Pyrolytic Oil Recovery from Recycled Tires
Tire pyrolysis oil (TPO) contains valuable hydrocarbons but presents significant processing challenges due to its high sulfur content (typically 0.8-1.4 wt%), heterogeneous composition, and presence of contaminants. Current valorization methods achieve oil yields of 45-50% by weight, but the resulting products often require extensive upgrading before commercial use.
The fundamental challenge lies in efficiently converting a complex, contaminated feedstock into standardized fuel products while maintaining economic viability at industrial scale.
This page brings together solutions from recent research—including catalytic hydroprocessing techniques, multi-stage distillation systems, microwave-assisted pyrolysis, and integrated waste processing approaches. These and other methods focus on producing market-ready fuels and chemical feedstocks while addressing both technical and economic constraints.
1. Continuous Pyrolysis Device with Pneumatic Tire Chip Feeding and Oil Film Gas Condensation
ENTOP TECHNOLOGY CO LTD, 2025
Continuous low-temperature pyrolysis device that efficiently converts waste tires into useful products like carbon black and oil. The device uses pneumatic feeding of waste tire chips into the reactor instead of mechanical conveyors to prevent air introduction. It also condenses the pyrolysis gas to extract oil by forming an oil film inside the condensation chamber. This increases condensation efficiency and allows higher quality oil extraction. The carbon black is recovered by vacuum suction instead of conveyors for compactness. The modularized design enables compact pyrolysis facilities with reduced footprint, cost, and maintenance compared to conventional systems.
2. Waste tire-based pyrolysis for synthetic fuel and study of its properties
abdugaffor khurmamatov, kumush shakhobiddin kizi akhmedova, giyosiddin o sidikov - The Oil and Gas Institute - National Research Institute, 2025
Thermal pyrolysis of waste tires is an economically viable industrial method for material recovery and energy production. This article presents the results research on processing used car by in a nitrogen-free environment under atmospheric pressure. Tires sourced from local vulcanization center were as raw material. The process was conducted using experimental setup consisting reactor, collector gases liquids, condenser. For experiment, 4180 g tire fragments used. carried out at temperature 500C pressure one hour. As result, 1800 ml oil, 1320 carbon black, 600 metallic cord, 630 gas obtained. physical properties oil studied: density 0.906 kg/m3, kinematic viscosity 0.75 mm2/s, acidity 104.4 mg/dm3. Infrared spectroscopy analysis revealed presence aromatic, alkene, alkyne groups. Liquid fuel obtained distillation unit. From 150 60 liquid produced. Elemental indicated that contained nitrogen (2.57%) sulfur (1.27%).
3. Development and Characterization of KOH-Activated Carbons Derived from Zeolite-Catalyzed Pyrolysis of Waste Tires
camila aguilarccuno, rossibel churata, kattia martinez - Multidisciplinary Digital Publishing Institute, 2025
This study focuses on the production and characterization of activated carbons derived from carbonaceous residue obtained through catalytic pyrolysis waste tires. A process was conducted at 450 C 575 C, employing two zeolitic catalysts, commercial ZSM-5 a synthesized zeolite (PZ2), developed natural pozzolan, which played key role in performance quality resulting carbons. After pyrolysis, solid residues were chemically using KOH to improve their porous structure surface characteristics. Comprehensive carried out, including textural properties (BET area porosity) morphological (SEM) analysis carbons, as well crystallinity evaluation (XRD) catalysts. The BET areas PZ2-T1-AK PZ2-T2-AK reached 608.65 m2/g 624.37 m2/g, respectively, values that surpass those reported for similar materials under comparable activation conditions. suggests strong potential applications adsorption processes, pollutant removal. These findings demonstrate effectiveness zeolite-catalyzed particularly PZ2, sustainable strategy transforming tire into high-performance adsorbent materials. approach supports circ... Read More
4. Pyrolysis Furnace with Dual Screws Featuring Notched Blades and Integrated Heating System
MIN-CHEN SHIUE, 2025
Pyrolysis furnace with upper and lower screws for efficiently converting waste tires into oil and gas. The furnace has two screws, one on top and one below, that rotate simultaneously. The screws have blades with notches forming fin-like protrusions. This allows the screws to both convey the waste tire feedstock and agitate it simultaneously. The upper screw feeds the waste tires into the furnace, the lower screw extracts the pyrolysis products. The screws have heating around them to thermally crack the tires. The upper and lower screws smoothen the cracking process and reduce back pressure. The fin-like protrusions agitate the feedstock for increased conversion efficiency.
