EV Battery Mass Reduction Through Materials and Design
Current EV battery packs contribute 20-25% of total vehicle mass, with energy densities typically ranging from 150-200 Wh/kg at the pack level. This weight impacts vehicle range, handling, and overall efficiency, while creating additional structural requirements for the vehicle chassis and suspension systems.
The fundamental challenge lies in reducing pack mass while maintaining structural integrity, thermal management capability, and protection against mechanical and thermal events.
This page brings together solutions from recent research—including integrated cooling and exhaust duct designs, lightweight composite enclosure materials, cell-to-pack architectures that eliminate module housings, and optimized compression methods for cell stacks. These and other approaches demonstrate practical ways to improve gravimetric energy density without compromising safety or performance.
TABLE OF CONTENTS
1. Thin Foil Pouching, Hybrid Leads, and Low-Profile Busbars
Mass reduction begins at cell level. A standard 60 Ah pouch wrapped in a multilayer polymer-aluminium laminate dedicates almost 7 % of its weight to sealing and current-lead material. The stack-bonded metal-foil cell architecture attacks this overhead by making the containment skin double as the current collector. Two ultra-thin metal foils are laser-welded edge-to-edge with a sub-millimetre seam, replacing the 3-5 mm heat-sealed flange. Tear-down of a 20-cell stack shows a 12 mm height reduction and a 450 g drop in inactive mass while helium-leak testing reports rates below 1 × 10⁻⁹ mbar L s⁻¹. Because the foils also spread pressure, lighter mechanical restraints are possible further up the hierarchy.
Every copper tab that protrudes from a cell adds grams and galvanic risk. The friction-welded copper–aluminum hybrid lead keeps a short copper stub inside the high-current region, then joins it to a long aluminium ribbon through high-speed rotary friction welding. Metallography reveals a 10 µm diffusion interface free of brittle intermetallics, and salt-spray endurance exceeds 1000 h. Tab copper usage falls by 60 %, trimming roughly 1.4 kg from a 96s2p SUV pack and enabling direct aluminium-to-busbar welding without transition plates.
Envelope height can be tightened further at the interconnect. In the low-profile busbar with an integrated thermistor groove a 2 mm-deep channel milled along the neutral axis houses both the NTC sensor and its ribbon cable. The busbar now sits below the gas-vent plane, which removes a dedicated ABS pocket, shortens the copper trace, and cuts response time to thermal excursions by 25 %. Combined, foil pouching, bi-metal leads and slim busbars strip about 2.5 kg from a 75 kWh pack while setting up the architectural freedom required for the module-less concepts introduced in Section 3.
2. Fiber-Reinforced Thermoplastic and Polymer-Based Battery Casings
Pressed-steel trays with welded ribs can add 60-70 kg to a mid-size EV. Replacing them with continuous-fibre thermoplastic laminates yields rapid cycle times and steep mass savings. The fully thermoplastic composite battery enclosure uses a 1.5 mm carbon-fibre organosheet and over-moulded glass-fibre ribs. A 1200 mm × 1600 mm floor pan weighs 19.4 kg and still meets Euro-NCAP side-pole stiffness targets. Tool recesses shape inlet bosses, M6 captive nuts and honeycomb crush initiators in a single press stroke, eliminating forty steel brackets and a three-metre laser seam for a further 4 kg saving. Post-impact panels can be reheated and reshaped, and ISO 14044 lifecycle analysis records a 32 % GHG benefit compared with aluminium at equal stiffness.
At module scale, aluminium housings remain common because they double as heat spreaders. The thermally-conductive plastic module housing answers with a graphite-loaded PPS compound that reaches 60 W m⁻¹ K⁻¹ through-plane conductivity. A thirty-cell 2170 module weighs 1.3 kg less than its cast AlSi10Mg counterpart yet passes 3 kV dielectric withstand without extra Kapton liners. Specific energy climbs from 177 to 190 Wh kg⁻¹ and the melt-processable compound aligns with the floor-pan over-moulding process, enabling a one-material supply chain. The stiff yet resilient composite shell also tolerates the larger unsupported cell areas inherent in the module-free architectures discussed next.
3. Cell-to-Pack and Monolithic Pack Architectures Eliminating Module Enclosures
Intermediate housings consume roughly 40 % of conventional pack volume. The prismatic-style terminal exposure for pouch cells folds electrode tabs upward, then stitches a continuous stainless frame across an entire row with an 80 cm laser sweep. When this frame bolts to the upper cover it applies a uniform 35 kPa pressure field that halts pouch swelling. Eliminating twelve aluminium module boxes, four silicone pads and 104 fasteners sheds 6.7 kg and frees 11 L of void space.
The monolithic structural battery pack pushes further by potting the cell array inside a load-bearing epoxy frame that incorporates aluminium shear webs. Four-point chassis tests on a 1100 mm span show 25 kN load with only 1.2 mm deflection, enabling removal of a traditional under-floor cross-member and delivering a 9 kg weight cut. Planar copper foils laminated inside the shear webs replace discrete busbars, further cleaning the bill of materials. OEM data shows a 14 % pack-level gravimetric gain and an 8 % material-cost reduction once module housings vanish.
