Advances in High-Capacity EV Batteries Research
Modern electric vehicle batteries face fundamental energy density limits, with current lithium-ion cells achieving 250-350 mAh/g in high-capacity layers. Despite optimized cell geometries and enhanced electrode materials, the practical energy density of production battery packs remains below 300 Wh/kg—far short of the theoretical maximum for lithium-based chemistries.
The core challenge lies in balancing increased energy density against cycle life, thermal stability, and fast-charging capability.
This page brings together solutions from recent research—including dual-layer electrode architectures, surface-modified lithium complex oxides, silicon-carbon composite materials, and optimized cell compression designs. These and other approaches focus on practical improvements that can be implemented in mass production while maintaining safety and reliability standards.
1. A Highly Conductive Halospinel Cathode for All-Solid-State Batteries
julian f baumgartner, daniel isler, hung quoc nguyen, 2025
High-power Lithium-ion batteries (LIBs) rely on highly ionically and electronically conductive cathode active materials (CAMs). While oxospinels meet these criteria are therefore widely employed in state-of-the-art LIBs, we demonstrate that halospinels offer greatly enhanced transport properties enable the incorporation of earth-abundant transition metals such as iron. Using spinel type Li2-xFeCl4 (02 mA h cm 2) at practical current densities (0.5 over 200 cycles. Our findings position LFC a commercially viable CAM, paving way for cost-effective, high-performance ASSBs.
2. Molecular Engineering Regulation Redox‐Active Sites and Nanostructures of Covalent Organic Framework for High‐Performance Lithium Sulfur Batteries
yiqun xiao, chenze qi, yixuan gao - Wiley, 2025
Abstract Research on the catalytic chemistry of lithium sulfur batteries (LSBs) primarily focuses development active sites, with limited attention given to their structural stability. Furthermore, regulating nanostructure catalysts can enhance stability without compromising intrinsic activity. This work presents a covalent organic framework (COF) dual redoxactive sites (CO and CN) large periodic conjugated (denoted as CONCOF). is constructed through molecular engineering mitigate shuttling polysulfides (LiPSs), accelerate conversion, regulate ions (Li + ) dynamics, prevent dendrite formation, maintain during cycling. Subsequently, CONCOF in situ grown carbon nanotubes enhances electrical conductivity further improves combination significantly boosts performance LSBs, achieving remarkable decay rate 0.021% over 1000 cycles, along an areal capacity 8.3 mAh cm 2 under lean electrolyte conditions. pouch cells incorporating this configuration demonstrate exceptional longterm stability, maintaining 200 cycles. strategy addresses limitations traditional catalyst de... Read More
3. Thin-Film All-Solid-State Battery with Stacked Layers for Lithium Ion Management and Dimensional Stability
SEMICONDUCTOR ENERGY LABORATORY CO LTD, 2025
A thin-film all-solid-state battery with improved safety and capacity compared to liquid electrolyte batteries. The battery has multiple thin films stacked in series to release, transport, and accumulate lithium ions. The films expand/contract during charging to maintain overall thickness. The films contain lithium-releasing, lithium-transporting, and lithium-accumulating layers. This prevents thickness changes and deformation. The films can contain silicon and oxygen to expand/contract during charging.
4. Lithium-Rich Manganese Oxide Cathode with Single Phase Rock Salt Crystal Structure
DYSON TECHNOLOGY LTD, 2025
High capacity lithium-rich manganese oxide cathode compositions for lithium-ion batteries that have a single phase rock salt crystal structure instead of the typical spinel or layered structures. The compositions have a general formula Li1+xMn1-xO2 where 0 < x <= 0.3. This unique crystal structure provides high capacity, stable cycling, and low cost compared to conventional manganese-rich cathodes. The absence of peaks below 35° in the X-ray diffraction pattern indicates the single phase rock salt structure.
