EV Battery Pack Engineering for Vehicle Integration
Electric vehicle battery packs face competing demands of structural integrity, thermal management, and accessibility while housing high-density cell arrays. Current pack designs must maintain compression loads of 5-15 psi across cell stacks, manage thermal paths that can exceed 150°C during fault conditions, and still allow serviceability of critical components.
The fundamental challenge lies in optimizing the mechanical, thermal, and safety interfaces between cells, modules, and vehicle structure while maintaining manufacturability and service access.
This page brings together solutions from recent research—including selective compression systems, structural pack integration methods, serviceability-focused architectures, and advanced degassing mechanisms. These and other approaches demonstrate how battery packaging can enhance both performance and safety in modern electric vehicles.
1. Traction Battery Pack Assembly with Electronics Modules Suspended from Enclosure Cover
Ford Global Technologies, LLC, 2023
Securing electronics modules within a traction battery pack assembly by suspending them from the enclosure cover. The battery pack has an enclosure with a removable cover. An electronics support plate is secured to the cover using brackets and fasteners. The electronics modules are mounted on the support plate. This allows the modules to be easily accessed and serviced by removing the cover, without having to disconnect wiring harnesses and other connections.
2. Solid-State Electrolytes for Next-Generation Energy Storge: Progress, Challenges, and Future Dierctions
dongming liu - EWA Publishing, 2025
Solid-state batteries (SSBs) represent a highly promising solution for the next generation of energy storage systems, offering high density, superior safety performance, and prolonged service life. The development solid-state electrolyte (SSE) materials is particularly critical, as their ionic conductivity interface stability directly determine overall performance batteries. Therefore, we focus on application in new vehicle This paper adopts method literature reading analytical research to review cutting-edge progress various field batteries, revealing key potential improving cycle study concludes that SSEs, including those with carbon nanomaterials, rare earth bromides, composite structures, significantly enhance safety, life However, further needed address challenges like silicon anode volume expansion lithium dendrite suppression, while future efforts should materials, optimization, cost-effective manufacturing, interdisciplinary collaboration accelerate battery commercialization sustainable sector.
3. Automation for Electric Vehicle Battery Pack Disassembly
abu reza md towfiqul islam, matthew dehaven, marshall neipert - Wiley, 2025
ABSTRACT Batteryelectric vehicles (EVs) are growing exponentially. The demand for these batteries is expected to increase sevenfold by 2035. EV reach their end of life when the capacity fades 70%80% new, with some being removed from primary applications even lower levels degradation. These can be used in less demanding applications. disassembly process currently manual, slow, unsafe, and expensive. Automation needed throughput. battery packs feature various continually changing designs form factors, which limit usefulness deterministically programmed robotic solutions. conceptual has attracted attention researchers. However, while many approaches have been proposed, practical implementations lacking. We review proposed concepts describe selected approach, elements partial solutions validated a laboratory setting, including selection commercial solutions, development custom effectors, methodologies detection, localization, classification fasteners. computer vision tasks employed an overhead 2D camera detect type pack approximate localization fasteners, 3D mounted on arm precise ... Read More
4. Battery Module with Integrated Heat Sink Featuring Parallel Flow Path Configuration
LG ENERGY SOLUTION LTD, 2025
Battery module with improved cooling performance for applications like electric vehicles. The module has a heat sink integrated into the lower frame to directly cool the battery cells. The heat sink has a flow path for refrigerant. The flow path has longer parallel paths between the cells versus perpendicular paths. This configuration allows direct cooling of the cells with better cooling efficiency compared to indirect cooling through a separate heat sink. The integrated heat sink also improves space utilization compared to a separate heat sink.
5. Battery Pack with Horizontal Fixing Rod and Recessed Groove Tray for Module Stabilization
LG ENERGY SOLUTION LTD, 2025
Battery pack design for electric vehicles that reduces fabrication time and weight compared to conventional packs. The pack has a horizontal fixing rod inserted into a tube between the battery modules to hold them in place instead of using long bolts. The rod prevents vertical movement. The pack tray has recessed grooves to press-fit and fix the rod ends. This simplifies module mounting and reduces time. The rod provides fixation without bolts. It also allows central crossbeam coupling to increase pack rigidity. The pack can be installed in vehicles.
6. Method and Apparatus for Non-Deforming Battery Cell Stack Mounting Using Dual-Film Interface
LG ENERGY SOLUTION LTD, 2025
Method and apparatus for mounting a battery cell stack in a frame without deforming the frame. The method involves using two films, one attached to each side cover of the frame and the other attached to the battery cell stack. The cell stack and frame are then moved together, with the cell stack sliding into the frame between the films. This allows the cell stack to be mounted without distorting the frame or damaging the cells.
