Lithium-Ion Battery Fire Suppression in EVs
Electric vehicle battery fires present unique challenges, with cells capable of reaching temperatures above 800°C during thermal runaway events. These fires can persist for hours, resist traditional water-based suppression methods, and reignite multiple times as thermal propagation moves through the pack's thousands of cells.
The fundamental challenge lies in simultaneously detecting thermal events early, containing cell-to-cell propagation, and safely managing the release of high-temperature gases and materials.
This page brings together solutions from recent research—including integrated gas sensing and venting systems, dielectric immersion techniques, aerosol-based suppression methods, and intelligent cooling architectures. These and other approaches focus on practical implementation across various vehicle types while addressing both immediate containment and long-term thermal management needs.
TABLE OF CONTENTS
1. Localized Fire Suppression Using Embedded or Adjacent Devices
Thermal runaway events in EV battery systems present a fundamental safety challenge: once initiated at the cell level, they can rapidly propagate throughout the entire battery pack with potentially catastrophic consequences. Addressing this challenge requires intervention methods that can detect and suppress thermal events at their source before propagation occurs.
Integrating suppression mechanisms directly within the battery structure represents one of the most promising approaches to localized fire control. Aerosol-based suppression devices embedded into battery arrays or structural spacers between cells create a first line of defense. These devices typically combine an ignition element (such as nitrocellulose) with a fire-suppressing aerosol generator (commonly potassium nitrate). When abnormal temperatures are detected, the ignition element activates the aerosol generator, producing particles that rapidly cool surrounding cells and interrupt the thermal runaway cascade. The compact nature of these devices allows them to be incorporated as multi-layer configurations or even as microcapsule-based nanocoatings, offering scalability without significantly compromising energy density.
The effectiveness of localized suppression also depends on the system's ability to navigate the complex architecture of sealed EV battery enclosures. Modular, sensor-driven suppression systems address this challenge by creating networks of environmental sensors that detect temperature spikes, gas leaks, and pressure anomalies throughout the battery pack. These systems connect to control units that can activate targeted suppression mechanisms in real time, injecting extinguishing agents directly into specific battery modules through movable spray units and valve-controlled channels. This precision targeting minimizes collateral damage to functioning components while maximizing fire containment efficiency.
At the chassis level, integration of suppression systems with vehicle architecture provides another layer of protection. Chassis-level suppression systems incorporate networks of temperature, gas, and smoke sensors alongside visual monitoring cameras, all connected to control modules that coordinate suppression actions. When hazardous conditions are detected, solenoid valves release high-pressure suppressants through strategically placed nozzles within the battery enclosure. These systems often include recovery tanks to collect residual suppressant, addressing environmental concerns while ensuring comprehensive coverage of the battery compartment.
For public transport applications, where passenger safety is paramount, sealed, liquid-cooled fire protection enclosures offer a specialized solution. These systems enclose battery packs in double-layered boxes filled with cooling liquid and equipped with both internal and external smoke sensors. During thermal events, nitrogen tanks rapidly displace oxygen and reduce temperature within the enclosure, while electromagnetically controlled circuit breakers disconnect power supplies to prevent electrical ignition sources. This combination of passive cooling, gas-based suppression, and automated power isolation creates a multi-layered defense particularly suited to the confined spaces and high occupancy of public transport vehicles.
2. Early Detection Systems Using Gas, Smoke, Pressure, and Temperature Sensors
The effectiveness of fire suppression in EV battery systems hinges on early detection of thermal anomalies before they escalate to full thermal runaway. Traditional temperature monitoring alone often provides insufficient warning time, as significant temperature increases typically occur only after internal cell degradation has already begun. This detection gap has driven the development of multi-parameter sensing technologies that can identify pre-combustion indicators.
Thermal sensing can be significantly enhanced through strategic material selection and placement. Thermally anisotropic materials with integrated sensors represent an innovative approach to early detection. By placing materials like graphite foil near battery cell vents, thermal events can be detected with greater precision and speed. These materials exhibit high in-plane thermal conductivity but low through-plane conductivity, allowing them to absorb and redirect localized heat from a venting cell while preventing propagation to adjacent cells. When coupled with thermal sensors, this configuration enables battery management systems to identify and isolate affected modules before full thermal runaway develops, maintaining operational capability through unaffected portions of the battery system.
Gas detection provides an even earlier warning of impending thermal events. During the initial phases of cell degradation, lithium-ion batteries emit specific gases including hydrogen, carbon monoxide, and various hydrocarbons—all precursors to visible smoke or flame. Gas-based detection mechanisms positioned near battery packs can identify these emissions in real time, often detecting problems minutes before temperature sensors would register anomalies. These systems can trigger automated responses ranging from enhanced cooling activation to vehicle isolation protocols, particularly valuable in autonomous or fleet-operated EVs where human intervention may not be immediately available.