5. An Enhanced Cascaded Deep Learning Framework for Multi-Cell Voltage Forecasting and State of Charge Estimation in Electric Vehicle Batteries Using LSTM Networks
supavee pourbunthidkul, narawit pahaisuk, popphon laon - Multidisciplinary Digital Publishing Institute, 2025
Enhanced Battery Management Systems (BMS) are essential for improving operational efficacy and safety within Electric Vehicles (EVs), especially in tropical climates where traditional systems encounter considerable performance constraints. This research introduces a novel two-tiered deep learning framework that utilizes two-stage Long Short-Term Memory (LSTM) precise prediction of battery voltage SoC. The first tier employs LSTM-1 forecasts individual cell voltages across full-scale 120-cell Lithium Iron Phosphate (LFP) pack using multivariate time-series data, including history, vehicle speed, current, temperature, load metrics, derived from dynamometer testing. Experiments simulate real-world urban driving, with speeds 6 km/h to 40 variations 0, 10, 20%. second uses LSTM-2 SoC estimation, designed handle temperature-dependent fluctuations high-temperature environments. cascade design allows the system capture complex temporal inter-cell dependencies, making it effective under variable-load Empirical validation demonstrates 15% improvement estimation accuracy over methods driving co... Read More
6. Composite Anode Particles with Porous Carbon Framework and Silicon Deposition
NEXEON LTD, 2025
High capacity anode material for rechargeable batteries with improved cycling stability and lower expansion compared to silicon-based materials. The anode comprises composite particles with a porous carbon framework containing deposited silicon. The carbon framework has specific pore structure and loading of silicon to balance properties like strength, capacity, and expansion. This allows higher silicon loadings than oxide hybrids while preventing capacity fade and fracturing. The carbon framework limits expansion and prevents electrolyte decomposition, and the controlled silicon deposition prevents agglomeration. The composite particles have high aspect ratio composite particles with high compressive strength.
7. Electrolyte Solution with Fluorinated Ether Compound for Lithium-Sulfur Batteries
DAIKIN INDUSTRIES LTD, 2025
Electrolyte solution for lithium-sulfur batteries that improves performance and lifespan. The electrolyte contains a specific fluorinated ether compound with low viscosity. The compound is represented by the formula CFx(CF2)yOzCH2CHxRy, where x, y, and z are defined numbers. This ether improves the battery output characteristics and capacity retention compared to conventional electrolytes. The low viscosity enables better penetration into the sulfur electrode and electrochemical reaction at the interface.
8. Anode for Lithium Secondary Battery Comprising Magnesium-Doped Silicon and Carbon
SK ON CO LTD, 2025
Lithium secondary battery anode with improved capacity and cycle life for high performance batteries like electric vehicles. The anode contains a silicon-based active material doped with magnesium, along with carbon. The magnesium-doped silicon reduces volume expansion during charging/discharging compared to undoped silicon. This prevents cracks and improves cycle life. The carbon provides electrical conductivity. By adjusting the silicon and carbon contents, rapid charge, room temperature, and high temperature cycle life can be optimized.
9. Stable Solid Electrolyte Interphase in Cylindrical Anode-Free Li-Metal NMC90 Batteries with Li<sub>2</sub>NiO<sub>2</sub> Prelithiation and Fluorine-Rich Electrolytes for High Energy Density
thitiphum sangsanit, ronnachai songthan, surat prempluem - American Chemical Society, 2025
This study advances anode-free lithium-metal batteries (AFLMBs) by integrating nickel-rich NMC90 cathodes and fluorine-rich electrolytes in large-format 18650 cylindrical cells. A key innovation is the incorporation of 10 wt % Li-rich Li2NiO2 as a prelithiation agent cathode, which mitigates initial lithium-loss improves Coulombic efficiency. The electrolyte includes 30% (v/v) fluoroethylene carbonate (FEC) cosolvent, suppresses inactive lithium deposition stabilizes solid interphase (SEI). Unlike conventional AFLMBs that require external pressure, this work uses stainless-steel casing with tailored jelly roll configuration to mechanically regulate plating. optimized cells deliver an energy density 320 Wh/kg, maintain stable cycling over 140 cycles, support 4C-rate operation. Post-mortem analysis reveals LiF-rich SEI extends cycle life, while operando X-ray diffraction provides insights into structural evolution. research offers scalable strategy for high-energy through synergy prelithiation, design, mechanical stabilization.
10. Wide temperature 500 Wh kg‐1 lithium metal pouch cells
zichun xiao, xu liu, feng hai - Wiley, 2025
The performance of lithium metal batteries is significantly affected by temperature variations, which makes it challenging for them to operate across a wide range. Herein, widetemperature adaption electrolyte proposed, enabling excellent electrochemical from 40 C 60 C. Large, 5.8 Ah pouch cells employing such an achieve high energy density 503.3 Wh kg1 at 25 with lifespan 260 cycles and outstanding 339 critical role the solid interphase (SEI) in determining temperaturedependent unveiled. It demonstrated that LiFrich, anionderived SEI facilitates Li+ diffusion SEI. Moreover, accelerated desolvation observed. These two aspects promote kinetics anodes further inhibit dendrite growth low temperatures. This work showcases importance understating chemistry enable batteries.
11. Carbon-Composite Silicon-Based Nanostructures with Variable Aspect Ratios for Lithium-Ion Battery Anodes
ONED MATERIAL INC, 2025
Nanostructured materials for improved lithium-ion battery anodes. The materials are carbon-comprising, silicon-based nanostructures like nanowires, nanoparticles, or nanostructures on a carbon substrate. These nanostructures have desirable properties like high capacity, fast charging, and cycling stability compared to bulk silicon. They can be added to battery slurries at low weight percentages to replace some graphite. The nanostructures can also have carbon coatings to further enhance performance. The nanostructures are suitable for high aspect ratio silicon nanowires with diameters below 500 nm and lengths below 50 microns.
