Dynamic Simulation of Tire Performance
Modern tire development requires precise modeling of dynamic behavior across multiple physical domains. Current simulations must capture complex interactions between materials, forces, and thermal conditions—with contact patch pressures exceeding 200 kPa and operating temperatures ranging from -20°C to 100°C during normal driving conditions.
The fundamental challenge lies in balancing simulation accuracy with computational efficiency while capturing the nonlinear, temperature-dependent behavior of tire materials under dynamic loading conditions.
This page brings together solutions from recent research—including adaptive friction coefficient modeling, thermodynamic prediction systems, multi-step cornering analysis, and real-time force estimation approaches. These and other methods demonstrate how tire behavior can be accurately predicted while maintaining practical computational requirements for development cycles.
1. Finite Element Simulation of Tire Longitudinal Slip Characteristics with Variable Slip Rates and Fitted Friction Model
HANGZHOU HAICHAO RUBBER CO LTD, ZHONGCE RUBBER GROUP CO LTD, 2024
Simulating tire longitudinal slip characteristics using finite element analysis to efficiently and accurately determine tire forces and moments when sliding on the road. The simulation involves steps like finite element pretreatment, 2D inflation analysis, 3D loading modeling, steady state simulation, and dynamic slip simulation. It uses explicit analysis with customizable slip rates and a fitted friction model from rubber testing to accurately replicate tire longitudinal behavior. This allows tire dynamics modeling and optimization without physical testing.
2. Simulation Method for Calculating Tire Sidewall Fatigue Life Under Flexural Deformation
ZHONGCE RUBBER GROUP CO LTD, 2024
A method to simulate and calculate fatigue life of tire sidewalls under flexural deformation. The method involves modeling tire sidewall flexure using simulation software like Abaqus. The simulation captures different deformation amounts and the entire flexure process. Fatigue life calculation is done using software like Endurica. The simulation output provides parameters like stress, strain, Mises stress, fatigue life for analyzing tire sidewall flexural fatigue.
3. Multi-Step Tire Cornering Simulation Method with Static Loading and Dynamic Analysis
HANGZHOU HAICHAO RUBBER CO LTD, ZHONGCE RUBBER GROUP CO LTD, 2024
Simulating tire cornering performance to improve tire design and development. The simulation method involves a multi-step process to efficiently and accurately model tire cornering characteristics. It starts with static loading analysis to calculate the inflation radius. Then dynamic cornering simulation is done to analyze the tire's lateral force, aligning moment, and steering angle. By breaking down the simulation into separate steps, it allows capturing the complex tire behavior while avoiding excessive computational complexity that would come with simulating all tire components at once.
4. Vehicle Dynamics Model Incorporating Real-World Trained Tire Data for Force Estimation
HUAWEI TECH CO LTD, HUAWEI TECHNOLOGIES CO LTD, 2024
Constructing a vehicle dynamics model that accurately reflects the dynamic performance of a vehicle. The method involves introducing a tire data model that is trained using real-world driving data. The tire data model generates tire force estimates. These are fused with forces calculated by a tire mechanism model and then fed into the whole vehicle dynamics model. This allows the vehicle dynamics model to be built using real-world tire forces, resulting in more accurate simulation of vehicle behavior.
5. Tire Durability Prediction Method Using Variable Finite Element Discretization
SUMITOMO RUBBER IND LTD, 2024
Tire simulation method that balances calculation accuracy and time for predicting tire durability. It involves discretizing the tire model using finite elements, but with different element sizes for certain regions. Specifically, the topping rubber covering the carcass cords is discretized with larger elements in a first region, and smaller elements in a second region closer to the tire bead. This allows improving durability calculation accuracy in the bead area without significantly increasing simulation time compared to uniform element sizes.
