BYD Blade Battery Technology for Enhanced Safety and Longevity
Lithium iron phosphate (LFP) batteries face persistent challenges in achieving both high energy density and long-term stability. Traditional LFP cells typically achieve specific capacities of 140-150 mAh/g, with particle morphology and conductivity limitations affecting their performance. BYD's blade battery technology represents a systematic approach to these fundamental constraints.
The core challenge lies in optimizing particle density, uniformity, and conductivity while maintaining the inherent safety advantages of LFP chemistry.
This page brings together solutions from recent research—including mixed-morphology particle engineering, controlled atmosphere sintering processes, and novel carbon-composite structures. These and other approaches demonstrate how manufacturing innovations are enabling higher energy density while preserving LFP's thermal stability advantages.
1. Preparation Method for High Density Lithium Iron Phosphate Electrode Material Using Mixed Morphology Particles
BYD COMPANY LTD, 2024
Method to prepare high density lithium iron phosphate (LFP) positive electrode material for lithium ion batteries with improved specific capacity and energy density. The method involves mixing two forms of LFP, one with spherical morphology and the other with irregular morphology, in equal mass ratio. The spherical LFP is made by conventional slurry processing and sintering. The irregular LFP is made by the same slurry processing, sintering, and then crushing. The mixed LFP has higher compaction density compared to either form alone due to the irregular LFP filling gaps between spherical particles.
2. Co-Precipitation Method for Synthesizing Homogeneous Single-Phase LiMnxFe1-xP4 Cathode Material
Shanghai BYD Company Limited, SHANGHAI BYD CO LTD, 2016
Preparation method for lithium manganese iron phosphate (LiMnxFe1-xP4) cathode material for lithium-ion batteries that provides homogeneous, single-phase crystalline LiMnxFe1-xP4. The method involves co-precipitating ferromanganese and divalent manganese salts in an aqueous solution, followed by adding lithium salt and phosphate to form a mixed precursor solution. The precursor is then aged and heat treated to convert into LiMnxFe1-xP4. This method avoids high-temperature solid-state synthesis and traditional hydrothermal methods to obtain uniform, single-phase LiMnxFe1-xP4 particles.
3. LiFePO4/Carbon Composite Cathode Material with Sequential Annealing and Sintering Process
BYD COMPANY LTD, 2014
Preparing LiFePO4/carbon composite cathode material for lithium batteries with enhanced electrical properties by using annealing and sintering steps. The method involves providing a mixture of lithium, iron, phosphorus, and carbon compounds, annealing it in an oxidizing atmosphere, and then sintering it under inert conditions. The annealing distributes carbon among the lithium iron phosphate particles and promotes uniform particle distributions. The sintering further densifies the material. The annealing before and/or after sintering steps help avoid air bubbles and rapid thermal changes.
4. Lithium Iron Phosphate Synthesis Using Static Normal Pressure Inert Atmosphere Sintering Method
BYD COMPANY LTD, 2014
Preparing lithium iron phosphate (LiFePO4) for lithium-ion batteries without using inert gas during sintering to avoid impurities. The method involves sintering a mixture of lithium, iron, phosphorus, and carbon sources in a static, normal pressure inert atmosphere. The static atmosphere protects the iron from oxidation without continuously introducing inert gas. This prevents impurities like Fe2P. The sintering steps are first at 300-450°C for 4-15 hours, then 600-800°C for 10-25 hours.
5. Method for Synthesizing Lithium Iron Phosphate Using Ferric Oxide and Phosphoric Acid with Water-Soluble Solvent
BYD CO LTD, 2013
Preparation method for lithium iron phosphate (LiFePO4) as a positive electrode material for lithium-ion batteries that provides uniform particle size and improved battery performance compared to conventional methods. The method involves mixing lithium, iron, phosphorus, carbon, and solvent (water and/or organic solvent) sources, then drying and sintering the mixture. The key steps are using water or water-soluble organic solvent as the solvent, ferric oxide as the iron source, and phosphoric acid as the phosphorus source. This enables better separation of elements during drying and prevents agglomeration, resulting in smaller, more uniform LiFePO4 particles for higher capacity and better battery performance.
6. Lithium Secondary Battery Cathode Comprising Mixed Crystal of LiFePO4 and Metal Oxides with Controlled Conductivity
BYD COMPANY LTD, 2011
Lithium secondary battery cathode material with improved electrical properties for higher capacity and longer cycle life. The cathode material is a mixed crystal containing lithium iron phosphate (LiFePO4) and a second crystalline compound made of metal oxides. The mixed crystal has electrical conductivity 0.01-10 S/cm at 25°C. The mixed crystal is prepared by sintering LiFePO4 with the second compound at 500-800°C for 5-32 hours. The second compound can be any mixture of metal oxides from groups IA-VB of the periodic table. Adding carbon enhances conductivity further. This mixed crystal cathode provides LiFePO4:second compound ratios 1:0.001-0.1.
