Mixing and Coating Techniques for EV Battery Electrode Materials
Manufacturing lithium-ion battery electrodes requires precise control over material distributions and interfaces across multiple length scales. Current mixing processes must handle active materials ranging from nanometers to microns, while coating techniques need to achieve uniform layers between 50-200 μm thick with porosity variations under 5% to ensure consistent battery performance.
The fundamental challenge lies in achieving uniform particle dispersion and controlled interface formation while maintaining high-speed, scalable production processes that can handle increasingly complex electrode formulations.
This page brings together solutions from recent research—including stabilized suspension systems for electrophoretic deposition, multi-step mixing protocols for silicon-based anodes, sequential coating approaches for composite current collectors, and low-viscosity compositions for precision dispensing. These and other approaches focus on improving electrode uniformity and performance while maintaining manufacturability at industrial scales.
1. Electrode Material with Core-Shell Structure Formed by Spray Drying
RUIPU LANJUN ENERGY CO LTD, 2024
Electrode material for batteries with improved cycle life and reduced expansion/contraction during charging/discharging. The electrode material has a core-shell structure made by spray drying. The core contains functional components, binder, and conductive agent. A shell layer with different binder and conductive content is sprayed onto the core. This provides a lower inner core conductivity and binder content compared to the shell. This prevents excessive expansion/contraction during cycling, preventing collapse and improving cycle life.
2. Manufacturing Method for Electrode Granules with Solid Electrolyte Coating via Mechanofusion
LG ENERGY SOLUTION, LTD., 2024
A method to manufacture electrodes for all-solid-state batteries that improves performance and enables using solid electrolytes. The method involves making larger primary electrode granules with a binder, then mixing them with solid electrolyte and compressing to form smaller secondary granules. These secondary granules have a solid electrolyte coating that densely adheres to the electrode material. This provides better solid-state electrolyte coverage on the electrode compared to using the solid electrolyte directly. The larger primary granules allow better mixing and compression during mechanofusion to coat the secondary granules.
3. Liquid Compositions Set for Electrode Layer Formation with Distinct Electrode Material Solvents
RICOH COMPANY LTD, 2024
A set of liquid compositions for forming electrode layers in lithium-ion batteries that improves flexibility and ease of design compared to using a single liquid composition. The set includes two compositions, one with a first electrode material dissolved in a first liquid, and the other with a second electrode material dissolved in a different second liquid. This allows optimizing solubility/dispersibility of each electrode component in its respective liquid. Applying the set sequentially or simultaneously onto the electrode substrate enables forming electrode layers with better adhesion, peel strength, and capacity compared to using a single composition.
4. Electrode Manufacturing Method with Perpendicular Electric Field Application for Controlled Binder Distribution
IUCF HYU, IUCF-HYU, SAMSUNG SDI CO LTD, 2024
Manufacturing method for electrodes in rechargeable lithium batteries that improves adhesion, cycle life, and high-rate charging performance. The method involves applying an electric field during drying to control binder migration and distribution. This prevents binder buildup on the electrode surface that can hinder ion transfer and degrade electrochemical properties. The electric field is applied in a direction perpendicular to the drying direction to counteract capillary forces and prevent binder migration.
5. Electrode Manufacturing Method with Heating and Defoaming Stirring Steps
NATIONAL INSTITUTE OF ADVANCED INDUSTRIAL SCIENCE AND TECH, NATIONAL INSTITUTE OF ADVANCED INDUSTRIAL SCIENCE AND TECHNOLOGY, SANOH IND CO LTD, 2024
Method for manufacturing electrodes for batteries that reduces electrode peeling during drying and improves yield. The method involves a kneading step using a heating stirring process at 150-200°C followed by a defoaming stirring process. The heating stirring removes moisture from the raw materials to prevent peeling during drying.
6. Method for Fabricating Solvent-Free Dry Electrodes with Direct Coating and Glue Layer Integration
SVOLT ENERGY TECH CO LTD, SVOLT ENERGY TECHNOLOGY COMPANY LTD, 2024
Method for making dry electrodes for batteries that improves conductivity, avoids solvent side reactions, and enhances performance compared to wet electrodes. The dry electrode manufacturing process involves coating the active material, conductive agent, and binder mixture directly onto the current collector without using a solvent. The coated mixture is preliminarily hot-pressed, then a glue layer is plated on the surface. Baking and drying removes moisture from the glue. This eliminates the need for a solvent surrounding the particles, improving contact and conductivity. It also prevents solvent reactions with the electrolyte.
