Materials for EV Battery Electrical Insulation
In modern EV battery packs, cells are densely packed to maximize energy density, with spacing between cells often less than 1mm. During normal operation, these cells can experience voltage differentials exceeding 400V, while thermal events can drive temperatures above 150°C—creating conditions where even minor insulation failures risk catastrophic short circuits.
The fundamental challenge lies in maintaining reliable electrical isolation between cells while minimizing the space dedicated to insulation materials and preserving thermal management capabilities.
This page brings together solutions from recent research—including multi-layer insulating films with temperature-responsive properties, gel-based adhesion systems that prevent delamination, and innovative spacer designs that combine mechanical and electrical protection. These and other approaches focus on practical implementations that balance safety requirements with energy density targets in production vehicles.
TABLE OF CONTENTS
1. Multi-Layer Insulation Sheets and Composite Barriers for Thermal Runaway Prevention
Thermal runaway in electric vehicle (EV) battery systems represents one of the most significant safety challenges for manufacturers and designers. Traditional insulation materials like silicone foam and mica boards have served basic needs but exhibit critical limitations in mechanical toughness, cost-effectiveness, and structural integrity under extreme conditions.
A significant advancement in addressing these limitations comes in the form of multi-layer aerogel composite insulation sheets with a sandwich structure. These sheets feature an aerogel core encapsulated between two protective layers, creating a configuration that substantially enhances both compression and bending resistance while maintaining excellent thermal insulation properties. The encapsulation design serves a dual purpose: it prevents dust generation from the fragile aerogel core and mitigates material aging, resulting in a more durable and integration-friendly solution for EV battery packs. This approach, detailed in a multi-layer aerogel composite insulation sheet design, represents a substantial improvement over conventional fragile insulators.
Thermal isolation systems have also evolved to address both temperature stabilization and containment of runaway events. An innovative multi-layer thermal isolation system integrates oxidized polypropylene nitrile fiber, high-silica fabrics, and stainless-steel foil facing. Each component in this system serves a specific function: thermal insulation, fire resistance, or mechanical containment. Working together, these layers maintain battery temperatures closer to optimal operating conditions (approximately 25°C), which not only extends battery life but significantly improves occupant safety by providing critical evacuation time during thermal events. This system aligns with global safety standards including GTR20 and GB/T38031.
For applications requiring extreme temperature resilience, a composite shell structure combines a ceramic slurry-based heat-proof layer with a silica aerogel thermal insulation layer. The heat-proof component features ceramic slurry and silicon carbide fiber cloth in a dual configuration that delivers superior ablation resistance. The insulation layer, constructed from nano-silica aerogel composite felt, provides exceptional thermal isolation properties. This integrated design can withstand direct exposure to 1300°C flames for 30 minutes without delamination or structural failure. Notably, it maintains post-ablation flexural strength above 100 MPa, substantially outperforming traditional materials like mica or ceramic fiber sheets.
Addressing the dual challenge of thermal insulation and lateral heat dissipation, a aerogel flame-retardant sheet integrates two aerogel-based insulation layers with strategically positioned copper foil or graphene heat-conducting layers. The conductive components are geometrically arranged to facilitate downward heat flow, effectively preventing vertical thermal propagation while maintaining lateral cell isolation. This configuration combines fire resistance, directional heat management, and mechanical flexibility in a lightweight, compact form factor suitable for high-density EV battery systems.
2. Phase Change and Fire-Suppressing Materials for Heat Absorption and Containment
As EV manufacturers push toward higher energy densities, effective thermal management becomes increasingly critical. Phase change materials (PCMs) represent a sophisticated approach to passive thermal management, offering advantages beyond conventional insulation.
An innovative insulation layer featuring a compressible structure embedded with PCMs provides both thermal insulation and active heat absorption. This endothermic phase change mechanism activates at predefined temperatures, absorbing energy through phase transitions and delaying thermal propagation. A key advancement in this technology is the incorporation of multiple activation temperatures within the PCM composition, creating a tiered thermal response system that adapts to various levels of heat stress. The compressible structure accommodates battery cell swelling during charge-discharge cycles, maintaining structural integrity and electrical contact throughout the battery's operational life.
This insulation layer goes beyond thermal absorption by incorporating an active fire suppression mechanism. When critical temperatures are reached, the dual-function thermal insulation structure not only undergoes phase change but also releases fire-extinguishing fluid. This active suppression capability represents a significant advancement over passive barriers, addressing potential ignition sources while maintaining mechanical compliance. The modular design allows integration across diverse EV battery architectures, offering scalability without compromising safety or performance.
Complementing these active thermal management approaches is a composite battery pack shell structure engineered for extreme thermal and mechanical stress resistance. Traditional materials like mica and ceramic fibers often fail under high-temperature conditions due to poor ablation resistance and structural degradation. The laminated ceramic composite shell addresses these limitations through a heat-proof layer made from ceramic slurry reinforced with SiC fibers, combined with a thermal insulation layer composed of nano-silica aerogel and pre-oxidized SiC felt. This dual-layer system maintains structural integrity and thermal insulation even under flame ablation at 1300°C for up to 30 minutes, with minimal material degradation.