7. Silicone-Coated Glass Fiber Fabric Insulator for Secondary Batteries
LG ENERGY SOLUTION LTD, 2025
Top insulator for secondary batteries with improved heat resistance, chemical resistance, and reduced dust generation during punching compared to conventional insulators. The top insulator is made by applying a silicone rubber to one or both surfaces of a glass fiber fabric. This silicone-coated glass fiber composite has better heat resistance, chemical resistance, and mechanical properties than pure glass fiber. It can withstand temperatures over 250°C, prevent short circuits at high temps, and resist electrolyte corrosion. The silicone coating also reduces dust generation during punching compared to pure glass fiber insulators.
8. Battery Pack with Rigid Shear Plates and Non-Conductive Tether Cables for Enhanced Structural Integrity
GM GLOBAL TECHNOLOGY OPERATIONS LLC, 2025
Battery pack design for electric vehicles that uses rigid shear plates sandwiched between the battery cells to increase stiffness and impact resistance. The shear plates are connected by non-conductive tether cables to prevent buckling during loading. This allows the battery pack to function as a structural member of the vehicle chassis.
9. Aluminum Alloy Bottom Sheet for Battery Boxes with Specific Element Composition
CONSTELLIUM NEUF-BRISACH, 2025
A lightweight, corrosion-resistant, and crush-resistant bottom sheet for battery boxes in electric and hybrid vehicles. The sheet is made of an aluminum alloy with specific composition ranges for elements like Mg, Mn, Si, Fe, Cu, Cr, Zn, and Ti. The alloy has 2.5-4.0% Mg, 0.1-0.8% Mn, 0.4% Si max, 0.5% Fe max, 0.5% Cu max, 0.1% Cr max, 0.1% Zn max, 0.1% Ti max, and rest Al. The alloy balance provides optimal properties like intrusion resistance, corrosion resistance, and stiffness for battery box bottoms.
10. Battery Pack Frame with Protruding Ribs for Aligned Electrode Tab and Circuit Module Connection
SAMSUNG SDI CO LTD, 2025
A battery pack design that simplifies electrical connection between the battery cells and protective circuit module. The battery pack has a frame with protruding ribs that press the cell electrode tabs and circuit module together. This tight contact allows easy laser welding between the tabs and module without a separate jig. The ribs keep the components aligned and pressed together for the welding process.
11. Battery Pack with Integrated Module End Plates for Enhanced Structural Support and Space Efficiency
LG ENERGY SOLUTION LTD, 2025
Battery pack for electric vehicles with improved energy density and structural integrity. The battery pack has a unique design that eliminates unnecessary gaps and space losses between the battery modules and pack case. Instead, the modules themselves provide structural support and rigidity. This is done by integrating the module end plates into the module housing. The pack case is a simple tray with a top cover that seals against the tray edges. This eliminates the need for separate crash beams or gap spaces. The integrated module/pack structure provides maximum space utilization and reduces weight compared to traditional designs.
12. Compact Antenna Coil with Opposing Segments and Conductive Element for Enhanced NFC Performance
GUANGDONG OPPO MOBILE TELECOMMUNICATIONS CORP LTD, 2025
An antenna design for electronic devices like smartphones with near-field communication (NFC) capabilities. The antenna is compact and improves NFC performance in limited device space. The design involves an antenna coil with segments on opposite sides of a winding center. A conductive element is placed opposite one segment to cancel its magnetic field. This reduces magnetic field cancellation inside the coil, improving NFC performance.
