Tire Material Response Analysis
Modern tire development requires understanding material behavior across complex loading conditions, temperature ranges, and wear states. Testing shows that rubber compounds exhibit non-linear viscoelastic responses, with loss tangents varying significantly under different strains and frequencies. Contact patch dynamics alone involve interactions between longitudinal forces exceeding 4000N and lateral forces up to 3500N during typical passenger vehicle operation.
The fundamental challenge lies in accurately modeling the complex interactions between tire deformation, contact mechanics, friction, and thermal behavior while maintaining computational efficiency in simulation environments.
This page brings together solutions from recent research—including physics-based force prediction models, advanced finite element approaches that account for residual stresses, and hybrid simulation methods that combine physical testing with computational modeling. These and other approaches focus on improving the accuracy of tire performance predictions while reducing development time and costs.
1. Vehicle Motion Control Method Incorporating Tire Parameter Estimation and Model-Based Rolling Resistance Analysis
VOLVO TRUCK CORP, 2024
Optimizing vehicle motion control to improve energy efficiency by considering tire parameters. The method involves estimating tire parameters like rolling resistance, wear rate, etc based on input data. A tire model is configured using these parameters to relate tire behavior to vehicle motion. This allows estimating effects like rolling resistance for different control strategies. The vehicle is then moved using the tire model to select options with lower rolling resistance for better efficiency.
2. Method for Simulating Tire Sidewall Fatigue Life Under Flexural Deformation Using Computational Modeling
ZHONGCE RUBBER GROUP CO LTD, 2024
A method to simulate and calculate fatigue life of tire sidewalls under flexural deformation. The method involves modeling tire sidewall flexure using simulation software like Abaqus. The simulation captures different deformation amounts and the entire flexure process. Fatigue life calculation is done using software like Endurica. The simulation output provides parameters like stress, strain, Mises stress, fatigue life for analyzing tire sidewall flexural fatigue.
3. Method for Predicting Tire Cornering Characteristics Using Model-Based Normalization of Reference Tire Data
HANGZHOU HAICHAO RUBBER CO LTD, ZHONGCE RUBBER GROUP CO LTD, 2024
A method to predict tire cornering characteristics without physical testing. The method involves modeling and normalizing tire side slip data from a reference tire, then applying target tire properties to generate predicted cornering behavior. It allows estimating tire cornering forces and moments without full finite element analysis or physical testing, using reference tire data. The steps are: 1) Select a reference tire with similar size to the target tire. 2) Normalize the lateral force and self-aligning torque data from the reference tire. 3) Model the normalized curves to obtain functions. 4) Substitute the target tire's sidewall stiffness and lateral dynamic friction coefficient into the side slip prediction model. 5) Use the modeled functions with the target tire properties to predict the normalized lateral force and self-aligning torque.
4. Vehicle Dynamics Model Incorporating Real-World Trained Tire Data for Force Estimation
HUAWEI TECH CO LTD, HUAWEI TECHNOLOGIES CO LTD, 2024
Constructing a vehicle dynamics model that accurately reflects the dynamic performance of a vehicle. The method involves introducing a tire data model that is trained using real-world driving data. The tire data model generates tire force estimates. These are fused with forces calculated by a tire mechanism model and then fed into the whole vehicle dynamics model. This allows the vehicle dynamics model to be built using real-world tire forces, resulting in more accurate simulation of vehicle behavior.
5. Neural Network-Based Inversion of Tire Material Parameters from Stiffness Test Data
CITIC Dicastal Co., Ltd., Beihang University, CITIC DICASTAL CO LTD, 2023
A method and system for reversing tire material parameters to improve wheel performance simulation accuracy. The method involves using neural networks to invert tire material properties from experimental tire stiffness test data. It involves steps like tire stiffness testing, neural network training, and verification. The neural network has input variables like tire dimensions and load-displacement curves. It outputs the tire material parameters. This allows rapid, data-driven inversion of tire properties for wheel simulation instead of destructive testing.