7. Lithium Iron Phosphate Anode Material with Uniform Particle Size and Carbon Content via Oxidative Grinding and Heating
BYD COMPANY LTD, 2011
Preparing lithium iron phosphate anode material for lithium-ion batteries with improved specific capacity and discharge performance. The method involves mixing iron source, phosphorus source, lithium source, and carbon additive in a solvent, grinding, and heating in an oxidizing environment. This provides uniformly sized lithium iron phosphate particles with consistent carbon content. The oxidizing environment during grinding promotes uniform lithium distribution. The heating conditions ensure proper conversion of iron to phosphate. This avoids large particle agglomerates and non-uniform carbon content that degrade discharge performance.
8. Method for Co-precipitating Iron Oxalate with Soluble Metal Salts via pH Control for Uniform Particle Size Distribution
BYD COMPANY LTD, 2011
A method for preparing an iron source for lithium iron phosphate batteries that enables preparing lithium iron phosphate with uniform particle size and improved electrochemical properties. The method involves co-precipitating iron oxalate and soluble non-iron metal salts by controlling the pH of the solution. This provides iron oxalate with a narrow particle size distribution and regular shape. The resulting iron source is used to make lithium iron phosphate batteries with better electrochemical performance compared to conventional methods.
9. Method for Preparing Homogeneous Lithium Iron Phosphate Electrode Material via Sequential Oxidizing Annealing and Inert Atmosphere Sintering
BYD COMPANY LTD, 2010
A method to prepare a uniform and homogeneous lithium iron phosphate (LFP) positive electrode material for lithium batteries with improved electrical performance. The method involves annealing the LFP precursor mixture in an oxidizing atmosphere followed by sintering in an inert atmosphere. Annealing before sintering allows more even distribution of carbon additive in the iron phosphate particles. The two-step heat treatment provides uniform particle size and shape.
10. Method for Synthesizing Iron-Based Lithium Phosphate Using Atmospheric Pressure Sealed Sintering
BYD COMPANY LTD, 2010
A method to prepare iron-based lithium phosphate for lithium-ion batteries without the need for inert gases during sintering. The method involves mixing lithium, iron, and phosphorus precursors and sintering them in a sealed container at normal atmospheric pressure. This allows the gases generated during sintering to protect against oxidation instead of introducing an inert gas. The resulting iron lithium phosphate has improved capacity, lower internal resistance, and better cycle performance compared to conventional methods.
11. Cathode Material Preparation via Dual-Stage Thermal Processing with Carbon Additive Distribution
BYD COMPANY LTD, 2010
Preparing a cathode material for lithium batteries with enhanced electrical properties through a multi-step thermal processing method. The method involves annealing the cathode precursor mixture in oxygen followed by sintering in an inert atmosphere. This two-step thermal treatment distributes carbon additives among the lithium iron phosphate particles, promotes uniform particle distributions, and predictable particle sizes for homogeneous cathode materials.
12. Method for Synthesizing Lithium Iron Phosphate Cathode with Dual Annealing and Sintering Stages
BYD COMPANY LTD, 2010
Preparation method for lithium iron phosphate (LiFePO4) cathode material for lithium-ion batteries with improved electrical properties. The method involves mixing lithium, iron, phosphorous, and carbon compounds, annealing at 60-250°C in oxygen, sintering at 300-600°C, annealing in oxygen again, then final sintering at 700-900°C. The two annealing steps distribute carbon and promote uniform particle size and homogeneity.
13. Method for Sintering Lithium Iron Phosphate with Static Pressure in Inert Atmosphere
BYD COMPANY LTD, 2009
A method for preparing lithium iron phosphate (LiFePO4) as a cathode active material for lithium-ion batteries that improves the conductivity and cycling performance of the material. The method involves sintering a mixture of lithium, iron, phosphorous, and carbon sources in an inert atmosphere with a static pressure. This prevents oxidation during sintering and enables high-purity, low-resistance LiFePO4 without the need for carbon coatings. Cooling the sintered product completes the process.
14. Ferrous Lithium Phosphate Anode Material with Nanometer Carbon and Iron Phosphide Agglutination
BYD COMPANY LTD, 2009
A ferrous lithium phosphate anode material for lithium-ion batteries with improved capacity and cycling performance. The anode active material is made by agglutinating ferrous phosphate lithium particles with nanometer carbon and iron phosphide. The agglutination is done at lower temperatures and times to control particle size and composition. This ferrous lithium phosphate anode material has higher specific capacity and capacity retention compared to standard lithium iron phosphate anodes.
