Range Prediction Improvement in Lithium Iron Phosphate for EV
Lithium iron phosphate (LFP) batteries in electric vehicles exhibit complex discharge patterns with flat voltage plateaus that make accurate state-of-charge estimation challenging. Internal measurements reveal that voltage variances can be as small as 50-100mV across 70% of the usable capacity range, while temperature fluctuations between -10°C and 45°C can alter effective capacity by up to 20%. These intrinsic characteristics, combined with variable driving conditions, create significant barriers to reliable range prediction.
The engineering challenge centers on developing predictive models that can overcome LFP's inherently flat voltage curve while accounting for the complex interplay between temperature, current draw, and cell-to-cell variations.
This page brings together solutions from recent research—including third-order RC models with temperature-based voltage correction, deep learning predictive frameworks that leverage recurrent neural networks, pulse discharge methods for nominal state identification, and error covariance frameworks with corrected ampere-hour integration. These and other approaches demonstrate how range prediction accuracy can be substantially improved without requiring additional sensors or hardware modifications to existing battery management systems.
1. Third-Order RC Model for Lithium Iron Phosphate Battery SOC Estimation with Temperature and Current-Based Voltage Correction
WANXIANG A123 SYSTEMS CORP, 2025
Adaptive SOC estimation for lithium iron phosphate battery cells using a third-order RC model. The method calculates the average electromotive force of the battery model based on its state parameters, then uses this value to derive a correction factor for voltage estimation. The correction factor is determined by temperature and current factors, which are determined using a lookup table. The correction factor is applied to the measured voltage to estimate the battery state of charge (SOC).
2. Battery Energy Management System with Recurrent Neural Network-Based State Estimation and Dynamic Power Adjustment
HUNAN INST ENGINEERING, 2024
Intelligent control and management system for chemical battery energy storage in electric vehicles, optimizing power management through advanced state estimation and predictive analytics. The system monitors and analyzes real-time battery state, including charge and discharge cycles, balance, and health metrics, using machine learning algorithms. It employs a recurrent neural network to predict battery state and optimize charging and discharging strategies based on predicted conditions, ensuring safe and efficient energy storage and utilization. The system dynamically adjusts power management to maintain optimal battery state, including preventing over-discharge and maintaining sufficient power reserves for vehicle functions.
3. Lithium Battery Control System with Integrated Monitoring, Charge Management, and Protection Mechanisms
JIANGXI DETAI INTELLIGENT CONTROL POWER SUPPLY CO LTD, 2023
Intelligent lithium battery control system that improves performance, reliability, and safety of lithium battery packs used in electric vehicles, drones, and energy storage systems. The system monitors battery status, optimizes charge/discharge strategies, predicts battery health, manages power peaks, balances energy use, provides remote monitoring, and implements short circuit protection. Algorithmic optimization, temperature management, and data analysis enhance battery performance and longevity.
4. Lithium Iron Phosphate Battery State Estimation Using Error Covariance Framework with Corrected Ampere-Hour Integration
MARKETING SERVICE CENTER STATE GRID ZHEJIANG ELECTRIC POWER CO LTD, 2023
A lithium iron phosphate battery state estimation method that improves accuracy through correction of the traditional ampere-hour integration method. The method employs an error covariance estimation framework that incorporates both the state estimation error and the measurement noise covariance to enhance the accuracy of the battery state estimation. This correction approach enables more precise state estimation in the battery's voltage plateau region, where traditional methods may suffer from significant errors due to measurement noise and initial state inaccuracies.
5. Lithium Iron Phosphate Battery Discharge Management System with Pulse Discharge-Based Nominal State of Charge Identification
Foshan Polytechnic, FOSHAN POLYTECHNIC, 2022
A lithium iron phosphate battery discharge management system that optimizes battery life through precise control of the discharge cut-off point. The system employs a pulse discharge method to identify the battery's nominal state of charge (NSOC) by analyzing the characteristic behavior of the battery's discharge curve. By comparing the pulse discharge characteristics to established thresholds, the system determines the optimal discharge cut-off point to prevent deep discharge while maintaining battery health. This approach eliminates the need for series capacitors and enables more accurate state of charge monitoring.