6. Static Loading Simulation Method for Evaluating Shear Strain-Induced Delamination in Radial Truck Tire Crowns
GUANGRAO COUNTY METROLOGY AND TESTING INSTITUTE, GUANGRAO COUNTY METROLOGY AND TESTING INSTITUTE GUANGRAO COUNTY PRODUCT QUALITY INSPECTION CENTER GU, TECHKING QINGDAO SPECIAL TIRE TECH RESEARCH AND DEVELOPMENT CO LTD, 2023
Simulation method to evaluate delamination damage performance in the crown of radial truck tires. The method involves static loading simulation to obtain tire geometry, and using the amplitude of shear strain in the center rubber versus the outer belt as an evaluation index for crown delamination. By simulating and analyzing shear strain in the tire crown, the method allows optimizing tire design to improve longevity and prevent premature delamination failure.
7. Finite Element Analysis System for Tires with Iterative Element Optimization and Force Analysis
DEZHOU LINGLONG TIRE CO LTD, SHANDONG LINGLONG RUBBER TECH CO LTD, SHANDONG LINGLONG RUBBER TECHNOLOGY CO LTD, 2023
A finite element analysis system for tires that improves tire performance by optimizing the finite element division, force analysis, and optimization steps. The system analyzes tire characteristics, optimizes element categories, builds element models, analyzes forces, optimizes elements again using durability prediction, and adjusts tire geometry to evenly distribute ground pressure. This iterative finite element analysis process aims to optimize tire wear, rolling resistance, and pass rate by analyzing and improving the finite element units that make up the tire.
8. Finite Element-Based Tire Simulation Method with Material Property Assignment
TOYO TIRE CORP, 2023
Tire simulation method that can be used for new products, etc. The method includes creating a tire model by dividing a tire into finite elements; assigning material property values to the tire model; and evaluating the tire model.
9. Tire Force Prediction System Utilizing Longitudinal and Lateral Slip Analysis with Incremental Time Step Calculation
GM GLOBAL TECHNOLOGY OPERATIONS LLC, 2023
Tire force prediction for integrated motion control in a motor vehicle that minimizes cost and complexity, improves simplicity, and provides increased redundancy and robustness. The prediction involves analyzing vehicle and tire characteristics in terms of longitudinal and lateral slip, and calculating tire force behavior in both linear and nonlinear regions at incremental time steps.
10. Real-Time Tire Force Estimation via Circumferential Strain Signal Analysis and Support Vector Regression
ROCKET FORCE UNIV OF ENGINEERING OF PLA, ROCKET FORCE UNIVERSITY OF ENGINEERING OF PLA, 2023
Accurately estimating tire vertical force and cornering force in real-time using strain analysis inside the tire. The method involves extracting features from the circumferential strain signal of the tire inner liner to characterize ground contact angle and length. By inputting these features into a support vector regression model, it estimates vertical force. Then, combining the cornering force features with the vertical force estimate allows accurate estimation of both forces during cornering. The method provides an alternative to indirect tire force estimation using sensors that is more accurate and applicable to various tire conditions.
11. Fatigue Life Prediction Method for Non-Pneumatic Tires Using Thermo-Mechanical Coupled Extended Finite Element Analysis
YANGZHOU UNIV, YANGZHOU UNIVERSITY, 2023
A method to predict the fatigue life of non-pneumatic tires using finite element analysis. The method involves modeling the tire structure and materials, simulating thermal-mechanical coupling during tire deformation, and using extended finite elements to predict crack growth. It accounts for temperature effects and fatigue failure mechanisms. The simulation steps include: 1) thermal analysis to determine high temperature areas, 2) meshing and crack initiation in those regions, 3) transferring temperature from the thermal analysis, 4) using extended FEM to calculate crack growth rate, and 5) predicting fatigue life based on crack propagation.
12. Heavy-Duty Tire Vertical Force Estimation via Circumferential Strain Sensor Data and Support Vector Machine Model
ROCKET FORCE UNIVERSITY OF ENGINEERING OF PLA, UNIV ROCKET FORCE ENGINEERING PLA, 2022
Estimating the vertical force of heavy-duty tires using circumferential strain analysis, which involves installing strain sensors in the tire tread center to measure deformation as the tire rolls. A support vector machine model is trained using finite element simulation data to predict tire vertical force based on the measured strain. The strain features, like ground contact angle and length, are identified as indicators of force. This provides a more direct and accurate way to estimate tire force compared to using acceleration or tire models, as it avoids issues like noise sensitivity and simplified tire dynamics.
