Techniques for Reducing Tire Noise
Vehicle tire noise, generated through air pumping, cavity resonance, and tread pattern impacts, creates acoustic signatures ranging from 65-80 dB at highway speeds. These mechanisms produce both tonal and broadband components across the frequency spectrum of 500-2000 Hz, with distinct variations based on road surfaces, vehicle speed, and loading conditions.
The fundamental challenge lies in modifying tire structure and materials to reduce noise generation while maintaining essential performance characteristics like grip, durability, and wet-weather safety.
This page brings together solutions from recent research—including internal foam dampers, optimized tread patterns with variable sipe geometries, resonator chambers in groove designs, and strategic mass distribution techniques. These and other approaches demonstrate practical methods for achieving noise reduction while preserving critical tire performance metrics.
TABLE OF CONTENTS
1. Contact-Patch Source Control: Geometry and Localized Stiffness Management
Design work at the level of the contact patch attacks noise at its origin. When the entering edge of a tread block compresses the trapped air, two physical mechanisms interact: air-pumping generates an airborne pulse and structural ringing travels through the belt to the cabin. The wide main groove ≥ 15 % footprint width concept selects one circumferential channel whose cumulative width is at least fifteen percent of the static contact patch. The generous void interrupts the air-pumping cycle, yet steering feel is preserved because the undertread is deliberately thinner beneath the central half of the footprint than beneath the shoulders, and the JIS hardness gap between cap and undertread rubber is tuned to absorb radial vibration before it reaches the carcass. Rolling-noise tests show a median 1.5 dB(A) pass-by reduction together with measurably crisper on-center response.
Suppressing a single amplitude peak does not solve the full problem because a modern tyre emits several narrowband tones. The segmented rib strategy with graded transverse-cut density partitions the tread into ribs that each obey one of three mutually exclusive cut regimes: zero cuts, sparse deep cuts, or dense deep cuts. Every rib therefore carries at least one quiet zone and one highly cut zone, which forces two discrete excitation spectra that are intentionally offset from the carcass eigenfrequencies. Because the cuts sit only in the crown they can be molded with conventional sipes, avoiding the tooling surcharge associated with internal protrusions and keeping wet-grip drainage intact.
The outer shoulder is the most efficient acoustic radiator on a tyre. Asymmetric chamfered shoulder sipes attack that hot spot by trimming each shoulder sipe along its full length, but the chamfer volume decays toward the tread edge. The larger inner chamfer allows the block to flex for lateral grip whereas the smaller outer chamfer maintains edge rigidity. This blocks the high-frequency “flap” mode that radiates into the wheel well, delivering up to 0.8 dB(A) of additional pass-by improvement with no measurable wet-handling penalty.
Directional patterns are often chosen for marketing reasons even though their solid center rib is notoriously noisy. The curved variable-length lateral grooves in directional treads break up that rib without creating fluid-drainage shortcuts. Alternating convex lateral grooves of unequal span locally soften the crown, then narrow (under 2 mm) center sipes add further compliance. Complementary shoulder features—short lateral grooves that terminate early in the shoulder—smooth the impact force when the tyre rolls into contact. The result is a peak-noise slice of roughly 1 dB(A) relative to the baseline directional pattern while steering precision and directional stability are maintained.
Together these four geometries illustrate how contact-patch design can attack both amplitude and spectral placement, laying a foundation for the deeper material and system interventions that follow.
2. Compound-Level Energy Dissipation and Embedded Inserts
Once the mechanical source is tamed, the next lever is material damping. High-loss rubber or embedded inserts can turn vibratory energy into harmless heat before it is broadcast into the cabin. The rib-aligned damping strips place 1-3 mm-thick polyurethane or porous high-tan δ sheets directly beneath each longitudinal rib. Grooves between ribs interrupt the sheet, so the strips never coalesce into a stiff layer and can be laid on the building drum with the same sequence as a conventional undertread. Impact-borne shear waves are filtered before they reach the belt package, trimming exterior pass-by noise by about 1.2 dB(A) while wear and rolling resistance remain within statistical scatter of the reference tyre.
Chemical engineering can achieve the same goal with fewer parts. The organic-amine-functionalised medic-stone filler grafts dimethylamine groups onto porous mineral particles and disperses them in an EPDM matrix together with glass fiber and zinc-oxide whiskers. Static-DMA testing shows a high internal loss factor in the 100–400 Hz band, and field mileage confirms resistance to cutting and chunking. Compared with a silica-filled S-SBR control, the compound returns a 1.1 dB(A) lower ISO 13325 pass-by value while treadwear index remains unchanged.
