EV Battery Pack Assembly Methods & Design Optimization
Modern EV battery packs contain thousands of individual cells operating at voltages above 400V, with cell-level thermal events capable of reaching temperatures exceeding 150°C and generating significant volumes of combustible gases. Traditional module-based assemblies, while providing structural support, can impede effective gas venting and contribute to cascading thermal failures across cell groups.
The fundamental challenge lies in balancing direct cell mounting efficiency with robust thermal isolation and gas evacuation pathways that prevent propagation of cell-level failures.
This page brings together solutions from recent research—including directional venting architectures, integrated heat exchanger barriers, circuit board isolation systems, and staggered cell arrangements. These and other approaches focus on preventing thermal propagation while maintaining pack energy density and assembly efficiency.
1. Battery Pack with Direct Cell Mounting and Integrated Venting System
LG NEW ENERGY LTD, 2024
Battery pack design to improve energy density, reduce space loss, enhance safety against thermal events, and enable direct battery cell mounting without intermediate modules. The pack has a housing with an inner space for cell cases containing the cells. The cells are directly mounted in the pack instead of being pre-assembled into modules. The cell cases have covers with insulating blocks to isolate the electrodes. This allows exhaust gases to vent through the slots. The pack case has frames and a removable drain cover to guide exhaust. The cell cases are stacked in the pack with the drain covers removed. This direct cell mounting eliminates module housing and simplifies assembly. It also allows the pack to be more compact and reduces space loss compared to module-based packs. The exhaust venting through the insulating blocks helps contain thermal events by preventing pressure buildup and preventing fire spread between cells. The removable drain cover allows pack venting during
2. Method for Assembling Battery Cell Core with Ultrasonic Welding and Compression Molding Techniques
HEFEI GUOXUAN HIGH TECH POWER ENERGY CO LTD, HEFEI GUOXUAN HIGH-TECH POWER ENERGY CO LTD, 2024
A method for assembling a battery cell core to improve battery volume and avoid the need for connecting tabs while ensuring stable welding. The assembly method involves: 1. Placing a battery tab against a battery electrode without connecting tabs. 2. Ultrasonically welding the tab to the electrode using a welding tip with a raised projection. 3. Applying pressure to the welded tab and electrode using a compression mold. This molding step compresses the tab and electrode together under pressure to create a strong welded joint. The compression molding replaces the need for connecting tabs between the tab and electrode. By eliminating connecting tabs and compressively molding the tab and electrode, the battery core can have increased volume without the added weight and space requirements of connecting tabs.
3. Z-Stacked Electrode and Separator Configuration for Enhanced Voltage Resistance in Lithium-Ion Batteries
BYD COMPANY LTD, 2024
Battery assembly method to reduce short circuits in lithium-ion batteries by improving voltage resistance at the separator cut edges. The method involves stacking the electrode sheets with the separator in a Z-shape, with the starting and ending edges covered by the positive sheet. This ensures the cut edges are on the same side when assembled. This stabilizes the cut edges and prevents short circuits when the battery is heated during manufacture. It avoids the need for coatings or additives to improve separator voltage resistance.
4. Method for Lithium-Ion Battery Assembly with Direct Terminal-Tab Connection and Controlled Component Protrusion
JINGKE ENERGY STORAGE TECH CO LTD, JINGKE ENERGY STORAGE TECHNOLOGY CO LTD, 2024
A method to manufacture lithium-ion batteries that improves battery assembly efficiency and space utilization while preventing internal component movement. The method involves fixing the positive and negative terminals to the electrode tabs before encapsulating the battery. This prevents the electrode components from shifting during sealing. The terminals are directly connected to the tabs instead of using separate terminal posts. This allows the electrode components to protrude from the battery cover at a controlled height for better electrical contact. The fixed terminals and adjusted component heights prevent displacement issues during battery operation.
5. Method for Assembling Square Lithium Batteries with Sequential Component Positioning, Sealing, Gas Exhaustion, and Electrolyte Filling
Hubei Runye New Energy Co., Ltd., HUBEI RUNYE NEW ENERGY CO LTD, 2024
A new method for assembling square lithium batteries that addresses issues with traditional cylindrical battery assembly. The method involves a sequence of steps for accurately positioning and sealing components, exhausting internal gas, and filling electrolyte in a square battery format. This involves using fixtures to hold components in place during assembly, sealing the battery edges before filling electrolyte, exhausting gas through specialized valves, and stacking cells in a square configuration. This improves assembly accuracy, prevents external gas entry, reduces electrolyte loss, and simplifies stacking compared to cylindrical batteries.
