Tire Behavior Simulation in Dynamic Conditions
Modern tire development requires precise understanding of tire behavior across diverse conditions, with loading forces ranging from 2-15 kN and contact patch pressures varying between 200-350 kPa. Traditional testing methods struggle to replicate the complex interactions between tire deformation, surface conditions, and dynamic forces that occur during real-world driving scenarios.
The fundamental challenge lies in accurately simulating the non-linear relationship between tire forces, road conditions, and vehicle dynamics while maintaining test repeatability and measurement precision.
This page brings together solutions from recent research—including real-time force computation methods, multi-roll testing devices, virtual load history generation, and controlled environment testing chambers. These and other approaches enable developers to evaluate tire performance through reproducible testing protocols that closely mirror real-world conditions.
1. Finite Element Simulation Method for Tire Longitudinal Slip Characteristics with Variable Slip Rates and Fitted Friction Model
HANGZHOU HAICHAO RUBBER CO LTD, ZHONGCE RUBBER GROUP CO LTD, 2024
Simulating tire longitudinal slip characteristics using finite element analysis to efficiently and accurately determine tire forces and moments when sliding on the road. The simulation involves steps like finite element pretreatment, 2D inflation analysis, 3D loading modeling, steady state simulation, and dynamic slip simulation. It uses explicit analysis with customizable slip rates and a fitted friction model from rubber testing to accurately replicate tire longitudinal behavior. This allows tire dynamics modeling and optimization without physical testing.
2. Simulation Method for Calculating Tire Sidewall Fatigue Life Under Flexural Deformation
ZHONGCE RUBBER GROUP CO LTD, 2024
A method to simulate and calculate fatigue life of tire sidewalls under flexural deformation. The method involves modeling tire sidewall flexure using simulation software like Abaqus. The simulation captures different deformation amounts and the entire flexure process. Fatigue life calculation is done using software like Endurica. The simulation output provides parameters like stress, strain, Mises stress, fatigue life for analyzing tire sidewall flexural fatigue.
3. Method for Predicting Tire Longitudinal Slip Characteristics Using Normalized Reference Tire Data
HANGZHOU HAICHAO RUBBER CO LTD, ZHONGCE RUBBER GROUP CO LTD, 2024
A method for predicting tire longitudinal slip characteristics with lower cost and higher efficiency compared to physical testing or finite element simulation. The method involves using a reference tire with similar size to predict the longitudinal force versus slip rate curve for a target tire. It normalizes the longitudinal force data of the reference tire, models the normalized curve, and then uses the longitudinal stiffness and friction coefficients from the target tire in the theoretical model to predict its longitudinal force versus slip rate.
4. Method for Predicting Tire Cornering Characteristics Using Normalized Reference Tire Data and Target Tire Properties
HANGZHOU HAICHAO RUBBER CO LTD, ZHONGCE RUBBER GROUP CO LTD, 2024
A method to predict tire cornering characteristics without physical testing. The method involves modeling and normalizing tire side slip data from a reference tire, then applying target tire properties to generate predicted cornering behavior. It allows estimating tire cornering forces and moments without full finite element analysis or physical testing, using reference tire data. The steps are: 1) Select a reference tire with similar size to the target tire. 2) Normalize the lateral force and self-aligning torque data from the reference tire. 3) Model the normalized curves to obtain functions. 4) Substitute the target tire's sidewall stiffness and lateral dynamic friction coefficient into the side slip prediction model. 5) Use the modeled functions with the target tire properties to predict the normalized lateral force and self-aligning torque.
5. Linear Simulation Method for Tire Unsteady Cornering Using High-Precision Exponential Function Approximation in Brush Theory Model
CHINA FAW GROUP CORP, 2024
Linear simulation method for tire unsteady cornering characteristics that improves accuracy over existing methods. The simulation involves simplifying the brush theory model of tire unsteady cornering using a high-precision approximation of an exponential function. This simplified model is then applied to linear simulation of tire unsteady cornering using spatial differential equations and characteristic parameters like ground contact length, stiffness, and width. This improves simulation accuracy compared to simplifying the brush theory directly.
