Silica Fillers in Tire Compound Development
Modern tire manufacturing must balance competing performance demands while meeting increasingly stringent efficiency standards. Current passenger vehicle tires contain precise blends of silica fillers with specific surface areas ranging from 60 to over 300 m²/g, interacting with complex rubber matrices to influence critical parameters like rolling resistance, wet grip, and wear characteristics.
The fundamental challenge lies in optimizing silica-rubber interactions at the molecular level while maintaining processability and cost-effectiveness at production scale.
This page brings together solutions from recent research—including dual-silica systems with functionalized and unfunctionalized particles, targeted coupling agent ratios, and rubber modifications that enhance filler dispersion. These and other approaches demonstrate how manufacturers are achieving previously incompatible performance targets through precise control of silica-rubber chemistry.
1. Anode Active Material Comprising Recycled Waste Glass-Derived Silicon with Metal-Oxygen-Silicon Bond Structure
LK TECHNOLOGY CO LTD, 2025
Anode active material for lithium-ion batteries made from recycled waste glass that contains silica and metal oxides. The material is produced by reducing waste glass at temperatures around 300°C to create silicon particles with a unique bond structure containing metal-oxygen-silicon bonds. This bonding helps prevent the silicon from expanding and delaminating during battery cycling, which is a major issue with pure silicon anodes. The recycled waste glass source also reduces costs and environmental impact compared to high-temperature silicon production methods.
2. Engineering Physicochemical Properties of Nanofillers for High-Performance Composite Solid-State Electrolytes in Lithium Metal Batteries
heming luo, jie yang, yanfei yang - American Chemical Society, 2025
High-performance organic-inorganic composite solid-state electrolytes (OICSEs) are pivotal for advancing lithium metal batteries (SSLMBs), offering the potential enhanced safety and higher energy density compared to conventional liquid electrolytes. This study systematically explores influence of nanofiller physicochemical properties (particle size, specific surface area, energy) on electrochemical performance polyethylene oxide (PEO)-based OICSEs. By optimizing these parameters, we developed a PEO/superhydrophobic SiO2 OICSE incorporating low nanofillers with an optimized particle size 7 nm high area 300 m2 g-1. engineered demonstrated exceptional ionic conductivity (4.3 10-4 S cm-1 at 30 C), Li-ion transference number (0.5), superior stability (up 5.1 V vs Li+/Li). When integrated into Li|LiFePO4 battery, battery exhibited outstanding rate 5.0 C) remarkable cycling (93.8% capacity retention after 500 cycles C) maintained stable even 0 C. These improvements attributed transport pathways solid/solid interfacial stability. The superhydrophobic presents scalable commercially v... Read More
3. Cross-Linked Polymer Binder Composition with Specific Monomers and Silica Anti-Caking Agent for Rechargeable Battery Anodes
ARLANXEO DEUTSCHLAND GMBH, 2025
Binder composition for rechargeable battery anodes that improves adhesion, coating uniformity, and performance. The binder is a cross-linked polymer obtained by grinding. It contains specific monomers (1,3 butadiene, (hydroxyethyl)methacrylate, trimethylolpropane trimethacrylate) with a particle size range of 180-450 μm. The binder also has a silica anti-caking agent. This composition provides better adhesion to the anode current collector compared to spray-dried binders. It also enables extrusion-based electrode processing for improved anode coating uniformity.
4. Battery Pack with Integrated Cell Enclosure and Filler Material for Thermal and Electrical Isolation
LG ENERGY SOLUTION LTD, 2025
Battery pack design with reduced components, improved energy density, and enhanced safety for applications like electric vehicles, drones, and portable electronics. The battery pack has a single enclosure that houses the battery cells directly against the inner wall without an intermediate module case. Filler material surrounds the cell sides to prevent electrical shorting and thermal runaway propagation. This simplifies the pack structure, reduces cost, and increases energy density compared to separate cell and pack housings. The filler also blocks heat transfer between cells to mitigate thermal runaway chain reactions.
