Inner Liner Extrusion for Tire Manufacturing
Inner liner extrusion presents persistent challenges in tire manufacturing, where thickness variations as small as 0.1mm can impact air retention performance. Current production processes must maintain precise temperature control between 110-130°C while managing material flow rates of 50-200 kg/hour through complex die geometries, all while preventing premature cross-linking of butyl rubber compounds.
The fundamental challenge lies in balancing material processing characteristics against the finished liner's air impermeability, adhesion strength, and fatigue resistance properties.
This page brings together solutions from recent research—including modified butyl rubber compositions with tailored molecular weight distributions, thermoplastic polyester film technologies, and advanced dispersant systems for nanocomposite materials. These and other approaches focus on achieving consistent extrusion quality while meeting increasingly stringent performance requirements for modern tire applications.
1. Forming Device with Extrusion Roller and Threaded Chamber for Non-Protruding Rubber Layers
COMPAGNIE GENERALE DES ETABLISSEMENTS MICHELIN, 2025
Complex forming device for making rubber products with non-protruding layers by using blades to pass underneath. The device has an extrusion roller with a chamber for plasticizing the rubber. The chamber is defined by the roller and a wall with projecting threads. The threads delimit the chamber to shape the rubber. But the device also has additional features to allow blades to pass beneath the extruded rubber. This prevents protrusions and provides smooth layers. The device has supports for an additional roller below the extrusion roller, and securing to hold it in place. This allows the blades to move between the rollers. It also enables removing any rubber particles trapped between the rollers. The device can be used in tire production lines to make tires with consistent smooth layers.
2. Multi-layered Structure with Core Layer and Polydiene Polyol-based Polyurethane Cap Layers
NIKE INC, 2025
Multi-layered structures with improved gas barrier properties for applications like tires, cushioning, and bladders. The structure has a core layer sandwiched between cap layers. The core layer has low gas transmission. The cap layers contain a polydiene polyol-based polyurethane with enhanced bonding to the core. The cap layers may also have uncured rubber to further bond. This reduces bubble formation during vulcanization. The multi-layered structure can be made by extruding the core, then laminating the cap layers onto it.
3. Real-Time Feedback Control System for Extrusion Process Parameter Optimization Based on Non-Contact Warm Profile Measurement
CONTINENTAL REIFEN DEUTSCHLAND GMBH, 2023
Improving the quality and efficiency of extrusion processes for manufacturing products like tires by using real-time feedback control to optimize extrusion parameters. The method involves determining the warm extrusion profile without contact, modeling the cold profile based on that, comparing to a target profile, iteratively optimizing parameters to reduce deviation, and selecting the optimized parameters to control the extrusion. This provides quicker and more accurate adjustments compared to waiting for downstream measurement.
4. Method for Determining Inner Liner Thickness Using Point-Specific Calculations Based on Tire Section and Material Properties
Anhui Giti Passenger Radial Tire Co., Ltd., ANHUI GITI PASSENGER RADIAL TIRE CO LTD, 2022
Method to accurately design the thickness of the inner liner of a passenger car tire to optimize air pressure and durability while minimizing material waste. The method involves calculating the required thickness of the tire inner liner at specific points along the tire section using a customized formula that takes into account factors like tire size, section shape, and material properties. This allows more precise thickness dimensions for the semi-finished tire liner component that better match the finished tire requirements. By calculating the liner thickness at multiple points instead of just the crown, it reduces over-thickening in other areas and avoids waste.
5. Method for Forming Laminated Inner Liner with Dual-Layer Rubber Sheets to Prevent Necking
BRIDGESTONE CORP, 2021
Tire manufacturing method that suppresses the occurrence of necking while ensuring light weight without changing the rubber composition for maintaining high gas barrier properties. The method includes obtaining a rubber sheet for an inner liner by extrusion molding using a rubber composition for an inner liner, at least two of the obtained rubber sheets for an inner liner are formed, the inner liner is laminated over the entire tire width direction to form the inner liner, and the inner liner is formed by combining two layers of rubber sheets.