The composite shell's primary advantage lies in its integration of high-temperature resistance with mechanical robustness in a lightweight, scalable format. The optimized ceramic slurry composition creates a cross-linked network that enhances flexural strength while resisting delamination and burn-through. The nano-aerogel materials further reduce thermal conductivity, minimizing heat transfer to internal battery modules. The structure also supports safe pressure relief during thermal incidents, reducing cascading failure risks while remaining compatible with existing manufacturing techniques.
3. Ceramifiable Silicone and Thermally Reactive Polymers
The risk of thermal runaway and short circuit propagation in high-capacity lithium-ion batteries has driven the development of advanced insulation materials that can maintain both thermal and mechanical integrity under extreme conditions.
Conventional insulation materials like aerogel felts often collapse under elevated pressure and temperature, losing their barrier function when most needed. A breakthrough solution comes in the form of ceramifiable elastomeric silicone material positioned between battery cells. This material consists of a cured silicone rubber matrix enriched with high-molecular-weight polydiorganosiloxane gums, flame retardants, and cerium hydroxide fillers. Unlike traditional solutions, this silicone-based insulation can partially transform into a ceramic-like structure under extreme heat, maintaining both thermal insulation and mechanical integrity at temperatures above 500°C and pressures exceeding 0.9 MPa.
The material's ability to undergo in-situ ceramification during thermal events represents its most significant innovation. This transformation prevents heat and flame propagation between cells while preserving structural form, contrasting sharply with aerogels that collapse under similar conditions. The silicone insulation also eliminates health hazards associated with silica particle dispersion from aerogels and doesn't require special handling measures. Its adaptability to various battery module architectures and compatibility with existing manufacturing processes makes it a practical alternative for thermal management in EV battery systems.
For battery pack enclosures requiring both thermal protection and structural strength, a multi-layer composite shell structure offers comprehensive protection. This design features a dual-layer ceramic slurry system composed of silicone resin and ceramic particles applied over silicon carbide fiber cloth to form a heat-proof layer. A thermal insulation component made from nano-silica aerogel composite lies beneath this protective layer. Together, these components create a barrier capable of withstanding direct flame exposure at temperatures up to 1300°C for 30 minutes with minimal material loss and structural degradation.
The composite shell's integrated ablation resistance and mechanical reinforcement allows the battery pack to maintain flexural strength even after exposure to extreme thermal conditions. While traditional materials degrade or fail under such stress, this solution maintains post-ablation mechanical strength above 100 MPa. The optimized slurry formulation reduces dependency on costly silicon carbide fibers and enhances process efficiency through solvent-stabilized dispersion, enabling the creation of thin, lightweight, high-performance battery enclosures.
4. Gel-Based and Adhesive Insulation Systems for Cell Bonding and Delamination Prevention
Battery pack assembly presents unique challenges for insulation integrity. Conventional methods apply insulation films to cell surfaces using adhesive glue, creating a three-layer structure (battery core, insulating film, and structural adhesive). This approach is labor-intensive and prone to manufacturing defects including wrinkles, bubbles, and misalignments. The low bonding strength of the adhesive layer further compromises mechanical integrity.
A novel gel-based insulation system addresses these limitations by using a colloid layer to bond the insulating film directly to the battery cell. This approach eliminates the separate adhesive layer, simplifying assembly while improving bonding uniformity and enhancing structural strength. The design also supports integration with liquid cooling plates, promoting efficient thermal management while improving insulation reliability and reducing material costs.
Internal damage from friction and vibration between adjacent cells represents another critical failure mode in EV battery systems. In tightly packed configurations, mechanical stress during charge-discharge cycles can lead to separator wear and electrode exposure. A gel-supported insulating layer system mitigates these risks by placing a resilient insulating layer between the largest opposing surfaces of adjacent cells. This configuration absorbs mechanical stress while preventing alignment shifts and internal short circuits caused by separator damage. Optimized electrode structures further ensure stable electrochemical behavior, reducing lithium dendrite formation risk and enhancing both electrical safety and mechanical durability.
Internal short circuits between the electrode group and cell casing represent a third common failure mode in high-capacity lithium-ion batteries. Traditional gaskets often lack the mechanical and electrical robustness needed for modern applications. A multi-functional conjoined insulating gasket integrates a phenolic resin-based insulating layer with waterproof and non-slip components. The gasket effectively isolates the pole group from the casing while resisting moisture ingress and maintaining secure positioning during vibration or thermal cycling. This integrated design improves assembly consistency while minimizing internal displacement and electrical faults.
5. Elastomeric and Flexible Insulation Layers for Mechanical Compliance
The close proximity of conductive components in EV battery packs necessitates robust electrical isolation that can withstand mechanical stress. Traditional insulation materials like Kapton and Nomex often fail to meet durability requirements, as they can be punctured or torn by sharp or abrasive surfaces during normal vehicle operation.
The elastomeric insulation system offers a solution through polyurethane-based elastomers with high tensile strength and elongation properties. These flexible materials provide superior resistance to puncture and mechanical deformation, maintaining electrical separation even under dynamic stress conditions. Their ability to conform to irregular geometries while resisting degradation significantly enhances long-term reliability and safety.
