Anode Current Collector Protection in EV Batteries
Current collector degradation in lithium-ion batteries leads to capacity fade and potential safety risks, with studies showing up to 20% capacity loss after 500 cycles due to surface corrosion and mechanical stress. The interaction between lithium ions and current collector surfaces during charging and discharging creates localized high-stress regions that can accelerate material breakdown.
The fundamental challenge lies in developing current collector materials that maintain structural integrity and conductivity while preventing dendrite formation and managing interfacial stresses during repeated cycling.
This page brings together solutions from recent research—including lithiophilic metal coatings for uniform lithium deposition, double-layer coating architectures for dendrite suppression, and alloy-based collectors with optimized corrosion resistance. These and other approaches focus on practical implementations that balance durability requirements with manufacturing feasibility.
1. Positive Electrode Current Collector with Aluminum-Copper Alloy Layer for Enhanced Structural Integrity
SK ON CO LTD, 2024
Positive electrode current collector for lithium secondary batteries that improves durability by preventing deformation or breakage of the collector when high-density active material layers are formed. The collector has an aluminum layer, an aluminum-copper alloy layer, and a copper layer. The aluminum-copper alloy layer provides electrical conductivity and prevents delamination between the aluminum and copper layers. The aluminum-copper alloy composition can be sequentially changed to act as a buffer. The thicknesses of the aluminum, copper, and alloy layers are optimized.
2. Positive Electrode Current Collector with Aluminum-Copper Alloy Layer and Gradient Composition
SK ON CO LTD, 2024
A positive electrode current collector for lithium secondary batteries with improved durability, a method to manufacture it, and a battery with the collector. The collector has an aluminum layer, an aluminum-copper alloy layer, and a copper layer. The aluminum-copper alloy layer buffers expansion/contraction between the aluminum and copper layers during cycling to prevent deformation or failure of the collector. The collector composition gradients between the layers can also prevent delamination. The manufacturing method involves hot rolling aluminum and copper foils together to form the alloy layer, then heat treating and cold rolling to form the final collector.
3. Lithium Metal Battery Anode Current Collector with Thin Film Metal for Uniform Lithium Deposition
NISSAN MOTOR CO LTD, NISSAN NORTH AMERICA INC, 2024
Lithium metal battery with modified anode current collector to suppress dendrite formation and improve battery performance. The modification is a thin film of metal directly applied to the anode current collector. This metal layer promotes dense and uniform lithium deposition during charging, preventing dendrites. The thin film metal has a low formation energy with lithium (≤0.0123 eV) and low overpotential (≤5 mV) for dense, homogeneous lithium plating without dendrites.
4. Anode Structure with Sulfurized Polyacrylonitrile Layer for Lithium Metal Batteries
Samsung SDI Co., Ltd., 2024
Anode design for lithium metal batteries that improves cycle life and stability by preventing lithium dendrite growth. The anode structure has a protective layer made of sulfurized polyacrylonitrile (SPAN) between the current collector and the lithium metal or alloy active layer. The SPAN layer reduces reactivity with the electrolyte compared to pure polyacrylonitrile. This inhibits side reactions that degrade the anode. The SPAN layer also prevents direct contact between the lithium metal and electrolyte, reducing lithium dendrite formation.
5. Aluminum Composite Current Collector with Vapor-Deposited Aluminum Layer on Polymer Film Containing Insulating Polymer and Filler
YANGZHOU NANOPORE INNOVATIVE MATERIALS TECH LTD, YANGZHOU NANOPORE INNOVATIVE MATERIALS TECHNOLOGY LTD, 2024
Aluminum composite current collector for batteries that improves strength, elongation, and impact resistance compared to conventional composite collectors. The preparation method involves evaporating an aluminum layer onto a polymer film without multiple high-temperature/cooling cycles that cause polymerization and degradation. The polymer film can be a composite of insulating polymer and filler (90% insulating polymer) to provide strength. This avoids polymerization issues and maintains high tensile strength and elongation in the composite. The aluminum composite collector can be used in batteries to improve extrusion, impact, and safety properties compared to conventional composite collectors.
6. Aluminum Composite Current Collector with Polymer Layers and Reusable Copper Foil Integration
YANGZHOU NANOPORE INNOVATIVE MATERIALS TECH LTD, YANGZHOU NANOPORE INNOVATIVE MATERIALS TECHNOLOGY LTD, 2024
Aluminum composite current collector for lithium-ion batteries with improved strength and durability compared to conventional composite collectors. The aluminum composite current collector has an aluminum layer sandwiched between two polymer layers. The polymer layers are made using a preparation method that involves rolling up and reusing the copper foil after evaporation and hot pressing to prevent shrinkage compared to the base film. This allows peeling off the copper foil for repeated use. The composite current collector prepared this way has higher tensile strength and elongation compared to conventional composite collectors. This improves extrusion resistance, impact resistance, and battery safety by preventing breakage during manufacturing and use.