6. Manufacturing Method for Tires with Non-Overlapping Thickened Inner Liner Sections
SUMITOMO RUBBER IND, SUMITOMO RUBBER IND LTD, 2021
Method for manufacturing tires that ensures uniform thickness of the inner liner when the tire is vulcanized. The method involves designing the raw tire inner liner with thicker sections that do not overlap the belt layer in the radial direction. This prevents the thicker sections from being compressed by the bladder during vulcanization, allowing the thinner base section to stretch and maintain a uniform inner liner thickness.
7. Butyl Rubber Compositions with Specified Hydrocarbon Resin Content and Reduced Glass Transition Temperatures
ExxonMobil Chemical Patents Inc., 2020
Low temperature fatigue resistant butyl rubber compositions with reduced glass transition temperatures. The compositions contain specific hydrocarbon resins having aromatic, olefinic, and aliphatic hydrogen contents in specific ranges, along with molecular weight and glass transition temperature ranges. These resins can be used in applications like tire inner liners to improve low temperature flexibility without increasing permeability.
8. Pneumatic Tire with Butyl Rubber Innerliner and Insulation Featuring Specific Composition Ratios for Enhanced Adhesion
SUMITOMO RUBBER INDUSTRIES, LTD., 2020
Pneumatic tire with improved air retention and reduced peeling between the innerliner and insulation. The tire has a carcass, insulation, and innerliner. The innerliner and insulation each contain a butyl rubber compound. The innerliner rubber has specific amounts of butyl rubber, carbon black, zinc oxide, and sulfur. The insulation rubber has specific amounts of butyl rubber, isoprene rubber, carbon black, and sulfur. The innerliner and insulation rubber compositions have predetermined ratios of butyl rubber content. This combination of high butyl rubber in the innerliner and specific ratios in the insulation improves adhesion between the two components, especially at the joint interface, to prevent peeling.
9. Butyl Rubber Composition with Isoprene Conjugated Diene Units and Tailored Molecular Weight Distribution
CHINA PETROLEUM & CHEMICAL CORPORATION, BEIJING RESEARCH INSTITUTE OF CHEMICAL INDUSTRY, CHINA PETROLEUM & CHEMICAL CORPORATION, 2019
Butyl rubber with improved processing and application properties for applications like tire inner liners, inner tubes, and curing bladders. The rubber contains isoprene conjugated diene units along with isobutylene units. This composition allows tailoring the molecular weight distribution to have higher proportions of high molecular weight components. This improves processing properties like green strength and elasticity while maintaining air tightness. The butyl rubber is prepared by copolymerizing isobutylene and isoprene using grafting agents, Lewis acids, and proton sources to control molecular weight and distribution.
10. Production Method for Consistent Dimensional Control in All-Steel Radial Truck Tires
Ningxia Shenzhou Tire Co., Ltd., 2019
Method to improve dynamic balance performance of all-steel radial truck tires by optimizing production processes to ensure consistent tire dimensions, thickness, and quality. Steps include: (1) Using a tread extrusion line with long cooling time and precise cutting to guarantee stable tread length and thickness. (2) Extruding symmetrical sidewalls in one step with consistent length. (3) Composite inner liner production with calendering to avoid distortion. (4) Constant tension calendering for even cord thickness. (5) Stable forming block pressure from separate gas tank. (6) Flat tire storage and transportation to prevent deformation.
11. Innerliner Composition with Butyl Rubber and Mercapto-Functional Silicone Oil
TOYO TIRE & RUBBER CO., LTD., 2019
Tire innerliner composition and pneumatic tire that improves both air impermeability and fatigue resistance compared to conventional tire innerliners. The innerliner composition contains a butyl rubber and silicone oil with silicone having at least two mercapto groups. This composition allows better fatigue resistance without compromising air impermeability compared to traditional tire innerliners that use oil. The pneumatic tire uses this innerliner composition to improve both air retention and durability.
12. Rubber Composition with Low Tg Terpene Resin for Enhanced Air Barrier Properties in Tire Inner Liners
SUMITOMO RUBBER INDUSTRIES, LTD., 2018
Rubber composition for inner liners in tires that balances air barrier properties, moldability, and durability. The composition contains a rubber component and a terpene-based resin with a glass transition temperature (Tg) of 60°C or lower. This composition has an air barrier property index of 110 or higher, indicating low air permeability. The Tg terpene resin improves air barrier while the rubber component provides moldability. The low Tg resin prevents cracks compared to higher Tg resins. The composition is useful for tire inner liners and bladders that require air barrier properties and durability.
