EV Battery Discharge Management Solutions
Electric vehicle batteries face significant capacity fade over their operational lifetime, with cells typically losing 20-30% of their initial capacity within 1000-2000 cycles. This degradation stems from multiple mechanisms: lithium loss during cycling, structural changes in electrode materials, and unwanted side reactions between electrodes and electrolytes—particularly during high-rate charging and temperature extremes.
The fundamental challenge lies in maintaining stable cycling efficiency while balancing the competing demands of fast charging capability, energy density, and battery longevity.
This page brings together solutions from recent research—including advanced electrolyte formulations with optimized lithium salt concentrations, electrode surface modification techniques, targeted lithium supplementation methods, and intelligent charging protocols. These and other approaches focus on practical implementations that can extend battery life while maintaining the performance requirements of modern electric vehicles.
1. Lithium Secondary Battery with Positive Electrode Additive Having Specific Charge/Discharge Capacity Ratio
LG Energy Solution, Ltd., 2023
Lithium secondary battery with improved performance by using a specific ratio of charge/discharge capacity for the positive electrode additive during initial charging. The additive, represented by formula 1, is an irreversible compound that reduces lithium ion loss during charging. By adjusting the charge/discharge capacity ratio of the additive to 50-100% during initial charging, it reduces oxygen gas generation, prevents self-discharging, and improves open circuit voltage. This improves battery performance compared to conventional additives with higher oxygen gas generation.
2. Lithium Manganese Nickel Oxide Positive Electrode with Sulfate Coating from Sulfur Precursor Treatment
UIF (University Industry Foundation), Yonsei University, 2023
Lithium-rich secondary battery with improved capacity, stability, and lifespan by modifying the surface of the positive electrode active material. The modification involves treating the lithium manganese nickel oxide (LMNO) positive electrode material with a sulfur precursor like thiourea to create a sulfate coating on the surface. The resulting battery has reduced oxygen irreversible extraction during charging/discharging, preventing structure collapse and voltage drop. The sulfur content in the modified electrode is 0.3-1.0% by weight.
3. Electrified Vehicle Battery Thermal Management System with Adaptive Temperature Threshold Adjustment
FORD GLOBAL TECH LLC, FORD GLOBAL TECHNOLOGIES LLC, 2023
An electrified vehicle with a thermal management system for the battery that can prioritize battery health or efficiency based on overall battery condition. The system sets multiple temperature thresholds for the battery, and adjusts them when the battery condition is outside a predefined range. It then conditions the battery at the appropriate threshold based on which one is met or exceeded. This allows selective prioritization of battery health preservation versus efficiency optimization.
4. Lithium-Ion Battery with Vinylene Carbonate Solvent and Non-Alloying Negative Electrode Current Collector
Panasonic Intellectual Property Management Co., Ltd., 2022
A lithium-ion battery design that reduces degradation during cycling by preventing reaction between lithium metal deposited on the negative electrode and the electrolyte. The battery uses a specific solvent, vinylene carbonate, in the electrolyte solution. Lithium metal precipitates on the negative electrode during charging, and during discharging, it dissolves back into the electrolyte. The vinylene carbonate solvent prevents direct contact between the lithium metal and the electrolyte, avoiding electrolyte decomposition and reaction with the lithium. This improves cycle life compared to batteries with other solvents. The battery also has a negative electrode current collector that doesn't alloy with lithium to further prevent electrolyte reactions.
5. Lithium Ion Battery Charging and Discharging Method with Selective Lithium Supplementation for Third and Fourth Electrodes
ZHEJIANG FUNLITHIUM NEW ENERGY TECH CO., LTD., 2022
Charging and discharging method for lithium ion batteries with high capacity retention rate, especially for batteries with additional third and fourth electrodes. The method involves selective lithium supplementation and controlled discharge of the third and fourth electrodes. When the battery capacity attenuates, the third and fourth electrodes are charged to replenish lithium. This prevents irreversible capacity loss. The discharge capacity of the third and fourth electrodes is calculated based on current and time to avoid excessive lithium precipitation. The method allows targeted lithium release based on cell needs and prevents dendrites.
