EV Battery Electrode Materials for Enhanced Safety
Modern EV battery electrodes operate at increasingly high energy densities, with cathode materials routinely experiencing temperatures above 60°C and current densities exceeding 4 mA/cm². Under these conditions, conventional electrode materials can develop microstructural instabilities, leading to capacity fade and potential safety concerns through dendrite formation and thermal hotspots.
The fundamental challenge lies in developing electrode materials that maintain structural integrity and electrochemical stability under high-stress operating conditions while remaining cost-effective for mass production.
This page brings together solutions from recent research—including self-supporting electrodes with fibrous nanostructures, dendrite-suppressing 3D graphene-carbon hybrid architectures, concentration gradient materials with protective barrier layers, and thermally-optimized composite structures. These and other approaches focus on practical implementations that enhance both safety and performance in commercial EV applications.
1. Core-Shell Positive Electrode Material with Transition Metal Gradient and Barrier Layer for Lithium-Ion Batteries
ECOPRO BM CO LTD, 2024
Positive electrode material for lithium-ion batteries that addresses the problem of transition metal elution from lithium-rich layered oxides. The material is a core-shell structure with a concentration gradient of transition metals from the core to shell. The shell region has higher concentrations of transition metals less prone to elution. This reduces transition metal elution from the core. A barrier layer on the shell further suppresses transition metal elution. The core-shell structure and barrier layer prevent transition metal contamination of the battery cathode. The lithium-rich layered oxide has a unique composition with coexisting phases from the C2/m and R3-m space groups.
2. Positive Electrode Composite Material with Specific Additives for Reduced Expansion Forces in Lithium Ion Secondary Batteries
NINGDE CONTEMPORARY AMPEREX TECH CO LTD, NINGDE CONTEMPORARY AMPEREX TECHNOLOGY CO LTD, 2024
A positive electrode composite material for lithium ion secondary batteries that improves cycle life and safety by reducing expansion forces during charge/discharge cycling. The positive electrode contains a conventional active material along with specific positive electrode additives selected from sodium/potassium oxides, sulfides, peroxides, azides, and carbon oxides. These additives open up the negative electrode during charge/discharge to reduce particle rearrangement and expansion.
3. Cathode Material with Lithium Nickel Oxide Coated by Solid Electrolyte and Lithium-Containing Ether Oligomers
TIANJIN BAMO TECH CO LTD, TIANJIN BAMO TECHNOLOGY CO LTD, 2023
Cathode material for lithium-ion batteries with improved cycling stability and safety, especially in solid-state batteries. The cathode has a coating layer on the lithium nickel oxide that contains solid electrolyte and lithium-containing ether oligomers. The ether oligomers form chemical bonds with the lithium nickel oxide and electrolyte, providing flexible and integral coating with enhanced stability compared to traditional coatings. The coating improves cycle life, reduces interface impedance, and mitigates safety issues like electrolyte decomposition at high nickel states.
4. Battery Electrode Material Comprising Li-Ti-O and Mo-O Active Components with Solid Electrolyte Containing Li-M-X
PANASONIC INTELLECTUAL PROPERTY MANAGEMENT CO LTD, PANASONIC IP MAN CO LTD, 2022
Battery electrode material with improved charge/discharge efficiency and capacity for lithium-ion batteries. The electrode contains two active materials, one with Li, Ti, and O, and the other with Mo and O. This combination reduces expansion/contraction during charging/discharging compared to using just one active material. It improves safety and capacity while maintaining efficiency. The electrode can also have a solid electrolyte containing Li, M, and X (M=metal or metalloid, X=F, Cl, Br, I) to further enhance output characteristics.
5. Lithium-Ion Battery Electrode with Composite Layer of Active Material, High Dielectric Oxide Solid, and Electrolyte
HONDA MOTOR CO LTD, 2022
Lithium-ion battery electrode design with improved thermal stability and volumetric energy density for high-nickel cathodes. The electrode contains a composite layer with three components: the active material, a high dielectric oxide solid, and electrolyte. The volume ratio of electrolyte to high dielectric solid is 99:1 to 76:24. This configuration allows the electrolyte to fill gaps between active material particles along with the solid, improving ionic conductivity and preventing dry-out. The high dielectric solid also provides stability benefits.