5. Method for Increasing Bulk Density of Low Density Materials via Liquid-Assisted Homogenization and Evaporation
ARKEMA INC, 2025
Method to increase the bulk density of low bulk density materials like fumed silica without forming agglomerates, grit, or altering absorption properties. The method involves gently mixing the low bulk density material with a liquid, like water or acid, to create a homogenous, densified material that retains its powdery form and dispersibility. The liquid is evaporated to leave behind the denser product. This avoids issues like over-densification, agglomeration, and reduced dispersion when using mechanical methods.
6. Silica Precipitation Control via Polycation-Polyanion Phase Separation Mechanism
YEDA RESEARCH AND DEVELOPMENT CO LTD, 2025
Controlling the morphology of precipitated silica by using polycation-polyanion phase separation. The process involves mixing oppositely charged polymer ions with silicon sources to induce silicification. The polymer dense phase formed by phase separation provides a distinct environment for silica precipitation. This enables regulating the silica morphology by tuning the polymer concentration and ionic strength.
7. Rubber Composition with Dual Silica Filler System Featuring Distinct Surface Areas
Bridgestone Europe NV/SA [BE/BE], 2024
Rubber compositions for vehicle tires that balance wet performance, rolling resistance, and wear resistance. The compositions contain a filler system with two different silicas. One is a surface-functionalized silica with specific surface areas of 250-310 m2/g and 230-285 m2/g. The other is an unfunctionalized silica with specific surface areas of 60-120 m2/g and 55-105 m2/g. This blend of silicas improves wet grip, rolling resistance, and wear resistance compared to similar filler systems using only one type of silica.
8. Rubber Mixture Comprising Specific Styrene-Butadiene Rubber, Silica Filler, and Thioacetate or Thiopropyl Silane
Continental Reifen Deutschland GmbH, 2024
Rubber mixture for tire treads with improved properties like rolling resistance, grip, and tear resistance. The mixture contains a specific type of styrene-butadiene rubber (SSBR) with a glass transition temperature between -35°C and -85°C. This rubber is combined with silica filler and a specific amount of a silane. The silane has a formula with a thioacetate or thiopropyl group (X) bonded to a silicon atom (Si) and a propyl group (R) with a siloxane (S) bond between them. The silane amount is 1-30 parts per hundred parts of rubber (phr). The mixture can be used in tire treads for vehicles to provide better balance of properties like rolling resistance, grip, and tear resistance compared to conventional tire tread compositions.
9. Rubber Composition with Dual Solution-Polymerized Styrene-Butadiene Rubbers and Dual Silica Fillers for Tire Applications
Apollo Tyres Global R&D B.V., 2024
Rubber composition for tires that provides improved rolling resistance, wet grip, and handling compared to conventional tire rubbers. The composition uses a blend of natural rubber, polybutadiene rubber, and two different solution-polymerized styrene-butadiene rubbers with specific glass transition temperatures. It also contains two silicas with different surface areas, along with coupling agents. The composition enables optimizing winter performance without sacrificing rolling resistance, by balancing silica-filler interactions and silanization. The cross-linkable composition can be used in tire treads, and the cross-linked tire has improved properties like rolling resistance, wet grip, and handling.
10. Tire Rubber Composition with Isoprene-Based and Modified Styrene-Butadiene Rubber, Hydrogenated Resin, Silica, and Carbon Black
BRIDGESTONE CORPORATION, 2024
Tire rubber composition for improved wet grip and fuel efficiency. It contains a specific combination of rubber components, hydrogenated resin, silica, and carbon black. The rubber components are isoprene-based and modified styrene-butadiene rubber with high styrene content (30% or more). The hydrogenated resin has a high softening point (100°C or above) and moderate molecular weight (1200-1600 g/mol). The silica loading is 50-100% of the total filler content. This composition balance provides optimal wet grip and rolling resistance.
11. Rubber Composition for Tire Treads with Specific Diene Rubber, Silica, Silane Coupling Agent, Fatty Acid Metal Salt, and Alkylsilane
The Yokohama Rubber Co., Ltd., 2024
Rubber composition for tire treads that provides a balance of low rolling resistance, good wet traction, and wear resistance. The composition contains specific diene rubber, silica, a silane coupling agent, a fatty acid metal salt, and an alkylsilane. The diene rubber has a high percentage of a specific conjugated diene rubber formed by reacting a siloxane with a diene-based polymer. This improves silica dispersion for rolling resistance. The alkylsilane plasticizer suppresses silica aggregation. The fatty acid salt further aids silica dispersion. The blend ratio of these components provides a balance of rolling resistance, wet traction, and wear resistance.
