Chemical and Mechanical Recycling of Tires
End-of-life tires present a significant materials recovery challenge, with over 1 billion waste tires generated annually worldwide. Current recycling methods recover only 20-30% of tire materials effectively, while traditional thermal treatments often produce low-grade carbon black with high ash content (>15%) and contaminated oil fractions that limit reuse potential.
The fundamental challenge lies in developing processes that can break down the complex cross-linked polymer networks and separate components while preserving their material value for circular use.
This page brings together solutions from recent research—including continuous thermal cracking systems for whole tires, microwave-assisted pyrolysis techniques, specialized reactor designs with selective heating zones, and mechanical-chemical hybrid approaches. These and other methods focus on achieving higher quality recoverable materials while maintaining economic viability at industrial scale.
1. Method for Co-Vulcanization of Recycled Rubber Using Diffusion Barrier Material
APPIA, LLC, 2024
Method for recycling vulcanized rubber to increase performance and allow higher recycled rubber content compared to prior methods. The key is using a barrier material to prevent sulfur and cure accelerators from the fresh rubber diffusing into the recycled rubber during co-vulcanization. This prevents additional crosslinking in the recycled rubber and improves bonding between the two types of rubber. The barrier material forms a diffusion barrier around the ground recycled rubber particles in the fresh rubber matrix during vulcanization.
2. System for Sequential Separation and Extraction of Steel Cords from Tires
JIANGSU LONGTENG CHENGKUANG INTELLIGENT ENVIRONMENTAL PROT EQUIPMENT CO LTD, JIANGSU LONGTENG CHENGKUANG INTELLIGENT ENVIRONMENTAL PROTECTION EQUIPMENT CO LTD, 2024
Waste tire processing system that extracts steel cords from tires in a more efficient and recyclable way compared to whole tire crushing. The system involves a series of machines to separate the rubber and steel components. The process involves washing tires, drying them, heating and flattening them, cutting them, pulling the steel wires, and grinding the rubber. This allows separating and recycling the steel cords separately from the rubber.
3. Integrated Tire Pulverizer with Simultaneous Multi-Surface Cutting and Vacuum Collection Mechanism
CHEN ZICAI, 2024
A simplified and efficient method for converting waste tires into rubber powder using a single machine. The method involves cutting, grinding, and separating the tire components in one process. A specialized tire pulverizer replaces the multiple machines and steps typically required. The pulverizer has tools that can simultaneously cut the tire top, sidewall, and inner surface at high speeds. The cut rubber is collected by vacuum instead of open grinding. This compact, integrated process reduces equipment, energy, and environmental issues compared to traditional tire powder production.
4. Tire Recycling Process Incorporating Low-Temperature Freezing and Sequential Crushing for Material Separation
DAVID MAX SHIN, 2024
Method for pollution-free recycling of used tires without generating pollution or odor. The process involves shredding tires, spraying them with water, freezing the shreds, crushing the frozen pieces, separating metal fibers, re-crushing, and screening. The freezing step is done at very low temperatures to prevent decomposition and odor generation. It allows clean recycling of tires without using high temperatures and chemicals that cause pollution.
5. Continuous Thermal Cracking System with Preheating Tank and Sealed Reactor for Whole Tires
Qingdao Ikeda Intelligent Equipment Co., Ltd., QINGDAO YIKESIDA INTELLIGENT EQUIPMENT CO LTD, 2023
A continuous thermal cracking system and method for whole tires of waste tires that allows recycling of whole tires without the need for crushing them into blocks first. The system uses a preheating tank, thermal cracking reactor, and condensing system connected in a ring. The preheating tank has front and rear sections filled with water and oil respectively to heat the tires. The reactor has a sealing screw, front bin, internal kettle, and hot air heater. The condensing system separates heavy and light oil. The sealed preheating and reactor sections prevent volatile oil escape. The hot air heater preheats the kettle. This allows fully cracking the whole tires without crushing.
6. Waste Rubber Recycling Machine with Rotor-Based Grinding and Demagnetization Chambers
MIANYANG RUIYANG NEW MATERIAL TECH DEVELOPMENT CO LTD, MIANYANG RUIYANG NEW MATERIAL TECHNOLOGY DEVELOPMENT CO LTD, 2023
Recycling method for waste rubber using a specialized machine that reduces pollution compared to traditional chemical regeneration methods. The machine has a mixing chamber with rotors that grind the rubber block. It also has a demagnetization chamber to remove magnetic impurities from the ground rubber. The machine uses motors and augers to move the rubber through the stages.