6. Lithium-Ion Battery with Aluminum Current Collectors and High-Ni Cathode Featuring Non-Uniform Co Distribution
Camux Power LLC, CAMX POWER LLC, 2022
Lithium-ion battery design that provides improved safety, cycling performance, and storage stability over conventional lithium-ion batteries. The design uses specific electrode materials and current collectors to overcome issues like overdischarge, capacity fade, and parasitic reactions. The negative electrode uses an electrochemically active material coated on an aluminum current collector. The aluminum alloying potential prevents copper dissolution issues. The cathode uses a high-Ni polycrystalline material with non-uniform Co distribution. This reduces transition metal dissolution. The aluminum collector can also be used for the cathode. The cells can discharge to 0V, store for long periods, and cycle at low temperatures without decomposition. The aluminum collectors enable overdischarge without copper issues. The cells also have improved rate performance, cycle life, and tolerance to extreme mechanical misuse compared to conventional
7. Lithium-Ion Battery with Metal Oxide Coated Nickel-Cobalt-Manganese Positive Electrode
SHENZHEN XINCOPORAL SCIENCE AND TECH CO LTD, SHENZHEN XINCOPORAL SCIENCE AND TECHNOLOGY CO LTD, 2022
Lithium-ion battery with improved performance and lifetime by using a coated positive electrode material. The coating is made of a metal oxide like aluminum oxide, titanium oxide, magnesium oxide, zirconium oxide, or bismuth oxide. The coating is applied to the positive electrode active material, which is a nickel-cobalt-manganese ternary oxide. The coating layer prevents direct contact of the active material with the electrolyte, reducing ionic dissolution and migration. The coating also improves battery cycle life by inhibiting corrosion of the positive electrode. The coating thickness is 0.05-5% of the active material mass. The battery also contains a specific composition of lithium salt, organic solvent, and compound in the electrolyte to balance ionic conductivity and battery
8. Binder-Free Self-Supporting Electrodes with Fibrous Nanostructures for Rechargeable Batteries
BROOKHAVEN SCIENCE ASSOCIATES, LLC, 2021
Binder-free, self-supporting electrodes for rechargeable batteries that can be easily regenerated and reused without disassembly. The electrodes have active materials like cryptomelane-type manganese dioxide (OMS-2) that form fibrous nanostructures without binders or current collectors. These self-supporting electrodes can be thermally regenerated by heating under air to restore capacity after cycling. The regenerated electrodes can then be put back in the battery or a new one. The lack of binders allows the active materials to be self-supporting and regenerated without disassembly.
9. Lithium-Ion Battery with Aluminum Current Collector and Lithium Titanate Anode
Camx Power LLC, CAMX POWER LLC, 2021
Lithium-ion battery with improved safety, dischargeability, and cycling performance compared to conventional lithium-ion batteries. The battery uses lithium titanate (LTO) as the negative electrode material coated on an aluminum current collector instead of graphite or copper. This allows discharging to 0V without overdischarge protection. The aluminum collector provides a lower potential than copper or titanium, preventing issues like copper dissolution. The battery also uses a polycrystalline cathode with non-uniform Co distribution for better cycling. The aluminum collector, LTO negative, and polycrystalline cathode enable deep discharge, high capacity, and cycle life while avoiding overdischarge and decomposition issues of conventional lithium-ion batteries.
10. Porous Matrix-Based Lithium Battery Anodes for Dendrite Suppression and Enhanced Cycling Stability
THE BOARD OF TRUSTEES OF THE LELAND STANFORD JUNIOR UNIVERSITY, 2021
Lithium battery anodes with reduced dendrite growth and improved cycling stability through using a porous matrix as a host for the lithium metal. The matrix provides a stable structure that reduces the volume change during cycling compared to pure lithium foil. The matrix also has high surface area for uniform lithium deposition. This prevents dendrites and improves cycling performance. The matrix can be made of materials like graphene, nanotubes, or mesoporous carbon. The lithium infuses into the matrix during preparation and during cycling. This provides a composite anode with reduced dimension change, dendrite suppression, stable electrode interface, and uniform lithium deposition.
11. Lithium Secondary Battery with High-Nickel Single-Crystal Positive Electrode and Conductive Additive
SHENZHEN BAK BATTERY CO LTD, 2021
Lithium secondary battery with improved energy density, cycle life, and safety compared to conventional lithium-ion batteries. The battery uses a high-nickel, single-crystal positive electrode material with a conductive additive to provide high capacity, stability, and safety. The electrolyte is a non-aqueous organic solvent mixture. This design allows increasing energy density without compromising safety by using a high-nickel positive electrode with single crystal structure and conductive additive. The non-aqueous electrolyte further enhances cycle life and prevents swelling.
