Immersion Cooling for EV Battery Thermal Management
Electric vehicle battery packs operating at high discharge rates can generate heat loads exceeding 2.5 kW/m², with cell temperatures rising above 45°C during rapid charging. Traditional cooling methods, relying on indirect heat transfer through cooling plates or air channels, struggle to maintain uniform temperatures across densely packed cells.
The fundamental challenge lies in achieving complete thermal contact with cell surfaces while maintaining electrical isolation and system reliability in a vehicle environment.
This page brings together solutions from recent research—including metal-capped pouch cell designs with integrated exhaust systems, glycol-based coolant configurations with hermetic sealing, and flow path optimization for temperature uniformity. These and other approaches focus on practical implementation while addressing both thermal management and safety requirements for next-generation EV batteries.
TABLE OF CONTENTS
1. Coolant Chemistry, Expansion Management, and Pump Redundancy
Any immersion program starts with the fluid itself. The low-viscosity oleaginous dielectric resolves the long-standing conflict between thermal conductivity and electrical isolation that plagues water-glycol or silicone oils. By fixing viscosity in the 0.7–7 cSt range at 100 °C, holding the flash point comfortably above 50 °C, and keeping the pour point well below winter fast-charge temperatures, the oil remains pumpable while guarding against short circuits. Once fully flooded, the pack must absorb fluid expansion without jeopardising seal integrity. The expansion-tank–equipped immersion cabinet addresses that head-space problem with a dedicated reservoir tied to the main bath through a fill port; volumetric growth during hard acceleration or rapid DC charging is taken up in the tank rather than across O-rings. Agitation vanes inside the bath keep stratification below 5 °C so uniformity is preserved even when the fluid dilates.
Because the enclosure is now hermetic, coolant motion cannot depend on a single actuator. The fault-tolerant multi-pump architecture arrays at least two pumps around common storage tanks and connects them through fast-acting multi-port valves. If one pump stalls or a tank sensor faults, the controller cross-ties the remaining equipment in milliseconds; flow never ceases, and the pack remains within its 0–60 °C window. With the chemistry, expansion control, and redundancy pillars in place, designers can shift focus to how the fluid circulates through the cells.
2. Closed-Loop Dielectric Immersion Circulation Architectures
The first tier of hardware is the single-module loop. In the flow-rate-adaptive immersion module a variable-speed pump reacts linearly to temperature feedback, adding roughly 1–5 L min⁻¹ for every degree above set-point. A liquid plate welded to the vessel wall sends heat to the vehicle glycol loop, yet pump energy stays low because speed matches demand.
Scaling to multi-module packs introduces routing challenges. The diagonal cross-flow immersion case paired with its self-balancing recirculation manifold threads a single dielectric circuit through several rectangular housings. Coolant enters one corner and exits the opposite, sweeping every cell face before recombining with the main stream. Engineers can place cases in series for higher velocity or in parallel for lower inlet temperature and may even share the same insulated liquid with power electronics or the e-axle.
Where heat-flux density climbs further, the integrated pump-heat-exchanger pack merges pump, immersion cavity, and secondary coolant ports into one casting; pressure drop shrinks because remote hoses disappear. Thin conduction plates pierce the wall, creating a parallel path to ambient air or the vehicle loop, while internal fins steer liquid through densely stacked cells. At the opposite extreme, the module-level swirl pump cooler embeds miniature impellers inside each sealed case; circulation wakes only when on-board sensors flag a hot spot, so standby power is virtually nil. Surplus heat from either architecture can be handed off to a coil-assisted immersion assembly that wraps chilled water tubing around the module cluster. Together these layouts form the core catalogue of closed-loop immersion circulation solutions.
3. Flow Distribution and Turbulence Enhancement
Uniform delivery of liquid at the same enthalpy is the next lever. One route uses structural members as plumbing. The engineered gap-spray coolant circuit pours jets through tray ports positioned between modules, scrubbing shadow zones that would otherwise cook under fast charge. A companion idea, the 3-D side-beam flow lattice, drives coolant inside hollow longitudinal beams, across partition plates that snake between cells, and back through tapered outlets that equalise pressure. Where long prismatic stacks suffer head-to-tail rise, the multi-cavity vertical feed plate rains coolant downward through perforations, trimming path length and evening ΔT.
Once fluid reaches every surface, heat-transfer coefficients can be raised further by disturbing boundary layers. The inner-wall vortex generator array carves clearance pockets that spawn energetic eddies. The reciprocating turbulence fin system pushes the concept to active agitation: a gear-driven fin swings through the bath, knocking down laminar films during high power events. Inside discrete heat sinks, the multi-pass turbulence structure splits channels so velocity peaks near the hottest fin bases without an excessive pressure penalty.
Flow can even be budgeted module by module. In the module-isolated immersion loop a smart valve in each runner throttles local supply to erase pack-level gradients. Between neighbouring cells, a pressure-equalising inter-cell conduit made from a compressible pad cut with through-channels enlarges effective area while damping mechanical stress. Combined, these distribution and turbulence tools confine cell-to-cell spread to single-digit Celsius values under the most aggressive drive cycles.