Beyond electrical insulation, battery systems require materials that accommodate mechanical expansion and thermal stress between cells. The multi-layer thermal insulation buffer pad integrates ceramic fiber cotton, silicone rubber, and glass fiber into a cushion pad placed between battery cells. This structure provides high-temperature resistance during thermal events while acting as a mechanical buffer to absorb expansion forces. The silicone rubber layer adds flexibility and compliance, while ceramic and glass fiber layers enhance thermal insulation. This composite prevents heat and pressure propagation between cells, improving structural integrity and extending operational life.
Advancing flexible insulation technology further, the multi-layer thermal isolation system employs nonwoven layers made from oxidized polypropylene and polyacrylonitrile, high silica layers, and stainless steel foil to create a resilient insulation barrier. This system localizes and contains heat and fire during thermal runaway while maintaining mechanical integrity under stress. Its strategic placement around battery cells improves passive thermal management and enhances occupant safety by delaying fire and toxic gas spread, providing critical evacuation time. The lightweight nature and acoustic insulation benefits of these fibrous materials contribute to system-level performance and comfort.
6. Spacer and Gasket Structures for Mechanical and Electrical Isolation
Spacers and gaskets serve critical functions in battery pack design, providing both mechanical stability and electrical isolation. Conventional spacers often fail to provide immediate insulation during physical damage events, creating vulnerability to short circuits.
An innovative approach addresses this limitation through a spacer filled with insulating coating liquid encapsulated in an elastic pouch. This design responds dynamically to physical damage: when penetrated or impacted, it releases an insulating liquid that rapidly forms a protective film over the damaged area, providing instantaneous electrical insulation. The insulating medium contains finely dispersed fluoropolymer and inorganic oxide particles in a binder matrix, ensuring uniform coating and effective isolation. This responsive mechanism significantly enhances battery safety by preventing fire or explosion following physical damage.
Thermal insulation materials in battery packs must withstand extreme temperature events while maintaining structural integrity. The silica aerogel ceramic fiber composite sheet addresses limitations of conventional materials that suffer from ablation, ignition, or structural inconsistency. This composite integrates a ceramic fiber cloth base with a silica aerogel matrix, encapsulated using flame-retardant films or coatings. Tight dimensional tolerance and uniform density eliminate heat-trapping voids, while the ultra-low thermal conductivity of the aerogel ensures minimal heat transfer between cells. The structure prevents thermal propagation while maintaining integrity under thermal stress.
Space constraints and material deformation during battery cycling present additional challenges for insulation design. The multi-layer thermal insulation assembly features a compressible central layer sandwiched between two heat-resistant outer layers. The inner layer, with lower elastic modulus, deforms to absorb battery expansion, while the outer layers maintain thermal insulation and structural integrity. This configuration optimizes space utilization and ensures consistent insulation performance through elastic recovery, reducing thermal diffusion risk and supporting long-term reliability.
For internal cell components, the risk of short circuits between the pole group and cell casing requires specialized solutions. The co-jointed insulating gasket provides secure internal positioning and electrical isolation through a multilayer structure comprising an insulating phenolic resin core, a waterproof external layer, and a non-slip internal surface. These layers enhance moisture resistance, mechanical stability, and positional accuracy during assembly and operation. The integrated design simplifies manufacturing while reducing internal short circuit likelihood.
7. Insulating Films and Coatings Applied to Cell Surfaces or Housings
Direct application of insulating films and coatings to battery cell surfaces or housings provides a space-efficient approach to preventing short circuits and thermal events in EV battery systems.
The multilayer insulation system addresses extreme thermal conditions during events like thermal runaway through a first insulating layer made of high-temperature-resistant materials (polyimide, PTFE, or ceramics) directly adhered to the cell housing. A second insulating layer provides protection against moisture and mechanical damage. Adhesive layers between components ensure structural integrity and thermal reliability. This configuration enhances thermal stability at temperatures exceeding 400°C while preventing electrical arcing between adjacent cells, offering robust protection without significantly compromising energy density or manufacturability.
Metal-shelled battery cells present unique electrical conduction risks, particularly under high-pressure or liquid-cooled conditions. A comprehensive insulation coating applied to both inner and outer surfaces of the metal shell prevents direct contact between the electrode and shell. This approach is particularly important in high-voltage systems where the metal casing may become electrically charged. By electrically isolating the shell, the system mitigates risks of electrolyte decomposition, capacitive interference, and short circuits, enhancing reliability and safety in liquid-cooled battery packs.
For thermal management, the heat-insulating aluminum plate structure delays thermal runaway propagation across battery modules through a honeycomb layer filled with silica aerogel powder, enclosed by aluminum panels. The low thermal conductivity of silica aerogel combined with the honeycomb geometry impedes heat transfer between cells, providing critical evacuation time and minimizing the likelihood of full-module fires. The design supports manufacturing scalability with options like single-panel configurations that reduce material use and simplify production.
At the individual cell level, the thermal insulation layer applied to top and side surfaces of battery cores uses materials with thermal conductivity below 0.2 W/m·K to target the most vulnerable zones for heat and flame breakthrough. By impeding heat flow from cells undergoing thermal runaway, this insulation limits thermal propagation risk to adjacent cells without significantly impacting energy density or mechanical structure.
8. Terminal, Bus Bar, and Electrode Lead Insulation
Terminal and bus bar insulation represents a critical vulnerability point in battery pack design, particularly where electrode leads interface with structural components.
