Tesla's Crash Protection Methods for EV Batteries
Electric vehicle battery packs present unique crash protection challenges, with Tesla's Model S/3/X/Y packs containing thousands of cylindrical cells storing up to 100kWh of energy in spaces exceeding 2 meters in length. During severe impacts, maintaining pack integrity while managing thermal and electrical hazards requires multiple coordinated protection systems.
The fundamental challenge lies in protecting the high-voltage battery system from mechanical intrusion while simultaneously preventing thermal runaway propagation and maintaining electrical isolation in crash scenarios.
This page brings together solutions from recent research—including compartmentalized pack designs with dedicated venting, pyrotechnic battery disconnection systems, and structural integration of the pack into the vehicle's crash absorption architecture. These and other approaches demonstrate how modern EVs achieve both occupant and battery protection during collision events.
1. Self-Activating Battery Enclosure Drain with Expandable Absorbent Material and Membrane Release Mechanism
TESLA, INC., 2018
A self-activating drain device for battery systems that automatically expels leaked liquid from the battery enclosure when a coolant leak occurs. The drain device has a sealed port covered by a membrane. Inside is an absorbing material that expands when it comes into contact with the leaking liquid. This expansion opens the membrane and allows the liquid to drain out. The expanded absorbing material can also trigger other actions like deactivating coolant pumps or warning the user. The drain device is positioned in the battery enclosure wall to catch any leaks and prevent internal components from coming into contact with the liquid.
2. Electric Vehicle High Voltage Battery Decoupling System with Integrated Pyrotechnic Switch
Tesla Motors, Inc., 2015
Decoupling the high voltage battery of an electric vehicle in the event of a collision to prevent electrical hazards and fires. It replaces the conventional inertial switch with a pyrotechnic switch integrated into the vehicle electrical system. The pyrotechnic switch receives activation signal from the airbag system during a crash. In the normal state, it allows battery connection through the main contactor. But upon collision detection, it severs the connection preventing the battery from supplying power to the vehicle electrical system. This ensures decoupling in controlled conditions versus inertial switches that can trigger prematurely.
3. Vehicle Adapter with Integrated Drive Shaft Passage and Crash Load Path Bridging Mechanism
Tesla Motors, Inc., 2015
Vehicle adapter to route a drive shaft through a crash load path while allowing the vehicle crush rail to direct crash forces into a back-up structure. The adapter bridges between the crash rail and back-up structure, has a socket for the rail, a plug for the back-up, and an opening for the shaft. The adapter can deform during crashes to absorb impact energy. This keeps the crash load path low vertically to accommodate the shaft while still directing forces into the back-up structure.
4. Vehicle Side Impact Protection System Incorporating Battery Pack with Integrated Cross-Members
Tesla Motors, Inc., 2015
A vehicle side impact protection system that uses the battery pack enclosure as an integral part of the vehicle structure to absorb and distribute side impact forces. The battery pack is positioned between the front and rear suspension and mechanically coupled to the rocker panels. Cross-members within the battery pack absorb and distribute impact forces when either side of the vehicle is hit. This avoids the need for dedicated heavy side impact structures while still providing protection. The battery pack enclosure also segregates the batteries into groups and can thermally isolate them.
5. Reinforced B-Pillar Assembly with Integrated Rocker Panel Coupling and Extended Brace
Tesla Motors, Inc., 2014
A reinforced B-pillar assembly for vehicles that provides improved side impact protection by directly coupling the B-pillar to the rocker panel and an extended brace above the rocker. The assembly has a B-pillar brace welded to the rocker's upper surface, extending above, and a B-pillar section welded to the rocker's outer surface. The B-pillar section also connects to the brace section. This integrates the B-pillar into the rocker structure for stronger side impact resistance compared to separate components.
6. Innovative Compartmentalized Battery Pack Design for Enhanced Thermal Runaway Mitigation
Tesla Motors, Inc., 2013
Battery pack design to mitigate the hazards of battery thermal runaway. The pack has multiple sealed compartments, each containing a battery. Each compartment has a vent assembly with a valve and exhaust port. The valve seals the port under normal conditions. During thermal runaway, the valve unseals and allows hot gases to escape. The compartments are also divided by cross-members to prevent cell-to-cell propagation. A central member further isolates the cells. An exterior exhaust guide directs expelled gases away from the pack. This compartmentalization, isolated venting, and guided exhaust mitigates thermal runaway spread and prevents catastrophic pack failure.
7. Vehicle Side Rail with Integrated Friction and Deformation-Based Crash Structure
Tesla Motors, Inc., 2013
Crash structure integrated into a vehicle side rail that uses a combination of friction and deformation to achieve a crash structure that yields relatively constant loading during a collision. The structure has a hollow housing with deformable members inside. An actuator member slides into the housing. The actuator has a larger diameter section that engages the deformable members. During a crash, the actuator slides into the housing while the deformable members deform and the actuator frictionally engages them. This provides consistent loading on the vehicle structure compared to step-like deformation. The structure can be tuned by varying deformable member stiffness.