6. Vehicle Dynamics Model Incorporating Real-World Trained Tire Data Model for Enhanced Force Estimation
HUAWEI TECH CO LTD, HUAWEI TECHNOLOGIES CO LTD, 2024
Constructing a vehicle dynamics model that accurately reflects the dynamic performance of a vehicle. The method involves introducing a tire data model that is trained using real-world driving data. The tire data model generates tire force estimates. These are fused with forces calculated by a tire mechanism model and then fed into the whole vehicle dynamics model. This allows the vehicle dynamics model to be built using real-world tire forces, resulting in more accurate simulation of vehicle behavior.
7. Double-Shaft Automobile Vibration Model for Tire Performance Parameter Simulation in Whole Vehicle Analysis
FAW BESTURN CAR CO LTD, 2024
Simulating tire performance parameters using a whole vehicle simulation to enable faster and more accurate tire development. The method involves building a double-shaft automobile equivalent vibration model in Simulink that takes road surface and tire inputs and outputs body motion like vertical displacement, pitch, roll, and yaw. This allows simulating tire performance parameters by running the whole vehicle simulation and extracting tire-specific forces and motions. By matching tire and vehicle simulation results, tire and whole vehicle performance are better balanced.
8. Kinetic and Compliance System with Mathematical Tire Model for Coupled Load Simulation
HUAZHONG UNIV OF SCIENCE AND TECHNOLOGY, HUAZHONG UNIVERSITY OF SCIENCE AND TECHNOLOGY, 2024
A new K&C (kinetic and compliance) experimental system and method for more accurately simulating vehicle performance parameters and understanding vehicle behavior under different driving conditions. The system involves modeling tire operating conditions mathematically and using a tire model based on tire mechanical characteristics to calculate the coupled tire loads. This allows comprehensive consideration of the coupling effect between multiple inputs acting simultaneously on the suspension. The coupled tire loads are then input into a suspension model to simulate its K&C characteristics.
9. Indoor Tire Testing Device with Carriage-Coupled Drum and Torque-Isolated Wheel Speed Control
KOKUSAI KEISOKUKI KABUSHIKI KAISHA, KOKUSAI KEISOKUKI KK, 2024
Indoor tire testing device that can accurately simulate road conditions like rain, snow, and gravel for tire performance evaluation. The device allows testing on a rotating drum with simulated road surfaces, but it addresses the limitation of high-speed drum rotation by having a carriage that travels along the drum at a lower speed. This allows accurate testing of tire performance on specific road conditions by matching the carriage speed to the desired condition. The carriage and test wheel are both driven by a common power source, with a torque-applying device to isolate the wheel speed control from the power source. This allows the wheel to rotate at the carriage speed for accurate testing.
10. Tire Wear Prediction System Utilizing Vehicle Model-Driven Force Extraction and Validation
HANKOOK TIRE & TECH CO LTD, HANKOOK TIRE & TECHNOLOGY CO LTD, 2024
A tire wear prediction system that uses vehicle driving data to accurately predict tire wear. The system extracts driving forces and loads from a vehicle model driven based on real driving data. These forces are applied to a tire model to calculate wear. The extracted driving forces are compared to real vehicle forces to validate the simulation. If the difference is within a certain range, tire wear is predicted using the simulated forces. This allows more accurate wear prediction compared to just using the tire model since it accounts for the actual vehicle dynamics.
11. Tire Rolling Behavior Simulation with Iterative Contact Parameter Averaging
SUMITOMO RUBBER IND LTD, 2024
Tire simulation method to accurately evaluate tire rolling behavior by averaging ground contact parameters over multiple rolling iterations. The method involves inputting a tire and road model, rolling the tire, calculating ground contact parameters multiple times, averaging those parameters, and displaying the averaged contact parameters. This provides a more representative view of the tire's rolling contact compared to just a single iteration.
12. Tire Testing Device with Independently Controlled Wheel Torque Mechanism and Carriage System
KOKUSAI KEISOKUKI KABUSHIKI KAISHA, 2024
Tire testing device that allows accurate evaluation of tire performance on simulated road surfaces, particularly for wet, snowy, or gravel conditions that are difficult to replicate in indoor testing. The device has a carriage that travels along a base with a test wheel mounted. The carriage and wheel are driven by a common power source, but the wheel speed is controlled separately using a torque applying device. This allows the wheel to spin freely at base speed when the torque device is inactive, then apply torque to match the wheel to the carriage speed. This maintains consistent wheel speed versus road speed, enabling accurate testing on simulated surfaces.
