Refrigerant Based Cooling for EV Batteries
Electric vehicle battery packs generate substantial heat during operation, with cell temperatures potentially reaching 45°C during rapid charging and high-power discharge events. Managing this thermal load requires careful balance, as temperature variations as small as 5°C between cells can accelerate degradation and reduce pack lifetime.
The fundamental challenge lies in delivering uniform cooling across densely-packed cells while managing the competing demands of system weight, complexity, and thermal performance.
This page brings together solutions from recent research—including direct refrigerant cooling through microchannels, integrated dual-loop systems that share components with cabin climate control, and modular designs with individual temperature monitoring. These and other approaches focus on achieving consistent cell temperatures while minimizing system complexity and potential failure points.
TABLE OF CONTENTS
1. Direct Refrigerant Contact Cooling of Battery Cells or Modules
Effective thermal management represents one of the most significant engineering challenges in electric vehicle (EV) battery design, particularly as energy density requirements continue to increase. Conventional cooling approaches using external plates or heat sinks impose substantial penalties in terms of packaging space, weight, and system complexity. These limitations have driven the development of direct refrigerant contact cooling technologies that fundamentally reimagine the thermal interface between cooling medium and battery cells.
A novel thermal management architecture introduces direct on-cell refrigerant contact that eliminates traditional external cooling structures entirely. This system allows refrigerant to circulate directly around battery cells within a sealed aluminum casing, creating immediate thermal contact without intervening materials. The design integrates the refrigerant supply and circulation components within the pack structure itself, while using elastic pressing components to maintain mechanical stability. This approach yields multiple benefits: improved cooling efficiency through direct thermal contact, enhanced volumetric utilization by eliminating dedicated cooling structures, and reduced manufacturing complexity by decreasing component count.
The challenge of managing uneven thermal loads across battery modules has led to hybrid approaches that combine direct refrigerant contact with phase-change mechanisms. One such system employs direct liquid refrigerant cooling with heat transfer members (HTMs) strategically positioned between battery modules. These HTMs contain internal refrigerants that undergo phase change during operation, creating an effective thermal buffer that absorbs and redistributes heat through capillary action or convection. The system's architecture deliberately avoids high-density electrical regions to maintain safety while maximizing thermal contact at critical heat-generating zones. The HTMs feature variable thickness and surface area configurations based on thermal modeling of heat distribution patterns, ensuring uniform temperature regulation throughout the pack.
Bidirectional thermal management represents a further evolution in refrigerant-based battery cooling. Rather than implementing separate systems for heating and cooling functions, a bidirectional battery thermal management system integrates both capabilities into a single refrigerant loop. This system employs multi-way valves and check valves to dynamically reconfigure refrigerant flow paths, effectively functioning as a heat pump that can either deliver thermal energy to or extract it from the battery pack. The unified approach reduces component redundancy, simplifies system architecture, and improves energy efficiency across varying environmental conditions. This adaptability is particularly valuable for vehicles operating in regions with significant seasonal temperature variations, where both heating and cooling capabilities are essential for optimal battery performance.
2. Phase Change-Based Refrigerant Cooling Systems
Phase change-based refrigerant cooling leverages the latent heat of vaporization to achieve significantly higher cooling efficiency compared to single-phase systems. This approach addresses fundamental limitations in conventional cooling methods, where heat transfer is constrained by the specific heat capacity of the cooling medium and the temperature differential between the medium and battery cells.
A key innovation in this domain is the development of a cooling fin structure with an internal two-phase refrigerant flow path positioned directly between adjacent battery cells. Unlike traditional cooling systems that rely on conduction through multiple materials, this architecture creates a direct thermal pathway between cells and refrigerant. As the two-phase refrigerant enters the fin structure, it absorbs heat from the cells and undergoes vaporization within the fin itself. This direct phase-change heat absorption mechanism provides exceptional cooling capacity while maintaining a compact form factor. The refrigerant then cycles through a conventional refrigeration loop comprising a compressor, condenser, and expansion valve. The system's efficiency derives from eliminating intermediate heat transfer steps and utilizing the refrigerant's phase change enthalpy directly at the thermal interface.
Environmental adaptability represents another critical aspect of advanced thermal management systems. A hybrid refrigerant and air cooling system addresses this need by implementing dynamic mode switching based on ambient conditions and cooling demand. The system incorporates a brine loop that interfaces with both a refrigerant heat exchanger and an air-cooled heat exchanger, controlled by a three-way valve that routes flow according to temperature thresholds. When cooling demands are high or ambient temperatures elevated, the refrigerant circuit provides intensive cooling; when conditions permit, the system switches to air cooling to conserve energy. This dual-mode thermal control logic enables precise temperature regulation while minimizing energy consumption, representing a significant advancement over fixed-mode cooling systems.