6. Double-Shaft Automobile Vibration Model for Tire Performance Parameter Simulation in Whole Vehicle Systems
FAW BESTURN CAR CO LTD, 2024
Simulating tire performance parameters using a whole vehicle simulation to enable faster and more accurate tire development. The method involves building a double-shaft automobile equivalent vibration model in Simulink that takes road surface and tire inputs and outputs body motion like vertical displacement, pitch, roll, and yaw. This allows simulating tire performance parameters by running the whole vehicle simulation and extracting tire-specific forces and motions. By matching tire and vehicle simulation results, tire and whole vehicle performance are better balanced.
7. Kinetic and Compliance System with Coupled Tire Load Calculation for Suspension Simulation
HUAZHONG UNIV OF SCIENCE AND TECHNOLOGY, HUAZHONG UNIVERSITY OF SCIENCE AND TECHNOLOGY, 2024
A new K&C (kinetic and compliance) experimental system and method for more accurately simulating vehicle performance parameters and understanding vehicle behavior under different driving conditions. The system involves modeling tire operating conditions mathematically and using a tire model based on tire mechanical characteristics to calculate the coupled tire loads. This allows comprehensive consideration of the coupling effect between multiple inputs acting simultaneously on the suspension. The coupled tire loads are then input into a suspension model to simulate its K&C characteristics.
8. Tire Wear Prediction System Utilizing Vehicle Driving Data and Dynamic Force Validation
HANKOOK TIRE & TECH CO LTD, HANKOOK TIRE & TECHNOLOGY CO LTD, 2024
A tire wear prediction system that uses vehicle driving data to accurately predict tire wear. The system extracts driving forces and loads from a vehicle model driven based on real driving data. These forces are applied to a tire model to calculate wear. The extracted driving forces are compared to real vehicle forces to validate the simulation. If the difference is within a certain range, tire wear is predicted using the simulated forces. This allows more accurate wear prediction compared to just using the tire model since it accounts for the actual vehicle dynamics.
9. Finite Element Simulation Method for Tire Pattern Blocks with Localized Modeling
SHANGHAI JIAOTONG UNIVERSITY, UNIV SHANGHAI JIAOTONG, ZHONGCE RUBBER GROUP CO LTD, 2023
Simulating and evaluating the local equivalent finite element of tire pattern blocks to improve safety and performance of tires with patterns. The method involves breaking down the tire pattern into smaller blocks and creating a simplified finite element model of each block. This allows analyzing the block's deformation and contact forces under load without the complexity of modeling the whole tire. The local block models can then be used to optimize pattern shapes, groove depths, sheet gaps, and contact forces for better tire performance in scenes like snow.
10. Dynamic Calculation Method for Tire Steady-State Rolling Behavior via Deformation and Tension Analysis
CHANGCHUN INST APPLIED CHEMISTRY CAS, CHANGCHUN INSTITUTE OF APPLIED CHEMISTRY CHINESE ACADEMY OF SCIENCES, JILIN UNIVERSITY, 2023
Dynamic calculation method to accurately and efficiently determine tire steady-state rolling behavior without needing to calculate angular and linear velocities. The method involves solving for tire deformation, cord tension, contact pressure, and pressure depth when the tire is rolling steadily. It reduces calculation requirements compared to traditional methods by only needing to calculate the rolling angular velocity, eliminating the need for contact algorithms that can be difficult to converge.
11. Finite Element Method for Predicting Tire Steady-State Lateral Force Using Transient Simulation-Derived Relaxation Length Parameters
ANHUI GITI RADIAL TIRE CO LTD, 2023
Predicting tire steady-state lateral force using finite element simulation by leveraging transient simulation results. The method involves simulating tire lateral force during transient motion using finite elements, then analyzing the results to extract parameters that can be used to predict steady-state lateral force. This avoids the long simulation times needed for direct steady-state simulations by leveraging transient data. The extracted parameters are identified from a relaxation length expression. By fitting the identified parameters to known steady-state lateral force data, the method accurately predicts steady-state lateral force using transient simulation results.
