Battery Charging and Discharging Optimization for EV
Thermal management in battery packs requires balancing multiple critical parameters. Individual cells can reach temperatures above 150°C during thermal events, with gas evolution rates exceeding 2L/min per cell and pressure buildups that can compromise pack integrity. Current systems must manage heat transfer between cells while maintaining optimal operating temperatures across varying charge/discharge profiles.
The fundamental challenge lies in detecting and containing thermal events at the cell level while preserving the pack's energy density and performance characteristics.
This page brings together solutions from recent research—including adaptive thermal management systems with individual cell control, selective discharge protocols for preventing propagation, and intelligent charging systems with thermal protection. These and other approaches focus on practical implementation strategies that can be integrated into existing battery architectures while maintaining safety margins and operational efficiency.
1. Battery Management System with Dynamic Charge and Discharge Limit Adjustment Based on Cell Condition Analysis
GM Global Technology Operations LLC, 2024
Adaptive battery management for extending the life of high-voltage battery packs in electric vehicles by automatically adjusting charging and discharging limits based on cell condition data. The method involves measuring cell voltage, current, and temperature, processing the data through calibrated relationships to determine cell degradation values, and then modifying charge/discharge limits and thermal limits based on those values. This allows operating the battery at lower limits when cells are degrading to delay failure and extend overall pack life.
2. Battery Charging System with Temperature-Responsive Power Regulation and Integrated Temperature Sensing
E MAT LAB INC, E MATERIAL LAB INC, 2023
A system to prevent battery damage during charging by measuring battery temperature and controlling charge/discharge power. The system includes a temperature sensor in the battery to monitor temperature during charging. A battery management system (BMS) receives the temperature data and adjusts the charge/discharge power to prevent overheating and damage. This allows proactive cooling and protection of the battery during charging based on real-time temperature feedback.
3. Vehicle Battery System with Individual Cell Overcharge Disconnection and Exclusion Mechanism
Ford Global Technologies, LLC, 2023
A vehicle battery system that can prevent damage from overcharging and cell failures. The system has an overcharge limit device that individually disconnects cells with high pressure. When a cell is disconnected, the controller stops controlling that cell and continues operating the rest. This prevents further overcharging. If multiple cells are disconnected, it stops all cells. This prevents overcharging of remaining cells. It also excludes disconnected cells from balancing and lowers the overall battery output limit.
4. Battery Thermal Management System with Gradual Power Limitation Based on Coolant Fluid Thermal Exchange Capacity
Ford Global Technologies, LLC, 2022
Electrified vehicle with a battery that can be power limited based on the thermal exchange capacity of the coolant fluid circulated by the thermal management system. The power limit is gradually reduced at higher battery temperatures to prevent sudden power interruptions. The limit lines increasing in steepness in correlation with thermal exchange capacity allow higher charge/discharge rates when the coolant temperature is lower. This balances battery performance and temperature management without unnecessary power limits.
5. Battery Cell with Thermoelectric Cooling Activated by State of Charge and Temperature Sensors
Apple Inc., 2022
Reducing battery swelling and degradation during charging by actively cooling the battery cell when it reaches full charge and high temperature. A thermoelectric cooler (TEC) is used to cool the battery cell when the state of charge (SOC) exceeds a threshold and the temperature exceeds a threshold. This prevents excessive heating and swelling during float or trickle charging, which can degrade battery life. The cooling is activated by the battery management system (BMS) controller based on SOC and temperature sensors.
6. Rechargeable Battery with Internal Heat Spreader for Preheating Prior to Fast Charging
Global Graphene Group, Inc., 2022
Fast charging of rechargeable batteries like lithium-ion cells without degradation or safety issues at low temperatures by preheating the battery internally using a heat spreader. The spreader is inserted partially or fully inside the battery cell and conducts heat from an external source to warm the cell before charging. This avoids the dangers of high current densities and lithium plating at cold temperatures. The spreader can contact the electrode terminals or be inside the cell housing. It enables rapid charging at temperatures like room temperature, which reduces time compared to waiting for internal heating during charging at low temperatures.
7. Battery Pack Thermal Runaway Mitigation via Selective Module Discharge and Isolation
GM Global Technology Operations LLC, 2022
Controlling thermal runaway propagation in battery packs with multiple modules by selectively discharging modules to prevent runaway spread. When a thermal runaway is detected in one module, the controller checks if current is flowing through that module. If not, it decouples the module to isolate the runaway. If current is flowing, it connects the other modules to an external load to discharge them, preventing runaway propagation. This controlled discharge can mitigate thermal runaway chain reactions in battery packs.
8. Battery Module with Independent Cell Temperature Control Using Fluid-Based Heat Transfer System
ISUZU MOTORS LTD, 2021
Vehicle battery module with independent temperature control for each battery cell to prevent temperature variations between cells. The module has a heat transfer system with a heater, pipes, and a flow rate controller. A temperature sensor monitors each cell. The controller adjusts the heated fluid flow rate based on cell temperatures. It prioritizes heated fluid to low temperature cells. This prevents overheating or undercooling issues that can degrade battery performance or life.