Solid tyres on forklifts and industrial loaders emit structure-borne noise that open-shoulder passenger-car patterns rarely face. The waste-rubber–ceramic-fiber hybrid tread addresses the problem with a multi-phase matrix that includes epoxy-bonded crumb rubber, ceramic and silicon-carbide fibers, activated carbon, and expanded perlite. Dynamic-mechanical analysis shows a significantly lower storage modulus in the 150–600 Hz audio band yet no loss of compressive strength. Operators report a subjective 3-dB cabin-noise drop without sacrificing the puncture immunity expected from a solid tyre.
Moving inward, sensor mounts can be an unexpected noise source. A dual-modulus mounting zone stiffens the inner-liner rubber directly beneath the TPMS device while increasing the loss tangent of the overlying tread compound. The stiffness jump eliminates the “slap” of the electronics against the carcass, whereas the higher-loss tread smooths the abrupt modulus transition across speed and temperature. Direct A-weighted cabin measurements register a 0.5 dB reduction in the 180–260 Hz band that coincides with TPMS resonance.
The examples above show how properly placed damping, either in discrete inserts or via tailored polymer physics, complements geometric solutions and reduces the acoustic burden on downstream cavity treatments.
3. Groove-Level Aeroacoustic Resonators
Even with a well-behaved contact patch, the longitudinal grooves themselves can act as organ pipes. The folded C-spine expansion insert converts each groove into a train of miniature expansion chambers. A 2–3 mm-thick C-shaped spine bends at right angles and carries a modular sequence of SS, M, LL, S, and L ribs that alternate about the groove centerline. The mixed heights and lengths impose a broadband impedance mismatch, so the standing-wave gain is cut by more than 8 dB in a guarded microphone test while tread stiffness in braking remains statistically constant.
Where mold-integrated hardware is impractical for cost or SKU count, a retrofit layer can achieve comparable attenuation. The porous strip-based resonance-damping layer is bonded flush to the groove floor and contains A-shaped chambers or a central bore with inclined branch holes. Multiple reflections inside these passages transform viscous losses into broadband acoustic attenuation that measures 3–5 dB across 1⁄3-octave bands from 800 to 2000 Hz. Adhesive attachment eliminates secondary liners and does not interfere with water evacuation.
Some designs embed the resonator cavity inside the protrusion rather than on the groove floor. The self-healing muffler protrusion carries a sealed cavity packed with strip-shaped absorbers, an outer opening, and a circumferential airflow groove. Inner and outer coatings of self-healing rubber automatically close small punctures, retaining inflation pressure. Lab tests record a 1.4 dB(A) drop in external pass-by together with recovery from a 1.5-mm pinhole within 60 s.
Heavy off-road tyres must eject stones yet remain quiet during on-road transfers. The dual-purpose stone-ejector/anti-noise protuberance partitions each wide groove with a large main ejector and a smaller barrier closer to the groove wall. During on-road travel the smaller barrier interrupts the resonating air column while the larger one retains its stone-ejection role. A-weight pass-by drops by 1 dB on asphalt, whereas the number of retained stones after a standardized gravel loop falls by forty percent.
These groove-scale resonators filter cavity excitation before it even forms, reducing the workload of larger, heavier liners and foam rings.
4. Cavity Treatments: Bonded Foams, Free Assemblies, and Integrated Layers
4.1 Bonded Foam Strips and Continuous Bands
Where residual resonance persists in the toroidal air cavity, a bonded acoustic liner remains the workhorse. Early open-cell polyurethane pads absorbed well but absorbed water even better. The macrobubble polyolefin foam strip replaces open cells with closed macrobubbles of at least 1.5 mm. In ISO 10534-2 impedance-tube testing the strip matches the acoustic loss factor of PU yet shows less than 4 % weight gain after full immersion. Because the material neither swells nor embrittles, the adhesive can be lower-tack and easier to process.
Durability against centrifugal force improves when the element is gap-free. The continuous in-situ foamed polyurethane band is produced by spraying a reactive mixture into a rotating cured tyre so that it rises into a single annulus whose cross-section equals seven to twelve percent of the cavity area. Observed radial growth is under 0.2 mm at 300 km/h, and a molded-in density gradient suppresses drum-mode resonance without a brittle outer skin. Where imbalance control requires mass trimming, a variable-thickness single-stage insert alternates thick and thin sectors around the circumference; the butt joint hides in a thin section, which keeps static and couple imbalance under 5 g-cm.
Absorption bandwidth widens when air cavities coexist with porous matrices. The annular-hole cotton band forms a sealed 360-degree cavity that couples with thousands of micropores. Acoustic measurements show a 7 dB attenuation peak at 220 Hz plus 3 dB broadband loss out to 700 Hz. When puncture-sealant flow must be retained, a sponge whose outer surface carries flared longitudinal grooves lets liquids pass yet keeps the intervening lands acoustically active. Another tactic adds densely packed 5–10 mm projections to produce the multi-height topology, scattering cavity modes without added mass.
