Cryogenic Grinding in Tire Recycling
Recycling end-of-life tires presents significant material processing challenges. Traditional ambient grinding methods generate heat that causes rubber degradation, while mechanical shredding produces irregular particles with limited reuse potential. Current industrial processes require substantial energy input and achieve particle size reduction ratios of only 10:1 to 15:1, with significant variation in output quality.
The fundamental challenge lies in achieving consistent, fine particle sizes while maintaining the material properties of the rubber compound and managing the energy costs of cryogenic cooling.
This page brings together solutions from recent research—including multi-stage cooling processes, controlled particle size reduction techniques, cold energy recovery systems, and optimized grinding parameters. These and other approaches focus on producing high-quality rubber powder suitable for direct reuse in manufacturing while maximizing process efficiency.
1. Material recovery from waste rubber tyres and their geoenvironmental utilisation: a review
prithvendra singh, myint win bo, engchoon leong - ICE Publishing, 2025
The escalating environmental challenges posed by waste rubber tyres (WRTs) necessitate innovative solutions to address their detrimental effects on the geoenvironment. Thus, knowledge about recent advancements in material recovery from WRTs, emphasising utilisation within framework of United Nations Sustainable Development Goals (SDGs) and circular economy principles, is need hour. Keeping this mind, various techniques generally used for recovery, viz., ambient, cryogenic, waterjet, so on, which unveil approaches reclaiming valuable resources (viz., recycled rubber, textiles, steel wires, etc.) WRTs devulcanisation physical, chemical, microbial) are elaborated paper. In parallel, paper explores recovered materials, highlighting application geotechnical geoenvironmental engineering development projects while addressing necessary precautions associated risks/concerns. This incorporates principles into focuses achieving SDGs promoting resource efficiency minimising impact.
2. Cryogenic Freezing and Crushing Process for Tire Recycling
DAVID MAX SHIN, 2024
A pollution-free method for recycling tires that involves cryogenic freezing, crushing, and sieving instead of shredding and high-temperature treatment. The method involves shredding tires, spraying them with water, filtering, drying, freezing, crushing, separating metal fibers, crushing again, sieving, and screening to produce clean tire particles. The cryogenic freezing step reduces odor, dust, and pollution compared to high-temperature processing.
3. Cryogenic Tire Recycling Method with Sequential Shredding, Freezing, and Separation Steps
David Max Shin, 2023
Pollution-free tire recycling method using cryogenic freezing to recycle tires without generating high pollution levels. The process involves shredding tires, spraying them with water, blow-drying, freezing to -150 to -300°C, crushing, separating metal fibers, further crushing, cyclone separating, and screening to produce fine tire particles. This cryogenic recycling reduces odor, dust, and pollution compared to high-heat recycling.
4. Multi-Stage Freezing and Grinding System for Pulverizing Waste Tires into Rubber Powder
ZHUHAI QIANDING TECH CO LTD, ZHUHAI QIANDING TECHNOLOGY CO LTD, 2022
A waste tire recycling system that pulverizes tires into rubber powder without pollution. The system involves a series of crushing, washing, freezing, and grinding steps. The tire is first crushed into fragments. The fragments are washed and then crushed again to make smaller fragments. These fragments are then frozen and ground into primary powder. The primary powder is split and further frozen and ground into secondary powder. This multi-stage freezing and grinding process allows efficient pulverization of tires into rubber powder without generating pollutants like dioxins.
5. Cold Energy Recovery System with Insulated Chambers and Pipes for Cryogenic Pulverization of Tires and Plastics
SHANGHAI JIANTIAN NEW ENERGY TECH CO LTD, SHANGHAI JIANTIAN NEW ENERGY TECHNOLOGY CO LTD, 2022
A cold energy recovery system for recycling waste tires and plastics into powder using liquid nitrogen. The system has a material tank with chambers, a feeding pipe, a liquid nitrogen chamber, a powder tank, and pipes connecting them. Nitrogen from the liquid nitrogen chamber is pumped into the feeding pipe to cool the material. The cooled material goes to the liquid nitrogen chamber for further cooling. Nitrogen from there is pumped into the feeding pipe to cool more material. The powder produced in the liquid nitrogen chamber is pumped to the powder tank. This recycles and reuses the nitrogen's cold energy to reduce waste. The chambers, pipes, and tanks are insulated to further minimize cold energy loss.
