Active Cooling Techniques for EV Battery Protection
Electric vehicle batteries generate substantial heat during charging and discharge cycles, with cell temperatures routinely reaching 45-50°C under high load conditions. Managing this thermal load is critical, as every 10°C increase above optimal operating temperature can reduce battery life by 50% while also impacting charging speeds and power delivery.
The fundamental challenge lies in balancing cooling system efficiency against the added weight, complexity, and energy consumption of thermal management components.
This page brings together solutions from recent research—including direct liquid cooling interfaces, thermoelectric cooling arrays, counter-flow cold plates, and dynamic thermal conductivity materials. These and other approaches focus on achieving uniform temperature distribution across battery packs while minimizing parasitic energy losses from cooling systems.
1. A Correlational Study on Architectural Design and Thermal Distribution Patterns Using a Novel Multi-Terminal Approach in Cylindrical Li-Ion Cell-Integrated Battery Packs
d sagar, raja ramar, shama ravichandran - Multidisciplinary Digital Publishing Institute, 2025
A novel architectural design is proposed to mitigate uneven thermal distribution, peak temperature, and heat spot generation, which are common issues that observed in conventional battery packs. This approach features a multi-terminal configuration, incorporating modified pack structure along with switching algorithm identifies the optimal terminal for current flow load. In design, first second terminals placed at fourth series string while divided into four regions, each corresponding one string. Additionally, points represent zones level. Experiments were conducted evaluate performance of dual-terminal mechanism three configurations1S, 2S, 3S. The 1S setup outperformed single-terminal achieving 6.23% improvement reducing zone temperature difference (Pz). 2S configuration demonstrated an 11.11% improvement, 3S achieved region (Pr) >50%, without cooling system. Finally, forced air effectively lowers it insufficient addressing distribution formation. However, integrating enables effective control management all critical parameterspeak generation.
2. Thermophysical and Chemical Properties of Nano-Additives in Phase Change Materials for Enhanced Heat Transfer
padmavathi vustelamuri, rajesh s hajare, 2025
The enhancement of phase change materials (PCMs) through the incorporation nano-additives presents a promising approach to overcome intrinsic limitations in thermal conductivity and energy storage capacity, thereby advancing management technologies. This chapter provides comprehensive analysis thermophysical chemical properties various nanoparticles their synergistic interactions within PCM matrices. Emphasis is placed on role nanoparticle morphology, size distribution, surface functionalization optimizing heat transfer efficiency transition dynamics. critical evaluation dispersion stability long-term performance under cyclic conditions discussed. Environmental safety considerations, alongside evolving regulatory frameworks, are examined address sustainable integration nano-enhanced PCMs into practical applications. also highlights emerging algorithmic pedagogical strategies monitor, manage, mitigate potential ecological occupational risks. By bridging material science, environmental stewardship, policy development, this work establishes holistic foundation for future design deployme... Read More
3. Optimization and Key Factor Analysis of Immersion Cooling Performance for 18650 Lithium-Ion Batteries in a Serpentine Channel Based on Response Surface Methodology
zhenxing li, z fu, ruoyu huang, 2025
Efficient thermal management of lithium-ion batteries is crucial for electric vehicle safety and performance. This study investigates immersion cooling in serpentine channels 18650 batteries, aiming to identify key factors affecting maximum battery temperature (Tmax) pump power (Pw). A Box-Behnken experimental design implemented with Computational Fluid Dynamics simulations analyze responses Tmax Pw. Five variables are defined: partition length (Lp), charging/discharging rate (Crate), coolant volumetric flow (V), inlet (Tin) ambient (Tamb). Statistical significance evaluated via Analysis Variance. The results show that: Tin dominated Tmax, followed by Crate, V, Lp. Significant interactions (VTin VTamb) observed. For Pw, V V extreme significance, while Lp effects were minor. Interaction LpV was significant but secondary. After optimization minimize Tave the optimal values Lp, Tin, Tamb determined be 89.5 mm, 1.08 C, 0.51 LPM, 20 C, 25.62C respectively. corresponding optimized are: = 22.87C, 21.67C, Pw 0.279 mW. Optimal requires prioritizing control suppression regulati... Read More
4. Non‐Destructive Monitoring of Internal Temperature Distribution in Prismatic Li‐Ion Battery Cells with Ultrasound Tomography
shengyuan zhang, peng zuo, zheng fan - Wiley, 2025