The risk of electrical bridging between bus bars and conductive casings in stacked battery cells has driven the development of specialized insulation solutions. Conventional designs often allow the bus component to bypass the casing wall, creating short circuit risks. The first insulator integration places an insulating piece between the bus bar and cell wall for electrical isolation. A concave structure in the casing near the electrode lead-out area houses and protects the tabs, ensuring mechanical stability. This approach enhances electrical insulation while improving welding reliability through precise tab design, supporting high-current configurations and enabling more compact packaging for increased energy density.
High-temperature environments create additional challenges for terminal and electrode lead insulation. Traditional polymer separators can deform or crimp under thermal stress, leading to electrode contact and short circuits. The dual-zone insulator design addresses this through a porous isolation area and a mechanically reinforced support area. The support region surrounds and partially overlaps the isolation zone, preventing crimping or curling during operation. This design maintains structural integrity under elevated temperatures, reduces ceramic layer fracture risk, and allows integration of ceramic-rich materials for superior thermal resistance, with compatibility across diverse battery platforms.
Condensation and vibration can compromise insulation at the terminal and bus bar level. The elevated side plate structure modifies the geometry of side and end plates, deviating their bottom surfaces upward from the battery core to increase clearance between structural components and cell insulation film. This minimizes moisture-induced short circuit likelihood and improves thermal management by enhancing contact with heat dissipation pads. Welded integration of structural elements ensures mechanical robustness, maintaining insulation integrity during long-term operation and under vibrational loads.
9. Separator Reinforcement to Prevent Curling and Cracking
Separator failure represents one of the most common causes of internal short circuits in lithium-ion batteries. Traditional separators made from polyethylene or polypropylene exhibit poor thermal stability, tending to curl or deform at elevated temperatures, particularly at the edges.
This curling can lead to contact between cathode and anode, creating short circuits and potential thermal runaway. While ceramic-coated separators improve thermal resistance, the underlying polymer substrate remains vulnerable to deformation. The electrical insulator with a dual-region structure addresses this through a separation region between electrodes and a supporting region that reinforces the edges. The support region absorbs thermal and mechanical stress, preventing separator curling or cracking at high temperatures.
Edge reinforcement represents another approach to enhancing separator durability. The periphery of ceramic-coated separators is particularly susceptible to cracking due to ceramic brittleness. The flexible support region surrounding the isolation area prevents curling under thermal stress while protecting the brittle ceramic core from mechanical damage. This region contacts both the separator sidewalls and active material layers, forming an integrated structure that enhances dimensional stability. A sealing frame bonded to the support region and current collector ensures robust encapsulation, simplifying assembly while maintaining safety standards.
For flexible battery formats, where mechanical deformation is more prevalent, the support area that partially overlaps the isolation area provides mechanical reinforcement to reduce crimping or curling during operation. This design enables higher ceramic content within the separator without sacrificing flexibility, achieving superior thermal performance. The support area bonds with the battery's packaging or plastic frame, enhancing structural integrity while streamlining manufacturing. This integration reduces separator edge cracking and active material leakage risks, significantly lowering internal short circuit probability.
10. Integrated Insulation in Battery Module or Pack Structures
Battery pack design has evolved toward higher density configurations, making consistent insulation between closely packed cells increasingly critical for preventing electrical short circuits and ensuring mechanical stability.
Traditional assembly methods using adhesive-backed insulation sheets face reliability challenges as these components can shift or peel during assembly or operation. The integrated insulation structure within the battery housing embeds insulation components directly into the battery pack's structural walls. This eliminates separate insulation pieces prone to displacement and instead uses structural protrusions extending between cells to maintain insulation. The cells are mechanically secured to the housing walls, enhancing positional stability and reducing insulation failure risk during vehicle operation.
Thermal management in battery packs requires insulation systems that provide thermal protection while maintaining mechanical integrity under dynamic conditions. Aerogel-based systems offer excellent thermal properties but must be securely integrated to function effectively. The aerogel felt integration with mechanical locking uses hanging rings and hooks to securely attach insulation to the battery pack's side plates. This ensures uniform contact between insulation and battery surfaces, eliminating performance-compromising air gaps. The result is a robust insulation layer that resists detachment under vibration while enhancing thermal insulation and shock absorption.
Accommodating mechanical stresses from cell expansion during charge-discharge cycles while maintaining thermal isolation presents another design challenge. The layered thermal insulation assembly features a compressible core between two heat-resistant layers. This configuration allows the central layer to deform under pressure without permanent damage, absorbing mechanical stress while maintaining insulation performance. The outer layers with higher heat resistance act as thermal barriers preventing heat propagation between cells, improving adaptability under varying operational conditions while enhancing resilience and service life.
For containing thermal events within battery modules, targeted insulating barriers between cells provide an effective strategy. The ceramic fiber-based insulating sheet placed directly between adjacent battery cells acts as a thermal blockade during thermal runaway events. The ceramic fiber layer provides high-temperature resistance and prevents thermal energy transfer to neighboring cells, reducing cascading thermal failure risks and enhancing intrinsic safety.
11. Insulation with Venting and Gas Management Capabilities
High-voltage battery systems must address gas management during thermal events alongside electrical and thermal insulation requirements. Traditional insulation approaches often obstruct gas venting, increasing pressure buildup and thermal propagation risks.