6. Lithium Ion Battery Control System with Graphite Electrode Occlusion Monitoring for Charge/Discharge Adjustment
HONDA MOTOR CO., LTD., 2022
Lithium ion battery control to minimize deterioration by optimizing charging and discharging based on lithium ion occlusion. The control involves monitoring a degree of lithium ion occlusion in the battery's graphite negative electrode, which changes with charge/discharge, and adjusting charging/discharging to keep occlusion close to a specific region associated with lower degradation. This prevents excessive occlusion in regions prone to high occlusion. By targeting the region with lower occlusion, it reduces overall battery degradation compared to conventional methods.
7. Battery Management System with Dynamic Temperature Adjustment for Charge-Discharge Cycle Optimization
Alan C. Knudson, 2021
Battery management system that improves battery lifespan by dynamically adjusting battery temperature during charge and discharge cycles. The system cools new batteries to slow aging, heats older batteries during charge to prevent lithium plating, and cools partially charged batteries to slow aging. It predicts duty cycles, monitors plating, and adjusts charge temps to prevent plating. This targeted temperature control extends battery life beyond static temps.
8. Formation Cycle for Lithium-Ion Batteries with Spinel Cathodes Incorporating Controlled Charge-Discharge and Thermal Storage Steps
RENAULT s.a.s., 2020
Process to reduce degassing and self-discharge in lithium-ion batteries with spinel cathodes like LiNixMn2-xO4 (LNMO) with 0<x≤0.5. The process involves a specific formation cycle for the battery. It includes charging the battery to full capacity, discharging it to 10-0% state of charge, then storing it for a week at 15-45°C. This cycle improves stability and reduces degassing/self-discharge of the LNMO cathode compared to standard battery formation. The process can also involve charging to 10-20% instead of full capacity.
9. Battery Temperature Management System with Dynamic Target Adjustment for Charge/Discharge Cycles
OXIS ENERGY LTD, 2020
Temperature management of batteries like lithium-sulfur cells that allows optimizing performance and reducing energy consumption by dynamically adjusting the target battery temperature during charging and discharging. A controller changes the battery temperature using heating/cooling to a variable target instead of a constant one. This allows operating the battery at lower temperatures during certain parts of charge/discharge cycles without significantly degrading performance. By varying the target temperature instead of maintaining a constant one, less heating/cooling is needed overall and efficiency improves.
10. Lithium Metal Rechargeable Battery with Thin Anode, High Salt Electrolyte, and Low Capacity Cathode
SolidEnergy Systems, LLC, 2019
High energy density, high power lithium metal rechargeable batteries with volumetric energy density >1000 Wh/L and gravimetric energy density >350 Wh/kg, capable of discharging >1 C at room temperature. The batteries have thin lithium metal anodes (<20 µm), low capacity cathodes (n/p < 1), thin separators (<12 µm), and electrolytes with high salt concentration (>2 M Li) to suppress dendrite growth. The thin anode allows high capacity cathodes without excess lithium. The separator isolates dendrites from the cathode. The high salt electrolyte improves cycling.
11. Lithium-Ion Battery Cathode with Irreversible Capacity Loss and Voltage Step for Over-Discharge Protection
A123 Systems, LLC, 2019
Protecting lithium-ion batteries from over-discharge damage by using a cathode material that has irreversible capacity loss during charging and a voltage step below 2V versus lithium. This cathode provides over-discharge protection by preventing copper current collector dissolution during over-discharge because the anode voltage remains below the copper dissolution potential. The cathode composition is xLi2MnO3.(1−x)LiMnaNibCocO2 with x=0.41 to 0.59. The specific composition and ratio of Mn, Ni, Co, and Li can be selected to achieve the desired irreversible capacity loss and voltage plateau.