8. Vehicle Front Structure with Offset Non-Parallel Rails and Octagonal Hollow Channels
Tesla Motors, Inc., 2013
Vehicle front structure that provides enhanced load distribution, occupant safety, and weight reduction compared to conventional front end designs. The structure uses offset front rails, octagonal hollow channels, and integrated battery enclosures to improve crash protection and reduce weight. The front rails are non-parallel and wider than height. The hollow channels have octagonal cross-sections. The rails connect bumper to torque boxes with crush cans. The battery enclosure sits between rocker panels and is attached to the rails. This integrated layout improves load distribution, occupant protection, and simplifies repairs compared to separate bumper, rail, and battery structures.
9. Battery Pack with Cell Isolation and Venting via Interruptible Connectors and Scored Terminal Vents
Tesla Motors, Inc., 2013
A battery pack design that integrates cell isolation and venting to prevent propagation of cell failures. The design uses interruptible electrical connectors between the battery terminals and pack connectors. When a cell vent ruptures due to overpressure, the connector breaks, disconnecting the cell and preventing gas propagation. The connectors are ultrasonically or resistance welded to the terminals. The terminals have scored venting areas. An insulating potting material covers the terminals and connectors. A support substrate separates the connectors from the cell. This prevents vent gases from escaping into adjacent cells.
10. Battery Cell Enclosure with Secondary Can for Controlled Gas Venting and Thermal Insulation
Tesla Motors, Inc., 2013
Battery design to prevent thermal runaway propagation and collateral damage in multi-cell battery packs. The design involves adding a pre-formed secondary can around the battery cell case that inhibits gas escape through the cell wall during thermal runaway. The secondary can is made of high yield strength materials to prevent perforation. This forces gas to exit through the cell ends instead of the sides. The secondary can also have a higher thermal resistance to reduce conductive heat transfer.
11. Compact Vehicle Crash Structure with Frictional and Deformable Actuator Mechanism
Tesla Motors, Inc., 2013
Compact vehicle crash structure that provides relatively constant loading during a collision while requiring minimal space. The structure uses a combination of friction and deformation to achieve this. It has a hollow housing attached to the vehicle side rail, an actuator that slides into the housing, and deformable members surrounding part of the actuator. The actuator diameter increases between the housing and bumper. The deformable members deform as the actuator slides, then the housing collapses after. This provides consistent loading compared to stepwise folding structures.
12. Vehicle Seat Mounting Assembly with Cross-Members Connecting Seat Mounts to Structure and Battery Pack Enclosure
Tesla Motors, Inc., 2012
Vehicle seat mounting assembly that improves crash safety and reduces weight compared to conventional seat mounts. The assembly uses cross-members between the vehicle sides to connect the seat mounts to both the vehicle structure and the battery pack enclosure. This provides a rigid and load-sharing pathway for crash forces through the seat, structure, and battery pack. It also allows the seat mounts to be mounted lower and closer to the floor without affecting seat adjustment. The cross-members can be welded or bolted to the structure and battery pack.
13. Battery Cell Assembly with Intumescent Coating for Thermal Runaway Mitigation
Tesla Motors, Inc., 2012
Battery assembly to mitigate thermal runaway propagation between cells. The assembly has an intumescent coating on the cell casing sides and bottom, excluding contact regions. The intumescent material absorbs heat, expands, and forms a barrier as it charrs during thermal runaway. This prevents casing perforation, gas/flame spread, and containment of the affected cell. The coating resists thermal runaway propagation between cells.
14. Battery Cell with Recessed Terminal and Insulating Gasket Covering Terminal and Vent Element
Tesla Motors, Inc., 2011
Simplified design of a battery cell that reduces manufacturing cost, weight, and shorting risk compared to conventional cells. The cell design features a recessed terminal instead of a raised terminal to minimize shorting risk between the cell case and terminal. The terminal is covered by an insulating gasket that expands to cover at least 50% of the terminal surface. This reduces shorting further. The cell also has a simplified cap assembly with a current interrupt device (CID) that breaks connection if pressure exceeds a threshold. The CID is connected to the electrode assembly via the insulating gasket, protecting against shorting. The cap assembly has a vent element that serves as the terminal and is electrically connected to the CID. The vent element is also covered by the insulating gasket.
15. Battery Cell Center Pin with Intumescent Material for Thermal Expansion and Gas Containment
TESLA MOTORS, INC., 2011
Center pin for battery cells that improves thermal runaway behavior by using an intumescent material. The intumescent center pin expands and swells when heated during thermal runaway to prevent cell rupture and contain the internal gases. The intumescent material can fill the hollow center pin void or cover the pin surface. It activates at specific temperatures and expands less than 20x volume. This prevents electrode deformation and shorting while absorbing thermal energy. A secondary non-intumescent material can surround the intumescent layer to prevent chemical reactions.