The integration of multiple sensing modalities creates the most robust detection systems. Multi-parameter sensing technology combines temperature, smoke, gas, and flame sensors into comprehensive detection networks. These systems distribute detection control units throughout the battery pack, each linked to independent fire extinguishers that can be autonomously triggered when thermal anomalies are detected. Communication via CAN or RS485 bus protocols enables real-time feedback to central alarm displays, allowing for both automated and manual intervention. This modular architecture provides precise localization of thermal events and targeted suppression, significantly reducing both response time and extinguishing agent consumption compared to single-sensor approaches.
The evolution of detection systems reflects a shift from reactive to predictive safety paradigms. By identifying thermal events at their earliest stages through complementary sensing technologies, modern detection systems provide critical time advantages for suppression mechanisms to engage before propagation occurs. This early warning capability is particularly important in densely packed or thermally insulated battery modules where heat dissipation is limited and propagation risks are elevated.
3. Inert Gas and Aerosol-Based Suppression Systems
Fire suppression in EV battery systems presents unique challenges compared to conventional fire scenarios. Battery fires involve complex electrochemical reactions that can self-sustain even in oxygen-limited environments, making traditional water-based suppression methods potentially ineffective or hazardous. Inert gas and aerosol-based systems offer alternative approaches that address these specific challenges.
Oxygen displacement through inert gas injection provides one effective strategy for fire suppression. Nitrogen inflation systems integrated within battery enclosures can rapidly modify the internal atmosphere to suppress combustion. These systems typically feature permeable, self-inflating bags containing nitrogen that are housed within the battery pack. When triggered by thermal events, the nitrogen is released, displacing oxygen and creating an environment less conducive to flame propagation. The effectiveness of this approach is enhanced by one-way venting mechanisms that allow hazardous gases to escape while preventing ambient air from entering the battery enclosure. This combination of active suppression and passive containment helps control both the immediate fire risk and the potential for reignition.
Aerosol-based suppression offers a different mechanism that directly interrupts the combustion process at the chemical level. Aerosol generators embedded within battery arrays contain compounds such as potassium nitrate that, when activated, produce fine particles capable of inhibiting flame propagation. These devices can be configured as microcapsules or multi-layered structures integrated at the cell or module level, allowing for precise placement at potential failure points. When thermal sensors detect temperature excursions, control modules activate these aerosol devices, releasing suppression agents directly at the source of thermal events. This localized approach minimizes the quantity of suppression agent required while maximizing its effectiveness at the point of origin.
The complexity of thermal runaway events has also led to the development of two-stage fire suppression systems that combine multiple suppression strategies. These hierarchical systems monitor both temperature and pressure at the individual cell level, enabling them to detect early signs of failure and respond with targeted intervention. If initial suppression efforts prove insufficient, secondary systems activate to address the entire battery pack. This layered approach improves both the precision and scalability of suppression efforts, reducing the risk of system-wide failure while conserving suppression resources.
The integration of suppression mechanisms with intelligent control systems represents a significant advancement over passive protection methods. By coordinating detection and suppression activities through central control units, these systems can adapt their response based on the severity and location of thermal events. This intelligence allows for more efficient use of suppression resources and improved containment outcomes, particularly in large or complex battery architectures where thermal propagation paths may be difficult to predict.
4. Liquid-Based Cooling and Fire Suppression Systems
The dual requirements of thermal management during normal operation and fire suppression during thermal events have driven the development of integrated liquid-based systems that serve both functions. These systems leverage the high heat capacity and thermal conductivity of liquids to address the full spectrum of thermal challenges in EV battery systems.
Conventional approaches typically separate cooling and suppression functions into distinct systems, increasing complexity, weight, and cost. An innovative alternative integrates these functions through dual-purpose cooling circuits that circulate temperature control fluid through battery subsystems during normal operation. These circuits incorporate strategically placed check valves that, under normal conditions, maintain unidirectional flow for thermal regulation. However, when thermal sensors detect abnormal conditions, the system redirects coolant through damaged sections or predefined weak points in the cooling lines, allowing the fluid to escape directly at the fire site. This targeted delivery ensures that suppression occurs precisely where needed, minimizing coolant consumption while maximizing effectiveness.
The integration of cooling and suppression functions offers several advantages beyond simplification. By eliminating the need for separate extinguishing components, these systems reduce weight and volume requirements, critical factors in EV design where energy density directly impacts range. Additionally, the continuous circulation of coolant during normal operation ensures that suppression capability is regularly verified, unlike dedicated fire suppression systems that may remain dormant until needed, potentially developing undetected faults.
For applications with particularly stringent safety requirements, such as rail transport, more robust approaches combine active and passive protection methods. Gravity-fed dielectric suppression systems house battery packs in fire-protected cabinets connected to elevated tanks containing dielectric fluid. During normal operation, this fluid circulates through cooling circuits to maintain optimal battery temperature. In the event of a thermal incident, the elevated tank releases fluid via gravity, flooding the cabinet and suppressing the fire without requiring external power. This fail-safe design ensures protection even during system outages, a critical consideration in transportation applications where power loss may coincide with thermal events.