4. Partial and Indirect Immersion Variants
When packaging leaves little room for a full bath, partial submersion offers a compromise. The inner partition wall with cell apertures divides each module into a dry upper chamber and a wet lower chamber. Machined holes let the bottom of every cell dip into coolant while terminals remain dry; convection thus extracts heat over the largest surface without exposing sensitive electronics. The integrated immersion tray implements the same logic at assembly level: a shallow pan seals to the module perimeter so only the cell bottoms are immersed. Both schemes remove external cold plates and hoses while preserving energy density.
A different path minimises fluid volume by restricting liquid to thin films. Hollow inter-cell heat-conducting sheets sandwich metallic channels between adjacently packed 18650 cells; a film only a few tenths of a millimetre thick flows from manifold to manifold, yet ΔT stays within 5 °C at 25–40 °C bulk.
Indirect immersion takes the idea further by inserting conductive barriers. In the heat-conduction groove architecture every cell sits in a metal channel bathed externally in coolant; electrolyte never touches the fluid so compatibility worries fade and damaged cells can be swapped without draining the bath. Heavy-duty packs adopt a sealed fluid thermal bus integrated into the base plate; coolant spreads laterally beneath the array while through-holes vent abuse gases upward. For stationary installations, the composite conduction-insulation stack presses cells against a liquid-cooled plate yet cloaks each lateral spreader in an insulating film, marrying high extraction with electrical isolation.
5. Thermal Runaway Mitigation and Compartmentalisation
High-power packs risk chain reactions unless both heat and combustion products are removed quickly. The integrated gas-extraction manifold encloses every pouch in a thin metal can that routes an exhaust port into a common header; dielectric fluid removes steady-state heat while the header vents 600 °C gas jets before they permeate the bath.
Uniform coolant distribution also guards against runaway propagation. The flow-diverting upper cover and partition-beam architecture splits the battery box into liquid chambers sized for individual modules. A calibrated gap beneath the lid forces incoming fluid to sweep laterally over each array, eliminating long conduction paths seen in cold-plate packs. Continuous de-ionisation and live conductivity monitoring keep the fluid an electrical insulator despite full submersion. The joint effect of dedicated exhaust, partition walls, and conditioned coolant lowers propagation probability without adding bulky shields.
6. System-Level Integration: CTC, Modular Bricks, and Swappable Packs
Cell-to-chassis (CTC) designs compress thousands of cells into the floorpan, leaving no room for traditional cold plates. The chassis-level immersion bath fills the cavity beneath the passenger cell array with dielectric fluid; a pump switches between an external exchanger in hot weather and an integrated heater below 10 °C via a three-way valve. Guide plates keep velocity uniform, so near-isothermal conditions survive cornering loads and fast charge events.
For platforms that must scale from city cars to delivery vans, the fluid-distributor plate module offers a brick approach. Each module mates contoured plate to base, and coolant channels align automatically when bricks snap together; vertical outlet placement above inlets generates a passive thermosyphon that supplements the pump. Engineers grow capacity by adding bricks yet preserve identical flow geometry.
Where batteries must be swapped quickly, as in ride-hailing scooters or fleet logistics, the multi-speed guided docking rail lets a self-contained immersion module slide onto the vehicle. Floating connectors and elastomer bumpers absorb mis-alignment; once the module is seated, external ports tie into the pack so forced circulation can resume during ultra-fast charging. Tool-free exchange cycles do not compromise leak integrity or electrical resistance.
7. Hybrid Cooling Combining Immersion, Phase Change, and Heat Pipes
For some duty cycles neither immersion nor latent storage alone suffices. The double-layer counter-flow liquid jacket inserts PCM sheets between cells and runs twin coolant loops in opposite directions, extracting heat before the PCM saturates and eliminating hot zones. A metal-plate variant, the composite PCM heat sink with spring compliance, clamps doped PCM between crimped plates; integrated springs keep contact pressure stable as cells swell. Tall packs can apply the spiral water-loop composite PCM canister which coils twin circuits around cylindrical PCM cartridges so upper and lower regions cool independently.
Full immersion can itself become phase-change capable. The solid–liquid polyurethane immersion matrix cures around cells but liquefies locally at hotspots, raising conductivity just where needed while avoiding free fluid leaks. If circulation is preferred, the circulating phase-change fluid loop disperses PCM micro-capsules in a carrier liquid; the slurry absorbs peaks, then is reheated in winter to thaw the pack.
Capillary heat pipes create parallel channels for even faster transients. The coaxial dual-channel heat pipe-PCM network wraps each cell with an inner pipe and adds an outer graphite pipe tied to PCM. Light loads rely on latent storage; high loads trigger active liquid flow in the heat pipes. Pole-dominated hotspots adopt the unidirectional pole-insert heat pipe path that sinks current-collector heat while blocking ingress from harsh ambients. Cylindrical arrays can clamp a U-shaped flat pipe that shares pulses with paraffin-graphite slugs in the arc-shaped heat spreader with integrated PCM wells.