9. Electric Vehicle Charging Inlet with Flexible Thermal Sensor on Power Terminal
TE CONNECTIVITY CORPORATION, 2021
Charging inlet for electric vehicles that allows higher charging rates without risk of damaging the charging system due to heat. The charging inlet has a flexible thermal sensor mounted directly on the power terminal that curves along the terminal's outer surface. This allows more accurate and faster temperature monitoring compared to sensors farther away. It prevents overheating by enabling faster response to high temperatures and reducing the power transfer rate if needed. The sensor's flexibility conforms to the terminal shape for better contact.
10. Battery Temperature Regulation System with Adaptive Charging and Discharging Control Based on Location and Condition Analysis
Apple Inc., 2021
Optimizing battery charging and discharging to improve performance and longevity by regulating battery temperature based on charging location and anticipated charge/discharge conditions. The method involves identifying the charging location, determining if excess charge is available, and cooling the battery pack using that excess charge instead of charging at full rate. It also sets target temperatures based on charging location to prevent overheating in hot environments and overcooling in cold environments.
11. Battery Pack Coolant Circuit with Selectively Activated Thermoelectric Cooling Device
FORD GLOBAL TECHNOLOGIES, LLC, 2021
Battery thermal management system for electric vehicles that uses a selectively activated thermoelectric device to augment cooling of the battery pack during high thermal load events like DC fast charging. The thermoelectric device is positioned in the coolant circuit and powered separately from the battery during charging to draw heat from the coolant and further cool the battery. This prevents overheating during intense charging when the battery demands more power. The thermoelectric cooling is also activated if ambient temperatures exceed a threshold.
12. Charging Connector with Embedded Thermal Sensors and Circuit Management for Overheat Detection and Control
WEBASTO CHARGING SYSTEMS, INC., 2020
Safe charging of electric vehicles (EVs) using a thermal monitoring and circuit management feature in the charging connector itself. The connector has embedded thermal sensors that can detect overheating. If a predetermined threshold temperature is exceeded, the connector disrupts the charging control signal to the EV. This stops charging until the temperature drops. The connector can also reverse the charging polarity to allow the EVSE to detect thermal faults. The onboard thermal management prevents overheating issues without requiring additional wiring back to the EVSE.
13. Lithium-Ion Battery System with Active Cooling and Temperature-Responsive Current Regulation
BOSCH GMBH ROBERT, ROBERT BOSCH GMBH, 2020
Optimizing the performance of lithium-ion battery systems in electric vehicles by actively cooling them during charging and discharging. The method involves using a cooling system with a heat exchanger in each battery module. The system monitors the temperature of the modules and cells during charging/discharging. If the temperature exceeds a threshold, it reduces the charging/discharging current. This prevents overheating beyond the optimal temperature range for the cells. By actively managing cell temperatures, it allows higher charging/discharging rates without degradation.
14. Plate-Shaped Battery Cell with Bent Sealing Sections and Phase Change Material Coating
LG Chem, Ltd., 2020
Battery cell design to improve cycle life and safety by controlling temperature inside the cell. The cell has a plate shape with sealing parts around the edges that fuse together. The sealing parts have bent sections that closely contact the cell body. Phase change material (PCM) is coated on the inner bent surfaces. The PCM absorbs/releases heat to maintain stable cell temperature during charging/discharging. This prevents excessive temperature variations and mitigates internal damage. The bent sealing configuration maximizes PCM contact area.
15. Electric Vehicle Battery Temperature Control via Simulated Charge Rate and Temperature Response Modeling
CHONGQING JINKANG NEW ENERGY AUTOMOBILE CO., LTD., 2019
Optimizing temperature control in electric vehicle batteries during fast charging to prevent degradation and improve lifetime. The method involves simulating battery responses at different charge rates and temperatures to find an optimal input temperature profile that minimizes lithium plating and uniformly heats/cools the battery. This profile is then applied to the temperature management system to optimize charging without uneven heating/cooling. By accurately modeling and optimizing battery temperature profiles, lithium plating can be reduced during fast charging.
16. Method for Dynamic Adjustment of Charging Voltage Based on Predicted Temperature Rise in Secondary Batteries
LG CHEM, LTD., 2019
Adjusting the charging condition of a secondary battery to prevent overheating when cooling is not practical. The method involves predicting the temperature rise of the battery during charging based on its current temperature, current, and external conditions. If the predicted charging voltage is lower than the upper limit, it is lowered to match. This prevents excessive charging currents that raise temperature. By dynamically adjusting the charging limit based on prediction, it prevents overheating even without active cooling.
17. Battery Thermal Management System with Microcontroller-Governed Variable Current Control Based on Temperature and Internal Resistance
Yanfeng Visteon Electronics Technology (Nanjing) Co., Ltd., 2019
Battery thermal management system and charging/discharging control method for electric vehicles that improves battery life and safety by optimizing charging/discharging currents based on battery temperature, temperature rise, and internal resistance. The system uses a microcontroller (MCU) and temperature sensors to monitor battery conditions during charging and discharging. It adjusts current limits, balances charge/discharge, and regulates cooling to prevent overheating, smoldering, leaking, short circuiting, fires, and explosions.