Fast-charging scenarios present particularly demanding thermal management challenges due to the rapid heat generation within battery packs. A multi-loop thermal management system addresses this by coordinating refrigerant circulation through a sequence of heat exchangers. The refrigerant passes through external, motor, and battery heat exchangers in sequence, creating a multi-stage heat rejection pathway. A notable innovation in this system is the utilization of the motor coolant loop even when the drive motor is inactive, effectively repurposing it as an additional heat sink for the refrigerant circuit. This multi-stage heat rejection architecture significantly enhances thermal transfer capacity during fast charging, reducing battery temperature rise and enabling shorter charging durations without compromising cell longevity.
Structural integration represents a further advancement in phase-change cooling systems. A heat conduction row embedded with refrigerant and liquid pipes creates a hybrid thermal management solution that combines the advantages of both refrigerant and liquid cooling. The conduction bar runs longitudinally along the battery pack, with refrigerant and coolant pipes positioned in parallel within its structure. This design creates direct thermal contact with battery cells while enhancing surface area for heat exchange without requiring internal fans or fins. The modular and geometry-adaptive structure accommodates both prismatic and cylindrical cells, providing broad applicability across different battery configurations while maintaining high thermal performance with reduced energy consumption.
3. Modular or Parallel Cooling Architectures with Independent Control
Thermal uniformity across battery packs represents a persistent challenge in EV thermal management, particularly in vertically stacked configurations where gravitational effects and flow path differences can create significant temperature gradients. Advanced modular cooling architectures address this challenge by implementing parallel cooling paths with independent control mechanisms.
A modular cooling architecture with independently controlled parallel paths introduces multiple cooling elements, each equipped with dedicated valves and thermally coupled to corresponding battery modules via individual cooling plates. This approach enables precise refrigerant allocation based on the specific thermal needs of each module, rather than relying on a single cooling circuit for the entire pack. The modular design enhances thermal uniformity while supporting scalability for different battery configurations. The vertical stacking of cooling plates and battery modules optimizes space utilization, making this approach particularly suitable for constrained installation environments where packaging efficiency is critical.
Vertical battery configurations present unique thermal management challenges due to gravitational and thermal stratification effects that typically cause upper modules to accumulate more heat. A differential cooling strategy using strategically placed expansion valves addresses this issue by implementing a targeted refrigerant delivery system. The design increases the cross-sectional area of supply pipes to the first battery module group and positions expansion valves laterally adjacent to the modules. This configuration ensures higher refrigerant flow to the thermally critical regions while accommodating the space constraints typical of under-floor battery installations. The system also achieves cost efficiency by sharing the vehicle's HVAC compressor and providing passive cooling to adjacent electronic components such as the junction box.
High-capacity electric vehicles, particularly heavy-duty applications like electric trucks, impose thermal loads that exceed the capabilities of conventional single-loop cooling systems. A dual-loop refrigerant architecture addresses these demands by implementing two refrigerant circuits that can operate independently or in combination. Each loop incorporates dedicated compressors, heat exchangers, and control valves, enabling dynamic thermal load balancing across the system. This parallel configuration provides the flexibility to boost cooling capacity during high-demand scenarios while optimizing energy efficiency under lighter loads. The integration of sensors and throttling mechanisms enhances system responsiveness, making this approach well-suited for vehicles with high energy demands and extended operational cycles.
Multi-circuit thermal management represents a further evolution in modular cooling design, particularly for applications requiring both heating and cooling capabilities. A hybrid system with separate refrigerant, coolant, and battery cooling circuits employs a shared heat exchanger to facilitate thermal energy transfer between loops. This architecture enables the battery pack to be heated or cooled as needed using refrigerant-based processes, reducing reliance on energy-intensive electric heaters. The modularity of the individual loops combined with their coordinated operation provides fine-grained thermal control across various vehicle subsystems, enhancing energy efficiency particularly in cold climate operation while improving overall thermal reliability.
4. Refrigerant-Based Heat Pump Systems for Battery Heating and Cooling
Refrigerant-based heat pump systems represent a significant advancement over traditional thermal management approaches by providing bidirectional thermal control through a single system architecture. These systems leverage the thermodynamic principles of vapor compression cycles to efficiently transfer heat either to or from the battery pack, depending on operational requirements.