13. Sealing Compounds for Tires with Crosslinked Diene Rubber Gels and Specified Fillers
ARLANXEO Deutschland GmbH, 2018
Sealing compounds for tires with improved adhesion and cohesion properties for self-sealing tires. The compounds contain sealing gels made from diene rubbers crosslinked during polymerization. The gels have specific viscosities and molecular weight ranges. The compounds also have fillers like silica, carbon black, and clay. The sealing gels improve adhesion and cohesion compared to conventional sealants. The compounds are used as sealing layers in tire inner liners to prevent air leakage.
14. Halogenated Copolymer-Based Dispersant for Graphite and Graphene Nanofillers in Halobutyl Rubber Nanocomposites
ExxonMobil Chemical Patents Inc., 2017
Dispersant for improving dispersion of graphite or graphene nanofillers in elastomeric nanocomposites containing halobutyl rubber. The dispersant is made by reacting a halogenated copolymer derived from isobutylene and alkylstyrene with polycyclic aromatic hydrocarbons. This functionalized copolymer acts as a dispersant when added to halobutyl rubber nanocomposites containing graphite or graphene, leading to better exfoliation and dispersion of the nanofillers compared to unmodified halobutyl rubber. This improves the air barrier properties of the composites, making them suitable for tire innerliners.
15. Pneumatic Tire Innerliner Comprising Polyamide-α-Olefin-Ionomer Blend with Corona Treatment and Adhesive Layers
The Goodyear Tire & Rubber Company, 2016
A thinner and lighter weight innerliner for pneumatic tires that provides improved oxygen and air permeability compared to conventional butyl rubber liners. The innerliner uses a blend of polyamide, α-olefin graft copolymer, and ionomer in the film layer. The film is treated with corona discharge to enhance adhesion. An amine and resorcinol-formaldehyde-latex (RFL) adhesive are applied to the treated film. This allows reducing the innerliner thickness significantly while maintaining air retention by eliminating the need for a separate low hysteresis rubber layer. The corona treatment and adhesive layers improve adhesion to the tire carcass.
16. Thermoplastic Polyester Resin Film with Resorcin-Based Formaldehyde Condensates for Enhanced Rubber Adhesion
TOYO TIRE & RUBBER CO., LTD., 2015
Improving adhesion between thermoplastic polyester resin films and rubber in applications like inner liners of tires by adding resorcin-based formaldehyde condensates to the resin and melamine-formaldehyde resins to the rubber. The condensate in the resin and the melamine-formaldehyde resin in the rubber bond during vulcanization molding to enhance adhesion.
17. Tyre Inner Layer Composition with Diene Elastomers and Polyisobutylene Block Thermoplastic Elastomers
Michelin Recherche et Technique S.A., COMPAGNIE GENERALE DES ETABLISSEMENTS MICHELIN, 2014
Tyre inner layer composition with improved airtightness compared to traditional butyl rubber liners. The composition contains diene elastomers, thermoplastic elastomers with polyisobutylene blocks, reinforcing filler, and a crosslinking system. The thermoplastic elastomers and filler are added in small amounts (1-99 phr) to the diene elastomers. This improves airtightness by reducing permeability without the need for high butyl rubber content. The lower permeability allows maintaining lower tyre inflation pressures for longer periods without air loss, improving tyre performance stability over time.
18. Graphene Oxide/Rubber Composite with Islands-in-Sea Structure for Tire Inner Liners and Tubes
BEIJING UNIVERSITY OF CHEMICAL TECHNOLOGY, 2014
A composition for manufacturing inner liners and inner tubes of tires with low air permeability and good flexibility. The composition contains an islands-in-the-sea structure where the continuous phase is a graphene oxide/rubber composition and the dispersed phase is epoxy natural rubber or thermoplastic resin. The graphene oxide/rubber composition is made by dispersing graphene oxide in rubber with ionic or covalent bonding between the graphene oxide and reactive rubber. This provides uniform graphene oxide dispersion, impermeable layers, and low air permeability. The solid rubber in the composition improves flexibility.