6. Method for Assembling Cylindrical Aluminum Shell Batteries Using Continuous Penetration Welding and Modified Electrode Insertion Sequence
YANTAI LIHUA POWER SUPPLY TECH CO LTD, YANTAI LIHUA POWER SUPPLY TECHNOLOGY CO LTD, 2023
An improved method for assembling large cylindrical aluminum shell batteries with reduced leakage and internal damage risks. The assembly process uses continuous penetration welding instead of resistance welding or ultrasonic torque welding to join the positive electrode case to the aluminum shell. This avoids high heat generation that can burn the diaphragm and create metal shavings. Additionally, the assembly sequence is modified to prevent top leakage by inserting the electrode stack into the shell before sealing the top. This eliminates the need for liquid injection through the top pole, which can leak. The bottom leakage risk is reduced by using a special bottom sealing gasket.
7. Battery Cell with External Laser Welded Housing and Integrated Current Collector
LANJUN NEW ENERGY TECH CO LTD, LANJUN NEW ENERGY TECHNOLOGY CO LTD, 2023
Battery cell design with simplified assembly and reduced short circuit risk compared to conventional cells. The cell has a housing, battery assembly, cover, and current collector. The housing has an area around the opening that can be laser welded from the outside. This allows the cover and collector to be joined to the housing in that area without internal welding. This simplifies assembly and prevents metal dust from welding inside the cell. The external welding also facilitates electrical connection between the collector and housing.
8. Battery Cell with Current Collecting Member and Protrusion-Supported Tab for Enhanced Welding and Reduced Internal Resistance
Contemporary Amperex Technology Co., Limited (CATL), CONTEMPORARY AMPEREX TECHNOLOGY CO LTD, 2023
Battery cell design to improve safety and overcurrent capability by reducing internal resistance and welding defects. The cell has a case, electrode assembly, end cover, and current collecting member. The end cover seals the cell opening. The current collector is installed between the tab and cover, allowing welding to join them. This avoids uneven tab surfaces that cause welding defects. A protrusion on the cover supports the tab. The collector also has escape recesses to prevent welding the cover. The design reduces internal resistance by connecting current paths through the tab layers. It also improves uniformity and reduces welding defects.
9. Battery Cell with Locked Protective Film Secured to Insulating Member via Pawl or Boss Mechanism
Contemporary Amperex Technology Co., Limited, CONTEMPORARY AMPEREX TECHNOLOGY CO LTD, 2023
Battery cell design with improved reliability and reduced manufacturing complexity. The battery cell has a locked protective film around the electrode assembly that is secured to the insulating member. This prevents issues like film separation or stringing during assembly. The film has features like holes and extensions that engage the insulating member. The film locks to the insulating member using a pawl or boss. The locked film prevents film separation and stringing. This is achieved by a manufacturing method where the film is inserted around the assembly, locked to the insulating member, then the assembly is enclosed in the cell housing.
10. Battery Pack Assembly with Circuit Board Interconnection and Separated Thermal-Electrical Management Zones
SHENLAN AUTOMOBILE TECH CO LTD, SHENLAN AUTOMOBILE TECHNOLOGY CO LTD, 2023
Battery pack assembly for improved safety and assembly efficiency compared to conventional battery packs. The assembly has the battery cells connected in series/parallel using a circuit board between the cells and cases. This reduces the number of connectors compared to directly connecting the cells. The explosion-proof valve is on one end of the cell near the upper case and the electrical connection is on the other end near the lower case. This separates thermal and electrical management areas for improved safety by preventing electrical shorts during thermal runaway. The circuit board also has sensors to monitor cell parameters for protection.
11. Battery Cell Manufacturing Method and Apparatus with Evacuated Chamber Precharging and Gas Exhaust System
LG Energy Solution Limited, LG ENERGY SOLUTION LTD, 2023
Battery cell manufacturing method and apparatus to prevent venting and deformation during initial charging. The method involves placing the battery can with the electrode assembly and electrolyte in an evacuated chamber, precharging the cell in the chamber, and exhausting the gases generated during precharging into the chamber. This prevents internal pressure buildup and external deformation during initial charging. The exhaust chamber can be sealed or have an inert gas injection system. The design allows scaling up battery cell capacity without venting issues.