6. Refrigerated Airflow Tire Crushing Device with Pre-Cooling, Crushing, and Heat Exchange Chambers
HAOYI HUAIAN XUYI NEW MATERIALS TECH CO LTD, HAOYI NEW MATERIALS TECHNOLOGY CO LTD, 2020
A device for crushing old tires using refrigerated airflow that freezes and crushes tires in a uniform and efficient manner. The device has a crushing chamber, pre-cooling chamber, and heat exchange chamber. The crushing chamber has a rotating shaft with connecting rods and a top plate for tire crushing. The pre-cooling chamber has a refrigerator and the heat exchange chamber has an exhaust pipe. Air compressor cools and pressurizes air, which is sprayed downward by the first branch pipe and upward by the second branch pipe to freeze the tires. The reversing airflow and high pressure crush the frozen tires. The uniform freezing prevents uneven crushing. The heat exchange recovers refrigerant energy.
7. Two-Stage Cryogenic Grinding Process for Producing Fine Rubber Powder from Waste Tires
Putian Haifa New Energy Co., Ltd., PUTIAN HAIFA NEW ENERGY CO LTD, 2020
A method to produce high-quality rubber powder from waste tires for use in tire treads. The method involves cryogenic grinding of the tire rubber at sub-glass transition temperatures to achieve small particle sizes. It uses a two-stage nitrogen cooling process with normal and low temperatures. This produces a high proportion of fine rubber powder with improved properties for tire treads compared to conventional grinding. The cryogenic grinding prevents heat buildup and stickiness, allowing finer sizes. The resulting powder can be used in tire treads for better performance and sustainability.
8. Vibratory Feeder and Tumbling Pre-Cooling Chamber for Rubber Particle Size Reduction
QINGDAO UNIVERSITY, SHANDONG GUOSHUN CONSTRUCTION GROUP CO LTD, UNIV QINGDAO, 2020
Device to prepare fine rubber particles from waste tires that avoids the limitations of existing methods. The device uses a vibratory feeder to drop the crushed tire blocks into a pre-cooling chamber where they jump and tumble. This motion further breaks the rubber as it rolls down and exits through a chute. The chamber is cooled by a freezer to solidify the rubber. The freezing chamber has an air inlet and outlet to circulate cold air. The vibratory feeder and tumbling motion in the pre-cooling chamber improve particle size reduction compared to just freezing the rubber.
9. Low-Temperature Grinding Apparatus with Closed-Loop Liquid Nitrogen Cooling and Adjustable Pressure Crushing for Waste Tire Rubber Particulation
UNIV ZHEJIANG TECHNOLOGY, ZHEJIANG UNIVERSITY OF TECHNOLOGY, 2020
Low-temperature grinding equipment for recycling waste tires into fine rubber particles. The equipment uses a closed-loop cooling system with liquid nitrogen to precool and then cool the tire rubber before grinding. A low-temperature crushing device with adjustable pressure applies force between grinding discs at low temperatures to prevent carbonization and oxidation. The equipment has a feeder, cooling boxes, and a controller to optimize grinding parameters for customized particle size.
10. Production Line and Method for High-Precision Rubber Powder via Combined Normal and Cryogenic Grinding
China Gezhouba Group Green Technology Co., Ltd., CHINA GEZHOUBA GROUP LVYUAN TECHNOLOGY CO LTD, 2019
A production line and method for preparing high-precision rubber powder from waste rubber that enables efficient and scalable production of ultra-fine rubber powder for applications like thermoplastic elastomers. The method involves a combination of normal temperature grinding and freezing grinding to brittleize the rubber. The production line includes stages like crushing, granulation, milling, and freezing grinding. The freezing grinding is performed below the rubber embrittlement temperature using separate cryogenic subsystems. This allows the rubber to be frozen and brittle enough for fine grinding. The line also includes steps like metal separation, fiber removal, and drying.
11. Multi-Stage Rubber Powder Crushing Device with Progressive Screening and Cryogenic Grinding
Mianyang Ruiyang New Material Technology Development Co., Ltd., 2019
Multi-stage rubber powder crushing method and device that enables efficient recycling of rubber waste by crushing and grinding it into powder. The method involves using multiple stages of crushing devices with progressively finer screens to reduce the rubber particle size. The crushing sequence starts with a rough processing mechanism, then a semi-finishing device, followed by a freezing stage to cool the rubber below its glass transition temperature. The frozen rubber is then ground to a powder in a finishing mechanism. The powder is further ground and screened to separate out oversized pieces. This multi-stage process allows effective recycling of rubber by breaking it down into small particles suitable for reuse.