Heat and mass are the final constraints. A composite made of open-cell PU laced with hollow microspheres creates the ultralight foam-and-bead absorber that drops rotational mass by 3 % while keeping the cavity peak at bay. For high-speed applications, splitting the insert into two circumferential bands located away from the hottest tread lands, as in the dual-band layout, keeps tread temperatures down while still filling 10–40 % of the cavity volume. Carving through-grooves into the absorber surface, the ventilated groove matrix offers a tailored compromise between cooling airflow and structural adhesion.
4.2 Discrete Blocks, Panels, and 3-D Absorbers
Full-coverage liners are not mandatory if impedance can be placed strategically. The floating perforated panel resonator suspends a thin plate a set distance from the liner and concentrates at least 95 % of the perforations in that plate. The device weighs only a few grams yet cuts the first cavity mode by 6 dB in a drum test. Because the sidewalls of the device are solid, bonding integrity is preserved and the module can be located either on the tyre or on the rim.
A broader band is possible with discontinuous structures. The two-tier movable foam damper combines a thin continuous upper belt with spaced lower blocks. As the tyre deforms, the lower tier re-shapes, producing local impedance jumps, while the upper belt provides broadband absorption. Up to eighty percent of the lower tier is air, so weight falls and installation simplifies to a drop-in operation. A cousin concept is the circumferentially variable-impedance absorber that changes porosity or exposed area every few degrees, flattening the sharp 150–250 Hz peak instead of merely shifting it.
Three-dimensional modules go even further. The magnetically mounted concave-groove absorber uses a dome with a central trench and scatter-type protrusions; a built-in magnet snaps the module to a matching plate on the liner and leaves an additional gap that deepens low-frequency loss. Long-and-short beveled blocks alternate steep and gentle slopes; hook-and-loop fasteners plus an elastic ring allow repositioning. The film-supported cavity subdivision places two slim foam rings as standoffs for a perforated film, splitting the cavity into smaller volumes while consuming only twenty percent of the foam mass of a legacy liner. Finally, the flow-channeling cavity insert smooths the propagation pressure wave as the tyre enters and exits the contact patch, lowering the very airflow fluctuations that seed resonance.
4.3 Porous or Foamed Layers Formed During Vulcanization
Bond-on solutions add steps and adhesives. The built-in porous noise-damping layer lays a sheet containing a low-concentration blowing agent onto the building drum before the inner liner is applied. During vulcanization the agent activates, expanding to a density below 1.3 g/cm³, and co-cures with the liner. No adhesives are needed, splice lines disappear, and the porous layer can even be extended onto the sidewall. A-weighted drum measurements show up to a 4 dB cut at 225 Hz while mass savings offset the minor increase in compound cost.
When tread rigidity must be preserved, only the lower twenty percent of the tread is foamed. The micro-foamed lower tread uses 0.5–5 µm cells at one to five percent porosity to create a broadband absorber that lives beneath the cap tread. Because the foam layer remains 2–6 mm thick and at least one Shore A softer than the overlying rubber, the compound detunes the cavity resonance without softening the blocks that deliver steering.
A middle-path solution bonds a porous insert deeper in the carcass. The porous shock absorber with rough topography is laid on the carcass before vulcanization so that it cures into a structural ply. Its open-cell matrix converts acoustic energy into heat, and its intentionally rough upper surface scatters reflections. Positioned between two shock-absorbing layers, the insert damps belt, sidewall, and cavity vibration simultaneously and eliminates any post-cure balancing step.
5. Rim and Wheel Assemblies for Broadband Suppression
The tyre is only half of the acoustic system; the rim features prominently in the transmission path. The road-noise-reducing wheel and tyre assembly bonds one or two layers of open-cell honeycomb metamaterial to the rim barrel. Cell size ranges from 1 to 10 mm, and the structure can be skinned with an elastomeric membrane whose negative effective mass reflects low-frequency energy. A vented Helmholtz resonator molded into a rim groove targets the 200–250 Hz band, while optional polyurethane foam inside the tyre suppresses higher frequencies. A two-layer prototype shows 20–35 dB transmission loss from 50 Hz to 2 kHz, translating to a 50–70 % drop in perceived interior noise without increasing wheel moment of inertia.
Electric-vehicle cabins are so quiet that residual tyre cavity modes become obvious. The inflatable cavity-partition system converts the single toroidal cavity into multiple sealed chambers. Fabric-reinforced polyurethane baffles are plumbed to a circumferential airline; once pressurized they expand and press airtight lips against the inner liner, breaking up resonance paths. Because the baffles can be inflated or deflated on demand, the system adapts to temperature, tyre wear, or driver preference. Mass is negligible compared with solid inserts, yet a four-baffle setup shifts the dominant 220 Hz peak downward into a less audible 150 Hz band while trimming the original amplitude by half.