13. Method for Determining Tire Component Stiffness via Force-Displacement Analysis from Static Loading Data
ANHUI GITI RADIAL TIRE CO LTD, 2022
Indirectly measuring tire component stiffness like carcass and tread stiffness by analyzing tire force-displacement data from static loading tests. The method involves calculating stiffness values for tire components like tread and carcass separately instead of just overall tire stiffness. It accounts for road friction and zero point offsets to accurately obtain component stiffness from test data. The method involves defining stiffness as the ratio of force increment to displacement increment at specific points rather than just approximating from segments.
14. Method for Characterizing Tire Wear Resistance via Tan Delta Peak Temperature in Dynamic Mechanical Analysis
HANGZHOU HAICHAO RUBBER CO LTD, ZHONGCE RUBBER GROUP CO LTD, 2022
A method to characterize tire wear resistance using dynamic properties of the tire compound. The method involves measuring the temperature at which the tan delta (loss tangent) peaks in dynamic mechanical analysis (DMA) for the tire compound. The higher the temperature of the tan delta peak, the better the tire wear resistance. This provides a simple and faster way to evaluate tire wear compared to traditional wear testing methods like Lambourn abrasion.
15. Finite Element Tire Model with Iterative Material Property Calibration for Reduced Computational Complexity
CHINA FAW GROUP CORP, 2022
A method to create a finite element tire model that can accurately simulate tire dynamics for complete vehicle simulations. The method involves modeling the tire using fewer units and iteratively calibrating the material properties to match real tire rigidity. This reduces the computational resources needed compared to traditional finite element tire models. The iterative calibration involves setting the sidewall material as a variable and optimizing the rigidity in each direction. By calibrating the tire rigidity, the model's performance in each direction matches within 5-15% of actual tire rigidity.
16. Finite Element Analysis Method for Identifying Tire Failure Points Based on Stress and Strain Concentrations
ZHONGCE RUBBER GROUP CO LTD, 2022
Simulation method to analyze tire failure points for tire design optimization. The method involves using finite element analysis (FEA) to simulate tire deformation and stress under different loading conditions. It specifically focuses on identifying potential failure points based on localized regions with high stress or strain concentrations. By analyzing these areas, designers can identify design features that may contribute to tire failures and make improvements to prevent them. The simulation allows analysis of complex tire materials and geometries without the need for physical testing, reducing cost and time.
17. Method for Calculating Tire Rolling Resistance Based on Rubber Modulus Using Combined Simulation and Theoretical Model
HANGZHOU HAICHAO RUBBER CO LTD, ZHONGCE RUBBER GROUP CO LTD, 2022
A method for quickly calculating the influence of rubber material modulus on tire rolling resistance. The method combines simulation and theory to calculate the effect of modulus on rolling resistance. It allows faster determination of optimal material modulus for tire components compared to repeated simulation or experimental testing. The method involves calculating a rolling resistance coefficient for each component using a theoretical model. Then, using simulation, calculating rolling resistance for a baseline tire with known modulus values. Substituting the component rolling resistance coefficients into the theoretical model, adjusting modulus values for each component, and recalculating rolling resistance using simulation to find the optimal modulus combination.
18. Method for Analyzing Rubber Modulus Influence on Tire Rolling Resistance via Refined Deformation Index Decomposition
HANGZHOU SEA TIDE RUBBER LIMITED CO, HANGZHOU SEA TIDE RUBBER LTD CO, JIANGZHOU RUBBER GROUP LIMITED CO, 2022
Method to analyze the degree of influence of rubber modulus on tire rolling resistance, by refining and decomposing the deformation index. The method involves calculating a modified deformation index for each tire component by considering both strain and stress control. This provides a clear indication of how to adjust the rubber modulus of each tire part to reduce rolling resistance. The refined deformation index takes into account mixed deformation states where strain and stress control are both present. It helps tire designers make informed decisions about rubber compound choices for optimal rolling resistance.