12. Lithium-Ion Battery System with Manganese-Nickel Oxide Cathode and Lithium-Titanium Oxide Anode Featuring Specific Capacity Ratio
HITACHI CHEMICAL COMPANY, LTD., 2019
A lithium-ion battery system with improved input power and energy density by balancing the capacity ratio of the cathode and anode. The system uses a lithium-ion battery with a manganese-nickel oxide cathode and a lithium-titanium oxide anode. The anode-to-cathode capacity ratio is 0.7 or more and less than 1. This optimizes energy density and prevents excessive cathode potential to suppress electrolyte degradation. The end-of-charge voltage is regulated between 3.6 and 4.0V.
13. Vehicle Battery Temperature Equalization System with Heat Exchanger and Sensor-Controlled Activation
BYD Company Limited, 2019
Temperature regulation system for vehicle batteries that improves battery cycle life by equalizing battery temperatures when they differ significantly. The system uses a heat exchanger to balance temperatures between batteries when the difference exceeds a threshold. Temperature sensors monitor battery temperatures and a controller determines if equalization is needed. This prevents excessive heating or cooling of batteries that can degrade performance.
14. Heat Exchanger System for Equalizing Temperature Variations in Electric Vehicle Battery Packs
BYD CO LTD, BYD COMPANY LTD, BYD Company Limited, 2019
Temperature balancing system for electric vehicle batteries that improves cycle life by equalizing battery temperatures when they differ excessively. The system uses a heat exchanger connected to multiple battery thermal management systems. When battery temperature difference exceeds a threshold, a pump circulates coolant through the exchanger to balance temperatures. This prevents excessive temperature variations that degrade battery performance.
15. Lithium-Ion Battery with Dimethyl Carbonate Electrolyte and Defined Voltage Range
HITACHI CHEMICAL COMPANY, LTD., 2019
Lithium-ion battery with improved initial capacity and cycle life for applications like electric vehicles. The battery uses a specific electrolyte and voltage range when charging and discharging. The electrolyte contains dimethyl carbonate (DMC) and the charging voltage is 3.4-3.8 V. The discharging voltage is 2.0-2.8 V. This combination helps prevent electrolyte decomposition and manganese expansion during charging, while avoiding lithium plating and manganese reduction during discharging.
16. Battery Thermal Management System with Temperature-Responsive Current Regulation and Microcontroller-Based Monitoring
Yanfeng Visteon Electronics Technology (Nanjing) Co., Ltd., 2019
Battery thermal management system and charging/discharging control method for electric vehicles that improves battery life and safety by optimizing charging/discharging currents based on battery temperature, temperature rise, and internal resistance. The system uses a microcontroller (MCU) and temperature sensors to monitor battery conditions during charging and discharging. It adjusts current limits, balances charge/discharge, and regulates cooling to prevent overheating, smoldering, leaking, short circuiting, fires, and explosions.
17. Battery Pack with Controlled Cutoff Voltage for Silicon-Containing Negative Electrodes
SAMSUNG ELECTRONICS CO., LTD., 2018
Battery pack design and charge/discharge control to improve cycle life of lithium batteries with silicon-containing negative electrodes. The pack has a predetermined cutoff voltage during discharge to prevent excessive lithium deintercalation from the silicon that can cause cracks. This prevents capacity fade and cycle degradation by avoiding the strain-induced cracking in the amorphous lithium-silicon phase that forms during charge/discharge cycling. The cutoff voltage is set to limit lithium concentration in the silicon below a threshold that avoids cracking during discharge.
18. Battery System with Controller-Driven Thermal and Charge Rate Management
CPS TECHNOLOGY HOLDINGS LLC, 2017
Battery system for vehicles that improves battery charging efficiency and performance by optimizing temperature and charge conditions. The system uses a battery module, thermal management system, and controller. The controller analyzes factors like battery temperature, charge, capacity, power availability, and thermal capabilities. It then determines desired battery temperature and charge rate based on this data. The thermal system heats/cools the battery to the desired temp while the power sources charge the battery at the optimal rate. This allows maximizing battery charge capacity by matching the temperature to the charge rate. It also saves power by using excess regenerative braking energy to heat/cool the battery instead of dumping it.