12. Finite Element-Based Simulation Method for Tire Driving Force Calculation
ZHONGCE RUBBER GROUP CO LTD, 2023
Simulation method for calculating tire driving force that enables efficient and accurate optimization of tire quality and performance. The method involves discretizing the tire geometry into finite elements, modeling the tire-road contact using contact elements, and solving the finite element analysis to calculate the tire forces. It allows simulating tire rolling characteristics without expensive hardware.
13. Method for Simulating Tire Stiffness with Zonal Mixed Constraints Between Tire and Rim
HANGZHOU HAICHAO RUBBER CO LTD, ZHONGCE RUBBER GROUP CO LTD, 2023
A method for accurately simulating tire stiffness using mixed constraints between the tire and rim. The method involves dividing the contact region between the tire and rim into multiple zones with different constraint conditions. This allows capturing the nonlinear contact behavior as the tire deforms on the ground more realistically. By applying varying constraint levels in each zone, it prevents slipping between the tire and rim during simulation which can lead to inconsistent results and non-convergence. This improves simulation accuracy and efficiency compared to using a uniform constraint.
14. Dynamic Coupling Analysis Method for Vehicles, Bridges, and Pavement Using Finite Element and Multi-Body Dynamics Modeling
Shijiazhuang Tiedao University, SHIJIAZHUANG TIEDAO UNIVERSITY, 2023
Method to analyze the dynamic coupling between vehicles, bridges, and road pavement. The method involves using finite element and multi-body dynamics software to accurately model the vehicle, bridge, and pavement as separate entities. This allows analyzing their individual dynamics and the coupled interactions between them. The modeling considers factors like tire deformation, suspension, and pavement viscoelasticity. The coupled analysis enables understanding vehicle-bridge-road vibrations and fatigue effects.
15. Finite Element Analysis Method for Tire Tread Wear Simulation Using Strip Pattern Friction Work Calculation
ZHONGCE RUBBER GROUP CO LTD, 2023
Simulating tire tread wear using finite element analysis with strip patterns to accurately model tire wear behavior under mixed driving conditions. The method involves calculating friction work for each working condition and weighting/averaging based on mileage percentage to obtain overall wear. This allows more realistic simulation compared to modeling smooth tires and attaching patterns.
16. Rolling Resistance Prediction Using Fourier Leaf Transformation of Tire Sipe Patterns
HANGZHOU HAICHAO RUBBER CO LTD, ZHONGCE RUBBER GROUP CO LTD, 2023
Predicting rolling resistance of tires with complex patterns like sipes using a Fourier leaf transformation technique that allows quick calculation of rolling resistance without needing to simulate full tire cycles. The method involves rolling a simplified intercept angle section of the tire at various speeds and collecting strain data. This data is then Fourier transformed to extract the rolling resistance components. By analyzing the intercept angle section, which captures the key features of the complex pattern, the rolling resistance can be accurately predicted without needing to simulate the entire tire cycle. This provides a faster and more efficient way to evaluate rolling resistance of tires with complex patterns.
17. Finite Element Method for Predicting Fatigue Life of Non-Pneumatic Tires with Thermal-Mechanical Coupling and Crack Growth Simulation
YANGZHOU UNIV, YANGZHOU UNIVERSITY, 2023
A method to predict the fatigue life of non-pneumatic tires using finite element analysis. The method involves modeling the tire structure and materials, simulating thermal-mechanical coupling during tire deformation, and using extended finite elements to predict crack growth. It accounts for temperature effects and fatigue failure mechanisms. The simulation steps include: 1) thermal analysis to determine high temperature areas, 2) meshing and crack initiation in those regions, 3) transferring temperature from the thermal analysis, 4) using extended FEM to calculate crack growth rate, and 5) predicting fatigue life based on crack propagation.
18. Tire Modeling Method Using Cross-Sectional Calibration for Vehicle Vibration and Noise Simulation
CHONGQING CHANGAN AUTOMOBILE CO LTD, 2022
A method to quickly and accurately model tires for simulating whole vehicle vibrations and noise caused by road irregularities. The method involves creating a basic tire model using cross sections of the tire and rim, then calibrating it with standard test data. This allows using the linearized basic tire model in early stage vehicle simulations instead of detailed finite element analysis. The basic tire model can be obtained from tire suppliers or test equipment.