13. Vehicle Simulation Method Employing Lightweight Models for Center of Mass Speed Calculation
HUAREN YUNTONG SHANDONG TECH CO LTD, HUAREN YUNTONG TECHNOLOGY CO LTD, 2024
Improving the accuracy and efficiency of vehicle simulation testing by using lightweight models to calculate center of mass vehicle speed. The method involves establishing a vehicle dynamics model based on wheel end forces and a tire model containing longitudinal slip conditions. This allows calculating center of mass speed using the wheel forces and adhesion when less than road limits, or road adhesion when exceeded. This improves simulation testing by using realistic models and reducing computation compared to full vehicle dynamics simulations.
14. Method for Simulating Local Equivalent Finite Element Models of Tire Pattern Blocks
SHANGHAI JIAOTONG UNIVERSITY, UNIV SHANGHAI JIAOTONG, ZHONGCE RUBBER GROUP CO LTD, 2023
Simulating and evaluating the local equivalent finite element of tire pattern blocks to improve safety and performance of tires with patterns. The method involves breaking down the tire pattern into smaller blocks and creating a simplified finite element model of each block. This allows analyzing the block's deformation and contact forces under load without the complexity of modeling the whole tire. The local block models can then be used to optimize pattern shapes, groove depths, sheet gaps, and contact forces for better tire performance in scenes like snow.
15. Finite Element Simulation Method for Tire Extrusion Using 2D Cross-Section Model with Bidirectional Load Analysis
SHANGHAI JIAOTONG UNIVERSITY, UNIV SHANGHAI JIAOTONG, ZHONGCE RUBBER GROUP CO LTD, 2023
Fast and easy-to-converge finite element tire extrusion simulation method to evaluate tire durability and safety performance in extreme scenarios like bidirectional extrusion. It involves a specific process to create a 2D tire inflation cross-section model that is simpler and converges faster compared to a full 3D tire model. The steps include: 1. Define a 2D cross-section geometry representing the tire at inflation pressure. 2. Assign material properties to the cross-section elements based on the actual tire materials. 3. Load the cross-section model with bidirectional extrusion forces. 4. Simulate the extrusion deformation and failure of the cross-section to evaluate tire durability and safety. The method reduces simulation time and resources compared to full 3D models for scenarios where extreme loads are applied bidirectionally.
16. Finite Element-Based Simulation Method for Tire Driving Force Calculation Using Discretized Tire Geometry and Contact Element Modeling
ZHONGCE RUBBER GROUP CO LTD, 2023
Simulation method for calculating tire driving force that enables efficient and accurate optimization of tire quality and performance. The method involves discretizing the tire geometry into finite elements, modeling the tire-road contact using contact elements, and solving the finite element analysis to calculate the tire forces. It allows simulating tire rolling characteristics without expensive hardware.
17. Simulation Method for Tire Rigidity with Mixed Contact Constraints in Central, Transition, and Edge Areas
HANGZHOU HAICHAO RUBBER CO LTD, ZHONGCE RUBBER GROUP CO LTD, 2023
High-precision and high-efficiency simulation method for tire rigidity using mixed constraints in the tire-road contact area. The simulation improves accuracy and convergence by using different contact constraint methods in different contact areas. The method involves simulating tire rigidity by: 1. Using full friction constraints for the central contact area where the tire and road are fully in contact. 2. Using partial friction constraints for the transition area between the central and edge contact areas. Here, the constraints allow some slip to prevent sticking, but limit it to avoid excessive slip. 3. Using full slip constraints for the edge contact area where the tire and road are not fully in contact. This allows the tire to slide against the road in this area. The mixed constraint approach improves simulation accuracy by more accurately modeling the behavior near the ground contact edge, where full contact transitions to partial contact. It also improves efficiency by preventing convergence issues due to excessive
18. Method for Simulating Tire Stiffness with Zoned Mixed Constraints Between Tire and Rim
HANGZHOU HAICHAO RUBBER CO LTD, ZHONGCE RUBBER GROUP CO LTD, 2023
A method for accurately simulating tire stiffness using mixed constraints between the tire and rim. The method involves dividing the contact region between the tire and rim into multiple zones with different constraint conditions. This allows capturing the nonlinear contact behavior as the tire deforms on the ground more realistically. By applying varying constraint levels in each zone, it prevents slipping between the tire and rim during simulation which can lead to inconsistent results and non-convergence. This improves simulation accuracy and efficiency compared to using a uniform constraint.