Abstract Large prismatic cells are increasingly being used as the primary power source in transportation applications. Effective online thermal management of these is crucial for ensuring safety and maximizing performance. However, significant discrepancies between surface internal temperatures make it difficult to detect anomalies promptly, which hinders effective increases risk irreversible hazards. This paper introduces an innovative technology Liion batteries. By exploiting temperature sensitivity ultrasound velocity applying tomographic reconstruction based on surrounding measurements, enables detailed crosssectional imaging. allows nondestructive, realtime visualization temperatures. Furthermore, with its compact design costeffectiveness, this suitable insitu deployment, offering a precise feedback mechanism management. Demonstrations conducted during continuous discharging scenarios have shown that system can identify hightemperature regions near tabs remain undetected by thermocouples. advancement has potential significantly reduce fires or explosions whi... Read More
5. Novel hybrid vehicle battery cooling system: Integrating Peltier-based heat sinks for control of thermal management
h n sharma, gaurav saxena, ravindra randa - SAGE Publishing, 2025
This study presents an experimental investigation of a novel hybrid battery thermal management system (BTMS) that integrates solenoid-actuated Peltier-based heat sink with CuO/ethylene glycol (EG) nanofluid coolant loop. The delivers on-demand cooling through time-controlled thermoelectric operation, enhancing temperature regulation during surges. Experiments were conducted CuO nanoparticle concentrations ranging from 0.5% to 2.0% (vol.) and flow rates 1 5 LPM, at inlet 50C ambient 26C. Performance metrics such as drop, transfer rate, overall coefficient analyzed. Results showed maximum enhancement 40.63% (tube-side) 38.64% (air-side) CuO. Compared conventional liquid system, the setup demonstrated 7.01% higher rate improved variation control (up 28.53%). Life Cycle Cost (LCC) analysis demonstrates 25%30% reduction in long-term costs 36% life extension, supporting systems economic viability. scalable, energy-efficient BTMS offers promising solution for advanced electric vehicles requiring high-precision control.
6. Thermosiphon Cooling System with Vapor Phase Temperature Control and Adjustable Refrigerant Temperature for Electric Vehicle Battery Packs
TOYOTA JIDOSHA KABUSHIKI KAISHA, 2025
Battery cooling system for electric vehicles that prevents delays in cooling the battery pack when switching from cold to hot environments. The system uses a thermosiphon cooling circuit with condensers and coolers. If circulation stops due to liquid filling the circuit, it enters a vapor phase temperature rise control mode. This raises the condenser temperature to lower the liquid level, allowing circulation to restart sooner than waiting for natural evaporation. It also uses higher target refrigerant temperatures during circulation restart to further lower liquid levels. This prevents the condenser and coolers from fully filling with liquid when switching environments.
7. Thermal Management Systems for Lithium-Ion Batteries for Electric Vehicles: A Review
kenia yadira gomez diaz, susana estefany de leon aldaco, j aguayo - Multidisciplinary Digital Publishing Institute, 2025
Recently, electric vehicles (EVs) have proven to be a practical option for lowering greenhouse gas emissions and reducing reliance on fossil fuels. Lithium-ion batteries, at the core of this innovation, require efficient thermal management ensure optimal performance, safety, durability. This article reviews current scientific studies controlling temperature lithium-ion batteries used in vehicles. Several cooling strategies are discussed, including air cooling, liquid use phase change materials (PCMs), hybrids that combine these three types with primary objective enhancing performance batteries. Additionally, challenges proposed solutions battery pack design energy methodologies explored. As demand increases, improving systems (BTMSs) is becoming increasingly important. Implementing developing better BTMSs will help increase autonomy safety long term.
8. Thermal Management System with Integrated Glycol and Refrigerant Loops and Configurable Valve Network
FORD GLOBAL TECHNOLOGIES LLC, 2025
A thermal management system for electrified vehicles that efficiently manages heating and cooling of the battery and cabin using a combination of a glycol system and a refrigeration system. The system has valves to connect and isolate loops for the battery, power electronics, radiator, and cabin heating. By separating components of similar operating temperatures and allowing heat transfer between them, it reduces energy consumption and hardware compared to a single system. The glycol system actively heats the cabin, while the refrigerant system actively chills the battery and power electronics. Valve configurations allow optimization under different vehicle conditions.