13. Coupled Electro-Thermal FEM with Geometric Symmetry Constraints for Modular Battery Pack Design
yingshuai liu, chenxing liu, jianwei tan - Multidisciplinary Digital Publishing Institute, 2025
This study investigates the structural integrity and dynamic behavior of symmetry-optimized battery pack systems for new energy vehicles through advanced finite element analysis. It examines with mechanically stable thermally adaptive potentials. Leveraging geometric symmetry principles, a high-fidelity three-dimensional (3D) model was constructed in SolidWorks 2023 subjected to symmetry-constrained static analysis on ANSYS Workbench 2021 R1 platform. The performance systematically evaluated under three critical asymmetric loading scenarios: emergency left/right turns braking conditions, particular attention symmetric stress distribution patterns. numerical results confirmed initial designs compliance mechanical requirements while revealing deformation characteristics dominant mode shapes. Building upon symmetry-enhanced topology configuration, novel lightweight strategy implemented by substituting Q235 steel ZL104 aluminum alloy. While has been widely studied, thermal gradients packs can induce expansions. For example, uneven cooling may cause localized warping alloy shells. mult... Read More
14. Advances in the Battery Thermal Management Systems of Electric Vehicles for Thermal Runaway Prevention and Suppression
le duc tai, mooyeon lee - Multidisciplinary Digital Publishing Institute, 2025
In response to the global imperative reduce greenhouse gas emissions and fossil fuel dependency, electric vehicles (EVs) have emerged as a sustainable transportation alternative, primarily utilizing lithium-ion batteries (LIBs) due their high energy density efficiency. However, LIBs are highly sensitive temperature fluctuations, significantly affecting performance, lifespan, safety. One of most critical threats safe operation is thermal runaway (TR), an uncontrollable exothermic process that can lead catastrophic failure under abusive conditions. Moreover, propagation (TRP) rapidly spread failures across battery cells, intensifying safety threats. To address these challenges, developing advanced management systems (BTMS) essential ensure optimal control suppress TR TRP within LIB modules. This review systematically evaluates cooling strategies, including indirect liquid cooling, water mist immersion phase change material (PCM) hybrid based on latest studies published between 2020 2025. The highlights mechanisms, effectiveness, practical considerations for preventing initiation suppre... Read More
15. Modular battery pack design and serviceability in electric vehicles
oluwapelumi joseph adebowale - GSC Online Press, 2025
The rapid growth of electric vehicles (EVs) has heightened the demand for battery systems that not only deliver high performance but are also efficient to maintain, scale, and recycle. While much industrys focus been on energy density cost optimization, serviceabilitydefined by ease maintenance, diagnostic accessibility, component-level replacementhas emerged as a critical yet underprioritized factor. Traditional EV packs, often monolithic tightly integrated, pose significant challenges field technicians, including prolonged disassembly times, high-voltage safety risks, limited transparency. These limitations increase downtime, escalate service costs, constrain long-term sustainability platforms. This paper explores transformative role modular pack design in improving serviceability lifecycle efficiency across ecosystems. From broader perspective, it examines how modularity facilitates streamlined maintenance workflows, safer handling procedures, standardized replacement strategies. analysis narrows compare philosophies leading OEMs such Tesla, GM, Rivian, Lucid, evaluating ... Read More
16. Assessment of thermal characteristics in diverse lithium-ion battery enclosures and their influence on battery performance
n mahiban lindsay, m emimal - Institute of Advanced Engineering and Science (IAES), 2025
Battery technology is an emerging research domain within the automotive sector, with a focus on various battery chemistries such as Li-ion, LiFePO4, NMC, and NaCl, well specialized cells like LiSOCl2. These are crucial in advancing electric vehicle (EV) technology. Batteries available different packaging formats, including prismatic, cylindrical, pouch designs, each tailored to diverse operational environments. This study investigates impact of these packages overall performance. Additionally, it assesses influence temperature efficiency, aiming identify optimal range for maximum A significant part focuses development efficient thermal management (BTM) systems, which designed control maintain desired range, thereby enhancing efficiency. The outcomes this provide valuable insights improving reliability efficiency EV batteries. findings ensuring performance safety across field conditions. Automotive manufacturers suppliers can leverage refine their product dependability By through improved effective management, contributes significantly advancement technology, making vehicles more reli... Read More
17. Battery Box with Auxiliary Member Enclosing Exhaust Channel for Directional Gas Discharge
CONTEMPORARY AMPEREX TECHNOLOGY LTD, 2025
Battery box design to enable directional exhaust of gas from a pressure relief valve when installed in an enclosed electrical appariment like an electric vehicle. The battery box has an auxiliary member that encloses an exhaust channel with an external port. The pressure relief valve mounts through the channel exit. This allows gas expelled by the valve to flow through the channel and out the auxiliary member port instead of inside the battery box. This directs the exhaust to the vehicle's existing air outlet, preventing backpressure buildup in the battery compartment.
18. Battery Pack with Single Large Assembly and Integrated Reinforcing Member
BYD CO LTD, 2025
Battery pack design with simplified assembly, improved structural strength, higher space utilization, and energy density compared to conventional packs. The pack uses a single large battery assembly inside the pack housing instead of multiple smaller modules. The cells are connected by a reinforcing member. This assembly serves as a crossbeam/longbeam to reinforce the pack structure. The cells are arranged with misaligned sides to prevent deformation. The pack avoids additional internal frames/beams. The large assembly supports the pack and provides strength. This reduces pack weight, simplifies assembly, and allows higher cell density compared to modular packs.
