Tesla's Innovations in EV Battery Thermal Management
Tesla's battery packs operate across demanding thermal conditions, managing heat loads that can exceed 12kW during rapid charging and varying ambient temperatures from -30°C to 45°C. The thermal management system must maintain optimal cell temperatures while handling both routine heat generation and potential thermal events that can cascade through thousands of cells in minutes.
The fundamental challenge lies in balancing rapid heat extraction for performance with the reliability, safety, and energy efficiency demands of a mass-produced electric vehicle.
This page brings together solutions from recent research—including integrated heat exchanger designs, predictive thermal conditioning, multi-mode cooling valves, and passive safety systems for thermal events. These and other approaches demonstrate how Tesla addresses thermal management across normal operation, fast charging, and emergency scenarios while maintaining system simplicity.
1. Battery Pack Coolant Ingress System with Fill Port Access and Breach-Sealing Mechanism
Tesla, Inc., 2021
A system for providing coolant ingress into an electric vehicle battery pack during internal thermal events to mitigate chain reactions. The system has a fill port access mechanism that allows water or other coolant to be directed into the battery pack through a breach made in the enclosure wall. The breach is created using a specialized tool that pierces the enclosure without damaging it. This allows responders to introduce coolant into the pack during emergencies where the normal fill port is unavailable. The breach is sealed after coolant ingress to prevent ongoing ingress.
2. Electric Vehicle Battery Enclosure with High Voltage Electrolysis Detection and Response System
Tesla, Inc., 2020
Detecting and responding to high voltage electrolysis within an electric vehicle battery enclosure to limit possible excessive thermal conditions and prevent runaway thermal events. The system detects high voltage electrolysis, such as coolant bridging terminals and electrolysis, and responds by stopping the energy driving the electrolysis and lowering the coolant boiling point to prevent runaway thermal conditions. This mitigates risks from electrolysis-induced thermal runaway and hydrogen buildup in the battery pack.
3. Integrated Battery Pack Enclosure with Dual-Mode Heat Exchanger and Thermally Coupled Base Plate
Tesla, Inc., 2019
Integrated battery pack heat exchanger system for electric vehicles that provides efficient heat transfer while utilizing vehicle surfaces. The system involves integrating the heat exchanger into the battery pack enclosure that is mounted under the vehicle floor. The heat exchanger conduits are thermally coupled to the inside surface of the enclosure base plate. When the thermal management system configures the system into the first operational mode, the heat exchanger is coupled to the batteries. In the second operational mode, it is decoupled. This allows the base plate exposed to ambient air flow during vehicle motion to act as a large heat transfer surface. A blower fan can be used to direct air over the base plate.
4. Vehicle Thermal Management System with Adjustable Coolant Bypass Valve for Heat Exchanger Flow Regulation
TESLA, INC., 2019
A vehicle thermal management system that allows precise control of heat rejection from the battery coolant to the refrigeration system. The system uses a bypass valve in the coolant loop that allows splitting the coolant flow between directly passing through the heat exchanger and bypassing it. This allows regulating the coolant flow through the heat exchanger based on coolant temperature, battery pack temperature, or other factors. The bypassing reduces heat transfer if the coolant is already cool enough, preventing excessive heat rejection to the refrigeration system. The system continuously monitors coolant temperature and adjusts the bypass valve to maintain optimal coolant temperatures.
5. Heatsink Assembly with Interlocking Staggered Fins for Enhanced Liquid Cooling
Tesla, Inc., 2019
Heatsink design for liquid cooling of electronic components with internal fins that improve cooling performance. The heatsink has two cast parts, one with fins extending into an internal cavity and the other with fins that fit between the first part's fins. An inlet and outlet are on either part. The staggered fin arrangement allows efficient cooling by overlapping fin arrays. The internal cavity provides a contained path for liquid cooling. The cast fins can have drafts to aid manufacturing.