The insulator sheets with integrated spacer elements maintain a controlled gap between battery cells and the enclosure, creating dedicated vent paths for gases generated during cell failure. This design channels gases safely out of the pack rather than forcing them into adjacent cells. The vertical orientation of these insulator sheets creates aisles for gas flow, significantly reducing thermal runaway risk. Materials like mica, nickel, and steel provide electrical and thermal isolation while supporting high-temperature resilience and structural integrity.
Improving the interface between insulation materials and battery cells represents another key advancement, particularly for prismatic cell configurations. Conventional adhesive-based insulation films often suffer from alignment issues, wrinkles, and delamination. The insulating film pre-bonded to a colloid layer eliminates the separate adhesive layer, ensuring uniform coverage and reducing air pockets or misalignment. This approach improves bonding strength and structural cohesion, enhancing mechanical integrity and insulation performance. The integration of liquid cooling plates supports effective thermal management, contributing to system safety and longevity.
Internal cell insulation between the pole group and cell casing prevents short circuits and ensures safe operation. Traditional gaskets often lack multifunctionality and provide limited protection against internal failures. The conjoined insulating gasket integrates multiple functional layers: an insulating phenolic resin layer for electrical isolation, a waterproof outer layer to prevent moisture ingress, and a non-slip inner layer with surface protrusions for secure positioning. This multilayer structure enhances insulation while improving assembly stability and reducing component displacement risk during operation, significantly improving reliability and safety in high-capacity lithium-ion cells.
12. Insulation with Structural Reinforcement Against Vibration and Shock
Mechanical shock and vibration in EV battery systems threaten both insulation integrity and structural stability. Innovative approaches now integrate insulation and structural reinforcement functions to address these challenges.
The integrated insulation structure uses solidified materials like foam rubber between adjacent battery cells to mitigate internal displacement risks during mechanical impacts. This solution disperses impact forces away from battery cores while bonding with surrounding structural elements to enhance load distribution. The foam rubber, with a thixotropic index ≥ 5, resists flow during application and maintains structural integrity after solidification. This design simplifies manufacturing by preventing cell misalignment and providing consistent mechanical coupling between cells and their housing.
Advanced battery architectures like Cell-to-Pack (CTP) and Cell-to-Chassis (CTC) require reliable insulation placement during assembly. Traditional adhesive-based insulation components can shift or detach, compromising reliability and structural cohesion. The mechanically integrated insulation structure embeds insulation elements directly into the battery housing. This design features a pallet with side and bottom walls that provide physical separation and insulation between cells while eliminating adhesive requirements. By anchoring cells to the housing structure, the design enhances vibration resistance and ensures insulation remains properly positioned throughout operational life.
Within individual battery cells, internal short circuits between the pole group and casing due to mechanical displacement represent a critical concern. Traditional gaskets offer limited structural support and may fail under vibration. The multi-functional insulating gasket combines electrical insulation, moisture resistance, and mechanical fixation in a single component. The gasket's phenolic resin layer provides high-strength insulation, while its waterproof outer layer protects against environmental factors. The non-slip inner surface with micro-protrusions secures the pole group in place, ensuring internal components remain fixed during vibration or shock and reducing internal short circuit likelihood.
13. Insulation for Electrolyte Leak and Contamination Prevention
Electrolyte leakage and contamination create serious risks in compact battery packs where space constraints increase electrical bridging likelihood. Specialized insulation designs now address these specific challenges.
Specially shaped insulating papers between adjacent battery cells prevent short circuits from leaked electrolyte. These papers use configurations like a "glasses" shape for end-face coverage and a "straw-bag" form to wrap terminal sides, providing comprehensive terminal isolation. Independent positioning between cells prevents conduction paths even if electrolyte seeps through. The papers include slits allowing limited bypass current with high resistance, reducing excessive heat buildup risk. This electrolyte-isolating paper structure enables compact, lightweight battery pack designs without compromising safety, while eliminating individual cell casing requirements.
Multi-cell configurations using liquid or gel electrolytes face ion conduction risks between electrode groups. A novel solution places an insulating sheet between electrode groups, either partially or fully bonded to the battery's outer casing. This laminated architecture ensures physical and electrical separation, allowing high-conductivity gel electrolyte use without associated short-circuit risks. Routing part of the lead wire outside the casing facilitates individual voltage monitoring. This integrated insulation and casing design supports high-voltage scalability and maintains output performance, making it suitable for EV applications requiring compact, high-capacity energy storage.
In modular battery stacks with cells interconnected via conductive tabs, short circuits can arise from condensation, electrolyte leaks, or contaminant ingress. Traditional spatial separation proves insufficient under real-world environmental conditions. A cured adhesive insulating member applied directly over conductive interconnections conforms to stack geometry, encapsulating positive and negative terminal joints to create a robust physical barrier. The cured insulating adhesive layer enhances electrical insulation and mitigates environmental hazard effects, significantly improving EV power storage module reliability and safety.
14. Insulation for High-Voltage and High-Temperature Stability
High-voltage battery systems require insulation materials that maintain performance under extreme thermal conditions, particularly during thermal runaway events. Traditional insulation methods often degrade at elevated temperatures, creating electrical arcing risks between adjacent cells.