The evolution of liquid-based systems reflects a growing recognition that thermal management and fire suppression represent points on a continuum rather than distinct functions. By designing systems that can seamlessly transition between cooling and suppression modes based on thermal conditions, manufacturers can improve both safety and efficiency while reducing system complexity. This integrated approach also supports the development of more resilient battery systems that can potentially survive minor thermal events without requiring complete replacement.
5. Thermal Insulation and Heat-Absorbing Materials to Prevent Propagation
Preventing thermal runaway propagation through material-based strategies offers a passive yet highly effective approach to battery safety. Unlike active suppression systems that respond to thermal events after they begin, thermal insulation and heat-absorbing materials work continuously to contain thermal energy and prevent cell-to-cell propagation.
Conventional insulation materials primarily function as thermal barriers, slowing heat transfer but offering limited capacity to absorb energy from thermal events. Advanced ceramic matrix composites address this limitation by incorporating inorganic endothermic gas-generating materials into their structure. When exposed to high temperatures, these materials undergo endothermic decomposition, absorbing substantial thermal energy while simultaneously releasing non-flammable gases that dilute toxic emissions and control pressure buildup. This multifunctional approach provides both thermal isolation and active heat absorption, significantly enhancing protection compared to passive barriers alone.
The effectiveness of these materials stems from their customizable composition and structure. By varying the concentration and distribution of endothermic components, manufacturers can tailor thermal protection to specific battery geometries and risk profiles. These materials maintain mechanical integrity at temperatures exceeding 900°C, allowing for closer cell spacing and higher energy density without compromising safety. Their compatibility with various manufacturing methods, including dry pressing and vacuum forming, further enhances their practical applicability across different battery designs.
Thermal interface materials (TIMs) represent another critical component in propagation prevention. Traditional TIMs often suffer from poor conformity and limited thermal conductivity, creating hotspots that can accelerate thermal runaway. Coated filler-based TIMs address these challenges by combining functional fillers with hydroxyl-terminated polymers crosslinked with boron agents. This formulation achieves exceptionally high filler loading—up to 98%—while maintaining softness and flexibility, ensuring excellent contact with irregular battery surfaces. Beyond improving thermal transfer during normal operation, these materials also provide fire suppression capabilities, acting as multifunctional safety layers within battery assemblies.
Structural design also plays a crucial role in thermal propagation prevention. Dual-unit cell cover systems with directional venting eliminate intermediate module enclosures and create controlled pathways for venting gases and flames. By incorporating metal mesh within these venting paths, the system fragments and cools flames while absorbing heat through endothermic reactions. This targeted containment approach significantly reduces propagation risk while simplifying battery architecture and improving energy density.
The integration of these material-based strategies creates layered defense systems that address multiple aspects of thermal propagation. By combining thermal barriers, heat-absorbing materials, and engineered venting paths, manufacturers can develop battery systems that contain thermal events at their source, preventing the cascading failures that lead to catastrophic outcomes. This passive protection complements active suppression methods, creating comprehensive safety systems that remain effective even when active components fail.
6. Battery Compartmentalization and Structural Isolation
The architecture of battery systems plays a fundamental role in fire safety, with compartmentalization and structural isolation serving as primary strategies for containing thermal events and preventing system-wide failures. These approaches focus on limiting the spread of thermal runaway through physical barriers and dedicated venting pathways.
Compartmentalization divides battery systems into discrete sections that can be thermally and electrically isolated from one another. One effective implementation houses individual lithium-ion cells in smaller sub-containers within a larger enclosure. These compartments are constructed from materials such as fiberglass, aluminum, or cardboard, coated with heat-activated intumescent materials like FIREFREE 88. When exposed to high temperatures, these coatings expand to form insulating barriers that restrict heat transfer and fire spread. The dual-container configuration, with inner and outer enclosures separated by an intumescent-coated interstitial space, provides multiple layers of protection against thermal propagation.
For high-demand applications with stringent safety requirements, such as electric aircraft, structural isolation incorporates both containment and active thermal management. Battery assemblies with inward-angled side walls secure cells against mechanical ejection during failure events, while cooling plates coated with flame retardant paint serve as passive fire suppression elements between cell rows. These plates work in conjunction with insulation sleeves and thermal sensors to detect and limit thermal runaway spread. This integrated approach addresses both the mechanical and thermal aspects of battery safety, critical considerations in aviation applications where system failures cannot be tolerated.
Controlling the direction of thermal event propagation represents another structural approach to battery safety. Battery modules with dedicated venting holes in their top plates channel gases, flames, and particles upward rather than laterally toward adjacent cells. Filling materials between cells and end covers provide thermal and electrical insulation, preventing lateral escape of combustion byproducts. This architectural strategy ensures that thermal events follow predetermined paths away from vulnerable components, reducing the risk of cascading failures while maintaining structural integrity during high-temperature events.
In confined environments such as underwater vehicles, where external intervention is impossible, isolation strategies incorporate active thermal mitigation. Safety auxiliary systems integrated into modular battery architectures can inject refrigerant gas into overheating modules upon detecting thermal anomalies. This rapid intervention prevents thermal runaway propagation by actively cooling affected cells before they can impact adjacent modules. The system includes fail-safe logic that triggers gas injection if sensor data is lost, ensuring protection even under uncertain conditions.