19. Multilayer Pneumatic Tire Inner Liner with Integrated Gas Barrier and Elastomeric Adhesion Layers
KURARAY CO., LTD., BRIDGESTONE CORPORATION, 2014
Inner liner for pneumatic tires that adheres well to the rubber tire without needing an adhesive layer. The liner is a multilayer structure with a barrier layer containing a gas barrier resin, an elastomer layer, and an outermost layer containing an elastomer that adheres to diene rubber. This allows the liner to have good internal pressure retention and crack resistance without breaking or generating cracks due to tire deformation. The adhesion between the elastomer and rubber allows the liner to stick to the tire without separating during tire flexing.
20. Method for Manufacturing Pneumatic Tire with Thin Polymer Layer Stack Inner Liner Featuring SIBS and SEBS Block Copolymers
SUMITOMO RUBBER INDUSTRIES, LTD., 2014
A method for manufacturing a pneumatic tire with a thin inner liner that prevents air leakage and eliminates the "air-in" phenomenon where small air bubbles form between the inner liner and tire components. The method involves using a thin polymer layer stack with specific layers for the inner liner. The stack has a styrene-isobutylene-styrene (SIBS) block copolymer outer layer with 0.05-0.6 mm thickness and an epoxidized styrene-butadiene-styrene (SEBS) block copolymer inner layer with 0.01-0.3 mm thickness. The tire is molded with this stack, vulcanized with pressure from a bladder, and then cooled immediately at 120°C or lower for 10-300 seconds without removing the mold. This solid
Get Full Report
Access our comprehensive collection of 28 documents related to this technology
Identify Key Areas of Innovation in 2025
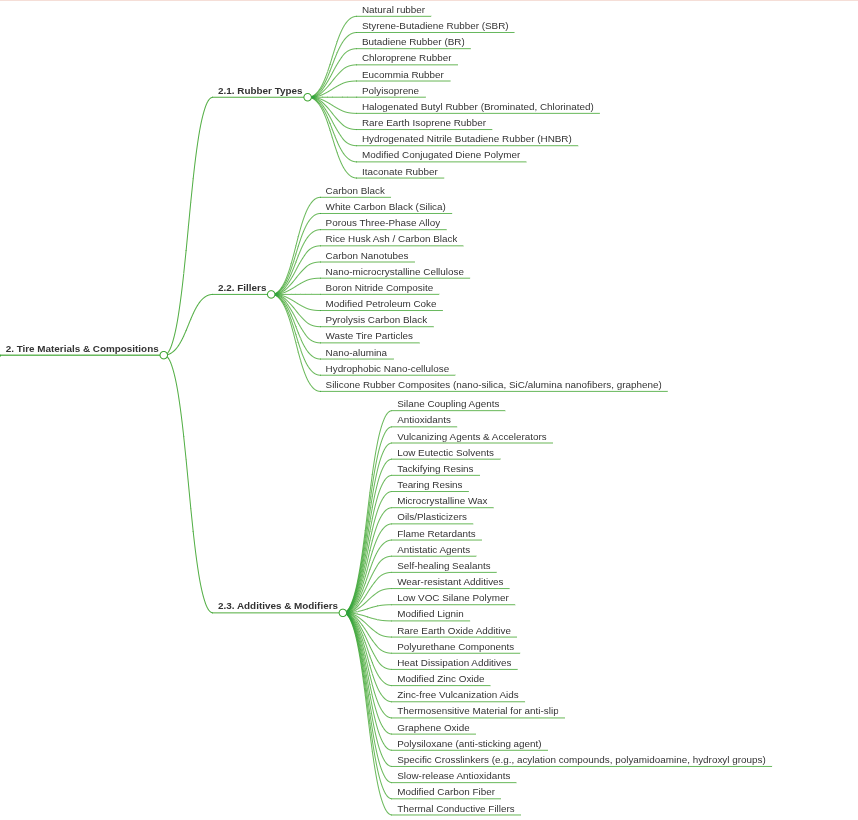