The multilayer insulation structure addresses this through a high-temperature-resistant inner layer directly bonded to the cell housing and a moisture-resistant outer layer. The inner layer uses materials like polyimide, PTFE, or mica with damage thresholds above 400°C, ensuring insulation integrity under severe thermal stress. This approach enhances arc resistance while improving mechanical stability and manufacturing yield through optimized outer layer thickness (approximately 30 μm).
Internal short circuits between the pole group and battery shell represent a critical concern in high-capacity lithium-ion batteries exceeding 50 Ah. Existing lower gasket designs often lack structural robustness and comprehensive insulation. The integrated insulating gasket combines multiple functional layers: a phenolic resin insulating layer for electrical isolation, a waterproof layer using materials like PVC and polyurethane for moisture resistance, and a non-slip layer with surface protrusions for mechanical stability. This design mitigates internal short circuit risks while improving long-term reliability under thermal and mechanical stress.
Thermal cycling and condensation within battery packs challenge high-voltage insulation maintenance. Traditional module designs allow water vapor to condense near vulnerable insulation film points, particularly at cell bottom edges, increasing electrical short risks. The redesigned battery module structure features elevated side and end plates that create physical separation between structural components and insulation film. This geometry prevents condensation-induced bridging while enhancing insulation reliability. The side plate design also improves thermal contact with heat dissipation pads, ensuring more uniform cell temperatures and increasing safety and performance.
15. Insulation for Simplified Manufacturing and Assembly
Battery manufacturing efficiency depends significantly on insulation application methods. Traditional approaches applying insulating layers individually to each electrode plate introduce complexity, labor intensity, and cost.
The zigzag-integrated insulation structure forms an insulating layer directly on the second electrode before assembly. This electrode, including a current collection tab, uses a zigzag shape that interleaves between adjacent positive electrode plates. The insulating layer extends integrally along the electrode, covering all critical surfaces except the tab. This innovation eliminates post-processing insulation steps, simplifying manufacturing while ensuring electrode edges are shielded, reducing internal short circuit risks and enhancing yield and production consistency.
Terminal joint insulation in stacked flat cell battery modules presents unique challenges. Conventional methods require high-precision placement of individual insulating components to prevent terminal contact during mechanical stress or vibration. The integrated insulating member between terminal joints inserts a single insulating component between multiple terminal joints rather than insulating each joint separately. This improves safety by minimizing short circuit risks from shifting components while reducing tight manufacturing tolerance requirements. The approach enhances long-term reliability through resistance to deformation and degradation while simplifying assembly for mass production.
Adhesives used to apply insulating films to battery cells can weaken over time, compromising structural integrity. The colloid-bonded insulating film technique pre-bonds the insulating film to a gel (colloid) layer before application to the cell surface. This eliminates separate adhesive layer requirements, reducing delamination risks and improving bond strength. The gel layer prevents manufacturing defects like air bubbles and wrinkles, streamlining the insulation process. This method supports better structural robustness and thermal management when integrated with liquid cooling plates, offering a scalable solution for EV battery packs and energy storage systems.
16. Insulation for Cell Stack Compression and Expansion Accommodation
Thermal expansion and contraction of lithium-ion battery cells create significant challenges for maintaining cell integrity and preventing short circuits. Traditional insulation materials like rigid aerogel films lack the mechanical adaptability needed to accommodate dimensional changes during charge-discharge cycles or temperature fluctuations.
The battery cell module design integrates dynamic mechanical compensation with high-performance thermal insulation. Pre-compressed elastomer components installed between cells in the displacement direction counteract thermal expansion and contraction movement. Each cell is wrapped in a heat insulation sheet comprising silica aerogel felt encapsulated by silicone fireproof or high-silica glass fiber cloth, stitched or bonded for durability. This approach prevents cell loosening, uneven force distribution, and compromised insulation performance that could increase internal short circuit and thermal runaway risks.
Similarly, the battery module design enhances thermal isolation and structural stability using insulation sheets between battery cells. These sheets contain silica or hybrid aerogel felt, encapsulated with coating layers and sealed using high-temperature-resistant materials like high-silica thread or mica glue. Pre-compressed elastomer parts dynamically accommodate cell volumetric changes, maintaining uniform mechanical pressure and consistent cell alignment. This design minimizes short circuit risks from cell-to-cell contact while providing robust thermal barriers against heat propagation during overheating events.
For internal cell insulation, the conjoined insulating gasket structure offers a multilayer solution preventing electrical contact between the pole group and cell casing. Traditional thin gaskets often provide insufficient dielectric strength and mechanical robustness under thermal or mechanical stress. The proposed gasket features a phenolic resin-based insulating layer, a waterproof outer layer using polymers like PVC or EPDM, and a non-slip inner layer with surface protrusions. This integrated structure enhances internal insulation, prevents moisture ingress, and maintains stable component positioning during assembly and operation, reducing internal short circuit likelihood and improving long-term reliability.
17. Thermal Runaway Suppression Sheets with Heat Diffusion and Absorption
Thermal runaway propagation represents one of the most serious safety concerns in lithium-ion battery modules. When a single cell enters thermal runaway, the heat generated can trigger neighboring cells, potentially causing catastrophic cascading failure.