12. Recycling System for Waste Tires Incorporating Transverse and Longitudinal Blade Cutting with Liquid Nitrogen Cooling
Hao Lu, 2019
A recycling system for waste tires from electric vehicles that uses cutting, cooling, crushing, screening, and sorting steps to convert the tires into usable rubber powder. The system involves a cutting device with transverse and longitudinal blades to shape the tires. Then, the tires are rapidly cooled using liquid nitrogen to make them brittle. The cooled pieces are crushed, ground, and screened to separate the rubber powder from impurities.
13. Cryogenic Grinding and Screening System for Micronized Powder Production from Heterogeneous Materials with PID-Controlled Warming and Vibrating Fiber Removal
LEHIGH TECHNOLOGIES INC, 2019
Producing micronized powders like rubber powder from heterogeneous materials like used tires in a predictable particle size range and concentration that allows incorporation into other applications regardless of the infeed material. The method involves cryogenic grinding, screening, warming, fiber and metal removal, and accumulation steps. Warming the particles using a PID loop with recirculation to improve efficiency. A vibrating screener removes fibers while letting the micronized powder pass. Accumulation decouples grinding and screening rates.
14. Rubber Powder Production Device with Multi-Stage Low Temperature Crushing and Particle Recovery System
CHANGAN UNIV, CHANGAN UNIVERSITY, Chang'an University, 2017
Rubber powder production device for recycling waste tires that improves quality, efficiency and reduces costs compared to room temperature crushing. The device uses low temperature crushing stages to prevent rubber degradation. It has conveyors, crushers, screens and a particle recovery system. The first crusher is below the feed conveyor, the second crusher is above the discharge conveyor, and the screens are between. This allows multiple crushing stages at lower temperatures. The particle recovery system captures fines from the screens to recycle them. The low temperature crushing prevents rubber degradation and improves powder quality. The multi-stage crushing and screening allows flexible particle size control.
15. Vacuum-Assisted Cryogenic Crushing Process for Fine Rubber Powder Production
TIANJIN MINGJI JINTAI RUBBER PLASTIC PROC CO LTD, TIANJIN MINGJI JINTAI RUBBER PLASTIC PROCESSING CO LTD, 2017
Low temperature processing of rubber powder to produce fine powder from waste tires at low energy consumption. The method involves freezing the 60-120 mesh rubber powder at very low temperatures (-60 to -10°C) in a vacuum chamber for 3-5 minutes. The frozen powder is then crushed into the desired size using a rubber crusher in the same low temperature environment. This allows efficient and energy-saving production of fine rubber powder from waste tires.
16. Cryogenic Pulverization Method for Scrap Tire Rubber Using Extended Freezing and Grinding at -180°C
TIANJIN MINGJI JINTAI RUBBER AND PLASTIC PRODUCT PROC CO LTD, TIANJIN MINGJI JINTAI RUBBER AND PLASTIC PRODUCT PROCESSING CO LTD, 2016
A low-cost, low-power, and efficient method to process scrap tire rubber into a modified powder. The method involves freezing the scrap tire rubber at -180°C for 24 hours, then pulverizing it into powder using a cryogenic grinder at -180°C. This freezing and pulverization process improves the performance of the powder compared to room temperature pulverization alone. The frozen rubber is easier to fracture into smaller particles, resulting in a powder with better properties for rubber products.
17. Waste Tire Recycling Process with Cryogenic Grinding and Impurity Separation
HE ZHIBIN, 2016
A recycling process for waste tires that cools and grinds the rubber into powder without incineration. The process involves cutting, grinding, separating impurities, screening, cooling, and cleaning the rubber particles. It uses machines like crushers, screens, cyclones, separators, shakers, and mills. The rubber is pre-cut, then quenched and ground into smaller pieces. Impurities are separated and classified. The rubber is cooled by grinding in liquid nitrogen mills. Powder screening removes fibers and dust. This produces uniform, cooled rubber powder for reuse. The process avoids incineration emissions.