7. Devulcanization of Vulcanized Rubber Using Twin-Screw Extruder with Upper Barrel Regenerative Agent Feed
CONTINENTAL REIFEN DEUTSCHLAND GMBH, 2023
Method for devulcanizing vulcanized rubber to recycle old tires and improve properties of rubber articles. The method involves using a twin-screw extruder with a regenerative agent feed point in the upper half of the barrel. The extruder devulcanizes the rubber at temperatures around 100-150°C. This breaks the sulfur bonds without shortening the polymer chains. The devulcanized rubber can be further processed into new rubber mixtures with better properties compared to using fully devulcanized rubber. The extruder configuration with regenerative agent feed allows efficient devulcanization without chain scission.
8. Ozone and Decrosslinking Agent-Based Process for Solvent-Mediated Decrosslinking of Vulcanized Elastomers
BERNARDO BARRETO ALVAREZ, LEONARDO CAMPOS RODOMONTE DE SOUZA, LUIZ FELIPE RODOMONTE DE SOUZA, 2022
Chemically recycling vulcanized elastomers like rubber without high temperatures or solvents. The process involves using ozone and decrosslinking agents like peroxides or persulfates in solvent to dissolve and decrosslink the rubber waste. The solvent swells the polymer chains and the decrosslinking agents break the bonds. Ozone then attacks the decrosslinked chains. This allows recycling vulcanized rubber without degradation or special equipment. The recycled elastomer can replace virgin rubber in new products.
9. Method for Producing Ultra-Fine Rubber Powder from Waste Tires Through Sequential Cutting, Soaking, Crushing, Fiber Separation, and Desulfurization
HEILONGJIANG INST TECH, HEILONGJIANG INSTITUTE OF TECHNOLOGY, 2022
A method for recycling waste tires into ultra-fine rubber powder that fully utilizes the renewable resources in waste tires. The method involves cutting the tires into rings, strips, and blocks, soaking the blocks in water to soften them, crushing them to a fine powder, cleaning, separating fibers, desulfurizing, and cooling the powder. This optimized process allows making high-quality ultra-fine rubber powder from waste tires.
10. Waste Tire Pulverization System with Sequential Crushing, Washing, Freezing, and Grinding Stages
ZHUHAI QIANDING TECH CO LTD, ZHUHAI QIANDING TECHNOLOGY CO LTD, 2022
A waste tire pulverization and rubber powder recovery system that efficiently and cleanly recycles waste tires into usable rubber powder. The system involves a series of crushing, washing, freezing, and grinding stages to progressively reduce the tire into powder. This allows recovery of the rubber without generating pollutants like dioxins. The stages include: 1. Primary normal temperature crushing to break the tires into fragments 2. Fragment washing to clean the pieces 3. Secondary normal temperature crushing to further break the fragments into smaller pieces 4. Primary freezing and grinding to freeze and grind the smaller pieces into powder 5. Secondary freezing and grinding to further grind the powder into finer powder The freezing stages enable cleaner grinding and powder separation. The system also uses liquid nitrogen in the primary grinding stage to further improve powder quality.
11. Modular Mobile Tire Recycling System with Induction-Based Bead Wire Separation
LAATUINSINOEOERIT OY, LAATUINSINÖÖRIT OY, 2022
Mobile tire recycling system that can be transported to sites for processing tires. The system involves a modular setup with separate modules for removing bead wires, cutting rubber sides, and further processing. The bead wire removal uses induction heating to separate the wires from the rubber. The tire is heated to break the bond, cooled, and then the wires are mechanically or magnetically separated. This allows recycling the metal wires separately from the rubber. The cut rubber sides are further processed into recyclable granules. The modular setup allows transporting the components to a site and assembling the recycling system there.