The evolution of compartmentalization and structural isolation reflects growing recognition that battery architecture itself must serve as an active component of safety systems. By designing battery structures that inherently resist thermal propagation, manufacturers can create systems that remain safe even when active protection mechanisms fail. This passive-by-design approach complements active suppression methods, creating multilayered protection that addresses the full spectrum of thermal runaway risks.
7. Gas Venting and Pressure Relief Mechanisms
Thermal runaway events in lithium-ion batteries generate significant quantities of high-pressure, high-temperature gases that can lead to mechanical failure and explosion if not properly managed. Effective gas venting and pressure relief mechanisms are therefore essential components of comprehensive battery safety systems.
Conventional venting approaches often direct gases directly to the external environment, creating potential hazards for vehicle occupants and first responders. More sophisticated systems employ gas redirection mechanisms that route hot gases from affected lithium-ion battery packs through controlled pathways. One innovative approach channels these gases into adjacent metal-air battery packs, which serve as thermal sinks to absorb heat and delay the release of flammable gases. This controlled pathway reduces autoignition risk upon contact with ambient air, significantly improving safety for both occupants and emergency personnel. System controllers dynamically manage valve actuation based on real-time temperature and pressure data, ensuring that gas exhaust occurs only when internal thresholds are exceeded.
The internal structure of battery pack enclosures can also incorporate dedicated venting features. Vent gas passageways integrated within enclosures align with individual cell vents to guide hot gases through controlled circuits rather than allowing free discharge into the battery compartment. These designs typically include frangible sections that rupture only under thermal stress, forming inlet ports that channel vent gases into circuitous internal paths. This structural approach redirects gases and debris away from sensitive components while reducing pressure spikes and maintaining enclosure integrity. The modular nature of these designs allows for scalability across various pack configurations while improving containment of potentially harmful emissions.
Prevention of pressure buildup through proactive thermal management represents a complementary strategy to dedicated venting systems. Coolant-integrated battery modules thermally isolate cells and dissipate heat before pressure reaches critical levels. In these configurations, each cell is housed within a dedicated cylinder surrounded by coolant medium, with thermal interface materials enhancing heat transfer efficiency. Manifold systems circulate coolant to secondary heat exchangers, minimizing localized heating and reducing the likelihood of thermal events that would necessitate pressure relief activation.
The integration of venting mechanisms with broader battery safety systems enables coordinated responses to thermal events. By linking pressure sensors with thermal monitoring and suppression systems, battery management systems can implement staged responses based on the severity of detected anomalies. This coordination ensures that venting occurs in conjunction with other protective measures, maximizing the effectiveness of each component while minimizing risks to vehicle occupants and surrounding infrastructure.
The evolution of gas venting and pressure relief mechanisms reflects growing understanding of the complex dynamics of thermal runaway events. By developing systems that can safely manage the gaseous byproducts of cell failure, manufacturers are addressing one of the most dangerous aspects of battery thermal events while creating more resilient energy storage systems for electric vehicles.
8. Fire Suppression via Immersion in Dielectric or Liquid Media
Immersion-based fire suppression represents one of the most comprehensive approaches to battery thermal management, providing both preventive cooling during normal operation and active suppression during thermal events. These systems leverage the high heat capacity and dielectric properties of specialized fluids to address the full spectrum of thermal challenges in EV battery systems.
In confined environments such as rail vehicles, where battery systems operate in close proximity to passengers, liquid dielectric-based fire suppression offers particularly robust protection. These systems house battery packs in fire protection cabinets spatially separated from occupied areas and connected to overhead dielectric fluid tanks. During normal operation, the dielectric fluid circulates in closed loops for active thermal regulation. If thermal incidents occur, the system floods the battery compartment with dielectric fluid through gravity-fed lines, enabling passive suppression even during power loss. This fail-safe operation ensures protection during critical scenarios when active systems might be compromised, while the integration of thermal monitoring and heat exchange capabilities enhances both safety and energy efficiency.
The integration of fire suppression with existing thermal management infrastructure represents another innovative approach that reduces system complexity and space requirements. Dual-purpose temperature control systems utilize temperature control lines with pumps and check valves to circulate coolant during normal operation. When thermal anomalies are detected, the system redirects coolant through designed leak points or reverses flow to deliver fluid directly to affected battery modules. This targeted approach achieves efficient suppression without requiring separate extinguishing systems, maintaining full thermal management capabilities even after suppression events.
For scenarios involving mechanical damage, such as vehicle collisions, selective emergency cooling systems supplement continuous cooling with module-specific emergency coolant canisters. These canisters activate upon detection of crash events or abnormal thermal behavior, rapidly flooding affected battery modules with coolant. This targeted approach slows reaction kinetics during thermal runaway and significantly reduces propagation risk to neighboring cells. By combining preventative and reactive cooling strategies, these systems enhance post-collision safety and mitigate catastrophic battery failure risks.
