General Motors Innovations in Li-ion Battery
In modern lithium-ion batteries, capacity fade and thermal management remain persistent engineering challenges. Current cells experience up to 20% capacity loss over 1000 cycles, while thermal events, though rare, can cascade through cell arrays when thermal runaway temperatures exceed 150°C. General Motors' battery development focuses on addressing these fundamental limitations at the material, cell, and system levels.
The core challenge lies in simultaneously improving energy density, cycle life, and safety without compromising the cost and manufacturability requirements of mass-market electric vehicles.
This page brings together solutions from recent research—including advanced electrode architectures with modified carbon membranes, multilayer protective coatings for silicon anodes, internal induction heating systems, and strategic lithium reservoirs for capacity retention. These and other approaches demonstrate practical pathways to enhance battery performance while maintaining manufacturing scalability.
1. Centrifugal Atomization of Lithiated Silicon Alloy Particles via Impingement Mixer Precursor Formation
GM GLOBAL TECHNOLOGY OPERATIONS LLC, 2024
Preparing lithiated silicon electrode materials for lithium-ion batteries using a centrifugal atomization process. The process involves forming a precursor by mixing lithium and silicon at elevated temperatures and pressures in an impingement mixer. The precursor is then centrifugally atomized to form small, spherical lithium-silicon alloy particles. This reduces lithium evaporation and gravity separation compared to melting and atomizing the lithium and silicon separately. The centrifugal atomization also forms uniform, monodisperse particles for improved battery performance.
2. Low-Temperature Atomic Layer Deposition of Interfacial Lithium Fluoride Layers via Lithium Hexafluoroacetylacetonate Reaction
GM GLOBAL TECHNOLOGY OPERATIONS LLC, 2024
Low-temperature atomic layer deposition (ALD) method to form interfacial lithium fluoride layers on components of lithium-ion batteries prior to cell assembly. The ALD process involves reacting lithium hexafluoroacetylacetonate precursor with functional groups on the component surface, then introducing oxidant like water to form a single molecular layer of lithium fluoride. Steps are repeated to build up thickness. The low-temp ALD allows forming ionically conductive, electrically insulating LiF layers directly on battery components like separators and electrodes before assembly. This prevents direct lithium-electrolyte contact during cycling.
3. Electrode with Modified Carbon Membrane for Enhanced Lithium Nucleation in Lithium-Ion Batteries
GM GLOBAL TECHNOLOGY OPERATIONS LLC, 2024
Electrode design for high-rate lithium-ion batteries that reduces dendrite formation, improves cycle life, and allows faster charging. The electrode has a modified carbon membrane with elevated lithium nucleation sites compared to the unmodified membrane. This modified region promotes uniform lithium plating/stripping and prevents dendrites. The rest of the membrane serves as the current collector. Modifications like laser ablation, doping, or coating a lithophilic layer are used to create the modified region. This allows faster charging without sacrificing cycle life due to dendrite formation.
4. Hybrid Electrochemical Cell with Stacked Electrode Featuring Distinct Battery and Capacitor Material Regions
GM GLOBAL TECHNOLOGY OPERATIONS LLC, 2024
Hybrid electrochemical cells that combine lithium-ion battery electrodes with capacitor electrodes to achieve higher energy density and power density compared to traditional lithium-ion batteries. The cells have hybrid electrodes with separate regions for battery materials like graphite, silicon, and lithium metal oxides, and capacitor materials like activated carbon, graphene, and lead oxide. The battery and capacitor regions are coated on opposite sides of a current collector to form a stacked electrode. This allows separate optimization of battery and capacitor properties for improved overall cell performance.
5. Reference Electrode Assembly with Porous Membrane and Carbon Layer for Secondary Lithium Ion Batteries
GM GLOBAL TECHNOLOGY OPERATIONS LLC, 2024
A reference electrode assembly for secondary lithium ion batteries that can be integrated into commercial battery cells for real-time monitoring and optimization of charging and discharging. The assembly has a porous membrane with a carbon layer and a reference electrode layer deposited on one side. The carbon layer provides conductivity to an external connector tab, allowing the reference electrode potential to be measured. This enables individual electrode potentials and state of charge monitoring during cycling. The carbon layer facilitates manufacturing using printing techniques.