12. Battery with Internal Chambered Support Structure for Isolated Pressure Relief Mechanism Containment
CONTEMPORARY AMPEREX TECHNOLOGY CO LTD, 2023
Battery design to improve assembly efficiency while maintaining safety. The battery has a support that separates the internal box into chambers. One chamber holds a pressure relief mechanism on the battery cell, and the other chamber holds the rest of the cell and a binder. This allows fixing the cell and binder together in the box while leaving the relief mechanism unobstructed. The support holds the cell steady and prevents binder from entering the relief chamber. This ensures stability and prevents dislodging of the relief mechanism during assembly. The design improves assembly efficiency by allowing multiple cells to be packed tightly together with fixed connections while still allowing functional relief mechanisms.
13. Cylindrical Battery with Grooved Positive Pole and Riveting Ribs for Enhanced Current Capacity
SVOLT ENERGY TECH CO LTD, SVOLT ENERGY TECHNOLOGY COMPANY LTD, 2023
Cylindrical battery assembly method and battery design that improves overcurrent capacity and reduces internal resistance. The method involves insulated and sealed installation of the positive pole in the housing, with a groove and riveting ribs. The positive current collector engages the groove. This provides larger welding area and thinner pole for lower resistance. The riveting block strengthens the positive side. The sealing and insulation between pole and housing prevent shorts.
14. Electric Vehicle Battery with Dual-Sided Busbar Arrangement and Insulation for Multi-Directional Cooling and Impact Protection
VOLKSWAGEN AG, 2023
Battery design for electric vehicles that improves cooling and protection compared to conventional batteries. The battery has cells with conductors connected to busbars covered by insulation. The first busbar is on one side of the cells and the second busbar on the opposite side. This allows cooling from multiple directions through the busbars, preventing hotspots. It also shields the cells from external impacts since the busbars are not aligned.
15. Battery Cell with Pressure Relief Mechanism and Insulating Member to Prevent Electrolyte Leakage
CONTEMPORARY AMPEREX TECH CO LTD, CONTEMPORARY AMPEREX TECHNOLOGY CO LTD, 2023
Battery cell design to improve safety and lifetime by preventing internal electrolyte leakage. The cell has a pressure relief mechanism that activates when pressure or temperature reaches critical values. It also has an insulating member between the cap and electrode assembly. This insulator covers the pressure relief mechanism when the cell is impacted, preventing accidental activation. A passage connects the cell interior to the insulator gap. When pressure builds, the relief mechanism vents through this gap instead of leaking internally. This avoids electrolyte impacting the relief mechanism. The insulator also stops electrolyte flowing into the gap when the cell shakes.
16. Battery Cell with Laser-Welded End Cap Featuring Convex Protrusion and Integrated Electrode Terminal
NINGDE CONTEMPORARY AMPEREX TECH CO LTD, NINGDE CONTEMPORARY AMPEREX TECHNOLOGY CO LTD, 2023
Battery cell design to improve safety and performance. The battery cell has a housing with an opening, and an end cap that can be joined to the housing using laser welding. The end cap has a convex protrusion that separates it from the tab inside the housing. This prevents laser light from passing through gaps during welding and burning internal components. The tab connects to a current collector that bridges the gap and provides uniform current flow to the end cap. The larger housing size improves flow capacity. An electrode terminal is installed in a hole on the bottom wall to access the electrodes.
17. Battery Cell with Insulator-Defined Diversion Channel for Thermosetting Prepolymer Reinforcement
NINGDE CONTEMPORARY AMPEREX TECH CO LTD, NINGDE CONTEMPORARY AMPEREX TECHNOLOGY CO LTD, 2023
Battery cell design that improves safety by preventing explosions during thermal runaway. The cell has a diversion channel between the battery housing and cover that guides a reinforcement material. This channel is formed by an insulator with features that abut against the housing and cover walls. Injecting a thermosetting prepolymer into the channel creates a reinforcement that connects both walls. This enhances the weld strength between the housing and cover, making it greater than the pressure relief valve's threshold. So the valve releases pressure before the housing ruptures.
18. Battery Energy Storage Device with Downward Venting and Integrated Cooling Plates
SAIC MOTOR CORPORATION LTD, 2023
Battery energy storage device for vehicles that improves use safety compared to conventional designs. The device has a lower shell, upper shell, and battery cell assembly sandwiched between. The battery cells have poles and explosion-proof valves below the cells instead of above. This prevents internal cell failures from erupting through the upper shell and into the vehicle cabin. It also allows thermal runaway to vent downward into the lower shell instead of upward. This reduces the risk of cabin fire or damage from exploding cells. The lower shell can also contain cooling plates integrated with the cells for improved thermal management.