5. Obtaining New Materials from Liquid Pyrolysis Products of Used Tires for Waste Valorization
serhiy pyshyev, bohdan korchak, d v miroshnichenko - Multidisciplinary Digital Publishing Institute, 2025
The innovative recycling of waste tires into fuel is essential for promoting sustainable development, enhancing valorization, and advancing waste-to-energy technologies. For the processing fr. 200 C, separated from liquid products pyrolysis process tires, polycondensation with formaldehyde extraction a polar solvent (N-methyl-2-pyrrolidone) was used. Due to sequential application these processes, raffinate product produced that contains significantly fewer undesirable compounds, such as reactive unsaturated hydrocarbons aromatics, which can negatively affect gasoline. Additionally, this demonstrates chemical stability during storage. its operational properties, obtained serve high-quality component gasoline production, advisable when mixed low-octane gas condensate. As result compounding, Euro 4 an octane number equal 93 according experimental method. possibility effectively using extract (concentrate aromatic compounds) plasticizer waterproofing mastic shown. Overall, valorization tire contributes reduction consistent industrial innovation by replacing primary petrochemical fe... Read More
6. Rubber waste tyre: Effect of temperature on pyrolysis char yield and properties
tung thanh ho, 2025
Abstract. Waste tyre pyrolysis is a viable technology to convert tyres into useful products such as oil, fuel and gas. Most of the research focus on investigating effect operating parameters oil product. With increasing applications solid char produced, it found that no detailed investigation temperature yield properties. Thus, this project aimed determine tyre- derived A total three samples were produced from rubber crumb, namely Char400, Char550 Char700, corresponding their at 400C, 550C 700C respectively. Rubber crumb these 3 sent Fourier Transform Infrared Spectroscopy (FTIR), Elemental analysis carbon, hydrogen, nitrogen sulphur (CHNS), Scanning Electron Microscopy (SEM) Brunauer-Emmett-Teller (BET) for characterization purposes. It was 400C led significant reduction 76% 36.25%. In terms composition, Char400 has additional alkane phenol functional groups indicating main constituents in did not decompose completely low temperatures. Furthermore, higher temperatures lower carbon content, specific surface area, average pore width more structured morphology. Overall, affects... Read More
7. Microwave-Assisted Surface Devulcanization Process for Recycling Waste Tires into Rubber Compounds
1307843 BC LTD, 2025
Recycling waste tires into useful rubber compounds using microwave-assisted surface devulcanization. The process involves separating metal and fibers from waste tires, micronizing the vulcanized crumb rubber, applying a dose of microwave energy to sever sulfidic crosslinks, mixing the devulcanized rubber with plastic and oil, and extruding it to produce recycled rubber compounds like crumb rubber or end-of-life tire compounds. The microwave devulcanization step enables efficient recycling of waste tires without harsh solvents or chemical compatibilizers.
8. Multi-Step Process for Chemical Production and Carbide Recovery from Waste Tires via Pyrolysis, Hydrogenolysis, and Steam Cracking
ENEOS Corporation, Bridgestone Corporation, 2025
Efficient production of chemical products and carbides from waste tires using a multi-step process involving pyrolysis, hydrogenolysis, and steam cracking. The process involves pyrolyzing crushed tire waste to obtain a gas fraction, oil fraction, and residual fraction. The carbide is recovered from the residual fraction. The oil fraction is hydrogenolysis to produce a light fraction and heavy fraction. The heavy fraction is steam cracked to create chemical products and a new carbide feedstock. This allows efficient conversion of tire waste into useful chemical products while recovering carbide as a byproduct.
9. Two-Step Hydrogenation Process for Waste Tire Pyrolysis Oil with Sequential High and Low Pressure Catalytic Treatment
LUOYANG AOHONG PETROCHEMICAL ENGINEERING TECH CO LTD, LUOYANG AOHONG PETROCHEMICAL ENGINEERING TECHNOLOGY CO LTD, 2024
Hydrotreatment process for waste tire pyrolysis oil that overcomes issues like high diolefin content, high sulfur, nitrogen, and chlorine levels. The process involves a specific sequence and catalyst to enable hydrogenation of waste tire pyrolysis oil. It includes mixing the pyrolysis oil with hydrogen at high pressure (15 MPa or more) to hydrogenate the oil. This is followed by a second mixing step with hydrogen at lower pressure (5 MPa or more) using a different hydrogenation catalyst. This two-step hydrogenation sequence allows effective hydrogenation of the oil without deactivating the catalyst due to sulfur and nitrogen levels.
10. Process for Hydroprocessing and Distillation of Pyrolysis Oil from Waste Tires with Hydrogen Recirculation and Power Generation
WASTEFRONT AS, 2024
Economically recovering desulfurized fuel oil and fuel gas from waste tires by using a combination of hydroprocessing and distillation. The process involves hydroprocessing the pyrolysis oil from tires to desulfurize it. The hydroprocessed oil is then distilled into multiple fuel products like kerosene, naphtha, fuel oil, fuel, and diesel. The hydrogen demand of the hydroprocessing is met by recirculating hydrogenated material. The excess fuel gas from pyrolysis is used to generate power. The power production from byproducts and electrolytic hydrogen production from the low-cost power co-produced further reduces costs.