19. Power Storage Module Housing with Through Holes and Protrusion-Equipped Duct Cover for Gas Venting
PANASONIC IP MAN CO LTD, 2025
Power storage module design with improved gas venting to prevent internal pressure buildup and cell damage. The module has a housing with multiple cells and through holes connecting them to the outside. A duct cover seals the cell exhaust openings. The cover has discrete protrusions facing the cell-free areas of the housing. This allows gas to escape through the holes when cells vent, preventing blockage by the duct cover collapsing. The protrusions stop gas flow from other cells. This ensures venting even if the cover is deformed from impact.
20. Driving circular economy in electric vehicle batteries
eduard piqueras, carlos a rios perez, v i vargas, 2025
Driving circular economy in electric vehicle batteries MARBEL project has designed, developed and demonstrated new modular, compact, lightweight high-performance battery packs together with flexible robust management systems for vehicles plug-in hybrids, while maintaining safety levels, allowing fast, high quality cost-effective large-scale production following ecodesign principles.
Get Full Report
Access our comprehensive collection of 406 documents related to this technology
Identify Key Areas of Innovation in 2025
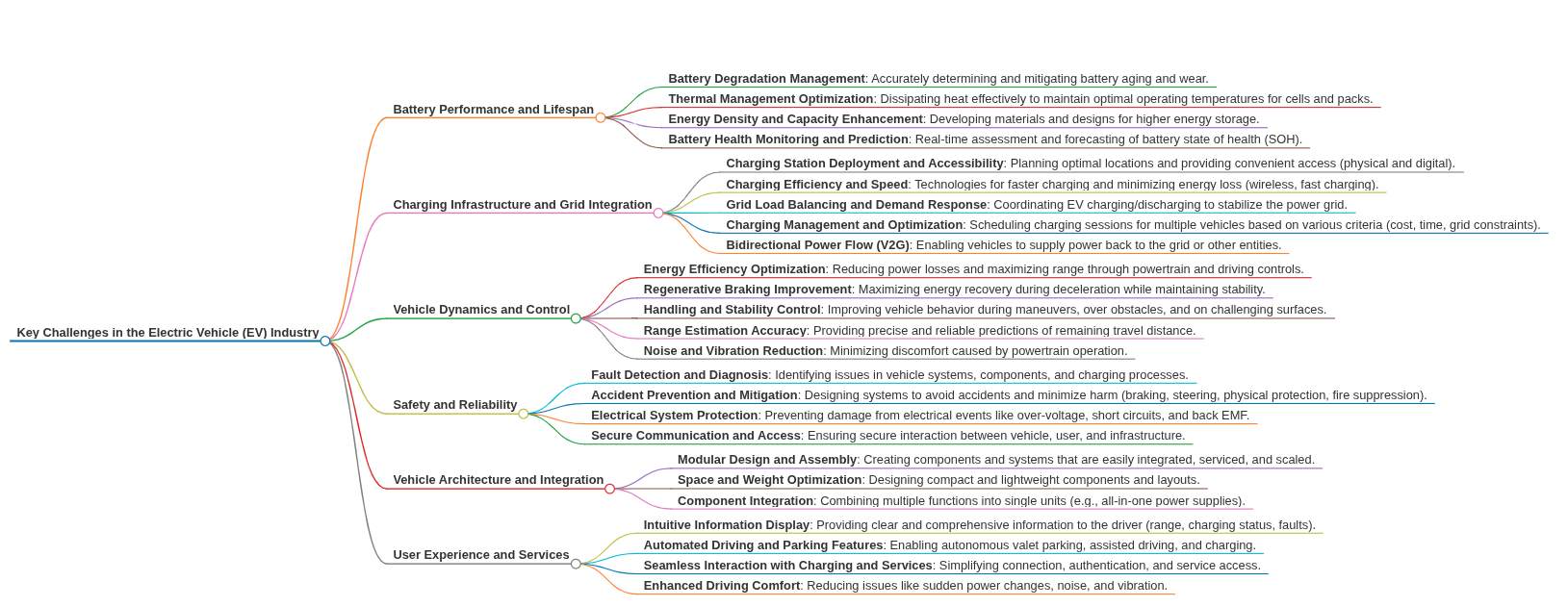