6. Passive Drain Device with Coolant-Reactive Expanding Element for Electric Vehicle Battery Enclosures
TESLA, INC., 2018
Self-activating drain system for electric vehicle battery packs to automatically remove leaked coolant without human intervention. The system uses a passive drain device with a dissolvable element that reacts to the coolant and expands to open a valve and drain the leaked coolant. The device is installed in the battery pack enclosure wall and seals tightly when coolant is present. If coolant leaks, the expanding element opens the valve to drain the leaked coolant. This protects the battery internals from coming into contact with coolant if the cooling system fails.
7. Battery Pack Cooling System with Flat Evaporator Heat Pipes for Direct Cell Contact
Tesla, Inc., 2017
A compact and efficient cooling solution for battery packs in electric vehicles. The cooling uses heat pipes with flat evaporators that contact the cell second ends. The cells are arranged with aligned second ends to maximize contact between the heat pipes and cells. This provides direct heat transfer from the cells to the heat pipes without intermediary cooling fluid. The heat pipes can then transfer the heat to an external heat sink or radiator. This eliminates the need for cooling fluid connections inside the battery pack and simplifies cooling system design.
8. Battery Pack System with Predictive Charge Rate Identification and Adaptive Temperature Profiling
TESLA, INC., 2017
Early identification of an impending fast-charge opportunity for battery packs in electric vehicles and using that information to prepare the batteries for fast-charging. The system predicts if an upcoming charge will be fast or slow, and adjusts the battery temperature profile accordingly. For fast charging, the temperature is raised above the standard operating temperature to improve performance. For slow charging, the temperature is lowered to preserve lifetime. This allows optimizing battery temperature for specific charge rates.
9. Automated Charging System with Dynamic Rate Adjustment for Low-Temperature Lithium-Ion Batteries
Tesla, Inc., 2017
Automated low temperature fast charging system for lithium-ion batteries that enables fast charging at cold temperatures without risk of lithium plating damage. The system monitors critical parameters periodically and dynamically scales the charging rate based on those parameters. If the parameters allow, it uses a high rate charging process. If not, it uses a slower rate charging process that won't cause plating. This allows charging at low temperatures without disabling fast charging.
10. Energy Storage Pack with Scalloped Cooling Tubes and Curved Internal Ribs for Battery Modules
Tesla Motors, Inc., 2017
Energy storage pack design with improved thermal management for battery modules. The pack uses scalloped cooling tubes that connect between cells instead of having the cells directly attach to the module housing. This allows curing the adhesive between cells and tubes using radiation. Areas shielded from radiation are cured using a secondary mechanism. The scalloped tubes also have curved or slanted internal ribs for easier manufacturing and better thermal performance with bends. The flexible module design allows using different cell types, orientations, and placeholders.
11. Vortex Separator System for Debris and Gas Management in Electrochemical Cell Enclosures
Tesla Motors, Inc., 2016
Containing and separating debris and gases during thermal runaway events in electrochemical cells like batteries to prevent ignition. The system uses a vortex separator inside the battery enclosure with an inlet from the battery chimney and outlets to the outside and a catch basin. During a thermal runaway, particles ejected by the cell are confined in the catch basin while the gases escape through the vortex separator. This prevents sparks from contacting the gases and potentially igniting.
12. Battery Pack Thermal Conditioning System with External Fluid Loop and Adaptive Temperature Control During Charging
Tesla Motors, Inc., 2016
System for thermally conditioning an electric vehicle's battery pack during charging to maintain optimal temperature. The system involves providing external cooling or heating to the battery pack while charging, based on information received from the vehicle about its battery temperature. This allows customized thermal management during charging, which can be different from driving conditions. The external cooling/heating can be provided using a separate fluid loop with an arm extending into the vehicle to connect to the battery pack. This allows more targeted thermal conditioning compared to relying solely on the vehicle's internal cooling system.
