Coating Uniformity Methods for EV Batteries
In modern EV battery manufacturing, electrode coating uniformity directly impacts cell performance and longevity. Current coating processes face challenges maintaining consistent material distribution, particularly at edges and curved regions where thickness variations of just 2-3 microns can lead to local capacity imbalances and accelerated degradation.
The fundamental challenge lies in achieving uniform coating density and thickness across the entire electrode surface while maintaining high-speed production and preventing material waste.
This page brings together solutions from recent research—including progressive coating mass distribution techniques, specialized edge treatments, functional interlayers, and optimized electrolyte formulations. These and other approaches focus on practical manufacturing methods that enhance coating uniformity while preserving production efficiency and cell performance metrics.
1. Electrode Material Coating Method Using Precursor Mixing, Ball Milling, and Sintering
JINAN ZRT NEW MATERIAL TECH CO LTD, JINAN ZRT NEW MATERIAL TECHNOLOGY CO LTD, 2024
A simple and efficient method to coat electrode materials for lithium-ion batteries to improve stability and cycle life. The method involves mixing the electrode material with a coating precursor like dicyandiamide or PVDF in a solvent, ball milling it, and then sintering to form a uniform coating layer on the electrode surface. This coating provides a stable interface and suppresses electrode reactions with the electrolyte to enhance battery performance.
2. Battery with Stacked Electrode Sheets Featuring Increased Positive Electrode Size and Coating Thickness
ZHUHAI COSMX BATTERY CO LTD, 2024
Battery design to improve energy density, safety, and flatness without increasing cell size. The battery has electrode sheets stacked inside a case. The positive electrode sheet size is increased compared to the negative sheet. This reduces the coverage margin of the negative sheet beyond the positive edge. The positive coating thickness is increased while keeping insulator thickness constant. This improves positive active material coverage. The second (negative) coating covers the first (positive) coating projection in thickness direction. The second coating edge is within the insulator. This prevents lithium precipitation at edges. The reduced edge thickness difference improves surface flatness.
3. Manufacturing Method for Anode with Internal Polymer Deposition via iCVD at Elevated Substrate Temperatures
LG ENERGY SOLUTION LTD, 2024
Method for manufacturing anode for lithium secondary battery that allows polymer deposition even inside the anode mixture layer to prevent cracking and improve durability. The anode is formed by applying a lithium composite transition metal oxide slurry on a current collector, then polymer coating using iCVD at substrate temperatures above 100°C. This allows uniform polymer distribution inside the anode's lower porosity compared to other electrodes.
4. Method for Producing Battery Electrodes Using Viscous Raw Layer with In-Situ Polymerizing Adhesive for Thickness Uniformity
VOLKSWAGEN AG, 2023
A method for producing battery electrodes that reduces layer thickness variation and prevents cracking during drying. The method involves coating the current collector with a viscous raw layer containing an activated adhesive starting component. This component is stabilized to form an adhesive before drying. The adhesive stabilizes the raw layer locally to prevent material flow and thickness variations during drying. This prevents cracking and ensures consistent electrode thickness. The activated adhesive can be a monomer that polymerizes into a long-chain adhesive during stabilization.
5. Method for Manufacturing Battery Electrodes Using High-Speed Slurry Coating Exceeding Yield Point
Nissan Motor Co., Ltd., NISSAN MOTOR CO LTD, 2023
Method for manufacturing battery electrodes with improved flatness and reduced thickness variation of the active material layer. The key is coating the electrode slurry at a speed that exceeds the yield point of the slurry. The slurry has specific flow properties with a region where shear stress is constant and a region where shear stress increases with speed but at decreasing rate. Coating at speeds exceeding the yield point prevents sagging and improves layer uniformity.
6. Method for Preparing Cathode Material with Uniform Conductive Coating via Modified Binder and Dual Sintering Process
ZHEJIANG MEIDU HAICHUANG LITHIUM BATTERY TECH CO LTD, ZHEJIANG MEIDU HAICHUANG LITHIUM BATTERY TECHNOLOGY CO LTD, 2023
A preparation method for cathode material for lithium-ion batteries with uniform and conductive coating layers that improves cycle life and capacity retention. The method involves steps like mixing precursor powder, primary sintering, coating with modified binder, and secondary calcination. The binder is treated to optimize coating properties. The precursor powder is prepared by complex co-precipitation to form NCM313 particles. The coating agent is applied at a specific concentration. The modified binder treatment improves coating uniformity and conductivity compared to standard binder. The secondary calcination step refines the particles and coating. This results in cathode material with uniform coating layers, better conductivity, and improved cycle life and capacity retention.