Traditional thermal suppression materials often fail at high temperatures (~1000°C), suffer from poor structural integrity, and offer limited energy absorption. The thermal runaway suppression sheet addresses these limitations through a multilayered design combining heat absorption and diffusion mechanisms. A silica fiber layer undergoes dehydration condensation at elevated temperatures, actively consuming thermal energy. A complementary heat diffusion layer using expanded graphite or boron nitride laterally disperses localized heat, minimizing propagation risk. The sheet maintains a thickness below 3 mm, ensuring compatibility with compact battery module designs while providing high-temperature endurance and mechanical resilience through optimized fiber entanglement and wet papermaking techniques.
The thermal insulation cushion pad offers a layered solution for inter-cell protection within battery modules, addressing both thermal propagation and mechanical stress from cell expansion. The structure integrates ceramic fiber cotton for high-temperature insulation, silicone rubber for absorbing expansion forces, and glass fiber for additional thermal resistance. This combination effectively isolates thermal events to the originating cell while distributing mechanical loads to prevent deformation and damage to adjacent cells. Its performance under extreme thermal conditions while maintaining module compactness makes it practical for enhancing battery pack safety and longevity.
Both solutions prioritize scalability and manufacturability. The thermal runaway suppression sheet is compatible with standard papermaking and lamination processes, enabling high-volume production without performance compromise. The thermal insulation cushion pad integrates seamlessly into existing battery architectures, providing safety upgrades without sacrificing energy density or requiring significant redesign. These innovations represent significant advancements in using functional insulation materials to manage thermal hazards in EV battery systems.
18. Heat-Insulating Sheets with Expandable or Foam Structures
Heat-insulating sheets with expandable or foam structures offer multifunctional solutions for thermal management and safety in EV battery systems. These materials address the challenges of managing heat in tightly packed modules where conventional insulation either lacks mechanical strength or occupies excessive space.
Traditional glass fiber sheets, while nonflammable, exhibit poor performance under mechanical stress due to low tensile and compressive strength, limiting their effectiveness in preventing thermal propagation. The high-strength heat insulating sheet made from reinforced glass fiber enhances fiber entanglement and structural integrity, maintaining a compressibility rate below 40% under 5 MPa pressure. This balance between compressibility and mechanical durability enables effective performance in compact spaces without compromising fire resistance. The sheet resists deformation from battery swelling or external loads while acting as a thermal barrier, significantly reducing thermal runaway propagation risk.
Foam-based insulation with active cooling capabilities offers another innovative approach. Conventional systems using high-density polyethylene (HDPE) tend to be heavy, non-porous, and ineffective at dissipating heat during thermal events. The low-density ceramic fiber reinforced foam block houses battery cells in individual recesses, with high porosity (up to 98% air content) allowing gas or liquid circulation for efficient thermal regulation. This design mitigates thermal runaway cascade effects while reducing insulation system weight. A ceramic matrix composite coating enhances structural rigidity and thermal resistance, creating a modular, scalable, and lightweight alternative to conventional materials that simultaneously provides insulation, mechanical support, and active cooling.
19. Thermal Insulation with Anisotropic or Directional Heat Transfer
Thermal management in high-energy-density battery packs requires sophisticated approaches to heat flow control. Anisotropic thermal insulation materials offer directional heat transfer capabilities that can significantly enhance battery safety and performance.
The laminated thermal insulator composed of an inner compressible layer between two anisotropic outer layers represents a significant advancement in this domain. The anisotropic layers exhibit higher in-plane thermal conductivity compared to through-plane conductivity, effectively channeling heat laterally toward designated heat sinks while restricting vertical heat transfer between cells. The compressible inner core, using low-conductivity materials like aerogel, provides thermal insulation while absorbing mechanical stress from cell expansion during charge-discharge cycles. This directional heat transfer mechanism enhances thermal isolation and safety without requiring costly graphene-based composites, offering a lightweight, scalable, and cost-effective solution for integration between prismatic or pouch cells.
The multi-layered aerogel flame-retardant sheet for new energy vehicle battery packs takes a different approach to directional heat management. This configuration includes two aerogel-based insulation layers with interleaved heat conduction layers made from copper foil and/or graphene composites. The insulation layers provide lateral thermal isolation between cells, while the conduction layers bend downward to direct heat away from the battery module's core without allowing cross-cell propagation. This controlled vertical heat dissipation design meets national flame-retardancy standards while enhancing mechanical buffering and structural flexibility. The design replaces traditional plastic separators and felt-based insulation with a lightweight, thermally efficient alternative that balances fire resistance and heat management.
Ultra-thin nano-insulation plates designed for extreme thermal events exceeding 900°C address critical requirements for thermal runaway containment. These plates are fabricated by compressing fumed silica powder between outer packaging materials, optionally integrating high-temperature-resistant mesh cloth for mechanical stability. Vacuum-sealing and edge treatment enhance durability, waterproofing, and vibration resistance. The high-temperature nano-insulation plate offers exceptionally low thermal conductivity that outperforms conventional fiber-based insulators and silicone aerogels while maintaining a slim form factor ideal for space-constrained battery modules. This ensures thermal containment even under catastrophic failure conditions, aligning with stringent safety regulations and improving occupant safety.
20. Miscellaneous Unique Insulation Concepts
Beyond conventional approaches, several unique insulation concepts offer novel solutions to specific challenges in EV battery design.