9. Battery Module with Horizontal Cooling Plate and Adhesive-Bonded Pouch Cells
LG ENERGY SOLUTION LTD, 2025
Battery module design for electric vehicles that improves cooling efficiency, reduces weight, and simplifies assembly compared to conventional battery packs. The module uses a horizontal cooling plate below and thermally conductive adhesive to bond pouch-type secondary batteries. This direct contact cooling provides better heat transfer than stacked cartridges. The adhesive secures the batteries without fasteners or cartridges. The design reduces module size and weight by eliminating cartridges and fasteners. It also allows closer battery spacing for improved cooling. The adhesive bonding ensures stable battery positioning without cartridge movement issues.
10. Thermal Regulation Device with Condensation Wall Featuring Relief Structures and Microscopic Channels for Dielectric Fluid Management
VALEO SYSTEMES THERMIQUES, 2025
Thermal regulation device for electronic components like batteries that overheat during charging or operation. The device has a housing with a condensation wall that promotes condensation of a dielectric fluid sprayed onto the component. The condensation wall has relief features to increase surface area for condensation and microscopic channels to aid liquid evacuation. This allows efficient cooling as the dielectric fluid vaporizes on the hot component and condenses back on the wall.
11. A Comparative Analysis of Thermal Runaway Predictions Across Lithium-Ion Battery Chemistries Used in Electric Vehicles
abhishek verma, ajay kumar pathania - International Journal for Multidisciplinary Research (IJFMR), 2025
Thermal runaway remains a critical safety challenge for lithium-ion batteries (LiBs) used in electric vehicles (EVs), with varying characteristics across different chemistries. This study presents comparative analysis of thermal predictions five widely LiB chemistries: Nickel Manganese Cobalt (NMC), Aluminum (NCA), Lithium Iron Phosphate (LFP), Oxide (LMO), and Titanate (LTO). A hybrid methodology combining controlled experimental abuse tests advanced physics-based machine learning models was employed to predict onset temperatures propagation behavior. Results reveal significant differences stability prediction accuracy among chemistries, LFP LTO exhibiting higher more reliable model predictions, whereas NMC NCA showed earlier rapid temperature escalation. These findings have direct implications battery management system (BMS) design protocols EVs, emphasizing chemistry-specific thresholds response strategies.
12. Influence of ambient temperature, discharge C‐rate, and convective heat transfer coefficient on thermal behaviour of lithium‐ion battery pack: A numerical study
ugur morali - Wiley, 2025
Abstract Lithiumion batteries play a crucial role in reducing carbon emissions and promoting the use of electric vehicles. There are numerous input variables influencing thermal profile lithiumion batteries. Therefore, precise assessment relative contributions various factors is essential for optimizing management control processes. In this study, we tested battery pack composed five 14.6 Ah prismatic cells connected series under different discharge rates (2C, 3C, 4C, 5C), ambient temperatures (30, 35, 40, 45C), convective heat transfer coefficients (5, 10, 20, 40 ). Results showed that temperature with contribution 58.01% had strong influence on maximum temperature. Furthermore, influences Crate coefficient were identical. Moreover, it was found homogeneousness very sensitive to Crate, contributing 71.07% increase difference. To ensure uniformity at same time, moderate temperatures, low Crates, high can be preferred. Consequently, statistically obtained results study may contribute towards performance optimization improved safety packs.
13. Integrated Thermal Management System with Shared Coolant Loop and Multi-Circuit Configuration for Electric Vehicles
HYUNDAI MOTOR CO, 2025
Integrated thermal management system for electric vehicles like purpose-built vehicles (PBVs) that can efficiently heat and cool the battery, power electronics, and cabin based on exterior temperature. The system uses a shared coolant loop with multiple circuits. The circuits branch from a reservoir, circulate through heat exchangers and radiators, and converge back. Compressor, pumps, valves, and accumulator are used. Modes are selected to optimize energy consumption and reach temperature goals.
14. Heat Pump System with Parallel Heating and Cooling Loops for Battery Electric Vehicles
HANON SYSTEMS, 2025
Heat pump system for battery electric vehicles that provides efficient heating and cooling for the cabin and battery. The system uses a heat pump with parallel cooling and heating loops. The main refrigerant loop cools the cabin using an external heat exchanger. Parallel loops draw heat from the battery and drive train. In cooling mode, the battery and drive train loops are bypassed. In heating mode, the battery and drive train loops are active. This allows efficient heating from ambient air, battery, and drive train sources. The parallel loops reduce pressure drop compared to serially connecting all heat sources.