19. Battery Cell Design with Same-Side Tab Configuration and Flexible Conductor Integration
CONTEMPORARY AMPEREX TECH CO LTD, CONTEMPORARY AMPEREX TECHNOLOGY CO LTD, 2023
Simplifying the design of battery cells to reduce size and improve safety. The battery cell has a housing, electrode assembly, end cover, and flexible conductor. The electrode assembly has a first tab at the end near the opening and a second tab at the far end. The end cover closes the opening and connects to the first tab. A flexible conductor connects the second tab to the end cover. This allows the positive and negative tabs to be on the same side of the electrode assembly. The flexible conductor prevents short circuits. It also allows the housing to have smaller openings, reducing size. The flexible conductor can pass through the electrode assembly center hole.
20. Battery Cell with Compressible Guide Members for Electrode Expansion Management
SK ENERGY CO LTD, 2023
Battery cell and module design to improve assembly efficiency and prevent deformation during charge/discharge cycling. The cell has an electrode assembly with negative electrode in a compressible guide member and positive electrode in another compressible guide member. This allows the expanding/contracting electrodes to compress the guides instead of deforming the cell housing. The guides are made of elastic material that compresses and expands with the electrodes. This prevents housing deformation and assembly issues when repeated charging/discharging causes expansion/contraction of the electrodes. The compressible guides also improve module assembly efficiency by eliminating the need for external expansion gaskets between the modules.
Get Full Report
Access our comprehensive collection of 62 documents related to this technology
Identify Key Areas of Innovation in 2025
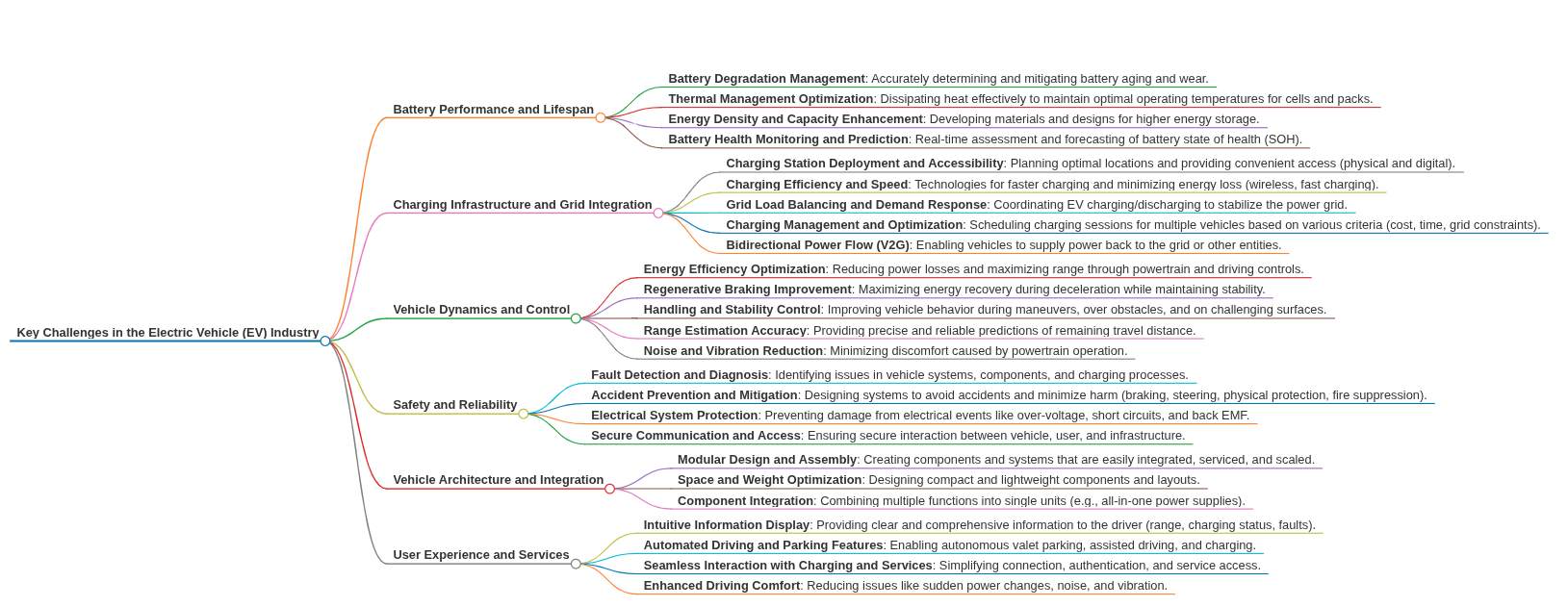