13. Manufacturing Method for Lithium-Ion Cells Using Liquid-Based Thermal Conditioning System
Tesla Motors, Inc., 2016
A manufacturing method for lithium-ion cells that improves efficiency and accuracy by using a liquid-based thermal system to condition the cells during various stages of assembly and testing. The method involves storing cells in contact with a liquid thermal system after assembly, circulating liquid at a first temperature, then cooling to a second lower temperature before testing. This allows even heating and cooling for more accurate capacity checks. The cells are discarded or kept based on open circuit voltage tests at different temperatures.
14. Series-Connected Battery Pack Management with Dual-Modality Exceptional Charge Event Detection and Response Mechanisms
Tesla Motors, Inc., 2016
Detecting and responding to exceptional charge events in series-connected battery packs to prevent overcharge and overdischarge in individual cells. The method involves detecting exceptional charge events using different modalities for steady state and transient charging conditions. Steady state detection involves analyzing statistical parameters over time. Transient detection looks for deviations in cell characteristics during fast charge/discharge. Responses to exceptional charge events include preventing further charging, increasing cooling, and limiting future charging.
15. Automotive Thermal Management System with Non-Stacked Heat Exchanger Configuration and Adjustable Airflow Louvers
Tesla Motors, Inc., 2016
An automotive thermal management system with improved cooling efficiency and reduced fan power compared to stacked heat exchangers. The system has multiple heat exchangers arranged in a non-stacked configuration with separate inlets and adjustable louvers. An airflow duct connects some heat exchangers. Louvers control airflow between heat exchangers in the duct. This allows optimized cooling by selectively routing air based on temperature and need. It prevents hotter upstream air affecting downstream heat exchangers. The non-stacked layout reduces overall fan power by avoiding ducting air through all exchangers.
16. Multi-Element Battery Pack with Charge State Detection and Remediation Mechanism
Tesla Motors, Inc., 2015
Detecting and remediating exceptional charge states in individual battery elements of a multi-element battery pack to prevent overcharging and overdischarging. The method involves monitoring charge-dependent parameters of each battery element during operation to establish a normal charge characteristic pattern. An exceptional charge event is detected when a battery element's charge pattern deviates from normal during a time segment where it should match. This indicates an imbalance that could lead to overcharge or overdischarge. Responses include preventing charging, increasing cooling, or limiting future charging to prevent further imbalance.
17. Battery Pack Thermal Runaway Mitigation System with Temperature-Activated Fluid Conduit
Tesla Motors, Inc., 2015
Mitigating the effects of thermal runaway in battery packs to prevent propagation and contain thermal events. The system uses a fluid-filled conduit around the cells that forms breaches when cells reach a threshold temperature. This discharges the fluid onto the hot cells to cool them and stabilize temperatures. It can also have pumps, valves, sensors, and gas sources to actively cool cells and breach the conduit. The fluid can be liquid, gas, or expanding foam.
18. Sealed Battery Pack Pressure Monitoring System with Exponential Decay Analysis for Thermal Runaway Detection
Tesla Motors, Inc., 2015
Early detection of thermal runaway events in sealed battery packs to quickly respond before propagation. The method involves monitoring pressure within the pack and analyzing pressure anomalies. Pressure peaks with anomalies are fitted with curves. If the trailing edge curves show exponential decay with a specific time constant range, it indicates thermal runaway. A response is triggered for that pack. Fitting and time constant checking distinguishes true runaway from false positives caused by vibration, altitude, etc.
19. Battery Arrangement System with Rigid Substrate Sandwiching and Opposing Flow Cooling Channels
Tesla Motors, Inc., 2015
A system for arranging multiple batteries in a stable and resilient configuration to improve reliability, thermal management, and packing density compared to stacking batteries. The batteries are sandwiched between rigid substrates to distribute force and prevent crushing. Conductors draw power and connect the batteries in parallel/series. Holes in the substrates prevent shorting. Cooling channels run between the batteries and adjacent tubes flow in opposite directions to maintain constant temperature.