A heat pump-type refrigerant direct thermal management system eliminates intermediate heat transfer steps by creating direct thermal contact between the refrigerant loop and battery cells. The system incorporates a compressor, a four-way reversing valve, and a heat exchanger embedded within the battery pack structure. This direct thermal interface minimizes temperature gradients across the pack while providing uniform thermal regulation. The bidirectional capability enables the system to maintain optimal battery temperatures across diverse environmental conditions without requiring separate heating and cooling subsystems. This approach significantly improves energy efficiency by eliminating the parasitic losses associated with electric heaters, which typically convert electrical energy to heat at a 1:1 ratio, whereas heat pumps can achieve coefficients of performance exceeding 3:1.
System integration represents another critical aspect of advanced thermal management. An integrated refrigerant-based thermal management system unifies the thermal control of both the battery pack and passenger cabin through a shared refrigerant infrastructure. The architecture incorporates multiple heat exchangers, a compressor, and dedicated circuits for direct battery thermal management. A coaxial tube design with strategically positioned expansion valves enables precise thermal control, while dual motor cooling circuits optimize overall energy utilization. The system's multifunctional heat exchange architecture dynamically balances thermal demands across vehicle subsystems, leveraging waste heat from the electric drive assembly when available. A centralized control system continuously adapts to changing operational conditions, maintaining the battery within the optimal temperature range of 20°C to 35°C regardless of ambient conditions or vehicle operating state.
Safety considerations have driven the development of alternative approaches to refrigerant-based thermal management. A hybrid system combining refrigerant-assisted and air-based cooling eliminates liquid coolant entirely, thereby removing the risk of coolant leakage within the battery enclosure. The system employs a refrigeration loop to cool air, which is then circulated through the battery pack via a dedicated duct and fan assembly. During periods of lower thermal demand, the system can switch to natural cooling mode, drawing ambient air directly without engaging the refrigeration circuit. This dual-mode operation enhances energy efficiency while the elimination of liquid coolant significantly improves safety by removing leakage risks that could potentially lead to electrical shorts or thermal events within the battery pack.
Cabin comfort integration presents unique challenges for EV thermal management systems that share cooling capacity between the battery and passenger compartment. An HVAC-integrated battery cooling system addresses these challenges through intelligent load management that prioritizes cabin comfort during periods of high demand. The system employs a sophisticated controller that dynamically adjusts refrigerant flow and expansion valve operation based on real-time inputs including blower speed and evaporator temperature. Unlike conventional systems that can cause cabin temperature fluctuations when sharing thermal capacity, this design implements load balancing logic that temporarily defers battery cooling during peak HVAC demand. This approach ensures consistent passenger comfort while optimizing refrigerant utilization across the system, making it particularly suitable for multi-zone climate control architectures in larger vehicle platforms.
5. Refrigerant Flow Control and Distribution Optimization
Uniform refrigerant distribution represents one of the most significant challenges in battery thermal management, particularly as battery packs increase in size and complexity. Uneven refrigerant flow can create temperature gradients across the pack, leading to differential aging, capacity imbalances, and potential thermal runaway risks. Advanced flow control and distribution technologies address these challenges through innovative system architectures and control strategies.
A selective dual-line operation system introduces fluidically separated cooling circuits that can operate independently or in combination depending on thermal demands. The system functions in two distinct modes: a single-line mode for normal operating conditions and a dual-line mode during high thermal load scenarios such as fast charging or simultaneous HVAC operation. By creating thermal contact between battery modules and both cooling lines, and incorporating distributed sub-lines with individual shut-off valves, the system ensures balanced refrigerant distribution without oversizing the entire thermal management infrastructure. This approach prevents refrigerant overheating while maintaining thermal uniformity across the pack, enhancing both energy efficiency and system reliability.
Large or asymmetrically configured battery packs present particular challenges for refrigerant distribution, especially under varying ambient conditions or at low compressor speeds when refrigerant flow is limited. An active refrigerant flow control system addresses these challenges through a network of temperature sensors and flow control valves that dynamically adjust refrigerant routing based on real-time thermal data. This intelligent control strategy enables targeted cooling of specific modules experiencing elevated temperatures, ensuring consistent thermal performance even when refrigerant supply is constrained. The ability to adapt flow paths according to actual cell temperatures preserves battery health and performance without requiring complex liquid cooling infrastructure.
Modular cooling architectures further enhance refrigerant distribution through independent cooling elements with dedicated valves. Each cooling element comprises multiple plates in direct thermal contact with battery modules, individually controlled to provide localized cooling where needed. This architecture improves thermal uniformity across the battery pack while supporting parallel flow paths that enhance refrigerant distribution even in vertically stacked configurations. The system achieves cost and complexity reductions by implementing passive distribution logic rather than requiring centralized control mechanisms, making it both scalable and economically viable for diverse battery layouts.