15. Battery Thermal Management System with Zoned Temperature Control Using Independent Flow Circuits and Valves
FORD GLOBAL TECHNOLOGIES LLC, 2025
Thermal management system for electric vehicle batteries that allows individual cooling or heating of different zones within the battery to optimize performance and lifespan. The system uses multiple distinct circuits, each associated with a cooling zone, with independent flow control valves. A controller ranks the zones by temperature and adjusts the valves to balance cooling and heating based on the hottest and coldest zones. This provides customized cooling/heating to prevent hot spots and improve overall battery temperature management.
16. Stacked Perforated Separator Plates with Interconnected Zigzag Coolant Channels for Liquid Immersion Cooling of Battery Packs
GM GLOBAL TECHNOLOGY OPERATIONS LLC, 2025
Liquid immersion cooling (LIC) system for battery packs that uses stacked perforated separator plates between cell rows to distribute coolant fluid vertically upward between the cells. The separator plates have interconnected coolant channels with angled grooves on one plate aligned with opposite angled grooves on the other plate. This zigzag channel pattern creates a pressure differential that forces coolant to flow vertically between the cells. The perforated plates with angled channels stacked between cell rows improve LIC cooling by distributing the coolant fluid over and between the cells.
17. Injection Valve for Lithium-Ion Battery Packs with Pressure-Activated Opening Mechanism
CONTEMPORARY AMPEREX TECHNOLOGY LTD, 2025
Valve for lithium-ion battery packs that allows fire-fighting medium to be injected into the pack during thermal runaway to extinguish internal fires. The valve has a closing member that seals an injection port. When pack pressure/temperature exceeds a threshold, the closing member opens the port for medium injection. This allows an external fire suppression system to deliver cooling agent into the pack to quench cell fires. The valve is mounted on the pack enclosure and connected to a fire-fighting device.
18. Energy Sources and Thermal Management Technologies for Electric Vehicle Batteries: A Technical Review
md atiqur rahman, g madhusudan reddy, rajeshwari chatterjee - Wiley, 2025
Abstract Efficient thermal management of highpower lithiumion batteries (LiBs) is critical for ensuring safety, longevity, and performance in electric vehicles (EVs). Battery systems (BTMS) play a crucial role regulating temperature, as LiBs are highly sensitive to fluctuations. Excessive heat generation during charging discharging can degrade battery performance, reduce lifespan, pose safety risks. Traditional cooling methods, such air liquid cooling, often require additional power complex components, making them less effective highenergydensity batteries. As result, recent advancements focus on immersion, indirect, hybrid solutions. Among these, phase change material (PCM)based BTMS has emerged promising passive approach. PCMs efficiently absorb store heat, maintaining optimal temperature without external power. Their further enhanced by integrating expanded graphite (EG) fillers, metal foams, or fins, improving dissipation. This review examines progress (20192024) technologies, with particular PCM applications fastcharging conditions. It also discusses under e... Read More