11. Integrated Process for Impurity Removal in Mixed Pyrolysis and Renewable Oils via Selective Hydrogenation and Hydrodemetallation
IFP ENERGIES NOUVELLES, IFP ENERGIES NOW, 2023
Simultaneous processing of feedstocks containing pyrolysis oil from plastic waste and renewable resource oils to remove impurities and prepare them for further refining. The process involves steps like selective hydrogenation, hydrodemetallation, and hydrotreating. It allows converting the feedstocks into cleaner products suitable for integration into existing refineries. The steps are done at elevated temperatures and hydrogen pressures to minimize gum formation. This enables handling the pyrolysis oil without clogging issues. The method reduces impurities like dienes, metals, metalloids, chlorine, and sulfur to levels compatible with refinery units.
12. Process for Refining Pyrolysis Oil into High-Quality Light Oil via Pre-Treatment, Heavy Oil Stripping, Hydrocarbon Cracking, Fractional Distillation, and Filtration
CHO SANG TAE, 2023
Refining high-quality light oil from pyrolysis oil to make it versatile as fuel. The process involves pre-treating the pyrolysis oil to remove impurities, stripping out heavy oil, cracking the remaining hydrocarbons, fractionally distilling the cracked oil, and filtering the final light oil to purify it. This refining method converts pyrolysis oil into high-quality light oil suitable as a general-purpose fuel.
13. Phase Separation Process for Impurity Reduction in Pyrolysis Oil Using Aqueous and Hydrocarbon Treatments
Refinitiv Ltd., REFINITI LTD, 2023
Upgrading pyrolysis oil from plastic and rubber waste to produce a higher quality fuel with reduced impurities like olefins, solid residues, and heteroatoms. The process involves treating the pyrolysis oil with an aqueous solution and optionally a hydrocarbon fluid to separate into phases. The organic phase is then separated and filtered to obtain the upgraded pyrolysis oil with reduced impurities compared to the original oil. This allows using the upgraded oil as transportation fuel, blending with other fuels, or as a chemical feedstock. The aqueous solution helps extract impurities from the pyrolysis oil into the water phase. The hydrocarbon fluid assists separation and reduces solid residues.
14. Pyrolysis and Hydrocracking Process for Deriving Chemical Products and Carbides from Waste Tires
BRIDGESTONE CORP, ENEOS CORP, 2023
Method for efficiently producing chemical products and carbides from waste tires. The method involves pyrolyzing crushed tires to obtain a gas, oil, and residue. Then, hydrocracking the tire oil to separate light and heavy fractions. The heavy fraction is steam cracked to make chemical products and carbide feedstock. The carbide is made by thermal decomposition or incomplete combustion of the carbide feedstock. This allows efficient extraction of both chemical products and carbides from waste tires.
15. End-of-Life Tire Pyrolysis with Subsequent Hydrorefining for Contaminant Removal
ITELYUM REGENERATION S P A, ITELYUM REGENERATION S.P.A, 2023
A process for disposing of end-of-life tires (ELT) that provides complete reuse without environmental problems. The process involves pyrolyzing the tires to produce pyrolysis oil. The pyrolysis oil is then subjected to hydrorefining to improve its quality and make it suitable for substituting fossil fuels in industrial processes. This allows converting the tires into a valuable product instead of burning them or landfilling them. The hydrorefining step removes impurities like rubber fines and contaminants to produce a cleaner, more useful oil.
16. Method for Co-Pyrolysis of Waste Tires and Polyolefin Plastics in Anaerobic Conditions
GUANGZHOU INST OF ENERGY CONVERSION CHINESE ACADEMY OF SCIENCES, GUANGZHOU INSTITUTE OF ENERGY CONVERSION CHINESE ACADEMY OF SCIENCES, 2023
A method to co-pyrolyze waste tires and waste polyolefin plastics in an anaerobic environment to produce low-oxygen high-quality pyrolysis oil. The method involves mixing the waste tire and waste polyolefin plastics in a 1:1-10 mass ratio, heating them at 400-800°C for 10-60 seconds, and collecting the liquid phase pyrolysis product. The co-pyrolysis of waste tires and waste polyolefin plastics significantly reduces the oxygen content in the pyrolysis oil, improves the yield and quality of the pyrolysis oil, and expands the relationship between waste tires and waste plastics. It provides a coordinated recycling solution for harmless treatment of waste tires and waste plastics while reducing carbon emissions.
17. Pyrolysis Oil Refinement via Secondary Cracking with Integrated Flashing, Washing, Condensation, and Separation
Guangdong Guoyu Equipment Co., Ltd., 2022
Upgrading pyrolysis oil from organic waste cracking to improve quality and enable deeper processing. The process involves secondary cracking of the pyrolysis oil and water mixture to separate and upgrade the pyrolysis oil. The secondary cracking involves flashing, washing, condensation, and separation to remove impurities and produce refined oil. This improves the quality of the pyrolysis oil compared to direct sale of the mixed condensate.