19. Dynamic Impact and Residual Tear Strength Testing Method for Evaluating Tire Carcass Material Explosion-Proof Performance
GUIZHOU UNIVERSITY, UNIV GUIZHOU, 2022
Simple pre-testing method to evaluate the explosion-proof performance of carcass materials in tires without needing to make and test entire tires. The method involves subjecting tire carcass samples to dynamic impact testing using falling balls, followed by tear testing to measure residual tear strength. The residual tear strength and microstructure after impact are used as indicators of explosion-proof performance. This provides a quick and easy way to assess carcass material resistance to repetitive impact forces, which is important for run-flat tire carcasses.
20. Two-Dimensional Stiffness Model for Heavy-Duty Tire Sidewall with Coupled Radial and Tangential Deformation Analysis
CHINESE PEOPLE LIBERATION ARMY ROCKET ARMY ENGINEERING UNIV, CHINESE PEOPLE LIBERATION ARMY ROCKET ARMY ENGINEERING UNIVERSITY, 2022
Modeling the two-dimensional stiffness of the sidewall of a heavy-duty tire with a large aspect ratio and analyzing the deformation characteristics of the tire. The method involves establishing a low-frequency dynamic model of the flexible ring tire based on an analytical elastic foundation, and deriving the radial and tangential two-dimensional sidewall stiffness. The model considers the coupling between radial and tangential deformation of the carcass ring, accurately characterizes tire deformation, and solves ground contact issues by introducing grounding springs.
Get Full Report
Access our comprehensive collection of 93 documents related to this technology
Identify Key Areas of Innovation in 2025
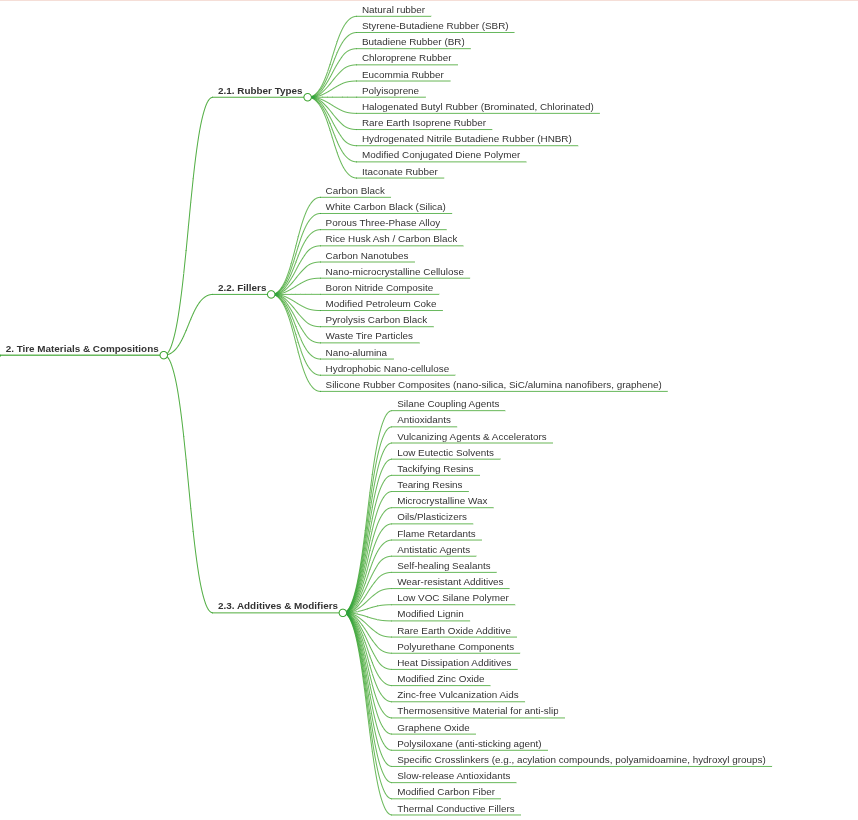