6. Temperature-Adapted Lithium Battery SOC Estimation Model with Modified RC Thevenin Circuit Incorporating Shutdown Factors
NORTH CHINA ELECTRIC POWER UNIVERSITY, 2021
Power lithium battery state-of-charge (SOC) estimation model that improves accuracy through temperature adaptation and battery shutdown considerations. The model incorporates a modified RC Thevenin equivalent circuit that accounts for temperature-dependent battery characteristics, while incorporating battery shutdown factors to mitigate potential errors. This approach enables more accurate SOC predictions across varying temperatures and battery states, particularly in applications where battery management systems rely on precise SOC estimation.
7. Lithium Iron Phosphate Battery System with Cell-Level Monitoring and CAN Bus Integration
国家电网有限公司, STATE GRID CORPORATION OF CHINA, State Grid Liaoning Electric Power Co., Ltd. Jinzhou Power Supply Company, 2021
Real-time monitoring and management system for lithium iron phosphate batteries that enables comprehensive DC system control through advanced cell-level monitoring. The system comprises a battery pack with multiple cells connected in series, a monitoring management unit that includes an isolation amplifier, analog-to-digital converter (ADC), microprocessor, CAN bus, host computer, temperature sensor, control gating unit, protection unit, and voltage switch matrix. The isolation amplifier processes each cell's voltage signal, while the ADC converts it into a digital signal. The microprocessor integrates this data with cell-level current and temperature measurements, enabling precise state of charge and temperature monitoring. The CAN bus transmits this comprehensive data to the host computer, which performs real-time analysis and control.
8. Integrated System for Real-Time Monitoring and Management of Lithium Iron Phosphate Batteries with Advanced Power System Control
STATE GRID CORPORATION OF CHINA, 2021
Real-time monitoring and management of lithium iron phosphate batteries through an integrated system that combines traditional battery monitoring with advanced power system control. The system enables comprehensive monitoring of battery state of charge, voltage, and capacity, while also monitoring the DC system of the substation and detecting potential issues before they become operational problems. This integrated approach ensures safe and reliable battery operation through real-time monitoring and precise control of the DC system.
9. Adaptive Neural Network Framework with Hierarchical Wavelet Architecture for Lithium Iron Phosphate Battery Life Estimation
ZHONGSHAN POLYTECHNIC, 2017
Estimating lithium iron phosphate battery life (LOC) through adaptive neural network analysis. The method employs a scalable wavelet neural network framework that incorporates adaptive node determination to optimize network structure for accurate LOC prediction. The network architecture is built using a hierarchical approach, with each level of the network learning from previous outputs. This adaptive learning enables the network to adaptively determine the optimal number of hidden layers and parameters while maintaining high accuracy. The network is trained using input parameters related to lithium iron phosphate battery performance, enabling precise LOC estimation.
10. Battery Management System with Relay-Based Equalization and Active Balancing for Lithium Iron Phosphate Cells
STATE GRID CORPORATION OF CHINA, 2016
Lithium iron phosphate battery management system for large-scale energy storage applications that ensures consistent performance through advanced equalization and balancing techniques. The system employs a relay-based equalization circuit to maintain uniform voltage across the battery pack, while employing active balancing strategies to prevent capacity fading and self-discharge. This enables reliable operation of lithium iron phosphate batteries in high-power applications, where traditional management systems may compromise performance due to nonlinear characteristics and aging effects.
11. Dynamic RC Model for Battery State-of-Charge Estimation with Temperature and Current-Dependent Parameters Using Extended Kalman Filter
UNIV NANCHANG HANGKONG, 2015
Battery state-of-charge estimation using a dynamic RC model that incorporates comprehensive factors like temperature, current, and charge/discharge rates. The model accounts for the complex interactions between internal resistance, temperature, current, and charge/discharge characteristics, enabling accurate predictions of remaining battery capacity. The estimation is performed using an extended Kalman filter algorithm, which incorporates the state-of-charge correction factor into the estimation process.