Refrigerant routing optimization represents another approach to improving distribution efficiency. A system featuring unified refrigerant port placement with internal flow passages configures both refrigerant inlet and outlet on the same side of the battery pack, simplifying the mechanical layout while enhancing flow consistency. Each battery module receives refrigerant through dedicated passages, ensuring uniform flow rates and minimizing thermal gradients across the pack. This design eliminates the need for top and bottom guide members, reducing system size and facilitating integration into compact vehicle platforms. The serpentine flow path enhances heat transfer efficiency by ensuring that each cell receives adequate cooling without excessive refrigerant consumption.
6. Integration of Refrigerant Components Inside Battery Pack Housing
Traditional battery thermal management systems typically route refrigerant lines externally to the battery housing, creating multiple potential leak points and increasing system complexity. Advanced designs now integrate refrigerant circuits directly within the battery structure, enhancing both thermal performance and system reliability.
An integrated refrigerant circuit within the battery housing eliminates external refrigerant routing by incorporating refrigerant pipes directly into the cooling body, which simultaneously serves as the mounting surface for battery cells. This internalized path significantly reduces the number of joints and connection points, enhancing sealing reliability while simplifying assembly processes. The design achieves structural integration through a flange portion formed integrally with the refrigerant pipe that creates a secure seal where the pipe exits the housing through a dedicated through-hole. This interface is reinforced using bolts and sealing members to prevent refrigerant leakage, while elastic conduits outside the housing provide mechanical flexibility that reduces stress on the sealed interfaces. This integrated approach enhances both thermal management efficiency and long-term reliability while simplifying maintenance procedures.
Direct evaporative cooling combined with passive heat transfer mechanisms represents another approach to internal refrigerant integration. A flat heat pipe array integrated between battery cells provides efficient lateral heat conduction to a bottom-mounted evaporative cold plate. The system uses R134a refrigerant, throttled via an expansion valve before entering the cold plate where it evaporates upon absorbing heat from the battery. This architecture bypasses the inefficiencies associated with intermediate heat transfer steps in liquid-based or indirect cooling systems, enabling rapid heat removal directly at the source of thermal generation.
The system's adaptive control strategy dynamically regulates fan speed, compressor operation, and solenoid valve opening based on real-time thermal loads, ensuring optimal cooling under high-demand scenarios such as rapid acceleration or hill climbing. The integration of direct phase-change cooling with heat pipe coupling enhances thermal safety and performance while supporting the increasing energy density requirements of modern battery packs. The elimination of liquid coolant volumes and immersion-type cooling further contributes to system reliability and weight reduction, critical factors in next-generation electric vehicle design.
7. Immersion and Encapsulated Cooling Using Refrigerant
Immersion cooling represents one of the most thermally efficient approaches to battery thermal management, creating direct contact between the cooling medium and all battery surfaces. Advanced refrigerant-based immersion systems enhance this approach by incorporating phase change dynamics and specialized dielectric fluids.
A closed-loop immersion system employs dielectric refrigerants such as transformer oil in direct contact with battery modules. The architecture includes an outer casing with internal battery cavities, directional flow grooves, and an auxiliary heat exchanger equipped with real-time temperature sensors. A through-groove thermal flow design ensures uniform refrigerant distribution throughout the pack, preventing thermal stagnation and localized hotspots that could compromise battery performance and safety. The system's adaptive pump operation responds to thermal feedback, modulating flow rates to maintain optimal temperature conditions while supporting modular scalability for different battery configurations.
Phase-change immersive cooling takes this concept further by encapsulating each battery cell module within its own coolant-filled compartment. This approach eliminates thermal interface materials and complex heat transfer paths, creating direct contact between the cooling liquid and battery cells. As the cells generate heat, the cooling liquid absorbs thermal energy and vaporizes, creating a highly efficient heat transfer mechanism. An integrated heat exchanger condenses the vapor back to liquid within the same structural enclosure, creating a self-contained direct phase-change cooling loop for each module. The use of non-conductive refrigerants enhances safety by eliminating short-circuit risks, while the simplified and modular design reduces system weight and complexity.
Heat pipe technology combined with direct refrigerant evaporation creates another high-performance thermal regulation approach. This system embeds a flat heat pipe array between battery cells to rapidly collect and transfer heat to a bottom-mounted cold plate. The refrigerant undergoes throttling through an expansion valve before entering the cold plate, where it evaporates to absorb thermal energy. This direct refrigerant evaporation via cold plate eliminates the inefficiencies associated with indirect cooling systems that require multiple heat transfer steps. The system's intelligent control mechanism continuously adjusts fan and compressor speeds along with solenoid valve openings to match dynamic thermal loads, ensuring optimal cooling under demanding conditions such as fast charging or high-gradient driving while maintaining a compact and lightweight system architecture.