12. Rubber Compound for Tire Treads with Functionalized Butadiene Rubber and Liquid-Modified Diene Polymer
Continental Reifen Deutschland GmbH, 2024
Rubber compound for tire treads that improves wet grip, rolling resistance, and profile stiffness. The compound contains a functionalized butadiene rubber, a liquid-modified diene polymer, a polar filler like silica, and a diene rubber. The functionalized butadiene rubber interacts with the polar filler. The modified diene polymer has a backbone modification that also allows interaction with the polar filler. This filler-rubber interaction improves wet grip and rolling resistance while maintaining stiffness.
13. Tire Rubber Composition with Isoprene Skeleton, Modified Styrene-Butadiene Rubber, Hydrogenated Resin, Silica, and Carbon Black
BRIDGESTONE CORPORATION, 2024
Tire rubber composition that provides improved wet grip and fuel efficiency. The composition contains an isoprene skeleton rubber, a modified styrene-butadiene rubber with 15% or less bound styrene, hydrogenated resin with a softening point over 100°C and Mw of 1200-1600, silica with 50-100% filler content, and carbon black. This balance of components enables optimized wet traction and reduced rolling resistance.
14. Rubber Composition with Modified and Unmodified Styrene-Butadiene Rubbers for Enhanced Filler Dispersion and Performance Balance
BRIDGESTONE CORPORATION, 2024
Rubber composition for tires that balances wet grip, fuel efficiency, and wear resistance. The composition contains a styrene-butadiene rubber (A) with a modified terminal group, and an unmodified styrene-butadiene rubber (B) with a higher glass transition temperature. The modified rubber (A) is produced by modifying an active polymer with a compound containing a silicon atom bonded to an amine group. This improves dispersion of fillers like silica for better wet grip and wear resistance. The unmodified rubber (B) provides the balance of fuel efficiency.
15. Rubber Composition with Modified Styrene-Butadiene Rubber, Silica, Thermoplastic Resin, and Silane Coupling Agent
The Yokohama Rubber Co., LTD., 2024
Rubber composition for tires with improved steering stability, wet performance, and low rolling resistance over a wide temperature range. The composition contains specific amounts of modified styrene-butadiene rubber, silica, thermoplastic resin, and a silane coupling agent. The modified styrene-butadiene rubber has a vinyl content of 9-45 mol% and a glass transition temperature of -45°C or lower, with terminal groups containing siloxane or amine functionalities. The composition also has silica, thermoplastic resin, and a silane coupling agent in specific ranges.
16. Tire Tread Rubber Composition with Diene Elastomer, High Surface Area Silica, Microsilica, and Silane Coupling Agent
CIE GENERALE DES ETABLISSEMENTS MICHELIN, COMPAGNIE GENERALE DES ETABLISSEMENTS MICHELIN, 2023
Rubber composition for tire treads that provides improved wet grip and rolling resistance compared to conventional tire rubber compositions. The composition contains a diene elastomer, a high surface area silica (Tl > 100 m2/g) as the main reinforcing filler, a microsilica (T2 < 50 m2/g) as a secondary filler, a silane coupling agent, and a crosslinking system. The microsilica in addition to the high surface area silica enhances wet grip and reduces rolling resistance compared to using just the high surface area silica.
17. Tire Tread Rubber Composition with White Carbon Black, Silica Fume, and High-Temperature Silane Coupling Agent
HANGZHOU HAICHAO RUBBER CO LTD, ZHONGCE RUBBER GROUP CO LTD, 2023
Low-rolling-resistance high-wear resistance tire tread rubber composition that can improve the dispersion of white carbon black in tread rubber and the processability of rubber materials by using white carbon black and silica fume as fillers and selecting a silane coupling agent capable of mixing at high temperature. The composition includes carbon black and white carbon black as fillers, and selecting a silane coupling agent capable of mixing at high temperature.