12. Multi-Parameter State-of-Charge Forecasting Method for Lithium Iron Phosphate Batteries
上海安科瑞电源管理系统有限公司, SHANGHAI ACREL POWER MANAGEMENT SYSTEMS CO LTD, 2015
A predictive method for lithium-ion battery state-of-charge (SoC) forecasting that accurately accounts for the complex dynamics of lithium iron phosphate (LiFePO4) batteries. The method employs a multi-parameter approach that incorporates voltage, current, stability, and temperature differences across individual battery cells, along with their dynamic behavior over time. This enables precise forecasting of battery SoC levels in real-time, particularly in LiFePO4 batteries where complex interactions between voltage, current, and temperature affect charge state. The method also incorporates control measures for balancing and health management.
Get Full Report
Access our comprehensive collection of 12 documents related to this technology
Identify Key Areas of Innovation in 2025
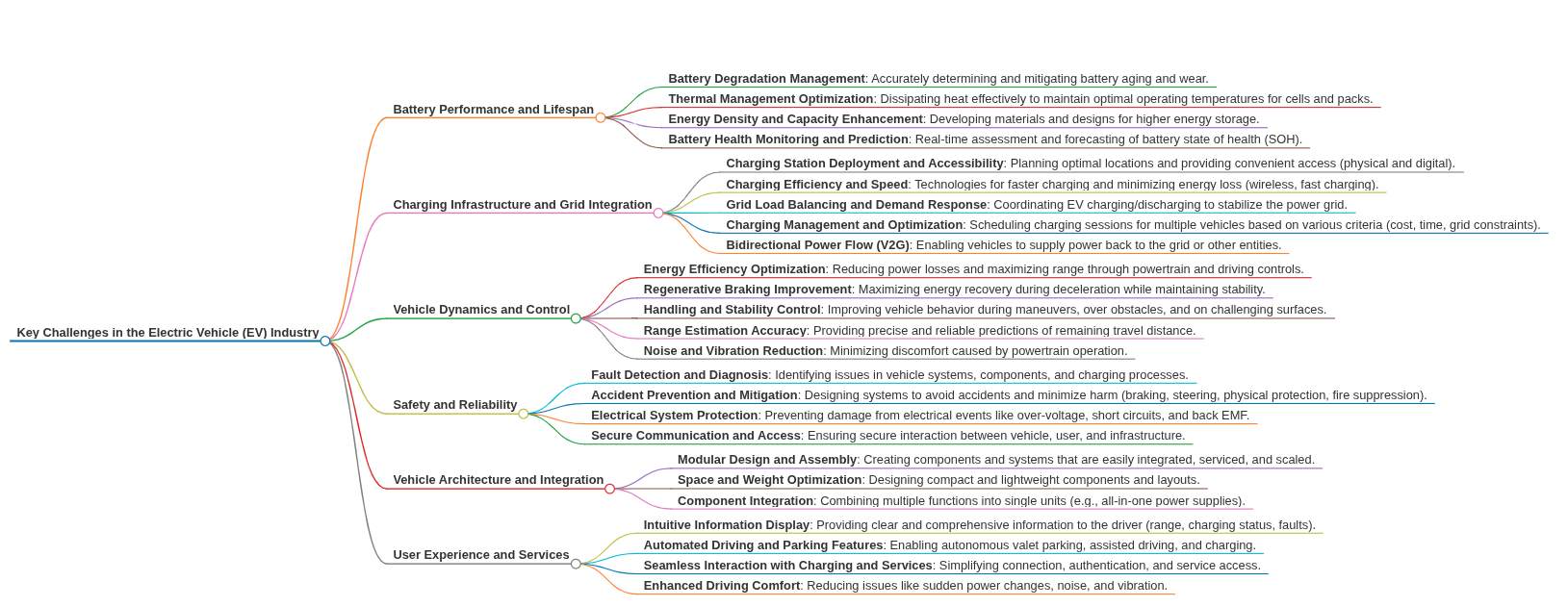