7. Electrode with Attachment Enhancing Layer for Improved Film-Collector Adhesion in Electrochemical Devices
LG Chem, Ltd., 2023
Electrode for an electrochemical device with improved adhesion strength between a free-standing dry electrode film and a current collector. The method involves forming an attachment enhancing layer on the current collector by coating a slurry of binder and conductive material, then stacking the dry electrode film on it and applying heat/pressure to permeate the binder into the electrode film surface. This enhances adhesion compared to direct film-current collector contact. The attachment layer prevents film delamination during cell assembly/operation.
8. Electrode with End Auxiliary Coating for Lithium Secondary Batteries and Simultaneous Application Method
LG ENERGY SOLUTION LTD, 2023
Electrode design and manufacturing method for lithium secondary batteries that prevents capacity imbalance and improves safety by preventing sliding at the electrode ends. The electrode has a single layer with an electrode mixture containing active material and an auxiliary coating at the end. The auxiliary coating layer improves adhesion, prevents thickness variation, and acts as a dam to prevent sliding at the end. This prevents capacity ratio inversion and lithium plating issues. The auxiliary coating is prepared by simultaneously applying an electrode slurry and auxiliary coating composition onto the current collector.
9. Active Material Particles with Embedded Conductive Filler for Dry Electrode Formation
GM GLOBAL TECH OPERATIONS LLC, GM GLOBAL TECHNOLOGY OPERATIONS LLC, 2023
Active material for dry electrode formation in lithium-ion batteries that has conductive filler particles already embedded in the active material particles. This improves electrode performance by providing better electrical conductivity compared to adding external conductive additives during electrode formation. The active material powder is mixed with conductive filler and then dried to form particles with conductive filler already attached. This pre-embedded active material is then used to coat the electrode current collector in the dry electrode formation process.
10. Method for Manufacturing Battery Electrodes Using High-Speed Slurry Coating Above Yield Point
Nissan Motor Co., Ltd., NISSAN MOTOR CO LTD, 2023
Method for manufacturing battery electrodes with improved flatness and reduced thickness variation of the active material layer. The key is coating the electrode slurry at a speed that exceeds the yield point of the slurry. The slurry has specific flow properties with a region where shear stress is constant and a region where shear stress increases with speed but at decreasing rate. Coating at speeds exceeding the yield point prevents sagging and improves layer uniformity.
11. Negative Electrode with Styrene Butadiene Rubber Primer Layer for Silicon-Based Lithium-Ion Batteries
SK ON CO LTD, 2023
Negative electrode, manufacturing method, and secondary battery with improved lifespan and capacity retention for silicon-based negative electrodes in lithium-ion batteries. The method involves applying a thin layer of styrene butadiene rubber onto the current collector before adding the silicon active material and binder. This primer layer reduces expansion and contraction of the silicon during charging/discharging and improves flexibility compared to using the binder alone.
12. Method for Producing Lithium Ion Battery Electrodes with Dual-Stage Pressing at Elevated Temperatures
ZEON CORP, 2023
A method for producing lithium ion battery electrodes that suppress cracking of the electrode active material during formation of the electrode and improve battery storage characteristics. The method involves pressing composite particles containing electrode active material and binder onto a substrate to form a compressed layer. This is followed by further pressing the compressed layer to form the electrode mixture layer. The key is to set the pressing temperature during both steps to be equal to or higher than the softening point of the water-soluble polymer in the binder. This prevents active material distortion and cracking. By dividing the pressing into two stages, the density can be increased without excessive stress. Using a binder with a softening point below the pressing temp also helps.
13. Manufacturing Method for Lithium Battery Electrodes Using Porous Substrate Dehydration and Binder Coating
SEOUL NATIONAL UNIV R&DB FOUNDATION, SEOUL NATIONAL UNIVERSITY R&DB FOUNDATION, 2023
Method for manufacturing high-performance lithium secondary battery electrodes with improved adhesion and productivity. The method involves using a dehydration process with a porous substrate to remove a significant amount of solvent from the electrode slurry before applying it to the current collector. This allows faster drying rates compared to traditional methods. Additionally, a coating solution containing a binder is applied to the current collector prior to laminating the electrode layer. This improves adhesion between the active material and current collector. The dehydrated electrode layer is then pressed onto the binder-coated current collector to physically bind them. After separating the porous substrate, the electrode is further dried.