7. Composite Current Collector with Polymer and Calcium Gluconate Layers for Lithium-Ion Batteries
HEADING GUOLIAN SICHUAN CELL MAT CO LTD, HEADING GUOLIAN SICHUAN CELL MATERIALS CO LTD, 2024
A composite current collector for lithium-ion batteries with improved safety compared to traditional composite collectors. The collector has a polymer layer sandwiched between protective agent layers on each side and a metal foil layer. The protective agent layers contain calcium gluconate that expands rapidly when heated, blocking short circuits and preventing battery damage. The polymer layer provides mechanical support. The metal foil layer collects current. This multi-layer structure provides redundant safety mechanisms to mitigate internal short circuits in lithium-ion batteries.
8. Multi-layer Current Collector with Alternating Carbon and Metal Layers on Polymer Film
YANGZHOU NANOPORE INNOVATIVE MATERIALS TECH LTD, YANGZHOU NANOPORE INNOVATIVE MATERIALS TECHNOLOGY LTD, 2023
Multi-layer structure current collector for lithium-ion batteries with improved electrical performance and mechanical strength compared to conventional current collectors. The multi-layer structure current collector has alternating layers of carbon coating and metal plating stacked on both sides of a polymer film layer. This configuration protects the polymer film from damage, reduces interface resistance, and improves adhesion. The carbon coating layers on the polymer film prevent delamination and enhance electrical contact. The carbon coating also provides a conductive path between the metal layers. By alternating carbon and metal layers, the number of evaporation steps can be reduced compared to traditional current collectors, which improves mechanical properties and reduces porosity.
9. Gradient Copper Phosphide/Copper Oxide/Copper Foam Lithium Metal Anode Current Collector
HARBIN UNIV OF SCIENCE AND TECHNOLOGY, HARBIN UNIVERSITY OF SCIENCE AND TECHNOLOGY, 2023
Preparation method and application of a gradient copper phosphide/copper oxide/copper foam lithium metal anode current collector to address the stability and safety issues of lithium metal batteries. The current collector has a copper foam base with copper oxide and copper phosphide nanowires grown on it. The copper oxide top layer provides lithium nucleation uniformity, while the copper phosphide bottom layer induces dense lithium filling. This gradient structure balances lithium plating uniformity and conductivity compared to a pure copper collector. It reduces dendrite growth, short circuits, and improves cycle life for lithium metal batteries.
10. Composite Current Collector with Sputtered Barrier and Protective Layers on Aluminum Base
UESTC, 2023
Current collector for lithium batteries that provides high conductivity, stability, and weight savings compared to traditional aluminum and copper foils. The collector structure has a thin aluminum base layer, barrier layers formed by sputtering metals/nitrides on one side, and a protective layer on the other side. This design provides ion barrier and electrochemical passivation to prevent corrosion, while the aluminum base has lower weight and better conductivity than copper. A transition layer between the barrier and protective layers strengthens the connection. The composite collector structure offers high electrical conductivity, stability, and light weight for lithium batteries compared to conventional aluminum or copper foils.
11. Copper Foil with Controlled Particle Size Differential and Surface Roughness for Enhanced Puncture Strength
Jiang Chun Petrochemical Company Limited, 2023
Copper foil with improved puncture strength for use as a current collector in high capacity lithium secondary batteries. The copper foil has a particle size difference between the deposition side and drum side of less than 0.55 microns. This reduces voids created during electrodeposition and improves strength. The deposition surface roughness is 2.0 microns or less to allow uniform coating of the negative electrode material. This copper foil has puncture strength suitable for high capacity lithium batteries without being brittle during manufacturing or cycling.
12. 3D Porous Copper Current Collector for Lithium Metal Anodes with Dendrite Suppression
SOOKMYUNG WOMENS UNIV INDUSTRY ACADEMIC COOPERATION FOUNDATION, SOOKMYUNG WOMENS UNIVERSITY INDUSTRY-ACADEMIC COOPERATION FOUNDATION, 2023
Lithium metal anode for lithium secondary batteries using a 3D porous copper current collector to suppress dendrite growth and improve battery performance. The copper collector has a 3D porous structure formed on its surface. This porous structure provides internal spaces where lithium dendrites can deposit during charging/discharging instead of vertically growing. This prevents dendrite short circuits and stabilizes the electrode. The porous copper can be made by modifying its surface through electrochemical plating. The porous collector can also be used in cathode-less battery designs to further increase energy density.