Cell-to-pack solutions require precise, lasting compression; Section 4 explores lightweight methods that deliver that preload without resorting to heavy aluminium bolt plates.
4. Compression, Vacuum, and Insert Techniques for Cell Stack Restraint
Pouch and prismatic stacks need 30-120 kPa compression to maintain electrode contact. The vacuum-assisted cell block bracing encloses the entire stack in a polycarbonate shell, pulls internal pressure down to 200 mbar, and generates an 80 kN clamp on a 600 mm × 700 mm surface. Modal analysis places the first torsional mode at 290 Hz, and four-poster testing shows no rise in cell-to-tab impedance after 300 h. The system saves 9.1 kg compared with a bolted steel frame.
Irregular floor pans create dead space when rectangular modules are used. The polymer block insert for irregular trays fills these voids with low-density, carbon-reinforced polyetherimide foam bonded by elastic urethane. Cells are compressed on an external jig and slid into the tray; inserts wedge between curved walls and the stack, keeping preload uniform while deleting metal end plates. Four litres are freed on the perimeter, room enough for a vapour-cooled electronics corridor.
Vacuum shells auto-compensate for cell swell because internal volume contracts as pressure remains low. Foam inserts rely on the stable compressive modulus of their carbon skeleton up to 120 °C. Combining vacuum bracing with cell-to-pack architecture raises pack-level energy density by a further 8 % over legacy end-plate designs.
5. Embedded Cooling, Heating, and Gas Venting Channels within Pack Housing
Thermal management can exceed 15 kg in a 75 kWh battery. The collapsed-expandable gas exhaust conduit hides a flattened silicone tube inside the main cooling plenum. Under normal airflow the tube lies dormant; if a cell vents the resulting 50-60 kPa pressure inflates it, sealing the coolant path and diverting gases to an exterior sill port. No dedicated vent pipe is needed, saving 1.2 kg and avoiding hot-gas impingement on cold module walls.
For routine heat rejection, the stacked thermally conductive cartridges wrap micro-groups of cells in graphite-loaded polymer sleeves. A sintered aluminium wick interfaces with the outer case via an indium pad. The path is 40 % shorter than a conventional cold plate and core temperatures run 3.5 °C lower at 4C discharge, yet total thermal content falls by 3.3 kg.
Liquid passages can be printed directly into the shell. The integrally molded cooling plate enclosure uses Multi-Jet Fusion to embed a lattice of 2.5 mm square conduits within a 4 mm PA12 skin, then electroplates the interior with 20 µm copper. The design survives 3.5 MPa burst tests, removes bolt-on plates and 19 screws, and cuts another 1.8 kg. Integrating coolant, venting and structural load paths in a single wall dovetails with the die-cast structures examined next.
6. Hollow, Die-Cast, and Sandwich Metal Pack Structures with Integrated Reinforcement
Side-impact loads normally pass into separate rocker beams. The one-piece die-cast case with integral cross members forms a 75 mm hollow rib across the full 1500 mm width, merging with the sill at two cast ears. It handles 45 kN lateral crush and drops 11 kg relative to a steel twin-sill beam. Post-impact finite element studies show 28 % of energy absorbed by the battery floor and 42 % by the cast rib, so bolt-on beams vanish along with 48 fixings.
Axial compression walls can also lighten. The metal–resin sandwich compression wall bonds two 0.8 mm 6000-series skins across a 5 mm foamed epoxy core. Bending stiffness reaches 70 % of a 6 mm solid aluminium plate at 40 % of the mass. Corner pockets fill with resin during moulding, fusing panels into a continuous load loop; long-term creep stays below 0.2 mm at 80 °C for 1000 h.
Adding diagonal CFRP tubes as in the triangular frame with diagonal supports closes load triangles between the side sill, die-cast cross member and floor. Tubes only 18 mm in diameter exceed 10 kN buckling load and also carry refrigerant micro-channels. First vertical bending mode rises by 34 %, improving ride quality. Casting, sandwich bonding and CFRP bracing all employ non-fusion joining, so galvanic risk is managed with a 10 µm plasma-electrolytic oxide while self-piercing rivets create the mechanical link. With core structures integrated, attention can shift to auxiliary hardware and fasteners.
7. Consolidated Component Mounting and Reduced-Fastener Pack Assemblies
The embedded high-current connector and switch module locates contactor, fuse and Hall sensor inside a recess in the die-cast bulkhead. High-voltage path length falls from 320 mm to 45 mm, eliminating a 0.6 kg copper busbar and two crimp joints. Sensor grounding becomes cleaner because the shell itself provides the reference.
Fastener count drops further with the dual-purpose cooling/support member. Tongue-and-groove edges on neighbouring cold plates align captured holes so a single M8 bolt locks three plates and the floor pan. Forty bolts and twenty brackets disappear, 0.9 kg of steel is saved, and torque cycles are halved. A nylon-66 sleeve insulates the bolt from the coolant gallery.