14. Preparation Method for Mixed Positive Electrode with High Voltage and Low Voltage Active Particles for Lithium Ion Batteries
SHENZHEN PINPU TECH CO LTD, SHENZHEN PINPU TECHNOLOGY CO LTD, 2023
Preparation method of lithium ion battery with high cycle performance by using a mixed positive electrode. The method involves mixing high voltage positive electrode active particles like nickel-cobalt-manganese ternary cathode material with conductive carbon black, spreading it on a battery current collector, and forming an electrode plate using binder spraying. This provides high specific capacity from the high voltage material. A coating of low voltage positive electrode active particles like lithium iron phosphate is then applied using spray drying or coating techniques on the electrode. This improves cycle life and safety by reducing voltage stress. The mixed positive electrode with optimized composition and structure from the preparation method enhances the energy density, cycling stability, and safety of the lithium ion battery.
15. Method for Forming Thick Lithium-Ion Battery Electrodes with Enhanced Ion and Electron Transport Through High-Temperature Slurry Compounding
SVOLT ENERGY TECH CO LTD, SVOLT ENERGY TECHNOLOGY COMPANY LTD, 2023
Preparation method for thick lithium-ion battery electrodes that allows high energy density without capacity degradation. The method involves mixing the electrode active material, conductive agent, binder, salt, and solvent to form a slurry. Then heating the slurry to 110-180°C to compound it with the current collector. This allows thick electrodes with high active material content and reduced tortuosity for improved ion and electron transport compared to conventional methods. The slurry is coated onto the current collector or pressed onto it.
16. Suspension Stabilization for Electrophoretic Deposition Using Specific Deflocculating Agents
3DBATTERIES LTD, 2023
Stabilizing slurry and electrophoretic deposition (EPD) bath suspensions for energy storage electrodes and separators to prevent particle agglomeration and settlement. The stabilization involves using specific deflocculating agents that reduce aggregation of nanoparticles and microparticles. These agents are selected from materials like phosphates and electron rich compounds with small effective radius. They are added to the carrier liquid before introducing the solid particles to create stable suspensions for electrode preparation and EPD deposition. The stabilized suspensions enable uniform electrode deposition with controlled particle size distribution.
17. Method for Manufacturing Electrodes Using Dual Binder System with Fibrillated Binder for Uniform Thin Film Formation
HYUNDAI MOTOR CO, KIA MOTORS CORP, 2023
A method to manufacture electrodes for all-solid-state batteries with high active material loading and uniform thin film thickness. The method involves using two binders: a first binder dispersed in a solvent to form an adhesive solution, and a second binder added later. The active material and solid electrolyte are mixed into a first slurry, then a second slurry is made by adding more binder solution. The second slurry is kneaded to fibrillate the second binder into a clay-like state. This fibrillated second binder provides mechanical properties to the electrode. Rolling the clay-like material forms the electrode. The fibrillated second binder allows uniform distribution and packing of the active material.
18. Secondary Battery Electrode with Nanoscale Metal Particle Coating for Sintered Bonding
KIM YONG SANG, 2023
A secondary battery electrode coated with nanoscale metal particles instead of a separate conductive material or binder. The electrode active material is coated with nanoscale metal particles like tin, silver, copper, antimony, lead, or solder alloys. The metal particles bond the active material together during sintering. This eliminates the need for a separate conductive material or binder for electrical contact and adhesion. The metal coating allows dense packing of the active material without volume expansion during charging/discharging. It also improves electrical conductivity compared to using a binder. The coated electrode can be made by immersing the active material in a dispersion of metal particles, drying, and pressing.
19. Two-Step Preparation Method for Negative Electrode Slurry with Segmented Component Integration
SK ON CO LTD, 2023
Method for preparing a negative electrode slurry for lithium-ion batteries with improved conductivity and reduced volume expansion during charging/discharging for silicon-based anodes. The slurry is prepared in two steps: (1) mixing a silicon-based negative electrode active material, conductive agent, and binder to form a first slurry; (2) adding carbon-based negative electrode active material and thickener to the first slurry and mixing. This allows a higher concentration of conductive agent around the silicon particles to improve conductivity. The thickener also helps prevent separation between the silicon and carbon particles during volume expansion.