12. Method for Producing Tungsten-Coated Lithium-Nickel Oxide Cathodes via Moderate Temperature Mixing and Heat Treatment
SUMITOMO METAL MINING CO LTD, 2025
Method to produce high capacity and high output lithium-ion battery cathodes using lithium-nickel oxide. The method involves mixing lithium-nickel oxide with tungsten oxide powder at moderate temperatures (30-65°C) while adding enough water to disperse the tungsten. This creates a tungsten-coated lithium-nickel oxide powder. Heat treating this powder forms lithium-tungsten compounds on the lithium-nickel oxide surface. This tungsten coating improves battery capacity and reduces resistance compared to uncoated lithium-nickel oxide.
13. Battery Electrode Plate with Controlled Pore Distribution and Specific Solid Electrolyte Mass Fraction
DONGGUAN AMPEREX TECHNOLOGY LTD, 2025
Battery electrode plate design for improved lithium-ion battery performance by controlling pore distribution. The electrode plate has a specific ratio of pore sizes in the active material and solid electrolyte particles. The active material pores are larger and fewer, while the solid electrolyte has smaller pores. This reduces closed holes and allows more effective lithium-ion transport paths. The electrode plate composition has a solid electrolyte mass fraction of 0.3-5% and matching particle sizes with the active material.
14. Anode Material with Controlled Crystallization Instability and Two-Step Sintering for Lithium-Ion Batteries
DINGYUAN NEW ENERGY TECHNOLOGY CO LTD, BTR NEW MATERIAL GROUP CO LTD, 2025
Anode material and battery with improved cycling stability, capacity, and expansion for lithium-ion batteries. The anode material has controlled crystallization instability to reduce grain boundary energy, stress concentration, and expansion. It involves a two-step sintering process followed by carbon coating. The first sintering reduces grain size by limiting growth. The second sintering disproportionates silicon oxide to further reduce grain size. Carbon coating fills pores and surfaces to improve conductivity and relieve expansion. The controlled crystallization instability degree of 0.01-500 improves cycling performance.
15. Electrolyte Composition with Iodine and Fluorosilicate Additives for Enhanced Solid Electrolyte Interphase Stability in Metal-Ion Batteries
SILA NANOTECHNOLOGIES INC, 2025
Electrolytes for metal-ion batteries like lithium-ion batteries that improve stability and performance of high capacity electrodes like silicon anodes. The electrolytes contain additives like iodine, iodine-containing salts, and fluorosilicates to enhance solid electrolyte interphase (SEI) stability and Coulombic efficiency (CE). These additives reduce solvent permeation, improve mechanical properties, and facilitate lithium transport through the SEI. They also reduce dendrite growth on lithium metal anodes. The electrolytes can contain multiple salts like lithium salts, alkaline earth salts, and fluorosilicates. The total concentration of additives is optimized for performance.
16. Method for Manufacturing Lithium Secondary Batteries with Controlled Activation Under Pressurization Conditions
LG ENERGY SOLUTION LTD, 2025
Manufacturing lithium secondary batteries with enhanced capacity retention and reduced gas generation through controlled activation. The method employs constant current charging until the charge cut-off voltage, followed by constant voltage charging. This approach prevents premature activation of the lithium-rich manganese-based oxide (LiMn2O3) phase during activation, which typically leads to abnormal capacity behavior and gas generation. The activation process is performed under pressurization conditions to minimize non-activated Li2MnO3 phase formation and prevent lithium precipitation.
17. Electric Vehicle Battery System with Dual Offset Side Housings
KUBOTA CORP, 2025
Layout of a battery system in an electric vehicle to increase storage capacity without sacrificing space inside the main cabin. The vehicle has two battery housings, one on each side of the vehicle, that overlap and are offset in the front-rear direction. This allows more batteries to be housed outside the cabin compared to just having a single battery pack under the seat. It also provides some visual benefits by improving forward visibility for the driver due to the front-rear offset and angled upper housing.
18. Rechargeable Lithium Battery Positive Electrode with Mixed Particle Size Nickel-Based Lithium Oxide Composition
SAMSUNG SDI CO LTD, 2025
Rechargeable lithium battery with improved cycle life and capacity by using a specific composition of particle sizes in the positive electrode. The electrode contains small 1-8 um monolithic particles and larger 10-20 um secondary particles, both containing nickel-based lithium oxide. This mixture with a density over 3.4 g/cc has an X-ray diffraction peak intensity ratio over 3. It provides high capacity and cycle life by reducing side reactions, improving efficiency and temperature stability.