19. Advances in the Battery Thermal Management Systems of Electric Vehicles for Thermal Runaway Prevention and Suppression
le duc tai, mooyeon lee - Multidisciplinary Digital Publishing Institute, 2025
In response to the global imperative reduce greenhouse gas emissions and fossil fuel dependency, electric vehicles (EVs) have emerged as a sustainable transportation alternative, primarily utilizing lithium-ion batteries (LIBs) due their high energy density efficiency. However, LIBs are highly sensitive temperature fluctuations, significantly affecting performance, lifespan, safety. One of most critical threats safe operation is thermal runaway (TR), an uncontrollable exothermic process that can lead catastrophic failure under abusive conditions. Moreover, propagation (TRP) rapidly spread failures across battery cells, intensifying safety threats. To address these challenges, developing advanced management systems (BTMS) essential ensure optimal control suppress TR TRP within LIB modules. This review systematically evaluates cooling strategies, including indirect liquid cooling, water mist immersion phase change material (PCM) hybrid based on latest studies published between 2020 2025. The highlights mechanisms, effectiveness, practical considerations for preventing initiation suppre... Read More
20. Design of Dielectric Fluid Immersion Cooling System for Efficient Thermal Management of Lithium‐Ion Battery Packs
s hemavathi, d a antopaul - Wiley, 2025
ABSTRACT Heat generation during fast charging and discharging of lithiumion batteries (LIBs) remains a significant challenge, potentially leading to overheating, reduced performance, or thermal runaway. Traditional battery management systems (BTMS), such as airbased cooling indirect liquid using cold plates, often result in high gradientsboth vertically within cells horizontally across packsespecially under highcurrent discharge rates. To address these issues, this study introduces evaluates steadystate convectionbased esteroil immersion (EOIC) technique for LIBs. Numerical simulations based on the Newman, Tiedemann, Gu Kim model, aligned with multiscale multidimensional principles, were performed both single 18650 cylindrical cell 4S2P pack. Experimental validations conducted 2C 3C rates at 25C ambient temperature. The EOIC system demonstrated temperature reduction up 13C 15C pack compared natural air convection achieved 10C gradient simulation results closely matched experimental data, maximum deviation only 2C, confirming model's reliabi... Read More
Get Full Report
Access our comprehensive collection of 301 documents related to this technology
Identify Key Areas of Innovation in 2025
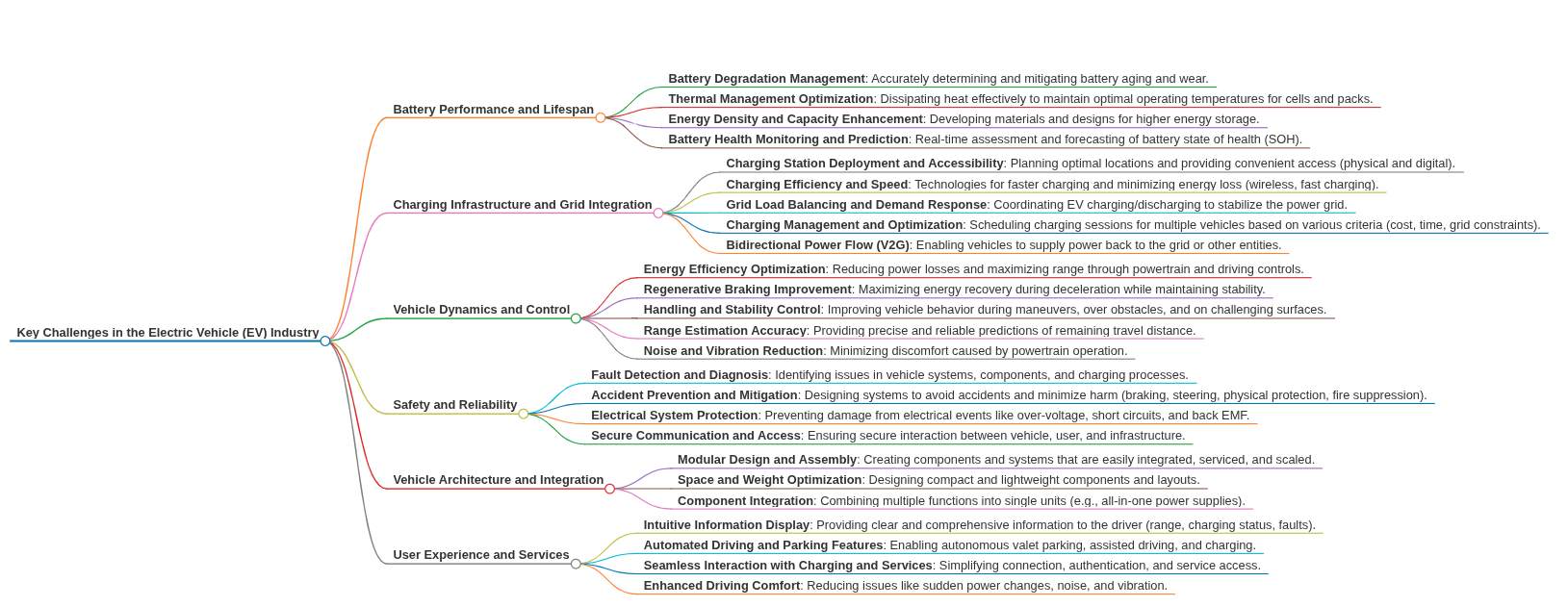