Low-power electronics benefit from skeletal mounts. The lightweight rod-based BMS bracket suspends the control board on two 10 mm carbon-pultruded rods without a solid deck. Air flows beneath the PCB, component temperatures drop by 8 °C during fast charge, and the bracket mass falls from 540 g to 110 g. Because brackets locate on bosses that already exist in the composite floor, no extra height penalty arises.
Switchgear integration, captive fasteners and skeletal brackets trim close to 4 kg from a large pack and simplify end-of-life disassembly, paving the way for system-level electrical optimisation.
8. Split Battery Packs and Converter-Free Electrical Architectures
Raising pack voltage cuts I²R loss but forces heavier insulation and pricier SiC devices. The mid-point grounded split pack divides a 600 V battery into two 300 V cartridges tied to chassis ground. Harness can shift from 35 mm² copper to 16 mm² aluminium, saving 1.8 kg and freeing tunnel space. Active balancing keeps state-of-charge divergence within 2 % over 1000 cycles.
Auxiliary loads no longer need a separate 12 V battery. The dual-subassembly pack with a staged interrupter powers low-voltage consumers from one half-pack via a resistor-limited pre-charge path. A lead-acid battery and its DC-DC converter, together weighing 15 kg, disappear. Quiescent current also falls because the DC-DC is idle.
Fuel-cell hybrids carry two DC-DC converters. The converter-free fuel-cell coupling removes the stack-side converter by aligning fuel-cell OCV with the low end of the battery discharge curve. The inverter briefly trims the bus voltage to match the stack before a switch closes. Silicon carbide switches, inductors and cooling plates totalling 5.2 kg vanish, while WLTP efficiency suffers only a 0.4 % penalty.
Integrating cell-level, structural, thermal, fastening and electrical levers allows a medium crossover to shed 75-90 kg compared with a 2020 baseline battery, boosting range by 7-10 % without changing cell chemistry.
Get Full Report
Access our comprehensive collection of 25 documents related to this technology
Identify Key Areas of Innovation in 2025
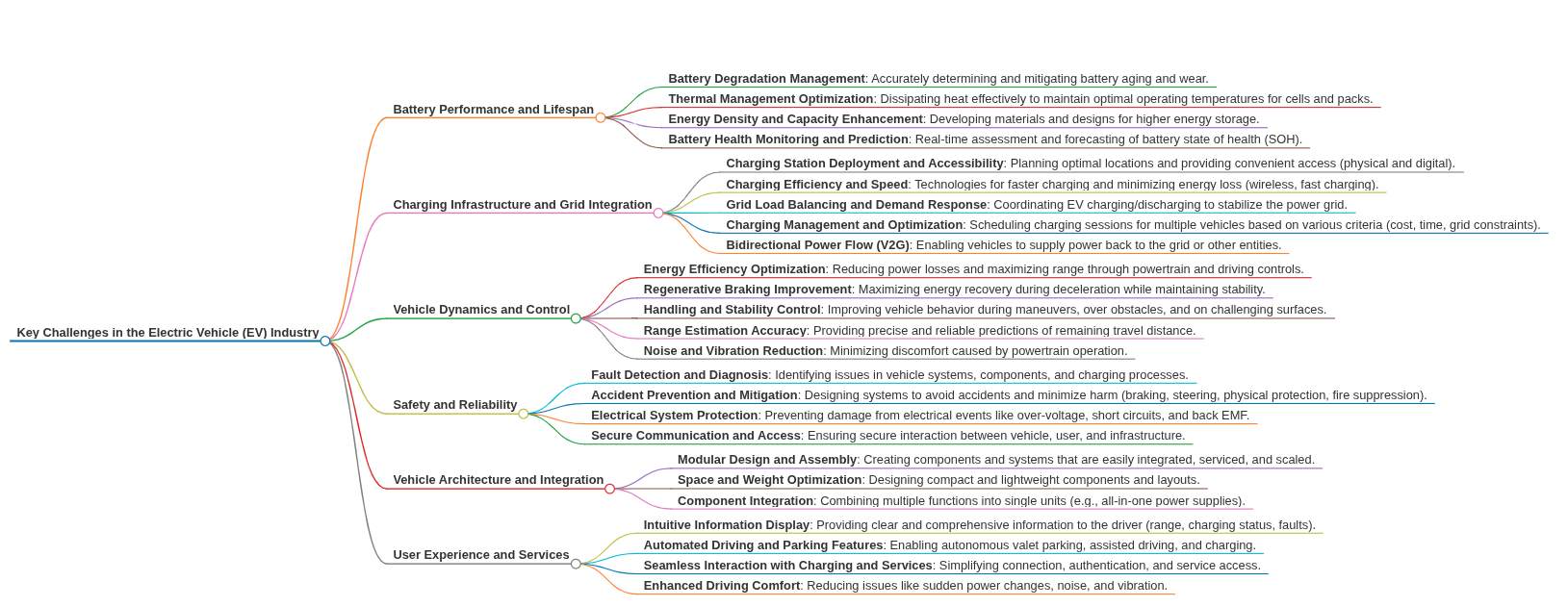