13. Composite Metal Foil with Graded Thickness Layers and Polymer Core for Lithium Battery Current Collectors
HEBEI HAIWEI ELECTRONIC NEW MATERIAL TECH CO LTD, HEBEI HAIWEI ELECTRONIC NEW MATERIAL TECHNOLOGY CO LTD, 2023
Composite metal foil for lithium battery current collectors that balances surface resistance, energy density, and strength. The composite foil has a thin polymer layer sandwiched between metal layers. The outer metal layer has a thickness of 15-100nm, the inner metal layer has a thickness of 50-110nm, and an intermediate metal layer has a thickness of 750-1100nm. The polymer layer improves strength, while the graded metal layers provide low surface resistance and high energy density. The composite foil can also absorb battery expansion stress.
14. Lithium-Ion Battery Anode with Indium Nitride Layer for Dendrite Suppression
GM GLOBAL TECH OPERATIONS LLC, GM GLOBAL TECHNOLOGY OPERATIONS LLC, 2023
Reducing dendrite formation in lithium-ion batteries to improve battery performance and reliability by using an indium nitride (InN) layer on the anode. The InN layer, containing indium nitride, a conductive material, and a polymer binder, suppresses lithium dendrite growth during charging and discharging. The InN layer provides a lithium-ion conductive surface that limits direct contact between lithium and the electrolyte, reducing dendrite formation. The InN layer is formed by coating a slurry of indium nitride, conductive material, and polymer binder onto the anode current collector and curing it to bond the layer to the substrate.
15. Anode Current Collector with Dual Coatings for Dendrite Mitigation in Solid-State Batteries
HYUNDAI MOTOR CO, KIA CORP, 2023
An anode current collector for all-solid-state batteries that prevents lithium dendrites during charging and discharging. The anode current collector has two coatings on the surface that contact the solid electrolyte layer. The first coating is a lithiophilic metal layer that attracts lithium ions. The second coating has less electronic conductivity than the first coating. This prevents electrons from moving into the solid electrolyte layer, preventing dendrite formation.
16. Anode Current Collector with Double Coating Structure for Uniform Lithium Plating
HYUNDAI MOTOR CO, KIA CORP, 2023
An anode current collector for all-solid-state batteries that enables uniform lithium plating without dendrite formation. The anode has a unique double coating structure. The outer coating has reduced electrical conductivity compared to the inner coating. The inner coating contains a lithiophilic metal that attracts lithium ions. The outer coating prevents electrons from moving into the solid electrolyte layer, preventing short circuits and efficiency loss. The double coating allows lithium plating on the anode while preventing electron migration into the electrolyte.
17. Multilayer Lithium Metal Current Collector with Stacked Conductive, Nucleation, Transport, and Rectifying Layers
WUHAN INSTITUTE OF MARINE ELECTRIC PROPULSION, WUHAN INSTITUTE OF MARINE ELECTRIC PROPULSION NO 712 RES INSTITUTE CHINA SHIPBUILDING GROUP CO LTD, 2023
Multilayer lithium metal current collector for high energy density lithium batteries that addresses safety and utilization issues of lithium metal anodes. The collector has layers of materials stacked in order: conductive support, lithium-philic nucleation, electron/ion transport, and nano-lithium rectifying. The layers are applied in thin (5-200um) successive coatings using techniques like spraying or scraping. The layers enhance lithium deposition uniformity, suppress dendrite growth, and improve rate capability. The lithium-philic nucleation layer promotes initial lithium plating, the transport layer aids ion transfer, and the rectifying layer regulates lithium diffusion.
18. Multi-layer Current Collector with Lithium-alloying Seed Layer for Anodeless Lithium Metal Cells
THE REGENTS OF THE UNIV OF COLORADO A BODY CORPORATE, THE REGENTS OF THE UNIVERSITY OF COLORADO A BODY CORPORATE, 2023
Multi-layer current collector design for anodeless lithium metal cells that enables stable cycling of lithium metal anodes without dendrite formation and capacity fade. The multi-layer current collector has a seed layer of a lithium-alloying or lithium-soluble material like silver between the current collector and a protective layer. This prevents direct lithium plating on the current collector and allows gradual lithium alloying with the seed layer. The protective layer shields the electrolyte from the current collector and seed layer.