12. Electrode Assembly with Selective Bonding for Reduced Short Circuit Risk in Temperature-Variable Conditions
KABUSHIKI KAISHA TOYOTA JIDOSHOKKI, 2019
Electricity storage device, such as a rechargeable battery, with an electrode assembly configuration that reduces short circuit heat generation when the electrodes contact due to separator contraction during temperature changes. The electrode assembly has overlapping electrodes with sections free of active material at the ends. The separators have strong bonding sections near the free-end sections and weaker bonding sections near the active material sections. This allows the separators to contract and move apart at the active material sections to prevent shorting, while the strong sections at the free-end sections hold the electrodes together and prevent separation.
13. Lithium Ion Battery Cell with Rectangular Shell, Gasket-Separated Core, and Coiled Electrode Layers
SHENZHEN BYD AUTO R&D COMPANY LIMITED, 2019
Lithium ion battery cells with improved performance, safety, and longevity for electric vehicles. The battery cells have a core wrapped in a rectangular shell with gaskets to prevent contact between the core and end caps. This prevents short circuits. The core can have coiled electrode layers for high power density. The electrode materials are mixed crystal lithium iron phosphate with additional metal oxides for better cycling. The gaskets compress the core away from the caps to prevent internal hotspots. The rectangular shape reduces stress concentrations compared to cylindrical cells. The improved cell design prevents failures like internal shorts, hotspots, and thermal runaway.
14. Lithium Secondary Battery with Cathode Featuring Metal Concentration Gradient and Single Crystal Structure
SK INNOVATION CO LTD, 2019
Lithium secondary battery with improved lifetime, overcharge, and penetration safety. The battery uses a cathode with a composite active material that has a metal concentration gradient between the center and surface. This gradient prevents metal migration during overcharge and prevents excessive heat generation if the battery is punctured. The cathode also contains a second active material with a single crystal structure. This provides stability and reduces heat generation during forced internal short circuits.
15. Lithium Battery with Modified Ternary Cathode, Nitrogen-Doped Carbon Coated Silicon Anode, and Enhanced Electrolyte and Separator
Jiangsu Tianpeng Power Supply Co., Ltd., 2019
High-capacity, high-safety, and fast charging lithium battery with improved performance through optimized materials and additives. The battery uses modified rich ternary cathode materials, nitrogen-doped carbon coated silicon anode, specific electrolyte additives, and a modified separator. The cathode uses lithium ion conductor coatings on ternary materials to enhance cycling and reduce capacity fade. The anode uses nitrogen-doped carbon coating on silicon to prevent expansion and capacity loss. The electrolyte has additives for SEI film formation, overcharge protection, flame retardancy, and temperature improvement. The separator is modified to prevent carbon migration. These materials and additives enhance battery life, safety, and charging rates.
16. Composite Positive Electrode Material with Differentiated Particle Sizes and Coatings for Lithium-Ion Batteries
LG Chem, Ltd., 2019
A mixed positive electrode material for lithium-ion batteries that improves both output voltage and cycle life at high temperatures. The material is a composite of two types of positive electrode active materials with different particle sizes. The composite contains a large-grain material with 10 μm or greater average diameter and a small-grain material with 5 μm or less average diameter. The two materials are separately coated with different materials between lithium triborate (or lithium boran oxide) and metal oxide. This coating composition allows high voltage operation while maintaining stability at elevated temperatures.
17. Electrode Materials with Electrochemically Applied Amorphous Carbon Coating and Specific D/G Ratio
HYDRO-QUEBEC, 2019
Carbon-coated electrode materials for lithium-ion batteries with improved performance and cycle life compared to uncoated materials. The carbon coating is applied using an electrochemical process. The carbon coating protects the active material particles during cycling, reducing capacity fade and improving cycle life. The coating is amorphous carbon with a D/G ratio of 2-3.5 as determined by Raman spectroscopy. The carbon coated particles can be used in lithium-ion battery electrodes, with potential benefits in applications like electric vehicles. The carbon coating also provides a buffer layer to reduce volume changes during cycling, further improving cycle life.
18. Solid-State Lithium-Ion Battery with Organic-Inorganic Composite Polymer Electrolyte and Porous Silicon-Based Negative Electrode
Xiamen Gaorong New Energy Technology Co., Ltd., 2018
High-capacity solid-state lithium-ion battery with improved energy density and safety compared to conventional liquid electrolyte batteries. The battery uses a novel organic-inorganic composite polymer electrolyte made by copolymerizing PVDF, TPU, PI, and LGPS. The composite electrolyte film has high ionic conductivity and prevents corrosion and decomposition issues of liquid electrolytes. The battery also uses a spherical porous silicon-based composite as the negative electrode material. This improves conductivity and reduces volume expansion compared to graphite. The composite electrolyte and negative electrode maximize energy density by leveraging high-capacity manganese-rich cathodes.