The effectiveness of immersion-based suppression stems from multiple complementary mechanisms. Direct contact between coolant and battery cells provides efficient heat transfer, rapidly reducing temperatures below critical thresholds. For dielectric fluids, the displacement of oxygen creates an environment inhospitable to combustion, while the fluid itself serves as a physical barrier preventing flame propagation between cells. These combined effects make immersion-based approaches particularly effective against the complex thermal challenges presented by lithium-ion battery failures.
The evolution of immersion-based suppression systems reflects growing recognition of the limitations of gas-based and aerosol-based approaches in high-energy-density battery applications. By developing systems that can deliver large thermal absorption capacity precisely where needed, manufacturers are creating more resilient battery systems capable of surviving thermal events that would otherwise lead to catastrophic failures.
9. Electrolyte and Material-Level Fire Retardant Integration
Addressing fire risks at the material level represents one of the most fundamental approaches to battery safety, potentially eliminating thermal runaway propagation at its source rather than merely containing its effects. Material-level interventions focus on modifying battery components to resist ignition and suppress flame propagation, creating inherently safer systems.
Electrolyte modification offers a direct path to reducing battery flammability. Conventional liquid electrolytes, while providing excellent ionic conductivity, contribute significantly to fire propagation during failure events. Flame-retarding electrolyte formulations incorporate thermal runaway inhibitors (TRIs) such as organophosphates and cyclic imido compounds that function as free radical scavengers or fire damping agents. These compounds chemically interfere with combustion processes while maintaining the ionic conductivity necessary for battery function. By integrating fire suppression directly into the electrolyte, these formulations provide intrinsic protection without requiring external safety components, making them particularly valuable for weight-sensitive and space-constrained EV applications.
Beyond the electrolyte, thermal interface materials (TIMs) play crucial roles in both normal thermal management and fire suppression. Multi-functional composite TIMs combine coated functional fillers with hydroxyl-terminated polymers crosslinked with boron agents to achieve exceptional thermal conductivity while also providing passive flame suppression. These materials can incorporate extremely high filler loadings—up to 98%—while maintaining the softness and conformability necessary for effective contact with battery surfaces. Their ability to enhance thermal dissipation during normal operation while actively suppressing flames during thermal events makes them valuable components in comprehensive battery safety systems.
Cell-level modifications further enhance safety through composite electrode and separator systems. Heat-absorbing inorganic particles incorporated into separator layers and electrode coatings actively absorb thermal energy during internal short circuits, preventing ignition and interrupting the thermal runaway sequence. Unlike conventional inert fillers, these materials provide dynamic thermal mitigation while maintaining electrochemical performance and mechanical stability at elevated temperatures. Their compatibility with existing manufacturing processes makes them particularly attractive for near-term safety enhancements in commercial battery systems.
Structural innovations at the cell assembly level complement material modifications by addressing risks associated with electrical shorting during thermal deformation. High-temperature-resistant insulating members positioned between adapters and battery housings prevent unintended electrical contact if electrode assemblies swell under thermal stress. These components maintain electrical isolation under extreme conditions, eliminating external short circuit risks that could exacerbate thermal events.
The integration of these material-level approaches creates multi-layered protection that addresses thermal runaway at multiple stages of development. By modifying electrolytes to resist ignition, incorporating heat-absorbing materials to manage thermal energy, and ensuring electrical isolation during deformation, manufacturers can develop battery systems that inherently resist the cascading failures characteristic of severe thermal events. This intrinsic safety complements external protection systems, creating comprehensive safety architectures that address the full spectrum of thermal risks in EV battery systems.
10. Hydrogel, Phase Change, and Endothermic Cooling Materials
The management of thermal energy during battery failure events represents a critical challenge in EV safety systems. Hydrogels, phase change materials (PCMs), and endothermic compounds offer passive yet highly effective approaches to thermal management, absorbing and dissipating heat without requiring active control systems.
Traditional PCMs like paraffin wax provide limited thermal absorption capacity and may themselves pose flammability risks. Hydrated hydrogel-based thermal suppression addresses these limitations through lightly crosslinked polyacrylic acid-based superabsorbent polymers placed in direct thermal contact with battery cells. These hydrogels leverage water's exceptional thermal properties—both specific heat and latent heat of vaporization—to absorb substantial thermal energy during overheating events. When cells rupture or experience thermal runaway, the hydrogel absorbs heat through both sensible heating and water vaporization, preventing adjacent cells from reaching critical temperatures. Unlike paraffin-based PCMs, hydrogels are non-flammable and conform to battery geometries, ensuring consistent thermal contact even when physically damaged.
For applications requiring higher temperature stability, ceramic matrix composites with inorganic endothermic gas-generating materials offer exceptional thermal protection. These materials combine passive insulation with active heat absorption through endothermic decomposition reactions that consume thermal energy while releasing non-flammable gases. The composite structure can be engineered with varying ratios of ceramic to endothermic material and may include inorganic fibers and microporous fillers to enhance thermal resistance and mechanical integrity. Operating independently of external power sources, these materials provide fail-safe protection that reduces adjacent cell ignition risk while allowing tighter cell packing for improved energy density.