19. Circumferential Strain-Based Vertical Force Estimation System for Heavy-Duty Tires
ROCKET FORCE UNIVERSITY OF ENGINEERING OF PLA, UNIV ROCKET FORCE ENGINEERING PLA, 2022
Estimating the vertical force of heavy-duty tires using circumferential strain analysis, which involves installing strain sensors in the tire tread center to measure deformation as the tire rolls. A support vector machine model is trained using finite element simulation data to predict tire vertical force based on the measured strain. The strain features, like ground contact angle and length, are identified as indicators of force. This provides a more direct and accurate way to estimate tire force compared to using acceleration or tire models, as it avoids issues like noise sensitivity and simplified tire dynamics.
20. Multi-Body Connection Model-Based Tire Simulation Method with Finite Element Analysis and Condition-Driven Manufacturing Parameters
SUMITOMO RUBBER IND, SUMITOMO RUBBER IND LTD, 2022
Tire simulation method that minimizes the time to calculate the physical quantities of a tire in a short time. The method includes setting a second condition, defining a vehicle model, analyzing the motion of the automobile based on the multi-body connection model, the external conditions occurring in the tire are obtained, the simulation using a tire finite element model is performed to acquire physical quantities of the tire, and manufacturing the tire based on the second condition that the physical quantity converges within a predetermined range.
Get Full Report
Access our comprehensive collection of 90 documents related to this technology
Identify Key Areas of Innovation in 2025
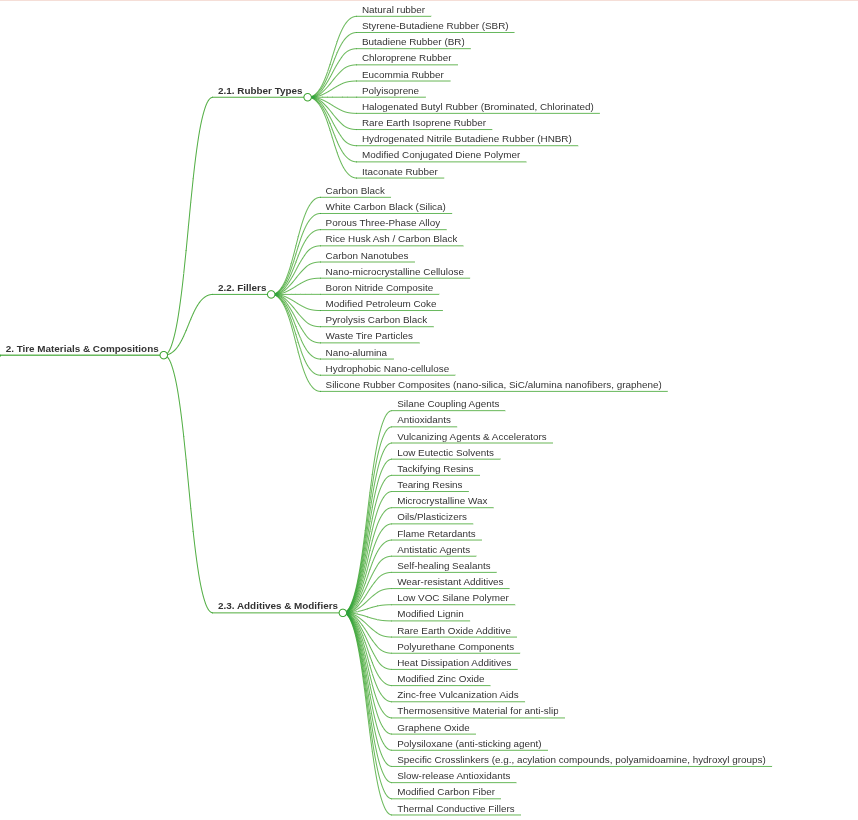