18. Cryogenic Tire Recycling System with Liquid Nitrogen Cooling and Impurity Removal
HE ZHIBIN, 2016
A system for recycling waste tires into powder using liquid nitrogen to break them down without burning or polluting. The system involves crushing the tires, cooling them with liquid nitrogen, and then grinding them into powder. The liquid nitrogen cooling helps make the rubber brittle for easier grinding into powder. The cooled rubber is then purified to remove impurities before final grinding. This allows clean, recyclable rubber powder to be produced from waste tires without incineration or other pollution.
19. Segmented Cryogenic Comminution System with Dual-Stage Crushing and Temperature-Controlled Water Cooling
OHERO GLOBAL CO LTD, 2016
A segmented cryogenic comminution system for efficiently and cost-effectively pulverizing waste rubber into powder without using expensive liquefied gases like nitrogen. The system uses a two-stage crushing process with temperature control between stages. The first stage crusher breaks the rubber into scraps while a water cooling device lowers the temperature below a critical point. This prevents softening during the second stage crushing. The cooled scraps are then fed to the second stage crusher for final pulverization. By controlling the temperature, the system eliminates the need for large volumes of expensive liquefied gases like nitrogen to absorb heat during crushing.
20. Scrap Tire Processing System with Liquid Nitrogen Cooling and Multi-Stage Purification
HE ZHIBIN, 2016
A scrap tire production system using liquid nitrogen to crush tires into high purity powder without pollution. The system involves a multi-step process including crushing, cooling, purification, and milling. Tires are crushed twice with screens to remove impurities. They are then cooled with liquid nitrogen to brittleness. Further purification stages separate impurities. Finally, the nitrogen-cooled particles are milled into powder. The liquid nitrogen cooling prevents pollution during crushing. It also allows efficient granulation and milling. The purification stages ensure high quality powder.
Get Full Report
Access our comprehensive collection of 47 documents related to this technology
Identify Key Areas of Innovation in 2025
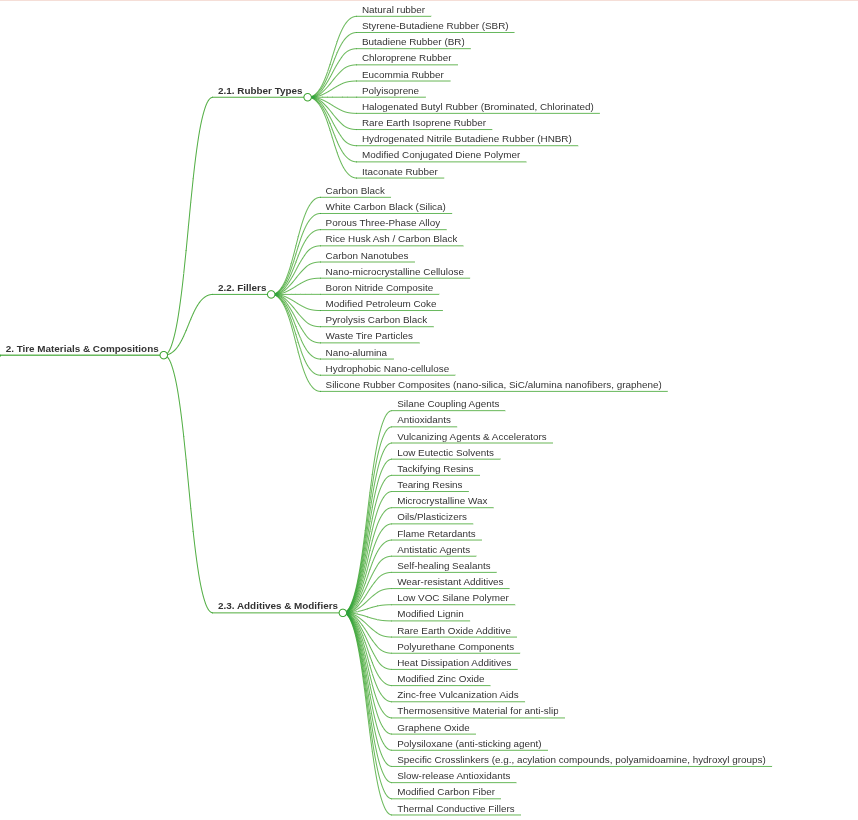