The effectiveness of these thermal management materials stems from their ability to intervene at multiple stages of thermal events. During initial temperature excursions, they absorb heat through sensible heating, potentially preventing cells from reaching thermal runaway thresholds. If thermal runaway occurs, endothermic decomposition and phase changes absorb substantial energy, slowing propagation to adjacent cells. Finally, the release of non-flammable gases or water vapor can displace oxygen and dilute flammable gases, reducing combustion risk in the battery enclosure.
The integration of these materials into battery systems requires careful consideration of placement and quantity. Strategic positioning between cells or modules maximizes thermal protection at potential propagation pathways, while material quantity must balance thermal absorption capacity against weight and volume constraints. Advanced battery designs may incorporate multiple thermal management materials in layered configurations, creating graduated responses to thermal events of varying severity.
The evolution of hydrogel, phase change, and endothermic materials reflects growing recognition of the limitations of active cooling systems in managing rapid thermal events. By developing materials that can passively absorb large quantities of thermal energy without requiring external activation, manufacturers are creating more resilient battery systems capable of containing thermal events even when active protection systems fail. This passive-by-design approach complements active suppression methods, creating comprehensive safety systems that address the full spectrum of thermal risks in EV applications.
11. Thermally Activated Valves and Passive Trigger Mechanisms
The reliability of fire suppression systems in EV batteries depends significantly on their activation mechanisms. While electronic sensors and control systems offer precision, they may fail during severe thermal events when power systems are compromised. Thermally activated valves and passive trigger mechanisms provide fail-safe alternatives that operate independently of electronic controls, ensuring protection even during catastrophic failures.
Conventional suppression systems typically rely on electronic sensors to detect thermal anomalies and activate suppression measures. Thermally activated coolant discharge systems take a fundamentally different approach by integrating valves containing phase-change materials directly into battery packs. These materials remain solid under normal operating conditions but melt or deform when temperatures exceed critical thresholds, opening valves that discharge coolant through turbulizer heads onto overheated modules. By placing coolant lines along battery case perimeters with at least 90% contact, these systems ensure uniform thermal sensitivity across the pack while eliminating reliance on potentially vulnerable electronic components.
The autonomous nature of these systems provides several advantages beyond reliability. Each valve operates independently, enabling localized and immediate cooling precisely where needed without requiring centralized decision-making. This modular response minimizes coolant usage and reduces the risk of thermal propagation to adjacent cells, while the passive activation mechanism ensures that suppression occurs even if battery management systems or power supplies fail. The simplicity of these systems also reduces maintenance requirements and potential points of failure, enhancing long-term reliability in field applications.
Structural approaches to passive fire mitigation complement valve-based systems by redirecting thermal energy away from vulnerable components. Cell covers with directional venting and flame suppression eliminate intermediate module cases and adopt Cell-to-Pack (CTP) configurations where each cell or cell group is enclosed by dual-layer covers. These covers include separation spaces that channel vented gases and flames laterally rather than vertically toward adjacent cells, while integrated metal mesh structures absorb heat and disrupt flame fronts. This passive architecture guides thermal discharge away from neighboring cells without requiring active control systems, significantly reducing propagation risk while simplifying manufacturing and improving energy density.
The integration of passive triggers with active suppression systems creates hybrid architectures that combine the reliability of thermal activation with the precision of controlled suppression. These systems typically use thermally sensitive elements to initiate suppression sequences that may then be modulated or extended by electronic controls if they remain functional. This layered approach ensures immediate response to thermal events while preserving the ability to adapt suppression strategies based on event severity and location.
The evolution of thermally activated systems reflects growing recognition of the vulnerabilities inherent in purely electronic safety systems. By developing mechanisms that respond directly to thermal conditions without requiring electronic mediation, manufacturers are creating more resilient protection systems that remain effective even under the most challenging failure scenarios. This passive-first design philosophy ensures that critical safety functions continue to operate when active systems fail, providing essential protection during catastrophic events when intervention is most needed.
12. Multi-Stage Fire Response and Escalation Systems
The complex nature of thermal runaway in lithium-ion batteries necessitates sophisticated response systems capable of adapting to evolving threat levels. Multi-stage fire response and escalation systems address this challenge by implementing hierarchical intervention strategies that match suppression measures to event severity.
Conventional battery management systems typically employ binary responses to thermal anomalies, either taking no action or implementing full-scale countermeasures that may unnecessarily disable the entire battery system. Multi-stage prevention and control systems take a more nuanced approach by introducing graduated responses based on real-time diagnostics and risk assessment. These systems feature central controllers with specialized modules for diagnosing faults, detecting thermal runaway at the cell level, and assessing propagation risk. Based on their analysis, they can trigger appropriate interventions ranging from cell disconnection for minor anomalies to inert gas deployment for more serious events, or pressure relief for critical situations. This graded response strategy enhances both safety and vehicle uptime by implementing only the level of intervention necessary to address the specific threat.