8. Safety-Oriented Refrigerant Cooling Designs
Safety considerations are paramount in refrigerant-based battery cooling systems, particularly regarding leak prevention and fire risk mitigation. Advanced designs incorporate multiple safety features to address these concerns while maintaining thermal performance.
A modular refrigerant distribution architecture enhances safety by isolating each battery module from others within the cooling system. Rather than employing a shared coolant loop that could propagate contamination throughout the pack in the event of a leak, this design uses dedicated refrigerant pipes per module connected to a central refrigerant tube housed within the pack frame. This configuration ensures that any leakage remains contained to the affected module, significantly reducing the risk of refrigerant-induced short circuits or thermal events across the pack. The system incorporates comprehensive sealing elements including gaskets and sealing rings at all connection interfaces, while an embedded leak detection sensor within the refrigerant tube housing provides early warning of potential failures. A dual-outlet drain valve enables controlled refrigerant discharge if a leak is detected, further enhancing the system's fire prevention capabilities.
Passive safety mechanisms represent another approach to enhancing thermal management safety. A capillary-integrated heat exchanger incorporates heat-deformable sealing elements within pressure relief holes that respond automatically to thermal events. When battery temperature exceeds safe operating limits, these seals deform to release refrigerant, which then evaporates and rapidly absorbs heat from the affected area. This passive response mechanism provides emergency cooling without requiring active control systems, suppressing potential fires while thermally isolating affected cells to prevent thermal runaway propagation. During normal operation, capillary layers such as sintered copper or metal foam ensure efficient heat transfer, while the sealed enclosure maintains system integrity until a critical event triggers the fail-safe mechanism.
Reducing electrical component dependencies further enhances safety in refrigerant cooling systems. A design leveraging passive refrigerant circulation minimizes fire risks by eliminating electrically driven pumps that represent potential failure points. The system utilizes natural circulation between a cooler in contact with the battery and an elevated radiator, driven by buoyancy and gravitational forces. Under favorable ambient conditions, refrigerant condenses passively without requiring active components, reducing system complexity and energy consumption. An intelligent control unit monitors both battery and ambient temperatures to determine when to activate a secondary water-cooling loop, ensuring thermal management continuity even in extreme conditions. The reduced mechanical complexity enhances reliability while the dual-mode operation provides adaptive cooling across diverse operational scenarios.
9. Refrigerant-Based Cooling for Fast Charging Scenarios
Fast charging represents one of the most thermally demanding scenarios for electric vehicle batteries, with high current flows generating substantial heat that must be efficiently managed to prevent degradation and ensure safety. Advanced refrigerant-based cooling systems address these challenges through innovative thermal management strategies.
Anticipatory thermal management provides a proactive approach to fast charging thermal control. A refrigerant-based pre-cooling system initiates battery cooling before fast charging begins, leveraging the vehicle's HVAC loop to store cold energy within the battery housing. This approach ensures the battery enters the charging phase at an optimal temperature, preventing the rapid temperature rise that typically occurs during the initial charging period. The system's intelligent control logic triggers pre-cooling based on the battery's state of charge or via manual user activation, creating an anticipatory thermal buffer that helps prevent thermal runaway and degradation during charging. The system operates with minimal noise by utilizing the refrigerant cycle directly, making it suitable for quiet charging environments without requiring noisy cooling fans.
Dedicated thermal management architectures further enhance fast charging capabilities. A dual refrigerant circulation system separates the thermal management of the cabin and battery into independent refrigerant loops, each optimized for its specific application. The battery cooling loop employs a high-speed compressor and dedicated chiller to deliver intensive cooling during fast charging, while thermal energy exchange between the loops occurs via a cooling water medium and radiators. This configuration avoids the compromises inherent in single-loop systems, enabling flexible multi-mode operation tailored to various driving and charging scenarios. The result is a durable and energy-efficient system capable of maintaining battery temperatures within safe limits even under aggressive fast charging profiles that would overwhelm conventional cooling systems.
Safety considerations during fast charging have driven the development of alternative cooling approaches. A hybrid thermal management system combines refrigerant-based cooling with air duct circulation, eliminating liquid coolant entirely to remove leakage risks during high-vibration events typical of vehicle operation. During active cooling modes, refrigerant cools a heat exchanger that conditions air circulated through the battery pack via a duct and fan assembly. When ambient conditions permit, the system switches to natural cooling mode to conserve energy while maintaining thermal control. Intelligent temperature-based feedback ensures cooling is applied precisely when needed, enhancing both safety and energy efficiency during fast charging operations without compromising thermal performance.