19. Manufacturing Method for Lithium Battery Positive Electrode Materials with Barrier-Layer-Coated Core and Continuous Gradient Shell
ECOPRO BM CO., LTD., 2017
A method to manufacture lithium battery positive electrode materials with a concentration gradient that improves stability and cycling life compared to conventional materials. The method involves coating the core particle with a barrier layer to prevent diffusion of transition metals during subsequent thermal treatment. This prevents degradation at high temperatures while still allowing a continuous concentration gradient between the core and outer shell layers. The barrier layer prevents sharp compositional boundaries and interfaces that can cause defects and instability.
20. Composite Electrode Material with Oxide Nanoparticle-Coated Active Material and Integrated Conductive Layer
JIUJIANG TINCI MATERIALS TECH LTD, JIUJIANG TINCI MATERIALS TECHNOLOGY LTD, TSINGHUA UNIVERSITY, 2017
Composite electrode material for all-solid-state lithium-ion batteries with reduced interface resistance, high energy density, safety, and chemical stability. The composite electrode contains a coated active material, electrolyte, filler, and conductive agent. The active material is coated with oxide nanoparticles to reduce lithium ion resistance. The coating contains electrolyte, filler, and conductive agent to further reduce resistance. This improves interface compatibility and reduces resistance compared to bare active materials. The composite electrode is used in all-solid-state lithium-ion batteries with solid electrolyte layers between positive and negative electrodes.
Get Full Report
Access our comprehensive collection of 45 documents related to this technology
Identify Key Areas of Innovation in 2025
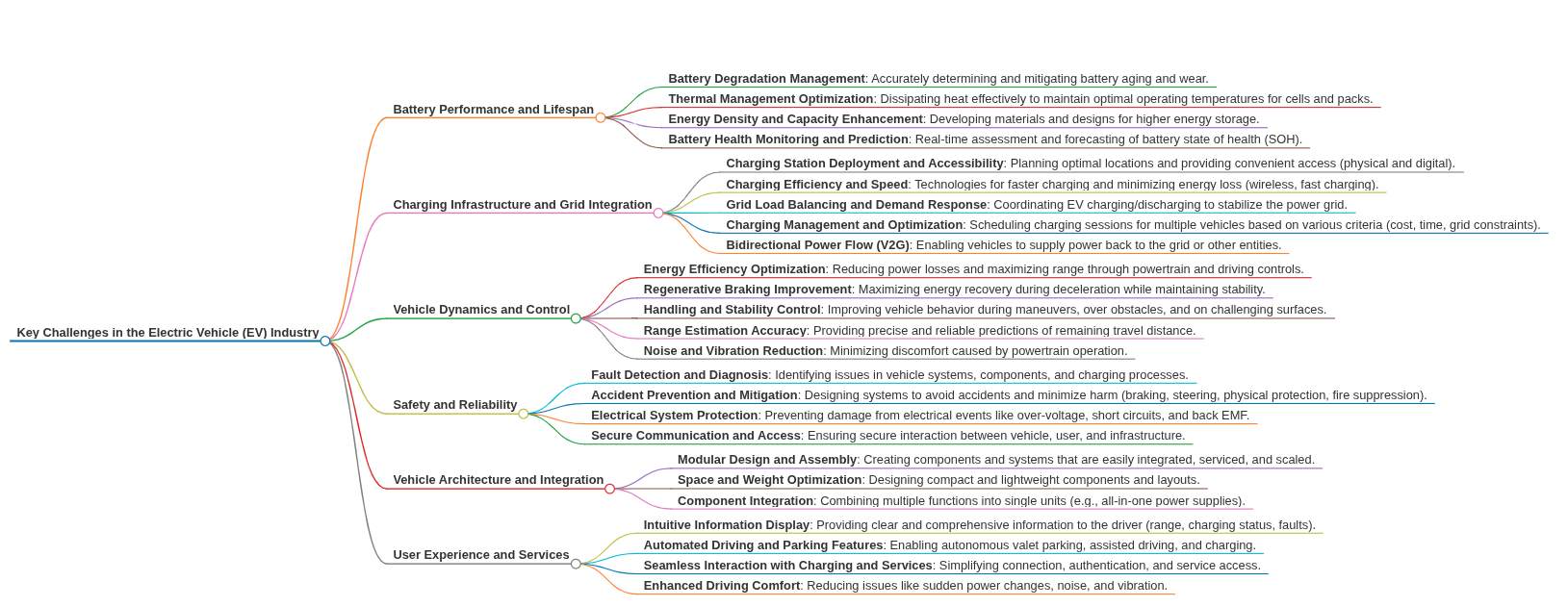