18. Pyrolysis-Based Rubber Shavings Recycling with Fractional Olefin Monomer Isolation for Resin Production
COMPAGNIE GENERALE DES ETABLISSEMENTS MICHELIN, MICHELIN & CIE, 2022
Process for recycling rubber shavings from end-of-life tires into resins that can be used in tire production without degrading tire performance. The process involves pyrolysis of the rubber shavings to generate an oil containing olefinic monomers. The oil is then separated into fractions, with the intermediate fraction containing the desired monomers. This fraction is polymerized to form the resins. The process conditions are optimized to maximize monomer yield from the shavings. The resulting resins can be used in tire manufacturing without negatively impacting tire performance.
19. Method for Producing Oil from Waste Tires via Ammonia Pyrolysis and Dichloromethane Extraction
NANJING FORESTRY UNIVERSITY, UNIV NANJING FORESTRY, 2021
A method for producing high-quality oil from waste tires by pyrolysis, separation, and refining. The method involves crushing the waste tires, pyrolyzing them in an ammonia atmosphere under pressure, separating the resulting liquid mixture, and refining the crude oil. The pyrolysis step is done at 425°C for 2 hours. The separation involves cooling and extracting with dichloromethane. The refining step involves hydrogenation with a catalyst and tetrahydronaphthalene. This results in high-quality oil with properties similar to industrial grade oil.
20. Pyrolysis-Derived Marine Fuel from Waste Rubber with Specified Physical and Chemical Properties
YANCHEP TECH LTD, YANCHEP TECHNOLOGY LTD, 2021
Pyrolysis of waste rubber like tires to make fuel products that can be used in marine applications. The fuel has specific properties like flash point, boiling range, density, acid number, styrene content, and halogen content. The fuel is derived from pyrolyzing rubber and separating the oil. The pyrolysis conditions are 400-550°C, 1-4 hours residence time, and negative pressure. The oil is then centrifuged to remove solids before separation. The fuel has a flash point above 40°C, boiling point above 140°C, density below 990 kg/m3, acid number below 12, styrene below 7000 ppm, and halogen below 50 mg/kg.
Get Full Report
Access our comprehensive collection of 40 documents related to this technology
Identify Key Areas of Innovation in 2025
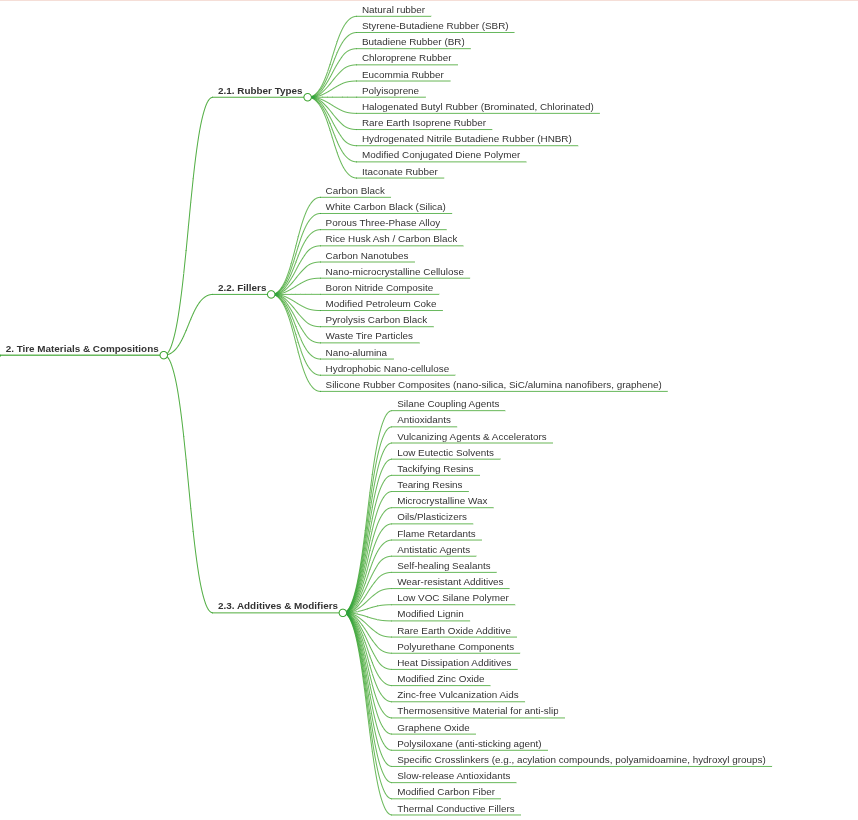