19. Secondary Battery Module with Multiple Switchable Cooling Circuits for Temperature Uniformity
HITACHI LTD, 2015
A secondary battery module for electric vehicles and energy storage systems that has multiple cooling circuits to prevent temperature variation and reduce battery life degradation in multi-cell modules. The module has multiple secondary batteries and a cooling system with multiple refrigerant flow paths. The flow paths can be switched so that cold refrigerant contacts the hottest batteries. This counterflow cooling configuration prevents temperature gradients and reduces variations in battery life due to self-heating during charging/discharging.
Get Full Report
Access our comprehensive collection of 19 documents related to this technology
Identify Key Areas of Innovation in 2025
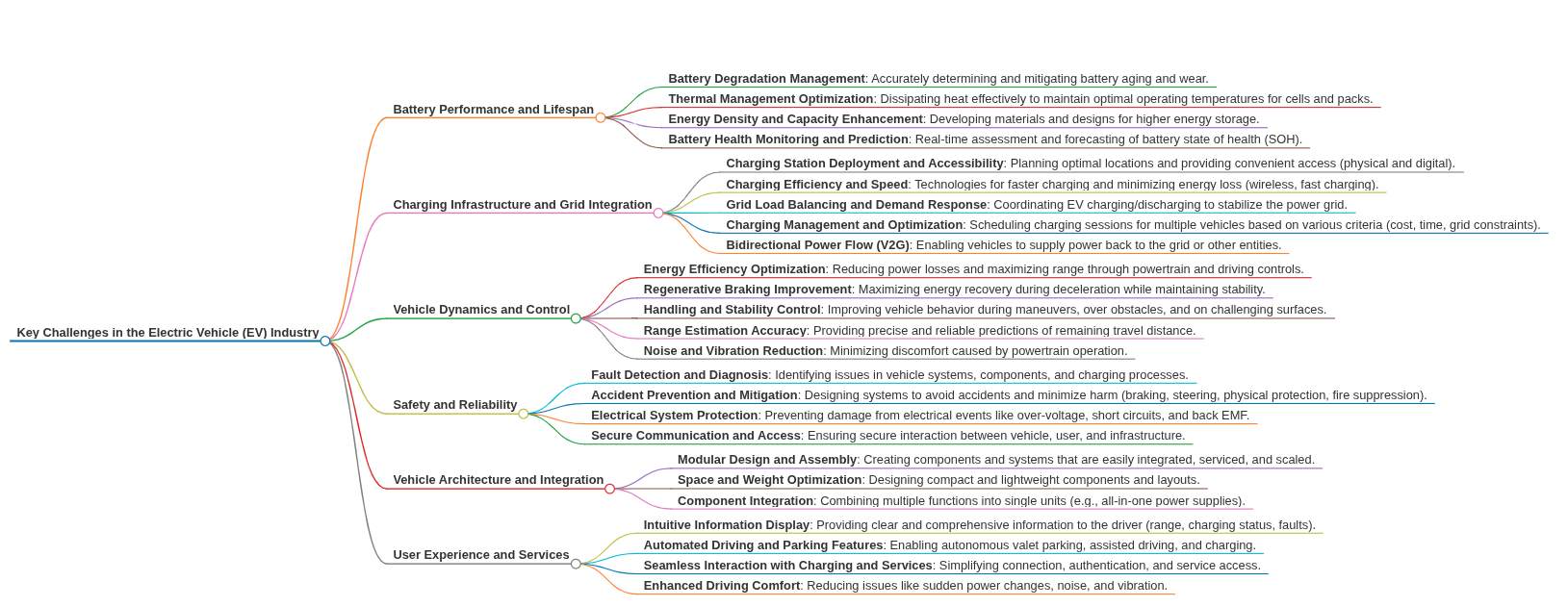