15. Cathode Material Preparation via Sequential Oxygen Annealing and Inert Gas Sintering for Enhanced Homogeneity and Electrical Properties
BYD COMPANY LTD, 2009
Preparing cathode material for lithium-ion batteries with improved electrical properties. The method involves annealing the cathode precursor mix in oxygen followed by sintering in inert gas. This sequence provides better particle homogeneity, size distribution, and electrical capacity compared to direct sintering. The annealing step distributes carbon additives among the lithium iron phosphate particles and promotes uniformity. The sintering completes the cathode structure.
16. Solid-Phase Synthesis Method for Lithium Iron Phosphate with Controlled Particle Size and Crystal Structure
BYD COMPANY LTD, 2009
A method for preparing lithium iron phosphate (LiFePO4) as anode active material for lithium-ion batteries that provides high specific capacity and good discharge performance. The method involves a solid-phase synthesis route with iron and phosphorus precursors. It involves mixing iron and phosphorus sources with lithium source and carbon additive, grinding, heating, and calcining at controlled conditions to obtain LiFePO4. The method provides uniform particle size and crystal structure for improved battery performance compared to other synthesis methods.
17. Synthesis of Lithium Iron Phosphate Using Mixed Iron Sources with Controlled Sintering Conditions
BYD COMPANY LTD, 2009
Synthesis methods for lithium iron phosphate, a cathode material for lithium-ion batteries, that provide higher purity, capacity, and safety compared to conventional synthesis methods. The methods involve using a mixture of iron sources, like ferrous oxalate and ferric carbonate, with specific ratios, instead of just ferrous salts. This reduces CO and H2 formation during sintering, preventing impurity formation and explosive hazards. The methods also involve sintering in an inert gas atmosphere at controlled temperatures.
Get Full Report
Access our comprehensive collection of 17 documents related to this technology
Identify Key Areas of Innovation in 2025
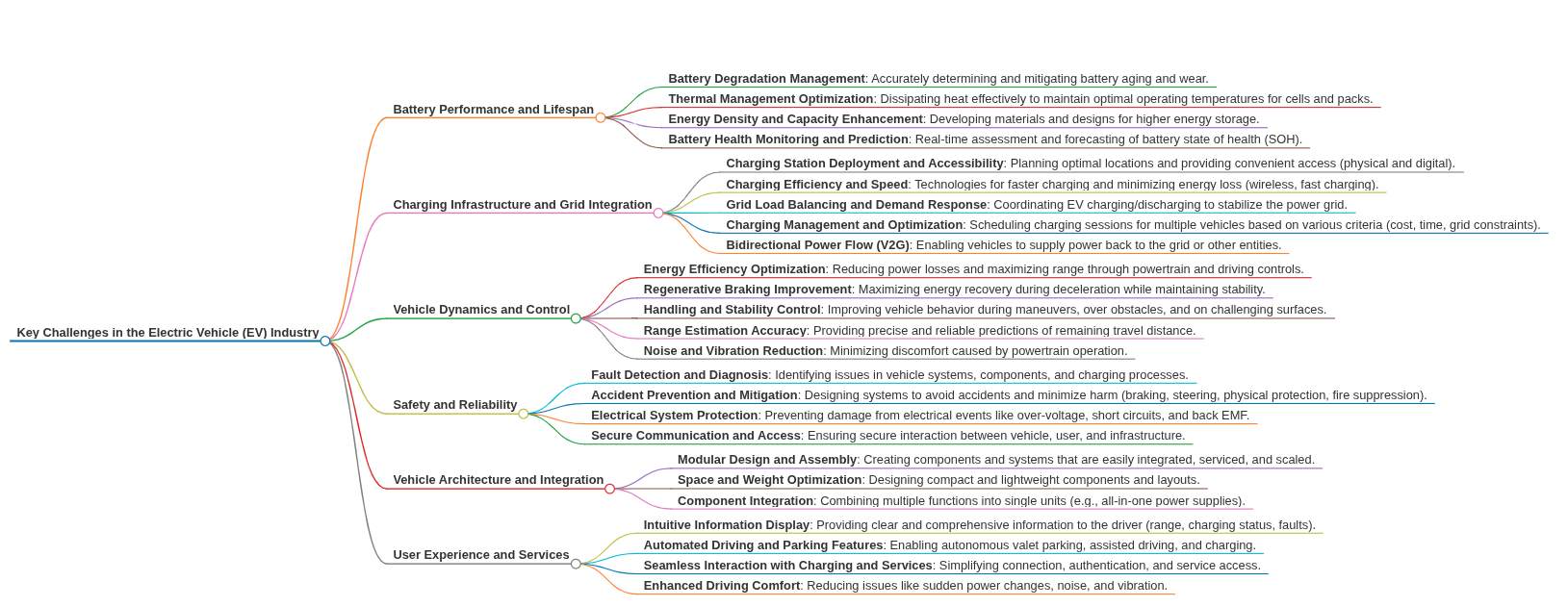