These rim-level interventions complete the acoustic chain by addressing radiation paths that originate outside the tyre sidewalls, allowing OEMs to define holistic NVH packages at the wheel-assembly level.
6. Manufacturing, Application, and Durability Enablers
Innovative noise solutions will not reach production unless they can be placed accurately, bonded reliably, and survive heat and centrifugal load. The two-stage alignment-and-compacting applicator first corrals individual absorber pads into a datum line and then gently compresses them until all gaps close before the adhesive film is applied. Advancing the entire array after lamination shears the film cleanly, delivering perfectly coated pads to the tyre. In the next workstation a camera-guided selective deposition workflow scans the inner liner, maps TPMS and RFID exclusion zones, and drives the glue head only within permitted arcs. Scrap falls to near zero and positional repeatability is inside ±1 mm.
Adhesive chemistry is equally critical. The silane-terminated polyacid polyurethane adhesive combines a rubber-like backbone with alkoxysilane end groups that cross-link into siloxane networks. Peel strength exceeds 2 N/mm after 700 h at 90 °C, yet viscosity remains low enough that the adhesive does not wick far into open-cell foams and block pores. If residual silicone release agent threatens adhesion, an inner-liner laser activation protocol selectively ablates or textures 20–80 % of the liner surface. The resulting micro-anchors withstand full-speed endurance tests without delamination.
Mechanical retention options grow more sophisticated at high speed. A rib-stiffened thermoplastic band replaces bulk thickness with continuous ribs that raise bending rigidity and prevent stress hot spots. For speeds beyond 300 km/h, the band may be enclosed in an over-wrapped heat-resistant reinforcing sleeve whose ends are stitched to the band through locking holes so that no circumferential slip occurs once the resin softens.
Temperature control measures backstop the entire system. The contact-area-controlled protrusion geometry raises the band off the liner on chamfered ribs so that only 10–80 % of the projected area touches rubber. Air gaps cut conductive heat flow and keep thermoplastic yield strength intact. On the tread side, a cyclic-polysulfide-stabilized tread compound resists oxidative ageing beneath thick acoustic strips. The dosage of stabilizer is matched to strip thickness so that grip, rolling resistance, and noise targets are met simultaneously over the full tyre life.
These process and durability enablers ensure that the acoustic technologies described in earlier sections survive the brutal combination of temperature, centrifugal force, moisture, and mechanical abuse that real roads deliver.
Get Full Report
Access our comprehensive collection of 158 documents related to this technology
Identify Key Areas of Innovation in 2025
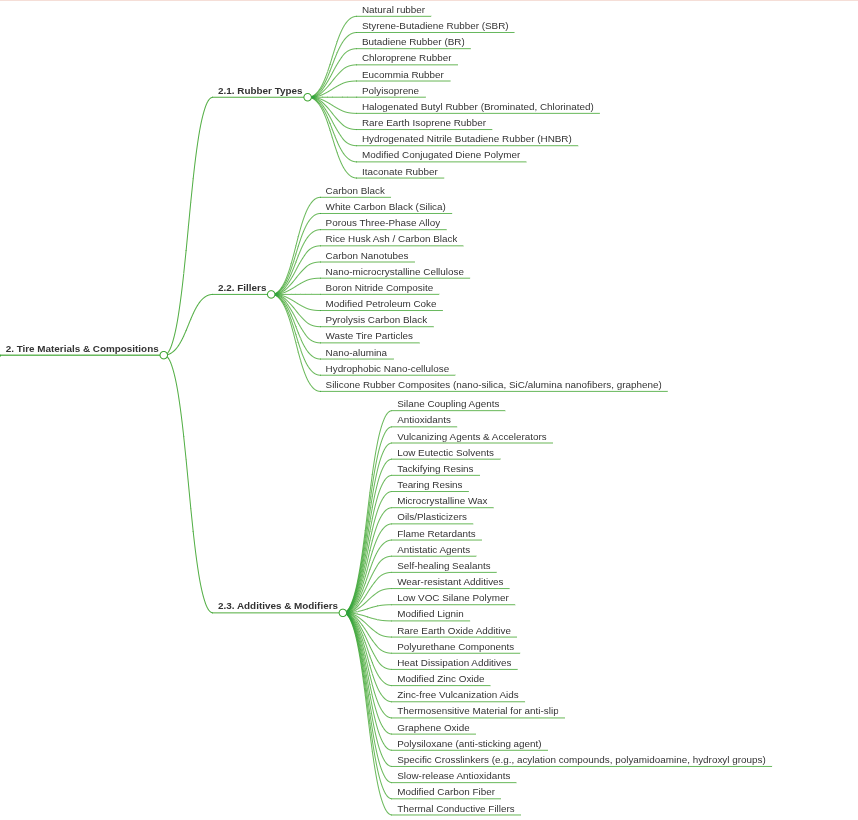