6. Electrode Fabrication Process Involving Multi-Step Rolling for Dense Lithium-Ion Battery Films
GM GLOBAL TECHNOLOGY OPERATIONS LLC, 2024
Electrode fabrication process for lithium-ion batteries with high energy density and long cycle life. The process involves rolling an admixture of electroactive material, binder, and solvent into a sheet, then forming a multi-layer stack. The stack is rolled through gaps of decreasing size to form thin, dense electrode films. This multi-step rolling process compresses the material and reduces porosity. The dense films are then dried to remove solvent. The resulting electrodes have lower tap density, high discharge capacity, and improved cycle life compared to wet coated electrodes.
7. Multilayer Carbon-Coated Negative Electrode Material with Intermediate Oxide Layer for Lithium-Ion Batteries
GM GLOBAL TECHNOLOGY OPERATIONS LLC, 2023
Negative electrode material for lithium-ion batteries with improved cycling life and capacity retention for high-energy density applications like electric vehicles. The negative electrode uses a multilayer carbon coating on the electroactive material like silicon to prevent fracturing during cycling. The coating is formed by treating the electrode with oxygen at high temperature to form an intermediate oxide layer, followed by carbon pyrolysis. The coating has an inner amorphous carbon layer next to the oxide and an outer graphitic carbon layer. This double-layer structure provides flexibility and durability during volume expansion/contraction.
8. Electrochemical Device with Integrated Induction Coil for Internal Heating via Eddy Currents
GM GLOBAL TECHNOLOGY OPERATIONS LLC, 2023
Electrochemical devices like lithium-ion batteries that internally heat themselves using induction to improve performance in cold environments without external heating. The device has an induction coil inside the cell that receives alternating current to generate a magnetic field. This field induces eddy currents in the conductive cell components like current collectors and electrodes, generating heat. The coil can be powered by the cell itself or an external source. This in-situ heating avoids heat loss to the environment and provides uniform temperature compared to external heating methods.
9. Prelithiated Negative Electrode with Lithium-Silicon Alloy and Pyrolyzed Polymer-Derived Conductive Carbon Matrix
GM GLOBAL TECHNOLOGY OPERATIONS LLC, 2023
Making prelithiated negative electrodes for lithium batteries with higher capacity and cycle life by loading the electrode with excess lithium before assembly. The method involves making a precursor mixture with lithium-silicon alloy particles, carbon particles, and a polymer binder dissolved in a solvent. This mixture is applied to a current collector and dried to form the electrode layer. During drying, the polymer pyrolyzes to form a conductive carbon matrix. The prelithiated electrode has a higher initial lithium content compared to a normal electrode, reducing lithium loss during initial charging and improving cycle life.
10. Lithium-Ion Battery Positive Electrode with Metal-Infused Lithiation Additive Forming Internal Lithium Reservoir
GM GLOBAL TECHNOLOGY OPERATIONS LLC, 2023
Creating a lithium reservoir in lithium-ion batteries to improve capacity retention by adding a lithiation additive containing lithium and metals like iron, copper, cobalt, or manganese to the positive electrode. This additive blended with the positive electroactive material helps prevent lithium loss during cycling by providing an internal lithium source. The lithiation additive forms a reservoir of lithium that can replenish the positive electrode during cycling to reduce capacity fade. It addresses the issue of lithium loss from volume-expanding negative electrodes during cycling by providing an internal source of lithium.
11. Gradient Electrodes with Layered Electroactive and Capacitor Materials for Lithium-Ion Batteries
GM GLOBAL TECHNOLOGY OPERATIONS LLC, 2023
Capacitor-assisted gradient electrodes for high-performance lithium-ion batteries with improved cycling and power capabilities. The electrodes have multiple layers of electroactive materials with different specific capacities, alternated with layers of capacitor materials. This graded structure absorbs regeneration currents during charging, preventing plating and enabling higher intercalation/deintercalation rates. The capacitor layers buffer the current density spikes during charging and discharging, reducing lithium plating on the active materials. The gradient electrodes can be made by coating the current collector with the electroactive materials, drying, pressing, and repeating with the capacitor materials.
12. Prelithiated Silicon-Based Negative Electrode Material with Centrifugally Atomized Spherical Particles
GM GLOBAL TECHNOLOGY OPERATIONS LLC, 2023
Prelithiated negative electrode material for lithium-ion batteries that improves cycle life and capacity retention compared to conventional lithium-ion batteries. The prelithiated electroactive material is made by centrifugally distributing a molten precursor containing silicon, lithium, and a small amount of additional metal. The centrifugal atomization process forms spherical particles with a composition of Li4.4xSixMy where x is a fraction between 0 and 0.85. The small amount of additional metal prevents segregation and evaporation during atomization. The prelithiated silicon particles have a size below 20 microns. This prelithiated silicon material provides higher specific capacity and reduced lithium loss compared to conventional silicon anodes.