19. Silicon Carbon Composite with Specific 29Si NMR Peak Intensity Ratios for Negative Electrodes
LG ENERGY SOLUTION LTD, 2025
Silicon carbon composite for high-performance negative electrodes in lithium-ion batteries. The composite has a specific ratio of peak intensities in a 29Si NMR spectrum. The ratio is 1.3-4, where peaks A, B, and C represent chemical shifts of 20-15 ppm, -20 to -100 ppm, and -110 to -140 ppm, respectively. The composite is formed by heat treating silicon oxide, etching, pulverizing, and reacting with carbon. This composition provides improved capacity, efficiency, and water-based processability compared to silicon-carbon composites without the specific NMR peak ratio.
20. Battery Architecture with Open Cell Design and Electrolyte-Mediated Metal-Air Electrode Separation
FORM ENERGY INC, 2025
Battery architecture for long duration energy storage (LODES) applications that allows operation at high capacity and low self-discharge rates. The batteries have open cell designs where the electrolyte separates the metal and air electrodes. This prevents direct contact between the metal and oxygen in sealed batteries. The electrolyte also has low oxygen solubility and carbonate levels. This prevents parasitic discharge of the metal electrode and oxygen barrier. The metal electrode can be submerged or removed from the electrolyte using pumps, bladders, or lifts to balance capacity and self-discharge.
Get Full Report
Access our comprehensive collection of 172 documents related to this technology
Identify Key Areas of Innovation in 2025
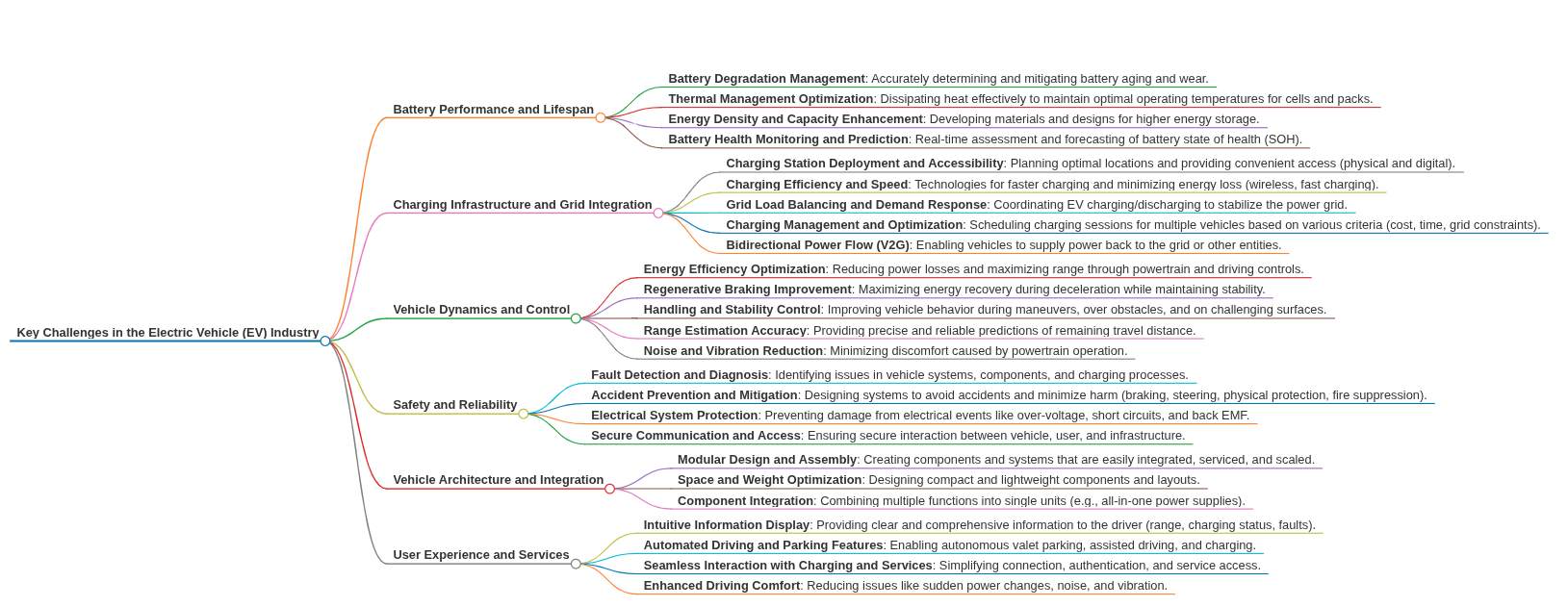