10. Refrigerant-Based Systems Using External Airflow or Ambient Conditions
Optimizing energy efficiency in electric vehicle thermal management requires systems that can leverage ambient conditions when favorable, reducing the energy consumption associated with active cooling. Advanced refrigerant-based systems incorporate passive cooling capabilities that utilize external airflow and ambient temperatures to enhance efficiency.
An unpowered refrigerant-based battery cooling system introduces a hybrid architecture that combines passive and active cooling modes based on ambient conditions. The system employs a thermosiphon loop where a radiator positioned above a refrigerant cooler creates natural circulation through gravity and buoyancy effects, eliminating the need for electrically powered pumps when conditions permit. When ambient temperatures are sufficiently low to support refrigerant condensation, the system operates in passive mode, conserving energy while maintaining thermal control. An electromagnetic valve opens or closes based on ambient conditions, enabling seamless transitions between passive and active cooling modes as required.
The system's dual-mode thermal control logic continuously evaluates environmental and battery temperature data to determine the optimal operating mode. A solenoid valve in the refrigerant return path provides precise flow modulation based on current conditions, enhancing energy efficiency by minimizing electrical input requirements. This adaptability not only reduces energy consumption but also simplifies the thermal architecture by decreasing component count and complexity. The passive cooling loop further enhances safety by maintaining thermal regulation even during system power loss, extending battery life while reducing thermal runaway risks.
Comprehensive thermal management across multiple vehicle systems presents additional challenges and opportunities for efficiency optimization. An integrated heat pump assembly addresses the complexity of managing multiple thermal loads through a centralized refrigerant circuit with a bypass-enabled ambient heat exchanger. The system incorporates dual coolant circuits—one for the battery and one for the drivetrain—enabling independent yet coordinated thermal management across vehicle subsystems. A 3/2-way refrigerant valve with expansion functionality provides flexible refrigerant routing that optimizes heat transfer paths based on ambient conditions and thermal demands.
The ambient heat exchanger bypass with refrigerant valve dynamically reconfigures refrigerant flow to maximize performance across varying climatic conditions. By capturing and redistributing waste heat from the battery and drivetrain, the system reduces dependency on electric heaters, improving overall coefficient of performance (COP) and energy efficiency. This integrated approach creates a cost-effective, scalable solution that maintains optimal temperatures across all vehicle thermal systems while supporting cabin climate functions including dehumidification and supplemental heating. The modular architecture facilitates integration across diverse vehicle platforms, enhancing thermal flexibility without compromising efficiency or passenger comfort.
11. Refrigerant-Based Systems with Integrated Heating for Cold Start or Winter Conditions
Cold ambient temperatures present significant challenges for electric vehicle batteries, reducing available capacity, limiting charging rates, and potentially accelerating degradation. Advanced refrigerant-based thermal management systems address these challenges by integrating heating capabilities that maintain optimal battery temperatures even in winter conditions.
A heat pump-based architecture creates an interconnected thermal network linking the battery, electric drive components, and cabin heating systems. This integrated approach uses refrigerant heat exchangers, a liquid-cooled condenser, and a six-way solenoid valve to dynamically redistribute thermal energy throughout the vehicle. The system extracts waste heat from the battery and motor during normal operation and transfers it to the cabin or back to the battery as needed, providing effective preheating during cold starts without requiring dedicated electric heaters. Multiple electronic expansion valves and sophisticated valve control enable seamless transitions between heating and cooling modes based on subsystem demands, improving energy efficiency while reducing thermal stress across components.
Adaptive thermal management strategies further enhance cold-weather performance. A dual-mode thermal management system implements a brine circuit that can route through either a refrigerant heat exchanger or an air-cooled heat exchanger depending on ambient conditions. In cold environments, the system activates the refrigerant loop to provide more effective heating or cooling, while defaulting to air cooling in milder conditions to conserve energy. A three-way valve combined with a frequency-controlled compressor enables real-time responsiveness to changing thermal loads, ensuring the battery remains within its optimal operating temperature range regardless of external conditions. This adaptability enhances both battery safety and longevity while improving overall system efficiency.
Safety considerations in cold climates have driven the development of alternative thermal management approaches. A refrigerant-air hybrid system eliminates liquid coolant entirely, removing the risk of coolant freezing or expansion damage in sub-zero conditions. The system employs a refrigeration loop for active thermal management and an air duct system for natural or forced convection depending on requirements. During heating mode, the refrigerant circuit operates as a heat pump, warming air that is then circulated through the battery compartment via a fan. An intelligent control unit modulates compressor and fan operation based on temperature sensor feedback, optimizing thermal performance and energy consumption while enhancing safety through the elimination of liquid coolant leakage risks.