20. Battery Pack Monitoring System with Electrical Isolation Resistance Detection for Thermal Runaway Precursors
Tesla Motors, Inc., 2015
Early detection of thermal runaway events in battery packs to mitigate fire risks and damage. The system monitors the electrical isolation resistance of the battery pack. When the resistance falls below a threshold, indicating cell failure, it triggers a response. The response may include warning indicators, reducing load, increasing cooling, and fire containment. The response is based on factors like fall-off rate, time to recovery, and secondary effects like voltage drop, temperature rise, or humidity increase. This allows detecting thermal runaway precursors and taking action before gas escapes.
Get Full Report
Access our comprehensive collection of 63 documents related to this technology
Identify Key Areas of Innovation in 2025
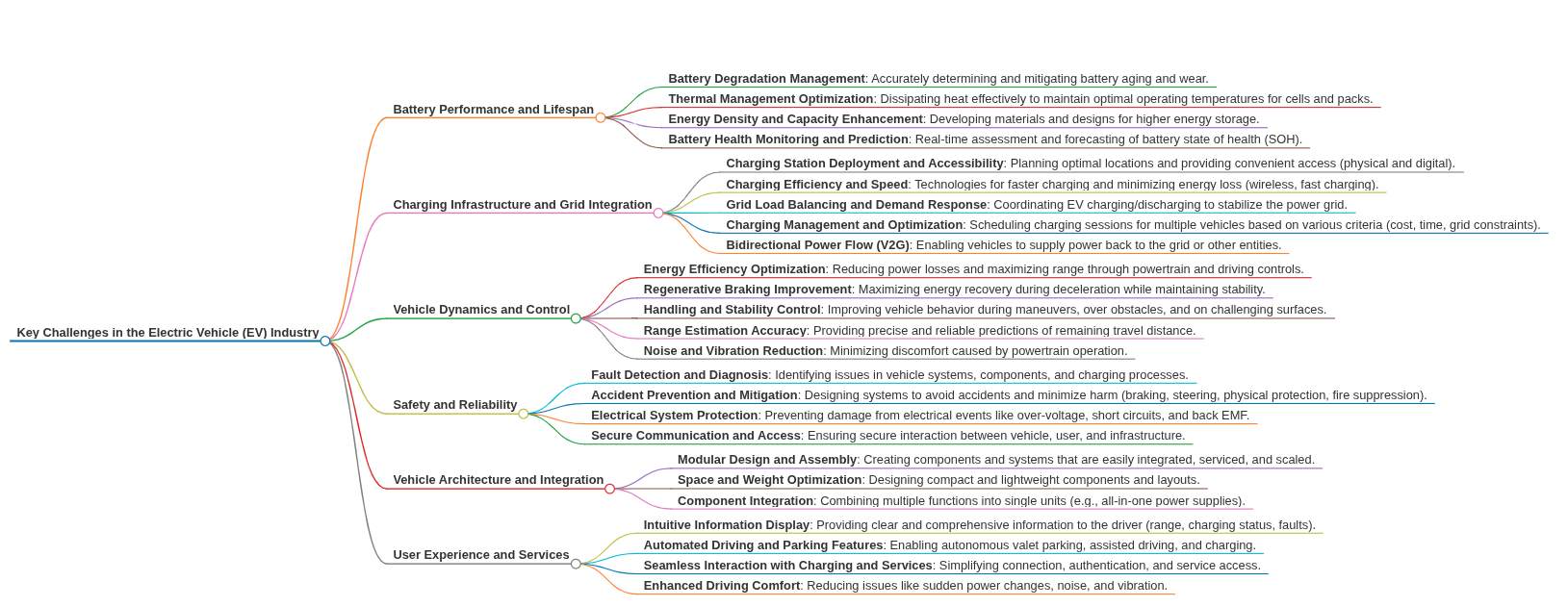