In large-scale energy storage environments, where battery density creates significant propagation risks, dual-agent fire protection systems implement two-tiered suppression approaches. The first tier uses localized agents like perfluorohexanone, delivered via thermosensitive glass bulbs embedded within battery enclosures. These bulbs burst at elevated temperatures, releasing suppression agents precisely at ignition sources. If this localized response proves insufficient, second-tier systems activate to protect broader areas using agents such as heptafluoropropane. This coordinated approach maximizes suppression efficiency while minimizing agent consumption and collateral damage to unaffected components.
For electrochemical energy storage stations with vertically stacked battery arrays, early detection and spatially aware suppression are essential. Very early composite detection and directional extinguishing systems deploy networks of optical, gas, and infrared sensors near high-risk emission zones to identify pre-ignition indicators before visible flames develop. Upon detection, these systems release extinguishing agents directionally, targeting only affected modules through staged suppression sequences calibrated to event severity. This spatially intelligent approach ensures minimal downtime and asset loss while enhancing personnel safety through proactive containment.
The effectiveness of multi-stage systems stems from their ability to balance precision and comprehensiveness. By implementing targeted interventions for minor events while maintaining the capability for system-wide response to major incidents, these systems optimize resource utilization while maximizing protection. The integration of multiple detection modalities—including temperature, pressure, gas, and optical sensing—enables accurate threat assessment, while the coordination of various suppression mechanisms ensures appropriate response regardless of event characteristics.
The evolution of multi-stage response systems reflects growing understanding of the progressive nature of thermal runaway events and the importance of early intervention. By developing systems capable of identifying and addressing thermal anomalies at their earliest stages, manufacturers are creating more resilient battery systems that can potentially survive minor thermal events without requiring complete replacement. This capability is particularly valuable in commercial applications where system downtime carries significant operational and financial impacts.
13. External Firefighting Interfaces and EV Parking Fire Suppression
The unique challenges of EV fires in parking and charging environments require specialized approaches to fire suppression that address both the internal battery dynamics and the external firefighting logistics. These systems must provide effective suppression while ensuring accessibility for emergency responders and minimizing collateral damage to surrounding vehicles and infrastructure.
Traditional fire suppression systems in parking structures often rely on sprinklers or manual intervention, both of which may prove ineffective against the high-energy, self-sustaining nature of battery fires. Temperature-sensing self-starting fire extinguishing devices address this limitation through distributed architectures where temperature-sensing nozzles are embedded directly within each battery box. This localized approach enables faster detection and more precise suppression than conventional systems mounted externally to the vehicle. Each battery box connects independently to a central delivery manifold via dedicated piping, allowing simultaneous and targeted activation without relying on centralized command systems. The use of individually connected temperature-sensing nozzles ensures that thermal anomalies are addressed at their source, while the central manifold design supports efficient agent distribution without bottlenecks.
For multi-level or automated parking structures, accessibility presents significant challenges for emergency responders. Self-elevating platforms with integrated conduits offer innovative solutions originally developed for offshore applications but adaptable to EV infrastructure. These platforms feature legs housing J-shaped conduits that create direct pathways between the platform and external systems, enabling rapid connection of fire suppressant delivery systems to vehicles in hard-to-reach parking zones. This integrated approach enhances operational safety and efficiency, particularly in scenarios where vehicle access is restricted due to fire or structural constraints.
The effectiveness of external firefighting interfaces depends significantly on their integration with vehicle architecture and emergency response protocols. Advanced systems incorporate standardized connection points that allow first responders to deliver suppression agents directly to battery compartments without requiring specialized knowledge of specific vehicle designs. These interfaces may include thermal barriers that prevent heat transfer from the battery to external components, protecting connection points from damage during thermal events and ensuring their availability when needed most.
The evolution of external firefighting interfaces and parking suppression systems reflects growing recognition of the unique challenges posed by EV fires in shared infrastructure. By developing systems that combine internal early detection with accessible external suppression capabilities, manufacturers and facility operators are creating more resilient environments capable of containing battery thermal events before they affect surrounding vehicles or infrastructure. This integrated approach enhances both safety and operational continuity in the rapidly expanding ecosystem of EV charging and parking facilities.
14. Modular or Distributed Suppression in Energy Storage Systems
The scale and complexity of modern energy storage systems require suppression architectures that can address thermal events at multiple levels, from individual cells to entire battery arrays. Modular or distributed suppression systems provide this capability by implementing localized protection that can operate independently or in coordination with broader system responses.
Conventional centralized suppression systems often suffer from delayed response times and inefficient agent distribution, particularly in large or compartmentalized battery installations. Point-to-point repeated and rapid response fire suppression systems address these limitations by placing local control modules at each battery pack, enabling immediate activation of suppression mechanisms upon detection of thermal or flame anomalies. These modules directly spray extinguishing agents at fire origins, minimizing propagation risk and response time while alerting central control units to initiate broader suppression if necessary. This hierarchical architecture ensures both localized and systemic defense, optimizing suppression efficiency while maintaining comprehensive protection.