7. Cylindrical Battery with Gradient Coating Mass Distribution on Pole Piece
DRAGONFLY LABORATORY CO LTD, DRAGONFLY LABORATORY SHENZHEN CO LTD, 2023
Battery design with a specialized pole piece and coating configuration to improve battery performance and longevity, especially in cylindrical lithium-ion batteries. The pole piece has a unique coating profile where the mass per area of the positive electrode coating increases progressively along the pole piece length, while the negative electrode coating decreases. This compensates for the inherent difference in coating mass between inner and outer pole piece segments during winding. This keeps the positive/negative coating ratio stable throughout the battery construction to prevent issues like local lithium precipitation, improve charging, cycle life, and safety.
8. Battery Electrode Coating with Artificial Solid Electrolyte Interface via Liquid Phase Deposition
CORESHELL TECH INC, CORESHELL TECHNOLOGIES INC, 2022
Coating battery electrodes with artificial solid electrolyte interfaces (SEI) to improve safety and thermal stability of batteries. The artificial SEI is formed by a liquid phase deposition process that involves exposing the electrode to reactant solutions in chambers and rinsing between chambers. The coating provides protective barrier on electrode surfaces to prevent exothermic reactions, reduce gas evolution, and raise thermal runaway onset temperatures compared to uncoated electrodes.
9. Cathode Active Material with Acidic Alumina Partial Coating via Zirconium Alkoxide Precursor
BASF SE, 2022
Partially coating lithium-ion battery cathode active materials with a thin layer of acidic alumina to reduce resistance build-up during cycling. The process involves reacting the active material with a zirconium alkoxide or amide to form a precursor. This precursor is then mixed with water and the active material to coat the particles. The coated material is dried and further mixed to homogenize the coating. The coating provides a protective barrier on the active material surface that prevents unwanted reactions during cycling, reducing resistance and improving cycle life.
10. Battery Production Process with Coated Aluminum Positive Electrode, Cladded Copper Negative Electrode, and Mixed Solvent Electrolyte
JIANGSU HONGYINGYUAN NEW ENERGY TECH CO LTD, JIANGSU HONGYINGYUAN NEW ENERGY TECHNOLOGY CO LTD, 2022
A production process for new energy batteries that improves battery quality and reduces issues like electrode thickness variation, sealing problems, and electrolyte leakage. The process involves using specific materials and steps for each battery component. The positive electrode is made by coating the active material onto aluminum foil. The negative electrode uses cladding on copper sheets. The electrolyte is a mixed solvent with ammonium salt or lithium salt. The diaphragm is a microporous membrane. This combination helps ensure consistent electrode thickness, better sealing, and prevent electrolyte leakage in the battery.
11. Double-Layer Coating Structure for Battery Cell Electrodes with Protective Bottom Layer and Separator-Contacting Surface Layer
HUIZHOU LIWEI NEW ENERGY SCIENCE AND TECH LIMITED CO, HUIZHOU LIWEI NEW ENERGY SCIENCE AND TECHNOLOGY LIMITED CO, 2022
Double-layer coating structure for battery cells and winding battery cells that improves performance and reliability. The coating structure has a bottom layer between the current collector and surface layer. This bottom layer provides additional protection against electrolyte penetration and improves cell longevity. The surface layer contacts the separator and helps prevent separator puncture. This double-layer coating can be used on both positive and negative electrodes.
12. Lithium-Ion Battery Positive Electrode Material Coated with Metal Salt of C10-C34 Fatty Acid via Solid-Phase Reaction
SHENZHEN ORI TECH CO LTD, SHENZHEN ORI TECHNOLOGY CO LTD, 2022
Preparing lithium-ion battery positive electrode materials with improved cycle life and stability by coating them using a fatty acid salt. The method involves mixing a metal salt of a C10-C34 fatty acid with the positive electrode material and sintering it at temperatures between 200-1000°C for 1-24 hours. This solid-phase reaction disperses the metal oxide coatings uniformly on the electrode surface, reducing the amount needed compared to conventional coatings. The fatty acid salt coating improves cycle life, energy retention, and resistance compared to uncoated materials.