18. Pneumatic Tire Tread Rubber Incorporating Specific Silane Coupling Agent with Defined Alkyl and Alkoxy Groups
2023
Pneumatic tire with improved durability and wear resistance by using a specific silane coupling agent in the tread rubber. The coupling agent is represented by a formula with a specific alkyl group, alkoxy group, and substitution on the silicon atom. This coupling agent provides enhanced durability and wear resistance when used in tire tread rubber containing silica as a reinforcing filler. The formula is: (R1)3Si(OR3)x, where R1 is an alkyl group with 5 to 20 carbon atoms, n is 1 to 3, and x is 1 to 5.
19. Rubber Composition with Isoprene Skeleton, Styrene-Butadiene Rubber, Silica Filler, and Thiol-Group Silane Coupling Agent
BRIDGESTONE CORP, 2023
Rubber composition that is excellent in wet grip performance and low rolling resistance. The composition includes an isoprene skeleton rubber and a styrene-butadiene rubber, the filler contains at least silica, the silane coupling agent has a thiol group, the content of the silane coupling agent is 1 part by mass or more and 10.5 parts by mass or less with respect to 100 parts by mass of the rubber component, and the content of the fatty acid metal salt is 0.1 part by mass with respect to 100 parts by mass of the rubber component.
20. Tire Tread Composition with Silane-Modified Diene Rubber and Silica Filler for Enhanced Dispersion and Mechanical Properties
GOODYEAR TIRE & RUBBER, THE GOODYEAR TIRE & RUBBER CO, 2023
Tire tread composition with improved properties like reduced rolling resistance, stiffness, and tear without compromising other performance metrics like traction, wear, and tensile strength. The composition uses a specific combination of silane coupling agents along with a diene rubber and silica filler. The silane agents include bis(dialkylalkoxysilyl-alkyl) polysulfide coupling agents. The agents improve silica dispersion and compatibility in the rubber matrix. This leads to better processing, reduced agglomeration, and enhanced rubber properties like hysteresis and stiffness without impacting tear and strength.
Get Full Report
Access our comprehensive collection of 131 documents related to this technology
Identify Key Areas of Innovation in 2025
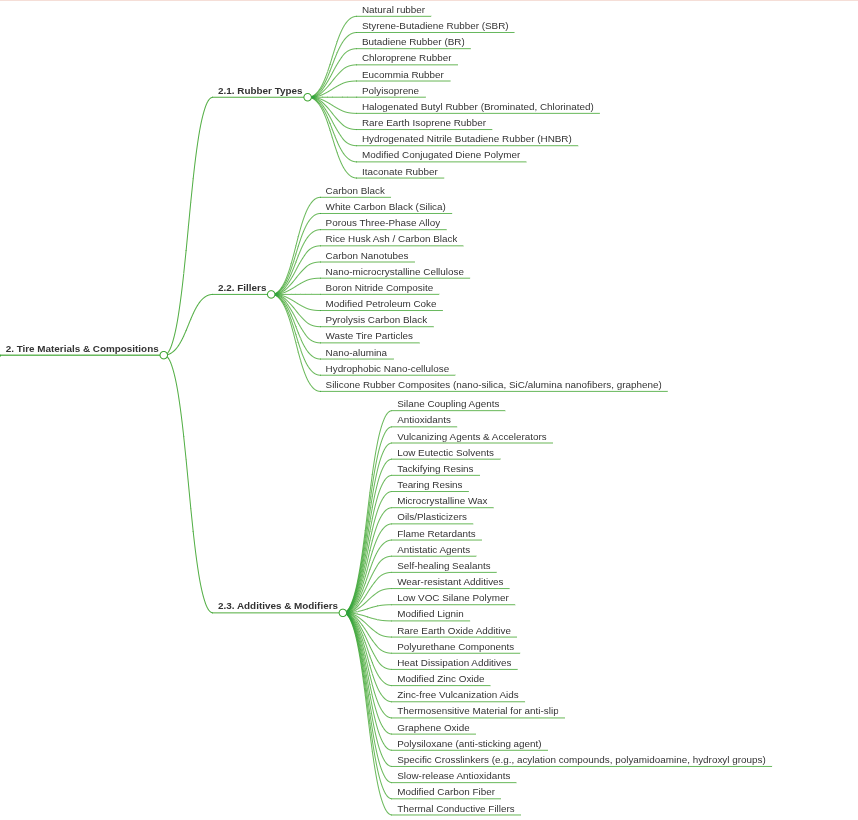