19. Method for Dynamic Tire Testing Under Composite Loading Conditions with Simulated Driving Scenarios
CHINA FAW GROUP CORP, 2023
Testing tires under dynamic loading conditions that mimic realistic driving scenarios to accurately analyze tire performance and behavior under composite working conditions. The method involves testing a tire under predetermined composite conditions like rolling, rolling with longitudinal slip, and rolling with longitudinal slip and lateral slip. This allows capturing tire response data under simulated driving scenarios. Analyzing the results provides a more accurate representation of tire behavior under complex conditions compared to testing single working conditions.
20. Method for Constructing Interconnected Vehicle, Tire, and Steering Models with Corrected Return Characteristics for Driving Simulators
CHINA FAW GROUP CORP, 2023
Method for accurately testing tire models for driving simulators to improve simulation realism and provide a basis for virtual development, adjustment, and matching. The method involves constructing a test model with interconnected vehicle, tire, and steering models. Steering parameters are input into the steering model to get tire torsion parameters. These are used with actual tire speeds to obtain corrected return characteristics for more accurate simulation.
Get Full Report
Access our comprehensive collection of 144 documents related to this technology
Identify Key Areas of Innovation in 2025
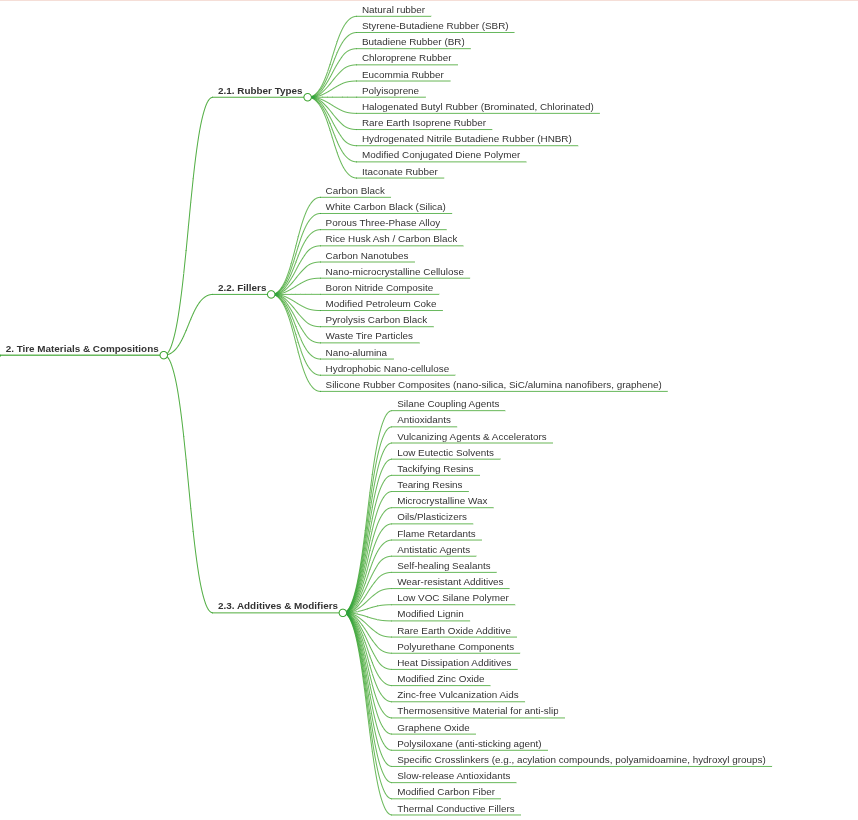