ratio between the top and bottom mixers is optimized for filler dispersion and homogeneity. The device can be used in a production line to make rubber compounds like tires.
16. Raw Material Mixing Equipment with Turret Adjustment and Stirring Reversal Mechanisms for Tire Rubber Production
XUZHOU CIMC NEW MATERIAL TECH DEVELOPMENT CO LTD, XUZHOU CIMC NEW MATERIAL TECHNOLOGY DEVELOPMENT CO LTD, 2023
Raw material mixing equipment for making tire rubber that improves production efficiency. The mixing equipment has a base with a collection assembly that contains a mixing assembly and a stirring assembly. The mixing assembly has a turret with an adjusting mechanism and a replacement mechanism. The stirring assembly has a support frame with a feeding trough and a reversing mechanism. The collection assembly also has a collecting groove. The swinging mechanism moves the suction head. The replacement mechanism allows turret ball size changes. The reversing mechanism moves the stirring columns. The base has a swing motor and gear train. The base also has a slide plate and gear train for turret height adjustment. The collection assembly has an adjusting motor, top cover, and heating plate.
17. Rubber Tire Production Feeding Device with Integrated Mixing, Crushing, and Pushing Mechanisms
HUAIAN CHANGFENG DYNAMO ELECTRIC EQUIPMENT CO LTD, HUAIAN CHANGFENG DYNAMO-ELECTRIC EQUIPMENT CO LTD, 2023
High-efficiency feeding device for rubber tire production that improves raw material mixing for better tire quality. The device has a box with a mixing mechanism, crushing device, pushing mechanism, and partition. The mixing mechanism has a motor, turntable, mixing plate, and positioning rod. The pushing mechanism has an electric push rod, discharge frame, and sealing plate. This setup allows efficient mixing, crushing, and pushing of the rubber materials inside the box to ensure homogeneous mixing before feeding to the next stage of tire production.
18. Rubber Mixing Process Utilizing Banbury Mixer and Parallel Open Mills with Reduced Vulcanizing Agent Loss
HUBEI LINGLONG TIRE CO LTD, SHANDONG LINGLONG TYRE CO LTD, 2023
A rubber mixing process for tires that reduces loss of vulcanizing agents during mixing to improve tire quality. The process involves using a banbury mixer followed by multiple parallel open mills for supplementary mixing. The banbury mixer initially mixes the rubber, then evenly divides the batch between the parallel open mills for further mixing. This longer supplementary mixing compensates for the reduced rubber quantity in each mill compared to fewer parallel mills, preventing quality fluctuations and loss of volatile additives.
19. Rubber Mixing Machine with Vertical Unloading Mechanism and Adjustable Screw Rod Assembly
SUQIAN BANGLU PROT ARTICLES CO LTD, SUQIAN BANGLU PROTECTION ARTICLES CO LTD, 2022
A rubber mixing and stirring machine with vertical unloading to improve efficiency and reduce labor compared to traditional horizontal unloading. The machine has a mixing drum, screw rod, adjustment assembly, and unloading assembly. The adjustment assembly allows vertical reciprocation of the screw rod to mix the rubber. The unloading assembly has vertical slides, racks, and springs to lift and push the mixed rubber out of the drum. The vertical unloading eliminates the need for manual lifting and reduces labor compared to horizontal unloading. The adjustment assembly allows vertical mixing without lifting the entire drum.
20. Device with Dual Mixing Chambers and Transfer Mechanism for Sequential Rubber and Additive Processing
CONTINENTAL REIFEN DEUTSCHLAND GMBH, 2022
Device and method for producing rubber mixtures used in tire manufacturing that improves efficiency and processability. The device has two mixing chambers connected by a transfer device. One chamber mixes rubber and filler, the other chamber mixes additives like zinc oxide and diamines. Solid additives are fed directly into the second chamber. This allows separate optimization of base rubber and additive mixing. The transfer device moves the base rubber into the second chamber for final mixing. The method involves separately mixing the rubber/filler and additives in each chamber, then transferring the rubber to the additive chamber for final mixing. This enables better control over the rubber properties and additive distribution compared to mixing everything together.
Get Full Report
Access our comprehensive collection of 45 documents related to this technology
Identify Key Areas of Innovation in 2025
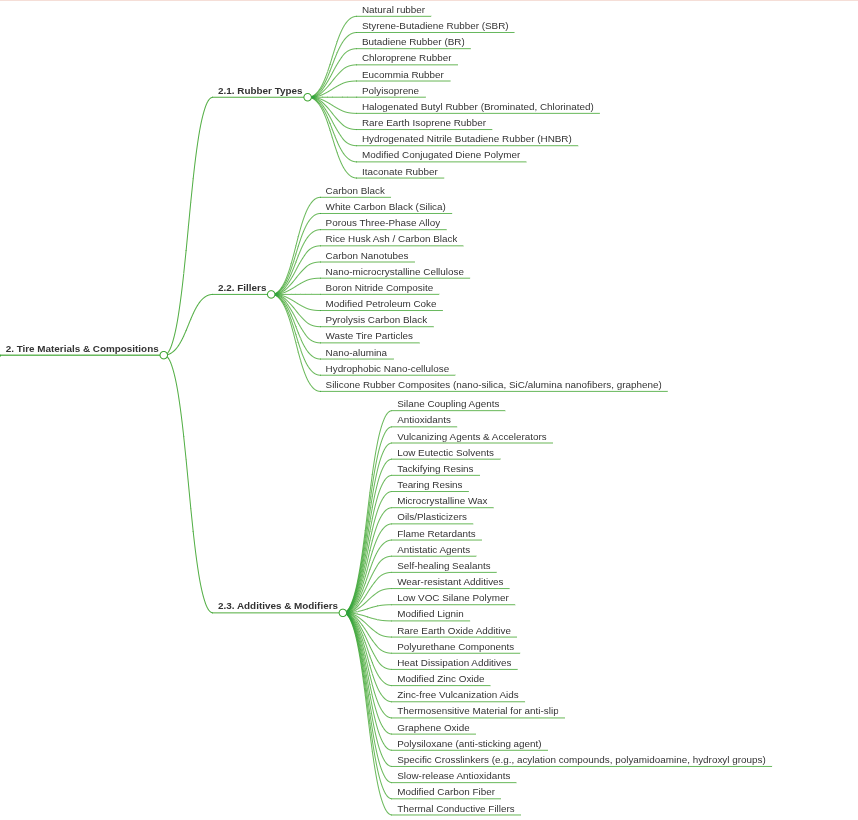