20. Surface Treatment System for Ternary Positive Electrode Materials with Sequential Sintering, Coating, and Smashing Steps
FOSHAN TIANJIN NEW ENERGY TECH CO LTD, FOSHAN TIANJIN NEW ENERGY TECHNOLOGY CO LTD, 2023
A surface treatment system and device for ternary positive electrode materials in lithium-ion batteries that improves coating uniformity and efficiency. The system involves separate steps of primary sintering, coating, secondary sintering, and smashing to treat the electrode material. This allows better mixing of the electrode and coating materials compared to conventional methods. The primary sintering step is done first to densify the electrode material. Then coating is applied. After coating, secondary sintering is done to further densify the electrode material and bond the coating. Finally, smashing is done to break up any agglomerates formed during sintering. This sequential treatment sequence helps ensure homogeneous mixing and dispersion of the coating material with the electrode material.
Get Full Report
Access our comprehensive collection of 135 documents related to this technology
Identify Key Areas of Innovation in 2025
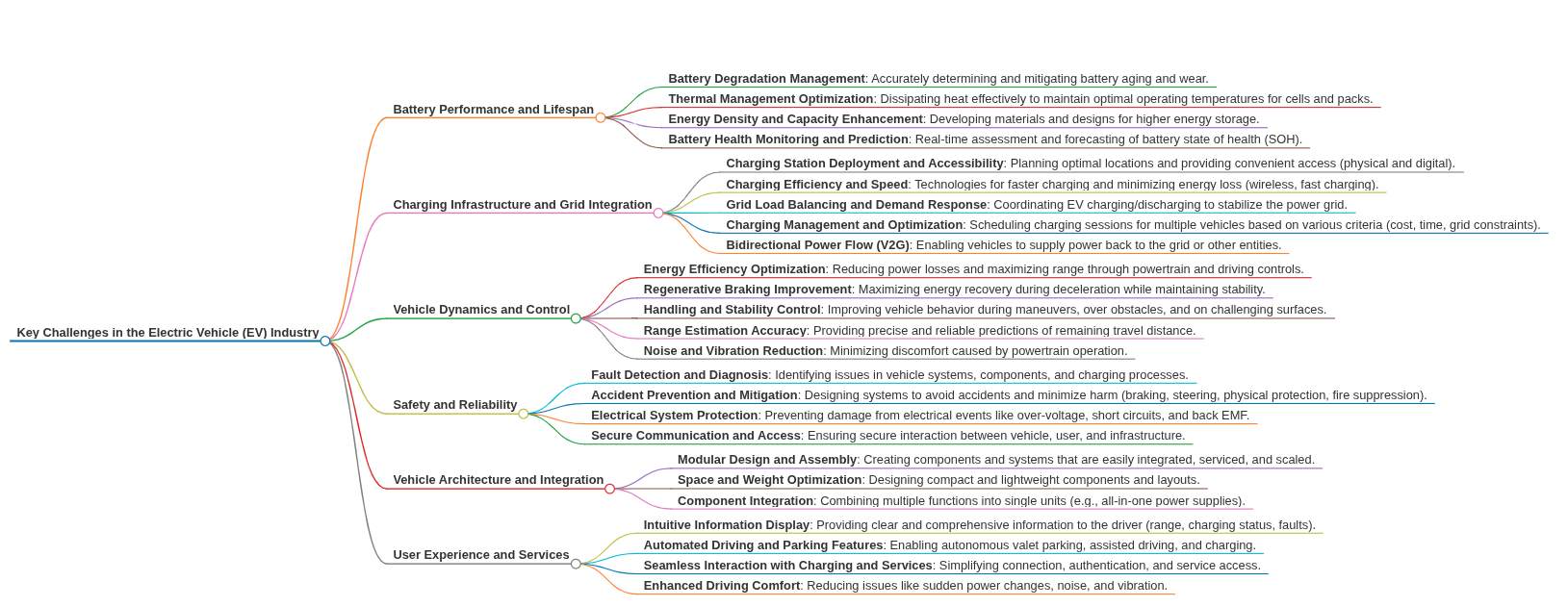