13. Method for Centrifugal Atomization of Molten Precursor to Form Spherical Prelithiated Silicon Oxide Particles for Lithium-Ion Battery Electrodes
GM GLOBAL TECHNOLOGY OPERATIONS LLC, 2023
Making prelithiated electroactive materials for lithium-ion battery negative electrodes that can minimize capacity fade and maximize charge capacity in commercial lithium-ion batteries with long lifespans, especially for transportation applications. The method involves centrifugally atomizing a molten precursor of silicon, lithium oxide, and optionally silicon oxide to form spherical prelithiated silicon oxide particles containing both lithium silicide and lithium silicate. The particles have a diameter less than 20 micrometers. This prelithiation reduces lithium consumption during cycling compared to lithiation after cell assembly. It also prevents large volumetric expansion during cycling that can damage the electrode structure. The prelithiated particles can be used in negative electrodes for lithium-ion batteries with improved cycling performance.
14. Anode Fabrication Method with Preformed Solid Electrolyte Interface via Sequential Electrolyte Layer Application
GM GLOBAL TECHNOLOGY OPERATIONS LLC, 2023
A method to form anodes for lithium-ion batteries that have solid electrolyte interfaces (SEIs) to prevent dendrite growth and improve cycle life. The anode SEI is formed separately before assembling the cell. It involves applying sequential electrolyte layers to the raw anode, drying between layers, and assembling the final anode into the cell. The SEI-forming electrolytes contain lithium salts dissolved in organic solvents. The separate SEI steps reduce dendrite growth and improve cycle stability compared to in-cell SEI formation.
15. Electrolyte System with Aliphatic Fluorinated Disulfonimide Lithium Salt in Tailored Organic Solvent Mixture
GM GLOBAL TECHNOLOGY OPERATIONS LLC, 2023
Electrolyte system for lithium-ion batteries that improves performance, especially for high-voltage applications like lithium-sulfur batteries. The electrolyte contains an aliphatic fluorinated disulfonimide lithium salt like lithium bis(fluorosulfonyl)imide in a mixture of organic solvents. The solvent mixture includes a first solvent like ether or carbonate, and a second solvent like fluorinated ether. The molar ratios of the solvents can be tailored. This electrolyte system provides good electrolyte stability, ionic conductivity, and battery cycling at high voltages.
16. Mesoporous Ceramic Oxide Coating for Metal Anodes in Lithium-Ion and Sodium-Ion Batteries
GM GLOBAL TECHNOLOGY OPERATIONS LLC, 2023
Protective coating for metal anodes in lithium-ion and sodium-ion batteries that prevents mossy SEI formation, dendrite growth, and impedance increases during cycling. The coating is a mesoporous film made of ceramic oxides like Li2SiO3, LiAlO2, Li2O-Al2O3-SiO2, etc. The mesoporous structure traps protons from HF without forming releasable water molecules. This scavenges HF without generating more HF. The coating also blocks electron transfer and regulates ion distribution. It improves cycle life, efficiency, and capacity retention compared to bare metal anodes.
17. Lithium-Ion Battery Negative Electrodes with Micron-Scale Silicon Particles, Graphene Nanoplatelets, and Polyimide Binder
GM GLOBAL TECHNOLOGY OPERATIONS LLC, 2023
High-performance lithium-ion battery negative electrodes with improved cycling stability and capacity retention, especially for vehicle applications. The negative electrodes contain silicon particles with an average diameter of at least 1 micron, graphene nanoplatelets as the conductive material, and a polyimide-based binder. The larger silicon particle size reduces volumetric expansion during lithiation/delithiation compared to smaller particles. The graphene nanoplatelets provide electrical conductivity. The polyimide binder promotes mechanical robustness. Heat treatments of the electrode at temperatures less than 400°C prevent excessive expansion.
18. Hybrid Lithium-Ion Battery with Voltage Modification Component for Dual Chemistry Electrodes
GM GLOBAL TECHNOLOGY OPERATIONS LLC, 2023
Hybrid lithium-ion battery that can successfully use two different electrode active material chemistries regardless of voltage mismatch, especially for transportation applications. The battery has positive and negative electrodes with distinct electroactive materials, but a voltage modification component like a diode between them to compensate for voltage mismatch during charging/discharging. This allows using high energy density and high power density materials together.