12. Composite or Multi-Stage Cooling Systems
Battery thermal management presents complex challenges that often exceed the capabilities of single-mode cooling systems, particularly across varying operational conditions and thermal loads. Composite or multi-stage cooling systems address these limitations by integrating multiple cooling technologies within a coordinated architecture.
A composite cooling system architecture implements a three-stage approach that adapts to the battery's thermal state. The system incorporates distinct cooling circuits: a room temperature radiator for low thermal loads, an indirect refrigerant circuit for moderate to high loads, and a direct refrigerant circuit for rapid intervention during critical overheating scenarios. Each circuit operates independently, enabling targeted thermal management without unnecessary energy expenditure. The system's core innovation lies in its dual-working-fluid heat exchange plate, which separates refrigerant and coolant flows into isolated channels to prevent cross-contamination while facilitating efficient heat transfer. This plate supports both single-layer and double-layer configurations, providing flexibility based on thermal performance requirements. A hierarchical control strategy activates the appropriate cooling stage based on real-time temperature data, optimizing energy efficiency while ensuring thermal stability.
System integration across vehicle thermal domains represents another approach to composite thermal management. An integrated thermal management system unifies the thermal control of the battery, cabin, and electric drive components within a coordinated architecture. The system employs a heat pump with multiple refrigerant heat exchangers, solenoid valves, and liquid-cooled condensers to create a flexible thermal network. A six-way solenoid valve combined with strategically positioned expansion valves enables dynamic reconfiguration of refrigerant pathways, facilitating seamless transitions between cooling, heating, and heat recovery modes. This approach captures waste heat from the battery and motor for cabin preheating or battery warming, significantly improving overall energy utilization while reducing component redundancy.
The refrigerant-based multi-mode operation provides precise temperature regulation across all vehicle systems, enhancing both battery protection and passenger comfort. The modular configuration and dynamic fluid routing capabilities make the system adaptable to diverse vehicle platforms and operational requirements, creating a scalable solution for next-generation electric vehicles with increasingly complex thermal management needs.
13. Compact or Integrated Thermal Management Modules
Vehicle packaging constraints and manufacturing efficiency requirements have driven the development of increasingly compact and integrated thermal management systems. These designs consolidate multiple thermal functions within unified modules that reduce spatial requirements while enhancing performance.
A compact battery cooling system addresses packaging limitations by integrating refrigerant lines into the bottom section of the battery case rather than routing them through the battery pack itself. This configuration creates a more compact assembly while improving thermal isolation between cells and refrigerant components. The system employs a simplified architecture with a single electromagnetic valve for refrigerant control and leverages the vehicle's existing HVAC infrastructure for coordinated cooling. A notable innovation is the battery case's functionality as a cold reserve, enhancing thermal retention and response time during operation. This integrated approach improves vehicle loadability and spatial efficiency without compromising thermal performance.
Component consolidation represents another approach to thermal system integration. A thermal management integrated unit (TMIU) consolidates key components—including compressor, heat exchangers, valves, and sensors—onto a single mounting plate. This highly integrated module addresses the inefficiencies associated with conventional distributed thermal subsystems, which typically require extensive piping and complex installation procedures. The TMIU supports multiple operational modes including battery cooling, cabin air conditioning, and dehumidification through a centralized control architecture. The inclusion of a secondary throttling device and dedicated temperature sensor on the battery cooler enables precise refrigerant flow control and real-time thermal monitoring. This compact, multifunctional unit reduces spatial requirements and manufacturing costs while enhancing overall system responsiveness.
Energy efficiency optimization has driven further innovations in thermal system architecture. A cascade refrigeration architecture creates an interconnected thermal network comprising two separate refrigerant cycles—one for HVAC and another for battery thermal management—linked through a shared refrigerant cooler. This design eliminates dependency on electric heaters by implementing refrigerant-based heating, significantly improving energy efficiency across all operating conditions. The battery cooling subsystem employs an indirect loop where coolant interfaces with the secondary refrigerant cycle, providing precise and uniform temperature control throughout the pack. Advanced valve control using electronically regulated expansion valves ensures dynamic refrigerant flow modulation based on real-time thermal demands. This indirect cooling approach enables tighter battery cell packaging for improved compactness while allowing simultaneous operation of HVAC and battery thermal management without redundant hardware.
14. Control Algorithms and Intelligent Switching for Thermal Management
Advanced control algorithms and intelligent switching mechanisms represent the operational intelligence behind modern refrigerant-based thermal management systems. These technologies optimize performance across varying conditions while enhancing safety and efficiency.