19. Current Collector with Porous Metal Layer and Lithium-Friendly Interface for Enhanced Plating Uniformity
SHANGHAI GUOXUAN NEW ENERGY CO LTD, 2023
A current collector structure for lithium batteries with improved lithium plating uniformity and reduced dendrite formation. The structure has a porous metal layer sandwiched between a substrate layer and a lithium-friendly layer. The porous metal layer has holes to accommodate lithium expansion. The lithium-friendly layer between the metal and substrate reduces lithium nucleation overpotential. This stack of layers allows lithium plating uniformity and volume expansion accommodation without dendrite formation.
20. Composite Battery Current Collector with Polymer Substrate and Partially Overlapping Metal Foils
SUZHOU QINGTAO NEW ENERGY TECH CO LTD, SUZHOU QINGTAO NEW ENERGY TECHNOLOGY CO LTD, 2022
Composite current collector for batteries with improved performance and reliability compared to traditional metal foil collectors. The composite collector has a polymer substrate sandwiched between metal foils. The metal foils partially overlap the polymer substrate edge and extend out. This provides multiple benefits: 1) A larger metal contact area compared to just the welding seam, improving conductivity and overcurrent capability. 2) Secure tab attachment without needing metal-on-metal welding, preventing tab falloff. 3) Reduced weight compared to thick metal tabs. The composite collector can be made by partially overlapping the metal foils with the polymer substrate edge.
Get Full Report
Access our comprehensive collection of 42 documents related to this technology
Identify Key Areas of Innovation in 2025
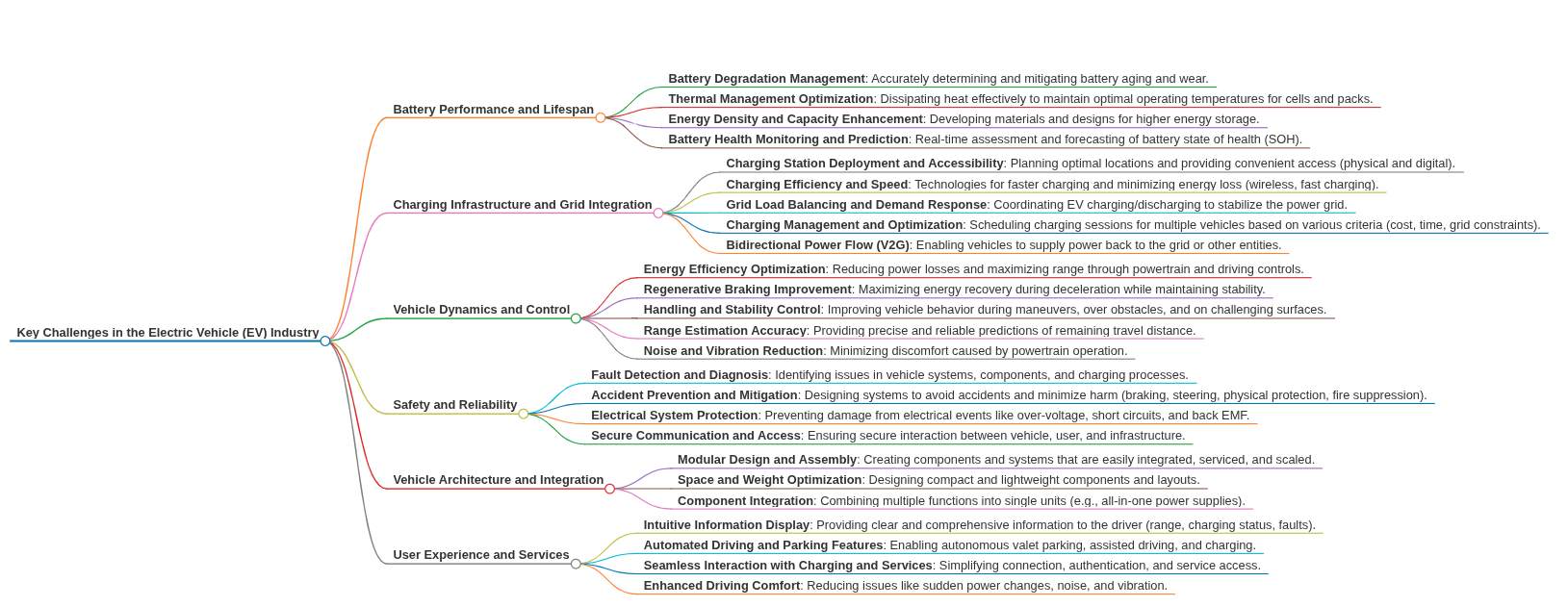