12. Multi-Stage Tire Recycling System with Coarse Pulverization and Magnetic Separation for Rubber Extraction
COMMON SANXIN ENVIRONMENTAL PROTECTION RESOURCE SCIENCE AND TECH UTILIZATION AND DEVELOPMENT LTD, COMMON SANXIN ENVIRONMENTAL PROTECTION RESOURCE SCIENCE AND TECHNOLOGY UTILIZATION AND DEVELOPMENT LIMITED CO, 2022
An environmentally friendly system for recycling waste tires into rubber. The system involves multi-stage grinding and separation to efficiently extract pure rubber from the tires. It has coarse pulverization, magnetic separation, and fine pulverization stages. The coarse pulverizing structure breaks the tires into larger pieces. The magnetic separation separates the pieces into pure rubber and iron-bearing rubber. The pure rubber goes to fine pulverization, while the iron-bearing rubber is magnetically separated again to improve purity. This allows fast, efficient, and high-quality recycling of tires into pure rubber.
13. Recycling Method for Converting Waste Tires into Rubber Powder with Additive Processing
JIANGSU GOUDIFF NEW MATERIAL TECH CO LTD, JIANGSU GOUDIFF NEW MATERIAL TECHNOLOGY CO LTD, 2022
Method for recycling waste tires into reusable rubber materials. The method involves grinding the waste tires into granular rubber, then sieving and conveying the granules to further grind them into powder. The powder is then processed with additives like carbon black, cross-linking agent, wax, and antioxidant to make a usable rubber compound. The compound is formed by kneading, cooling, and vulcanization.
14. Automated System for Dismantling and Separating Tire Components Using Integrated Machinery
Jiangsu Huahong Technology Co., Ltd., JIANGSU HUAHONG TECHNOLOGY STOCK CO LTD, 2022
Automatic processing system for recycling waste tires that can fully automate dismantling and separating the tire components for recycling. The system uses a series of connected machines like storage, bead wire separators, crown cutters, shredders, wire grinders, and wire sorting machines to automatically process and separate the tire into its components for recycling. This improves efficiency and consistency compared to manual dismantling.
15. Recycled Rubber Production System with Multi-Stage Grinding and Magnetic Separation
COMMON SANXIN ENVIRONMENTAL PROTECTION RESOURCE SCIENCE AND TECH UTILIZATION AND DEVELOPMENT LTD, COMMON SANXIN ENVIRONMENTAL PROTECTION RESOURCE SCIENCE AND TECHNOLOGY UTILIZATION AND DEVELOPMENT LIMITED CO, 2022
Environmentally friendly recycled rubber production system and method that improves efficiency and purity of recycling waste tires into rubber. The system involves a multi-stage process with separate grinding and magnetic separation steps. Coarse pulverization of tires is followed by magnetic separation to divide into pure rubber particles and iron-bearing rubber particles. Pure rubber particles are further finely ground, while iron-bearing rubber particles are magnetically separated again to ensure purity. This staged processing improves recycling speed and purity compared to direct grinding of whole tires.
16. Multi-Stage Tire Crushing System with Transverse Feeder and Surfactant Mixing Apparatus
HEBEI FOCEAN POLYMER TECH CO LTD, HEBEI FOCEAN POLYMER TECHNOLOGY CO LTD, 2022
Efficient and quick tire recycling system that crushes tires into fine powder. The system has a multi-stage crushing process with a transverse feeder, mills, oscillating screens, conveyors, and control system. It also has a stirring system to mix a surfactant with the crushed tire particles before grinding to reduce calorific value and prevent fires during grinding.
17. Tire Recycling Machine with Metal Detection and Extraction Mechanism
TAN WEIDI, 2021
Environmentally friendly tire recycling machine that can extract metal from waste tires before crushing the rubber. The machine has a rotating table, metal detector, cutting assembly, clamping assembly, crushing assembly, and conveyor belt. If metal is detected, the table stops and cuts off the metal part. The clamping assembly removes the uncut tire section. This allows separating metal objects from tires before crushing, preventing metal contamination in recycled rubber.
18. Two-Stage Tire Cracking System with Preheating, Separation, and Adjustable Spiral Feeder
ECON TECH CO LTD, 2021
A waste tire cracking system for efficiently and cleanly recycling end-of-life tires into useful products like carbon black and steel. The system uses a two-stage cracking furnace setup with preheating, separation, and condensation steps to maximize resource recovery. The first furnace cracks the tires to release the carbon black and steel. The second furnace further cracks the carbon black to increase yield. The condensers collect the water vapor and liquid condensates from the gases. The system also uses a spiral feeder to introduce the tires into the furnaces. This allows adjusting the feeding height based on tire composition. The system also has filters and exhaust ports to control emissions.