19. Electrolyte Composition with Propylene Carbonate and Stabilizing Additives for Lithium-Ion Batteries
GM GLOBAL TECHNOLOGY OPERATIONS LLC, 2023
Electrolyte composition for lithium-ion batteries with extended cycle life by stabilizing anode, cathode, and lithium salt against degradation. The electrolyte contains propylene carbonate solvent, a lithium salt, and three additives: vinylene carbonate, lithium difluorophosphate, and prop-1-ene-1,3-sultone. The additives stabilize the anode, cathode, and lithium salt respectively. This prevents graphite anode exfoliation and lithium salt decomposition during cycling.
20. Non-Aqueous Electrolytes with Cyclic and Acyclic Carbonates and Acyclic Fluorinated Ether Solvent
GM GLOBAL TECHNOLOGY OPERATIONS LLC, 2023
Non-aqueous, aprotic liquid electrolytes for lithium ion batteries that have improved low temperature operation, oxidative stability, and thermodynamic stability compared to conventional electrolytes. The electrolytes contain a combination of cyclic and acyclic carbonate solvents along with a specific acyclic fluorinated ether solvent. The fluorinated ether improves low temperature performance by avoiding solvent cointercalation in graphite-based negative electrodes. It also improves oxidative stability by inhibiting solvent oxidation during high voltage operation. Additionally, the fluorinated ether raises the electrolyte's flash point.
Get Full Report
Access our comprehensive collection of 43 documents related to this technology
Identify Key Areas of Innovation in 2025
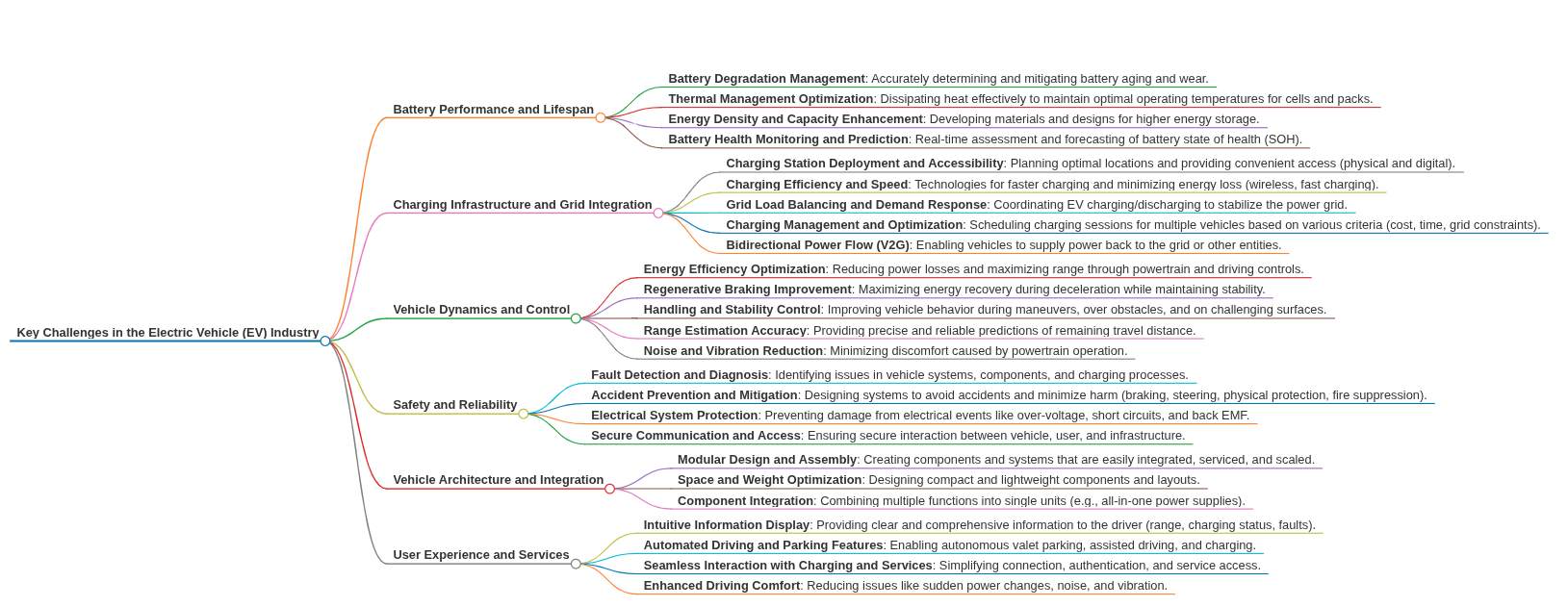