13. Lithium-Ion Battery with Edge-Coated Electrodes for Controlled Electron Flow Distribution
SK ON CO LTD, 2022
Lithium-ion secondary battery with improved cycle life by controlling the current flow within the battery cell to prevent localized deterioration. The battery design features a coating on the edges of the positive and negative electrodes that guides the electron flow toward the corners. This prevents concentration of current in the center and reduces localized degradation.
14. Method for Multi-Layer Coating of Electrode Slurry for Uniform Conductive Agent Distribution in Lithium-Ion Battery Pole Pieces
CHINA ELECTRONIC TECHNOLOGY GROUP CORPORATION NO.18 RESEARCH INSTITUTE, CN ELECT TECH NO 18 RES INST, TIANJIN SPACE POWER TECH CO LTD, 2022
Preparation method for electrode pole pieces of lithium-ion batteries with improved uniformity of conductive agent distribution to enhance high-rate discharge performance. The method involves multi-layer coating and drying of the electrode slurry instead of a single coating step. The coating is repeated multiple times to build up the electrode layer. This provides a more uniform distribution of conductive agents inside the pole piece compared to a single coating. The number of coating iterations can be adjusted to optimize performance.
15. Vacuum Evaporation Coating Method for Ternary Positive Electrodes in Lithium-Ion Batteries
SVOLT ENERGY TECH CO LTD, SVOLT ENERGY TECHNOLOGY COMPANY LTD, 2021
Coating method for ternary positive electrodes in lithium-ion batteries that improves cycle life and capacity by using vacuum evaporation instead of mechanical mixing. The method involves placing a target material on an evaporation boat inside a vacuum chamber, heating it to evaporate the material onto the electrode surface. This provides a uniform, compact coating without particle size issues. The vacuum environment prevents particle agglomeration and ensures the coating adheres well to the electrode.
16. Lithium Battery Cathode with Multilayer Oxide Coating of Nano Alumina, Zirconia, and Conductive Agent
SUZHOU REDEFINE IND DESIGN CO LTD, SUZHOU REDEFINE INDUSTRIAL DESIGN CO LTD, 2021
Preparing a lithium battery with improved storage life and safety by coating the cathode with a multilayer oxide coating. The coating consists of nano alumina, zirconia, and a conductive agent. The thickness is 5-8 microns. This coating on the cathode reduces dendrite growth on the lithium metal anode during cycling, preventing short circuits and capacity fade.
17. Lithium-Ion Battery with Electrode Active Material Coating of Defined Thickness and Particle Orientation
HUNAN LIFANG NEW ENERGY SCIENCE & TECH CO LTD, HUNAN LIFANG NEW ENERGY SCIENCE & TECHNOLOGY CO LTD, 2021
Lithium-ion battery with improved energy density by optimizing the coating thickness and particle orientation of the electrode active materials. The single-side coating density of the positive electrode is 23-50 mg/cm2 and negative electrode is 14-30 mg/cm2. The positive active material particles are consistently arranged and oriented with an angle <=30 degrees to the electrode thickness. This reduces ionic resistance and improves capacity compared to thicker coatings with disoriented particles.
18. Method for Manufacturing Secondary Batteries Using Low Boiling Point Solvent and Supercritical Carbon Dioxide in Airless Spraying Process
MTEK SMART CORP, MTEK-SMART CORP, 2021
Method for manufacturing secondary batteries like lithium-ion batteries and solid-state batteries with improved performance and throughput by using a solvent system with a low boiling point solvent and supercritical carbon dioxide (SCF) instead of traditional high boiling point solvents. The SCF is merged with the slurry upstream of the coating head and applied to the electrode substrate using airless spraying. This allows high solid content, high viscosity slurries to be applied without settling issues. The SCF expands after spraying to push out residual slurry. The low boiling point solvent evaporates quickly, reducing drying time and residual solvent.