19. Waste Tire Recycling Process with Magnetic Steel Extraction and Centrifugal Rubber Separation
JINYUN ENVIRONMENTAL TECH ENGINEERING SHANGHAI CO LTD, JINYUN ENVIRONMENTAL TECHNOLOGY ENGINEERING CO LTD, 2021
Recycling process for waste tires that involves shredding the tires, extracting the steel using magnetic separation, and then separating the rubber using centrifugation. This allows recovering the steel, eliminating the need for high temperature pyrolysis, reducing environmental impact, and reducing cost compared to traditional methods. The shredded tires are first magnetically separated to remove the steel. The remaining rubber is then centrifuged to separate the lighter rubber particles from the denser filler particles. The separated rubber can be used for recycled tire applications, while the filler is disposed of.
20. Device for Controlled Separation and Recovery of Steel, Rubber, and Sand from Waste Tires
Chaoyang Huaxing Wanda Tire Co., Ltd., CHAOYANG HUAXING WANDA TYRE CO LTD, 2021
Rubber tire recycling device that efficiently separates and recover valuable components like steel, rubber, and sand from waste tires. The device has stages to remove the tire crown, rims, and steel wire mesh in a controlled manner. It uses mechanisms like cutters, push rods, and gears to separate the tire components. This allows recovery of steel wire and mesh with integrity, avoiding residual adhesion issues. The sand is removed separately to prevent wrapping around the cutter. The separated components are then collected.
Get Full Report
Access our comprehensive collection of 93 documents related to this technology
Identify Key Areas of Innovation in 2025
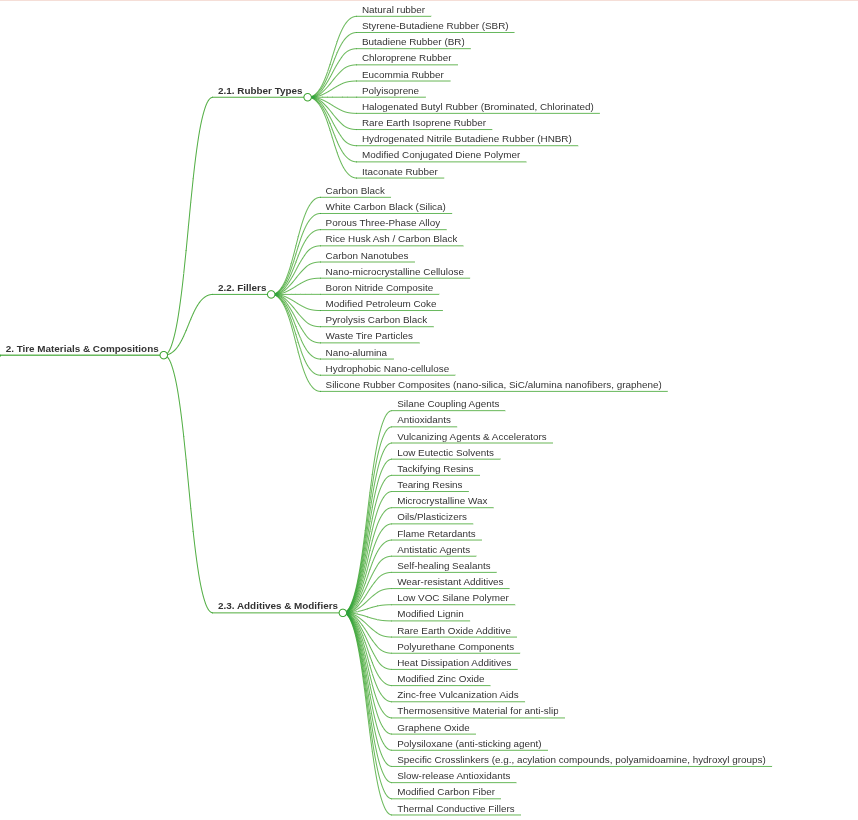