18. Thermal Management System for Power Batteries with Dual-Stage Charging and Sensor-Driven Cooling Control
SHENZHEN MINGFEIYUAN TECH CO LTD, SHENZHEN MINGFEIYUAN TECHNOLOGY CO LTD, 2017
A thermal management system for power batteries that effectively controls battery temperature to improve battery life and safety. The system has a temperature sensor, controller, cooling source, charging module, and discharge module. The charging module has two current stages, with the second stage having lower current. Batteries, the temperature sensor, and both modules connect to the system. This allows targeted cooling based on sensor readings during charging and discharging to prevent overheating and minimize temperature extremes.
19. Battery Power Exchange Controller with Temperature and Degradation Rate Equalization
NISSAN NORTH AMERICA, INC., 2015
Controlling battery degradation rate in electric vehicles by adjusting charging/discharging power to equalize temperature and deterioration across batteries. A power exchange controller monitors battery temperatures during charging/discharging and adjusts power flow to maintain an equalized temperature. This prevents faster degradation in hotter batteries by throttling their charge/discharge rate. By matching degradation rates across batteries, it aims to extend overall battery life.
20. Battery System with Microprocessor-Controlled MOSFET Switching for Cell Balancing and Fault Isolation
Coy A. Hudnall, William E. Bowman, Kevin J. Bennett, 2011
A lightweight, high-performance battery with regulated output voltage, cell balancing, and self-monitoring diagnostics to prevent thermal runaway. The battery has separate charging and output connections, allowing higher charging voltages. A microprocessor-controlled MOSFET switching circuit monitors cells, balances voltage, prevents overcharge/discharge, and isolates faulty cells. The output voltage is adjustable. A polling circuit disconnects cells to measure voltage and isolate faulty ones. The battery also has a microprocessor, display, and charging circuitry.
Get Full Report
Access our comprehensive collection of 27 documents related to this technology
Identify Key Areas of Innovation in 2025
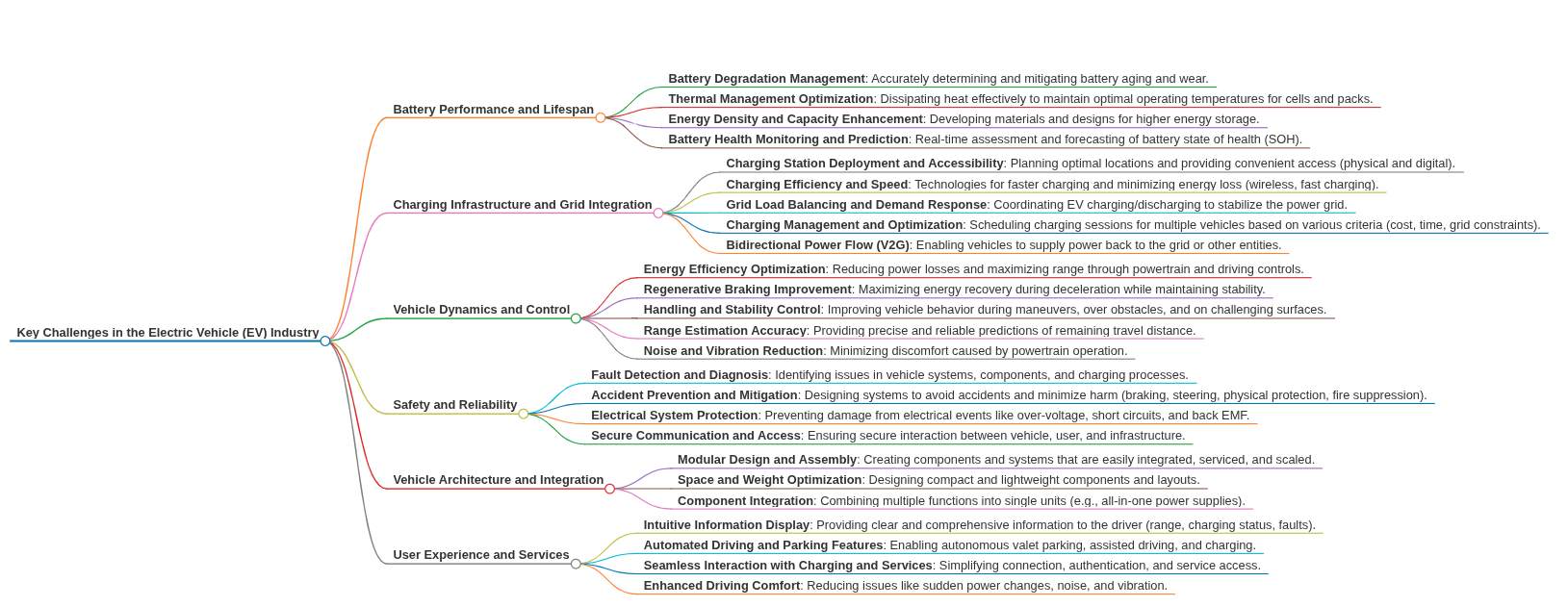