For installations requiring more specialized protection, thermal aerosol fire extinguishing devices integrated within battery boxes offer particularly effective solutions. These systems connect fire monitoring controllers to networks of sensors that continuously scan for early indicators of thermal runaway, including carbon monoxide, volatile organic compounds, smoke, and temperature anomalies. Upon detection, they activate aerosol generators strategically placed within the battery matrix, ensuring full-volume coverage through condensed aerosols that suppress fire by displacing oxygen, cooling affected areas, and chemically inhibiting combustion. The compact and scalable nature of these systems makes them particularly suitable for high-voltage, high-density energy storage installations where space constraints limit conventional suppression options.
In large-scale installations, balancing precision and comprehensive protection requires sophisticated coordination between multiple suppression components. Dual-level suppression strategies using compressed air foam combine pack-level and cabin-level responses to optimize suppression efficiency. These systems detect thermal anomalies at individual battery packs and selectively deploy foam to affected modules, avoiding unnecessary activation across entire cabins unless widespread abnormalities are detected. The dual-action mechanism of foam—providing both oxygen isolation and thermal cooling—enhances effectiveness against the complex thermal challenges of lithium-ion battery fires.
For electrochemical energy storage stations with vertically stacked battery arrays, spatial awareness and early detection capabilities are essential. Very early detection and directional fire extinguishing systems position sensors near battery module sides to capture emissions that conventional detectors might miss. Upon detecting thermal runaway indicators, these systems initiate staged suppression sequences calibrated to event severity, combining extinguishing and cooling in a directional manner that targets affected modules while preserving adjacent components. This modular approach treats each battery unit as an independent node within a protection matrix, enabling precise intervention without compromising system-wide integrity.
The evolution of modular and distributed suppression reflects growing recognition of the limitations of centralized approaches in complex energy storage environments. By developing systems that can identify and address thermal events at their source while maintaining coordination with broader protection architectures, manufacturers are creating more resilient storage systems capable of containing localized failures before they escalate to system-wide emergencies. This capability is particularly valuable in grid-scale installations where system availability directly impacts energy security and economic performance.
Get Full Report
Access our comprehensive collection of 204 documents related to this technology
Identify Key Areas of Innovation in 2025
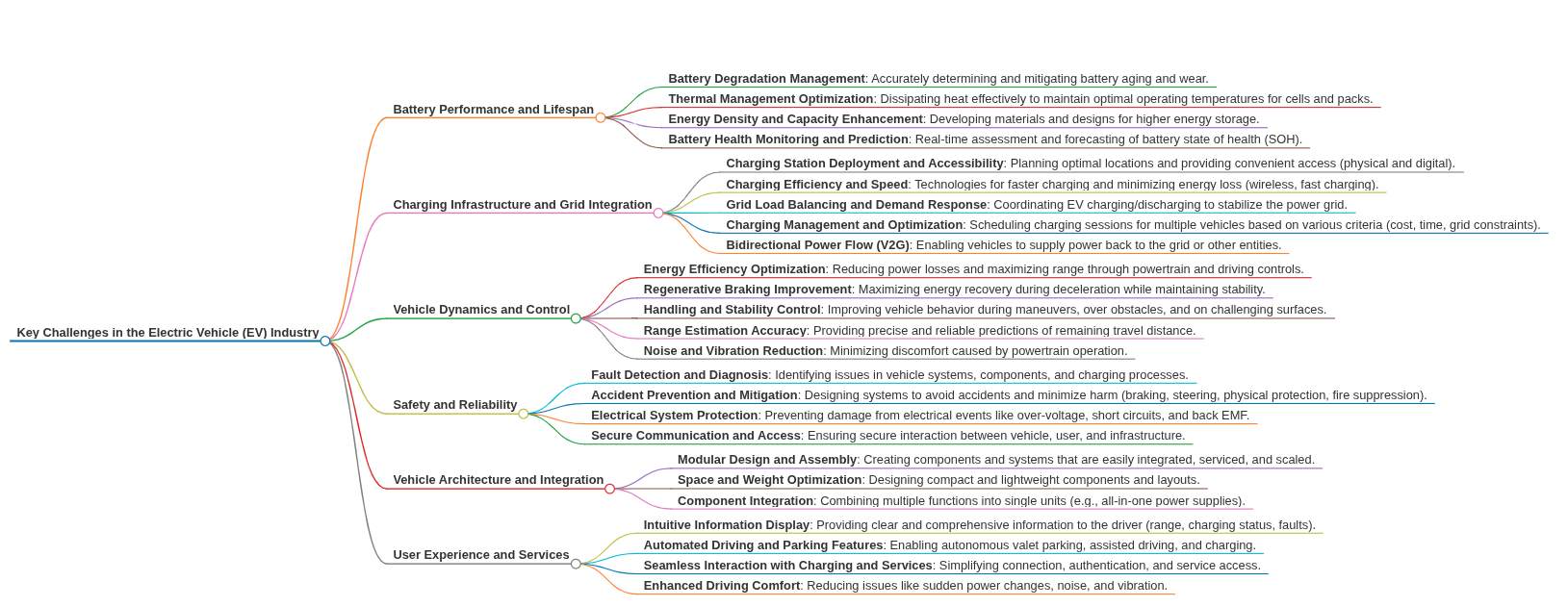