Temperature uniformity across battery cells presents a persistent challenge in refrigerant-based cooling systems, particularly under high power demand or limited cooling capacity scenarios. A cooling method based on available refrigeration power addresses this challenge through a sophisticated control algorithm that dynamically calculates residual cooling capacity after accounting for passenger compartment demands. Based on this real-time assessment, the system selects from discrete cooling power levels and adjusts refrigerant mass flow accordingly, ensuring that refrigerant is either fully utilized or not introduced at all. This approach prevents partial evaporation scenarios that can create thermal hotspots within the battery pack. The system's modular design incorporates dual counter-flow channels with precisely calculated contact surface area ratios, supporting uniform heat transfer across diverse battery configurations.
Direct refrigerant cooling with intelligent flow control provides another approach to optimizing thermal management. An actively-switched flow control mechanism addresses the challenges associated with maintaining consistent temperature regulation across large or asymmetrical battery packs, particularly in cold ambient conditions where compressor speeds and refrigerant flow rates are reduced. The system eliminates liquid coolant loops entirely, instead using refrigerant in direct thermal contact with the battery through a cooling plate. Temperature sensors integrated throughout the pack provide real-time thermal data to a closed-loop control system that modulates a network of flow control valves, including 3-way and shutoff valves. These valves dynamically alter refrigerant flow paths and concentration based on localized temperature readings, enabling precise thermal balancing across individual cells without requiring complex liquid cooling infrastructure.
Get Full Report
Access our comprehensive collection of 172 documents related to this technology
Identify Key Areas of Innovation in 2025
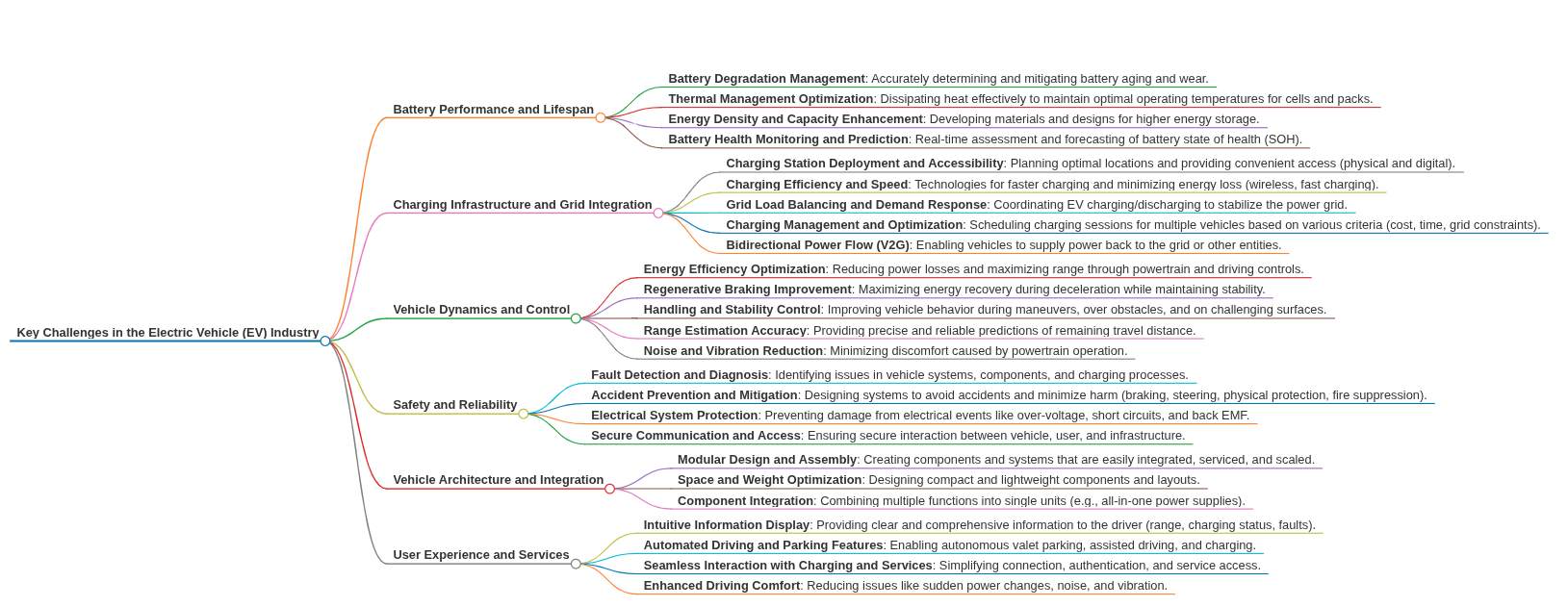