16. Battery Cell with Center Pin for Controlled Electrode Deformation During Thermal Runaway
TESLA MOTORS, INC., 2011
A battery cell design to prevent rupture during thermal runaway and reduce collateral damage. The cell uses a center pin that melts or deforms at elevated temperatures during abuse conditions like overcharging or short circuiting. This allows the electrode assembly to deform inward instead of outward, preventing wall rupture. The pin is rigid during normal operation to prevent electrode deformation. The pin material has a lower melting/softening point than cell operating temps.
17. Frangible Battery Pack System with Ultrasonically Bonded Aluminum-Magnesium-Nickel Conductors
Tesla Motors, Inc., 2011
Frangible battery pack system for electric vehicles and industrial equipment that disconnects the battery at low force or heat levels to prevent electrocution hazards. The system uses frangible aluminum conductors with magnesium and nickel added that break at specific forces or temperatures. The conductors are bonded to the battery cells and collector plates using ultrasonic wedge bonding. The tunable conductor width allows customization for disconnect strength. The aluminum frangible conductors provide a low-cost, easy-manufacturing alternative to prior art high-strength bonded conductors.
18. Battery Cell Enclosure with Intumescent Coating and Protective Sleeve for Controlled Gas Venting
Tesla Motors, Inc., 2010
Preventing perforations in battery cell walls during thermal runaway to mitigate cell-to-cell propagation and collateral damage. The method involves covering the outer surface of the cell with an intumescent material that expands and seals when heated. This prevents gas escaping through wall perforations and forces it to vent through the cell ends. A sleeve surrounding the intumescent layer maintains separation. This allows controlled gas escape while preventing inter-cell propagation. The intumescent material should have a start expansion temperature in the range of 100-300°C.
Get Full Report
Access our comprehensive collection of 18 documents related to this technology
Identify Key Areas of Innovation in 2025
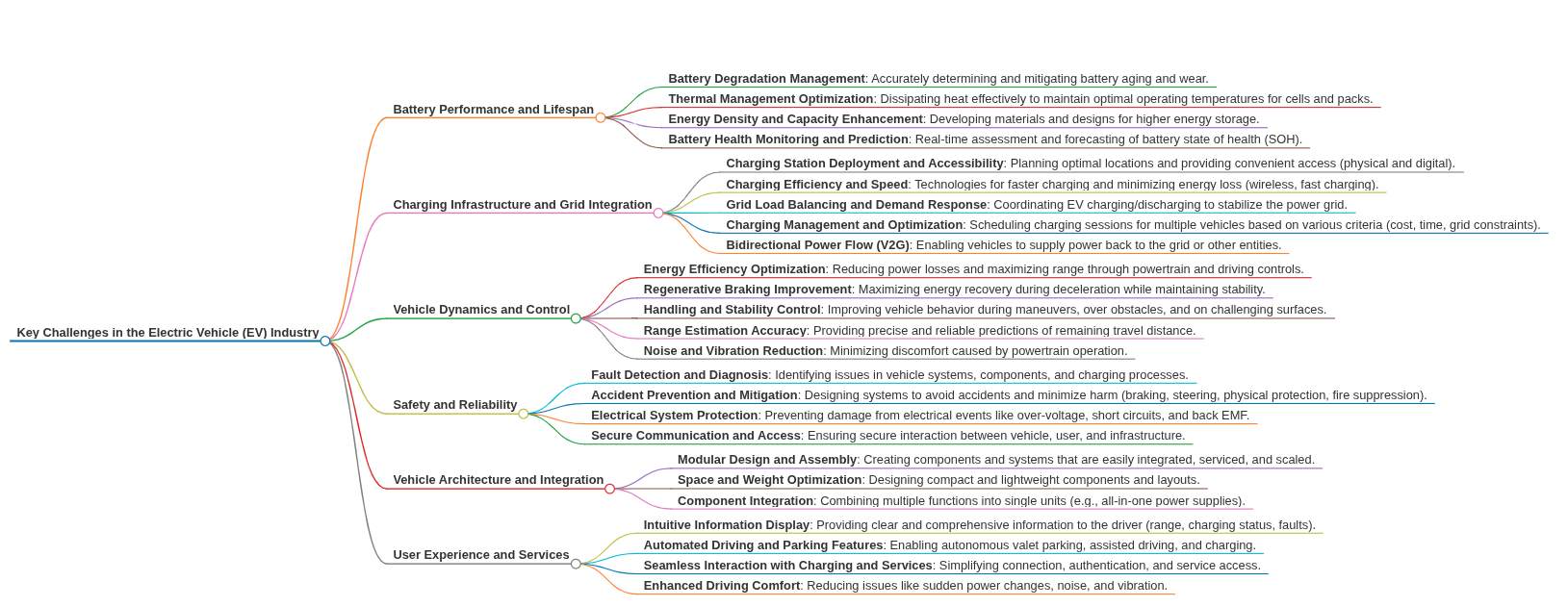