Where still higher coefficients are needed, immersion can be allowed to boil under control. The gap-controlled boiling-contact heat-exchange plate creates a micro-gap so expanding bubbles directly impinge on an overhead plate; coefficients spike during high load yet the surface stays dry under nominal operation. These hybrids knit together passive stability and active burst capacity in a single envelope.
8. Indirect Plates and Heat Pipe Benchmarks
Immersion is not always feasible, so indirect solutions remain vital references. Heat pipes offer pump-free conduction. The dual-stage heat-pipe architecture combines an internal pipe, a reversible Peltier element, and an external fan loop; polarity flips in winter so the same stack both heats and cools. Planar stacks may prefer the layered flat heat pipe with micro-pyramidal evaporators that places the phase change millimetres from the cell wall, while cylindrical modules can adopt the passive pulsating heat pipe sleeve whose serpentine capillary self-oscillates fluid toward a remote channel.
Cold plates stay the industrial workhorse. The variable-geometry aluminum cold plate thickens gradually downstream so area grows as temperature head shrinks, keeping ΔT within 5 °C. A similar effect comes from the funnel-shaped thermal interface which widens channels toward the outlet. Tight prismatic stacks may embed the parallel side-wall channel module that builds Z-headers into the frame and bridges with thin gaskets.
Hot-spot countermeasures refine these plates further. The fin-enhanced cell connector heat sinks turn busbars into ribbed radiators cooled by insulated liquid lines, while the electrically-insulated tab heat exchanger seats coolant channels directly at positive and negative tabs with ceramic walls. Removable packs can meet a refrigerant plate through a dry-coupled direct-expansion plate that avoids liquid interfaces.
Several novel concepts push beyond pumps. A magnetically-driven ferrofluid loop circulates fluid under an external field, a compliant three-sided heatsink keeps contact under swelling, and a high in-plane conductive solid-state stack spreads heat so effectively that ambient airflow suffices. Though outside immersion scope, these benchmarks quantify what immersion must beat on mass, cost, and ΔT.
Get Full Report
Access our comprehensive collection of 140 documents related to this technology
Identify Key Areas of Innovation in 2025
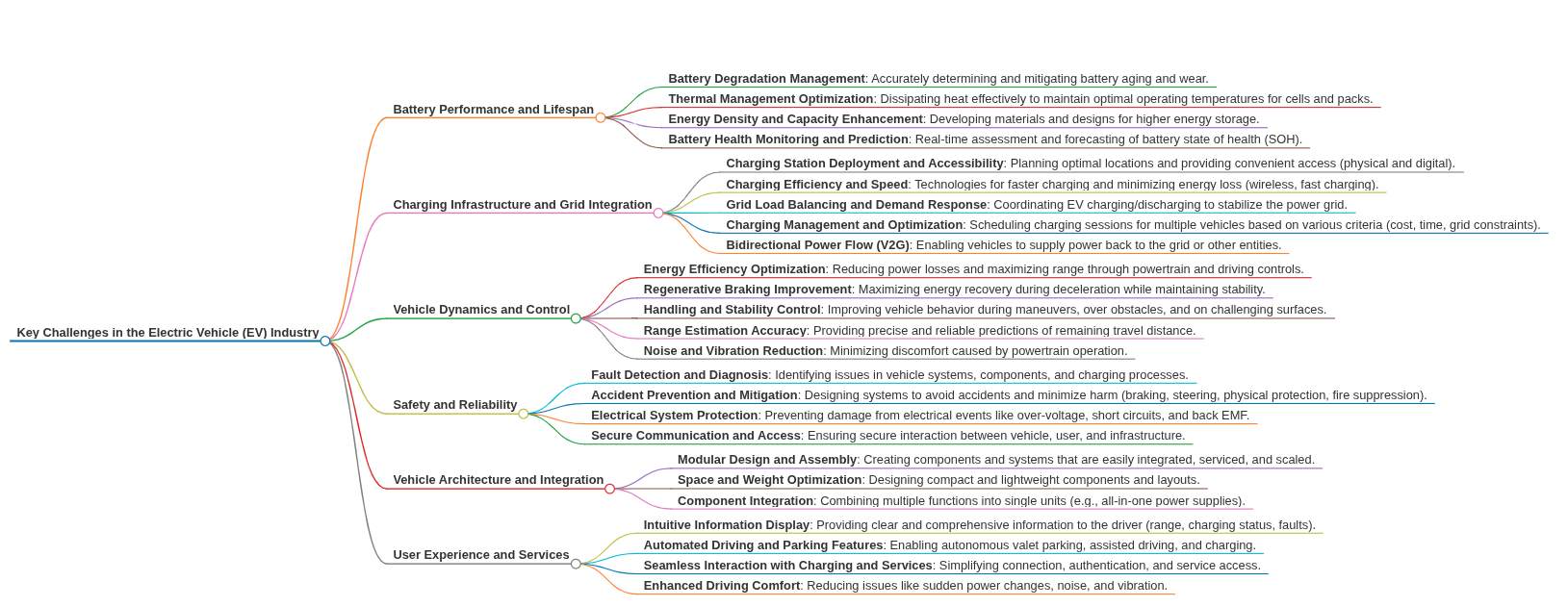