19. Battery with Positive Electrode Coatings Featuring Thickness, Particle Size, and Viscosity Relation
ZHUHAI COSMX BATTERY CO LTD, 2021
Battery with improved low temperature charge-discharge performance by optimizing the thickness, particle size, and electrolyte viscosity of the coatings on the positive electrode. The coating layers on the positive electrode surface are the first coating and second coating. The battery satisfies a specific relation between the thickness, particle size, and electrolyte viscosity of the coatings: eta * T1 / (D501 * D502) > 5, where eta is electrolyte viscosity, T1 is first coating thickness, D501 is first coating median particle size, T2 is second coating thickness, D502 is second coating median particle size. This relation reduces the lithium ion diffusion distance in the solid phase to improve direct current resistance at low temperature charge states. It also balances performance tradeoffs between viscosity, particle size
20. Lithium Ion Battery with Nanoprotective Layer Deposited by Magnetron Sputtering on Electrode and Current Collector Surfaces
Amprius Technologies, Inc., AMPRIUS CO LTD, Amprius (Nanjing) Co., Ltd., 2021
Lithium ion battery with improved energy density and safety through surface coating modification using magnetron sputtering. The battery has a nanoprotective layer on the electrode surfaces and the current collector areas. The nanoprotective layer is 10-200 nm thick and prevents electrolyte ingress during needle puncture. It allows higher energy density without thickening separators or adding flame retardants. The nanoprotective layer is deposited by magnetron sputtering on the electrode and current collector areas during winding. This enables uniform coating of both electrode surfaces regardless of spacing.
Get Full Report
Access our comprehensive collection of 52 documents related to this technology
Identify Key Areas of Innovation in 2025
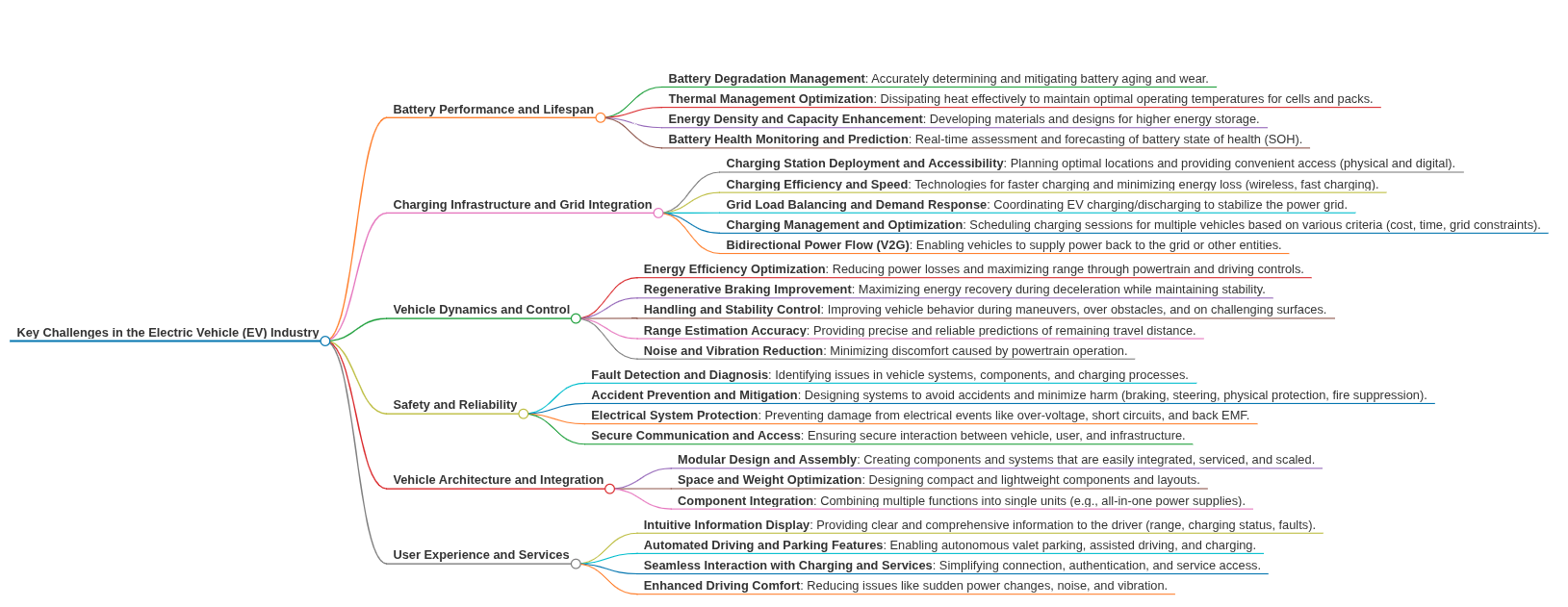