The insulating member with through-holes positioned between battery cells and conductive outer housing addresses dual challenges: preventing short circuits from mechanical contact while enabling uniform electrolyte distribution. In conventional designs, shocks or vibrations can cause cells to contact the housing, creating short circuit risks. Additionally, uneven electrolyte penetration can degrade battery performance. This innovation integrates an insulating member with pore sizes between 100 and 2000 microns, allowing uniform electrolyte distribution while preventing direct electrical contact. The design enhances both safety and electrochemical performance while supporting integration across various electrical devices.
Traditional thermal barriers like mica suffer from high density, low flexibility, and poor thermal conductivity, making them unsuitable for modern battery packs where space and weight are critical. The lightweight, fire-resistant porous insulation layer features a fiber-based porous structure embedded with hollow particles like silica aerogel powder, encased between sealing layers. This configuration achieves low thermal conductivity, high compression resilience, and excellent fire resistance without excessive bulk. The insulation maintains its properties even after carbonization at 600°C, offering robust protection against thermal runaway propagation while enhancing mechanical durability and safety.
The composite thermal insulator addresses limitations of fiberglass-based insulators that inadequately prevent flame spread and provide insufficient electrical insulation. This design incorporates layers of scrim-reinforced PEEK or silicone rubber, silica fabric, and pressure-sensitive adhesives, forming a thin, conformable barrier easily installed around or between battery cells. Withstanding temperatures up to 1000°C for 10 minutes while maintaining 2 kV dielectric strength, this composite wall structure provides dual thermal and electrical protection, significantly improving safety during critical fault scenarios.
Advanced aerogel-based heat control members isolate battery cells thermally and prevent runaway propagation without weight or thickness penalties. Conventional foam or fiber insulators require increased volume for comparable thermal resistance, making them incompatible with compact battery modules. These aerogel composites, reinforced with glass or polymeric fibers and open-cell macroporous foams, offer ultra-low thermal conductivity and high porosity while remaining thin and flexible. Additives like kaolin and aluminum trihydrate enhance fire resistance, and hydrophobic treatments ensure long-term performance in humid environments. These materials provide mechanical resilience and environmental stability while supporting scalable manufacturing processes for next-generation battery architectures.
Get Full Report
Access our comprehensive collection of 76 documents related to this technology
Identify Key Areas of Innovation in 2025
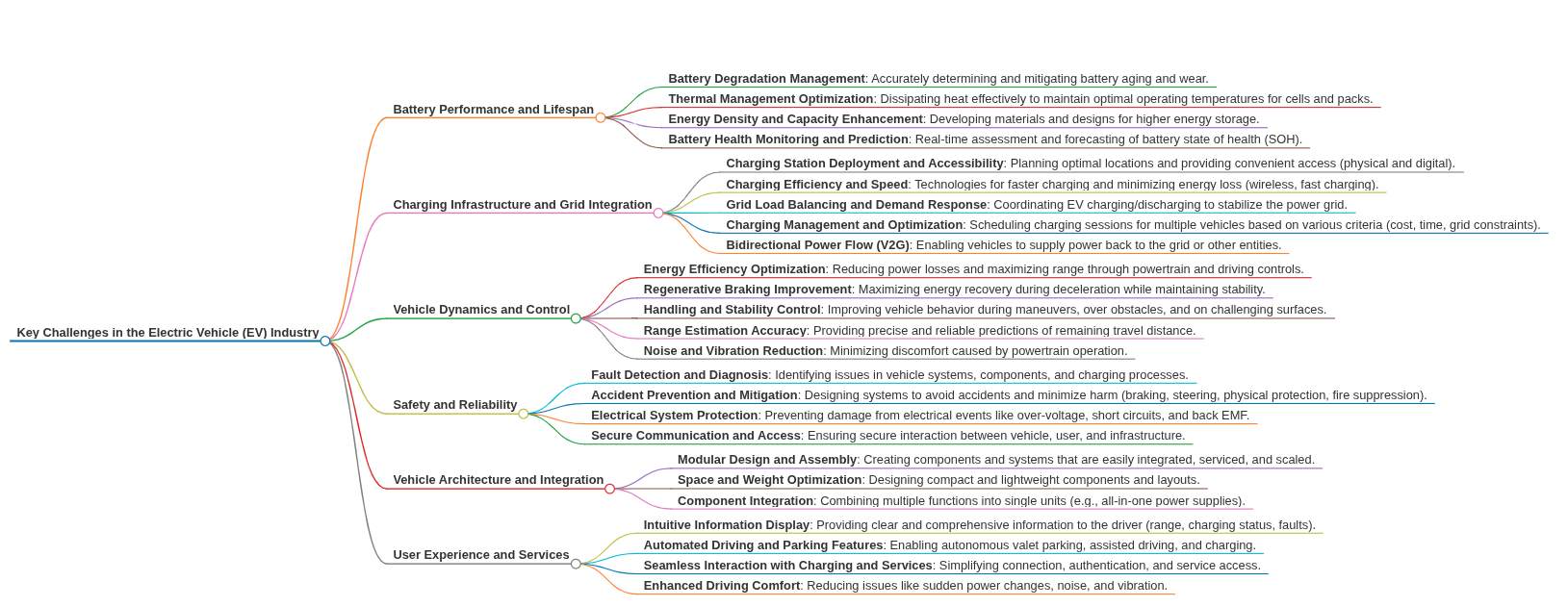